Tips for Cutting Stainless Steel Shims With Laser Cutting and Waterjet Technologies
Laser Cutting or Waterjet Technologies
Laser cutting and waterjet cutting each bring their own exciting processes for crafting stainless steel shims and metal alloy components. Both methods deliver outstanding precision and high-quality results, but they shine in different ways. While both technologies are excellent manufacturing methods, the choice is yours based on the specific needs of your project and the recommendations from established service providers. Let’s explore the fantastic differences:
Laser Cutting Technology
- Use intensified beams of focused wavelengths of light such as ultraviolet or infrared.
- Laser cutting is a non-contact process meaning only the beam of light is touching the material. No hard-edge tool or abrasive media is cutting.
- Laser cutting of shims and similar parts is done in thinner gauges of stainless steel (foils and sheets) and other alloys.
- Prototyping is a favored method to explore new designs and new materials.
- Can incur some heat affected zones or HAZ and minimized by adjusting the laser parameters.
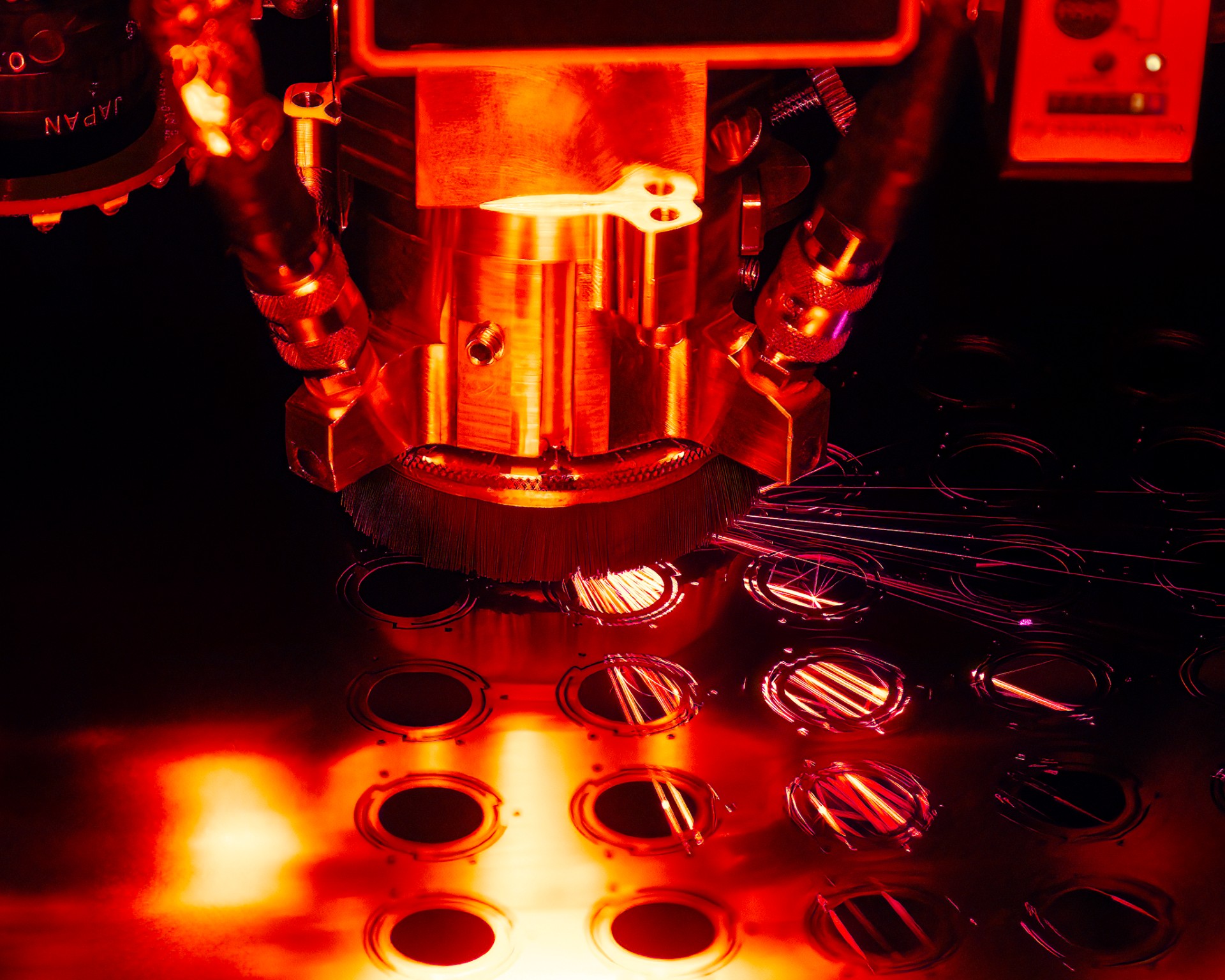
Waterjet Cutting Technology
- Waterjet technology applies a jet of highly pressurized water through a nozzle to cut.
- The stream of the jet is comprised of water and other abrasive media. The combination creates the cutting tool.
- Waterjet cutting can cut thicker gauges of stainless steel and other alloys.
- Production volumes can be done through waterjet technology.
- Good option for materials sensitive to heat affect.
These differences between laser and waterjet cutting offer options to manufacturers and anyone seeking high-quality stainless-steel shims. The following tips will aid in determining what technology is best to move forward with your desired service provider:
Laser Cutting Process
- What is the thickness of the stainless steel and the geometry to be cut? Laser cutting can produce some fine details and features on stainless steel foils and sheets from thickness between 0.0127mm to 4mm or thick, for example, with beam diameters of 10, 20 and 40microns for many systems.
- What is the projects tolerance? Laser cutting encompasses a variety of laser system types. They range from holding tolerances of +/- 0.0127mm to 0.100mm on many projects.
- Quantities- Laser cutting of stainless-steel shims can readily support R&D and prototyping runs. Once tested and approved, the laser process is easily adjusted to run higher volume production runs.
- Edge quality on laser cut shims will have straight walls and be dimensionally accurate, but may need post processing to remove burrs.
Waterjet Cutting Process
- Stainless steel from thicknesses ranging from ¼” inch to 12” inches, for example can be cut by waterjet systems. With some systems having a multi-axis cutting head, 3-dimensional applications are possible.
- The tolerance that can be held ranges typically from 0.050mm and higher, depending on the thickness of the stainless steel. A ¼ inch plate will hold a tighter tolerance than an 8.0” plate.
- Quantities cut by waterjet can be small runs and scale up to volume manufacturing.
- Waterjet cutting has no heat effect, but the wall smoothness does vary per the coarseness of the abrasive media used.
In conclusion, when manufacturing stainless steel shims, it is essential to consider the specific requirements of your project to determine whether laser cutting or waterjet cutting is more suitable. Laser cutting is ideal for achieving fine details and precise tolerances in thin materials, while waterjet cutting excels in handling thicker and multi-dimensional applications without heat effect. Carefully evaluate the material thickness, desired edge quality, and production volumes to choose the optimal cutting process that meets your project’s needs efficiently and effectively.