Navigating Laser Cutting Copper
In the intricate world of metal fabrication, copper presents its own set of challenges. A-Laser not only understands these challenges but excels at conquering them.
What Are the Best Ways to Cut Copper?
The best ways to cut copper will be determined by factors such as the desired accuracy and precision, materials thickness, design complexity and others. The manufacturing of precision copper parts has been well established for decades now and copper has been a resource for humankind for millennia. Copper and gold are believed to be the first alloys worked by humans which started as early as the Neolithic Age, or about 10,000 BCE.
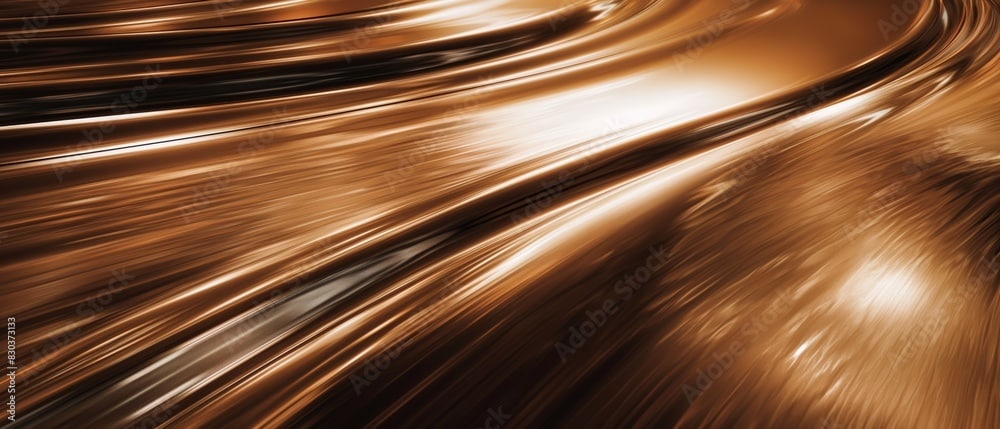
Those early discoveries of raw materials like copper did eventually contribute to changes in the human condition. Copper was used in the creation of ornate objects and vessels and for tools and weapons. The Bronze Age, which itself was significant in technological advancements, used copper and tin to create bronze and establish greater strength in the tools that were made. Processing copper, as every else goes in technology, advanced over the centuries with new methods, materials and ways to harness copper. Along this path of discovery and innovation, the characteristics of copper would push new ideas for its use. Some of the highest regarded characteristics of copper are having great electrical conductivity, thermal conductivity and antimicrobial properties. With such characteristics, advancements in medicine, science, and the development of electronics are just a fraction of how copper has made a substantial influence on technology. Today, there are multiple methods available to cut copper and this focuses often on the manufacturing of precision components. The days of crude tools and unregulated processes are now done through CNC lathes, CNC Mills, laser cutting and other methods. The following table highlights the best available ways that are used to cut copper:
Method | Technology | Accuracy | Thickness Range |
---|---|---|---|
CNC Lathe | A lathe is a machine tool that rotates a workpiece against a cutting tool. CNC Lathes for create cylindrical shapes and Intricate features on parts, good for high production. | 0.0127mm to 0.508mm | 0.025mm to Upper thickness range varies depending on the tool used. Good for 3,4 and 5 axis components. |
CNC Milling | A milling machine uses a rotating cutter to remove material from a workpiece. CNC Milling creates a wide variety of shapes and complex features. Good for high production. | 0.0127mm to 0.0508mm | 0.025mm Upper thickness range varies depending on the tool used. Good for 3,4 and 5 axis components. |
Laser Cutting | A laser beam is used to vaporize the material, creating precise cuts with minimal heat distortion. Laser cut copper is ideal for intricate designs and small parts. Great for R&D and production. | +/- 0.0127mm to 0.0508mm | From 0.0127mm thick up to 25mm thick, depending on the laser type used. Good for 2D geometries. |
Waterjet Cutting | Waterjet uses a high-pressure stream of water mixed with abrasive particles to cut through materials. It is highly accurate and can cut complex shapes without heat-affected zones. | +/- 0.025mm to 0.0127mm | 0.025mm to 12.6mm, typically can cut up to 3 axis. |
Wire EDM | Wire EDM uses a spark between a wire electrode and the workpiece to erode material away. It is highly accurate and can cut intricate shapes in hard-to-machine materials. | +/- 0.0025mm to 0.025mm | 0.0025mm up to 12.6mm-Good for 2 and 3 axis geometries. |
Plasma Cutting | A plasma torch is used to cut through materials by ionizing the surrounding gas. Plasma cutting is often used for thicker materials and can handle complex shapes. | +/- 0.254mm | 6.35mm up to 152.4mm up to 3 axis cutting. |
Because copper has characteristics of being antimicrobial, electrically conductive, recyclable and machinable, it is easy to understand that industries in space exploration, medical, electronics, thermal management and so on, are using this alloy. Comparing laser cut copper to CNC Milling of copper to wire EDM processing of copper is not equal. Each methods used is done to per the factors of the designed component and such considerations include:
- Desired accuracy and precision
- Material thickness
- Shape complexity
- Production volume
- Cost considerations
The best way to cut copper will be done by careful consideration of these factors in which manufacturers can discuss with their customers and select the most appropriate cutting method to produce high-quality copper components.
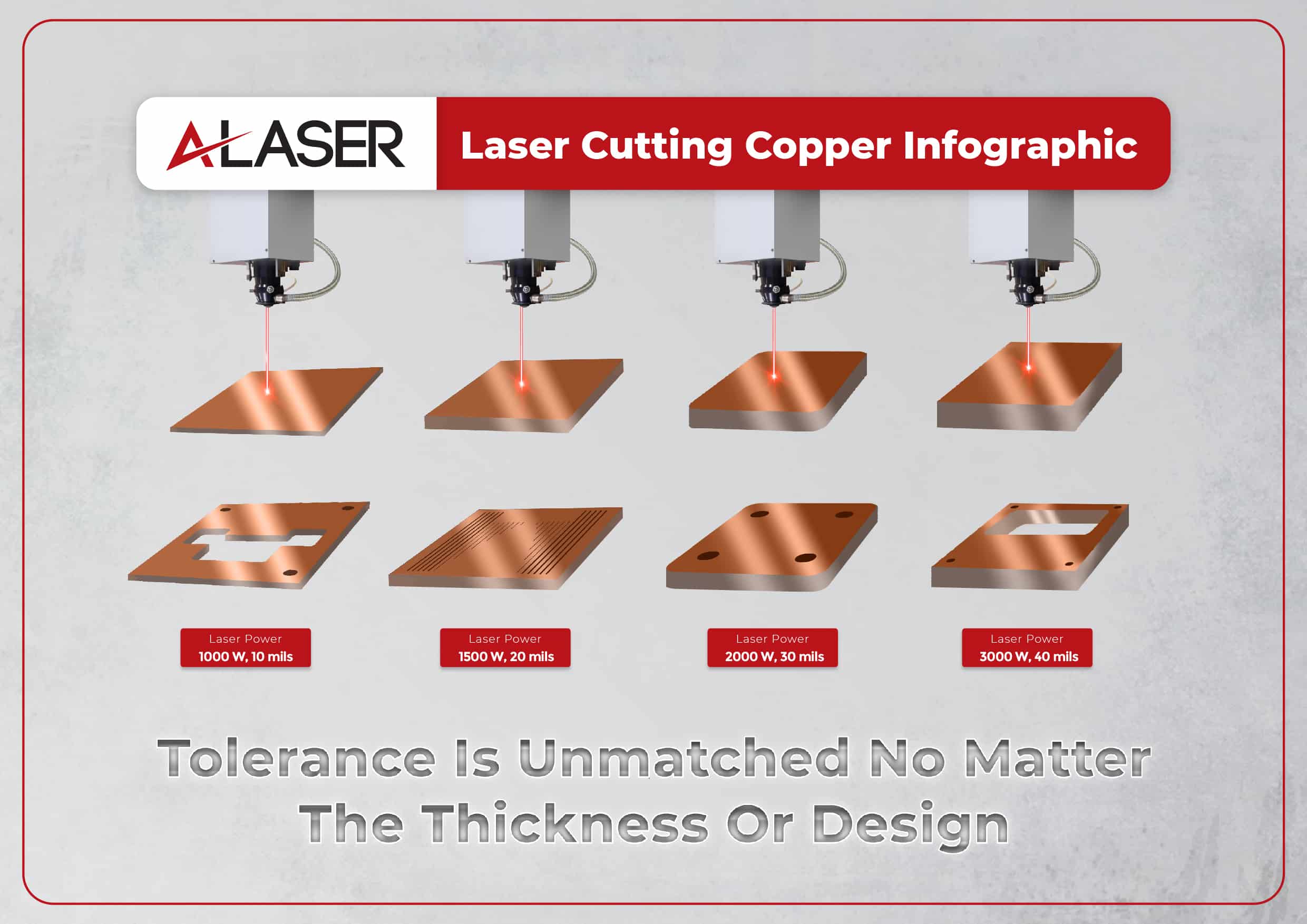
What Are the Benefits of Laser-Cutting Copper?
Though there may not be one overall best way to cut copper, laser cut copper can be beneficial to the end user and manufacturers. Laser cutting generally is faster than other methods because there is no tooling required or extensive set-up. The laser process allows for multiple iterations to be cut, thus advancing the progress of R&D and product development. Laser cut copper will be favorable in handling of extremely thin copper sheets or foils. Laser cutting copper offers a distinct advantage over traditional manufacturing methods due to its exceptional precision and versatility. As there are many options available to OEMs to get their precision components made, the following list is provided to review these benefits of laser cut copper such as:
- Material Versatility: Copper and other materials can be come in extremely thin gauges. Laser technology is a non-mechanical process that results in precision components made from foils as thin as 0.0127mm. Copper can also be cut with an adhesive layer, that other methods cannot cut without damaging the adhesive.
- Design Flexibility: Laser cut copper can be provided as simple washers and shims to complex gaskets and mesh configurations. Laser technology of copper excels at providing highly accurate 2D profiles.
- Rapid Laser Cutting: Copper components are used in numerous industrial applications and supporting the growth and development of these requires rapid turn-time. The ability to switch from different gauges is done by adjusting the laser settings and placement of the new material on the laser bed.
- Minimal to Maximum Quantities: The process of laser cutting enables manufacturers to support minimal quantity requests and support high volume manufacturing.
- Material Utilization: This material friendly method maximizes material usage by nesting of the selected components. The process allows for even smaller non-standard sheet sizes to be cut.
- Minimal Set-Up: The three main factors needed to laser cut copper are data, material, and quantity. Set-up of the data and material is fast compared to other methods and the selected quantities are completed.
- Repeatability Without Retooling: Recurring projects or ones that come every so often, can be processed by selection of the previous tool settings. These parameters include laser wattage, laser focus, laser dwell time, laser speed, laser frequency and others. These tools are saved indefinitely and do not wear out like mechanical tools can.
- Accuracy: Laser cutting, though not the most accurate manufacturing method, does support many critical industries like aerospace defense, medical device, satellite communications, energy, and nuclear development to name just a few. These industries not only choose laser technology for the benefits listed above, but the consistent accuracy laser cutting provides. When projects require laser cut copper, it can be accurate as +/- 0.0127mm. This accuracy is repeatable and subject to levels of quality conformance like AQL, Six Sigma, 100%, all under Quality Management Systems like ISO 9001, AS9100, TS 16949 and others.
In conclusion, laser cutting copper offers a superior solution for precision manufacturing due to its exceptional accuracy, versatility, and efficiency. Its ability to create intricate designs, minimize waste, and reduce lead times makes it an asset for industries ranging from electronics to automotive components. By embracing laser cutting technology, businesses can enhance their product quality, improve their bottom line, and stay competitive in today’s demanding market.
Why Cutting Copper Can Be Tricky
Thermal Sensitivity: Copper’s high thermal conductivity poses challenges during traditional cutting methods. A-Laser’s advanced technology tackles this head-on, minimizing heat-affected zones for pristine results.
Reflectivity: Copper’s reflective nature can be a stumbling block for some laser systems. Fear not. A-Laser’s expertise and cutting-edge solutions navigate the reflective labyrinth with ease.
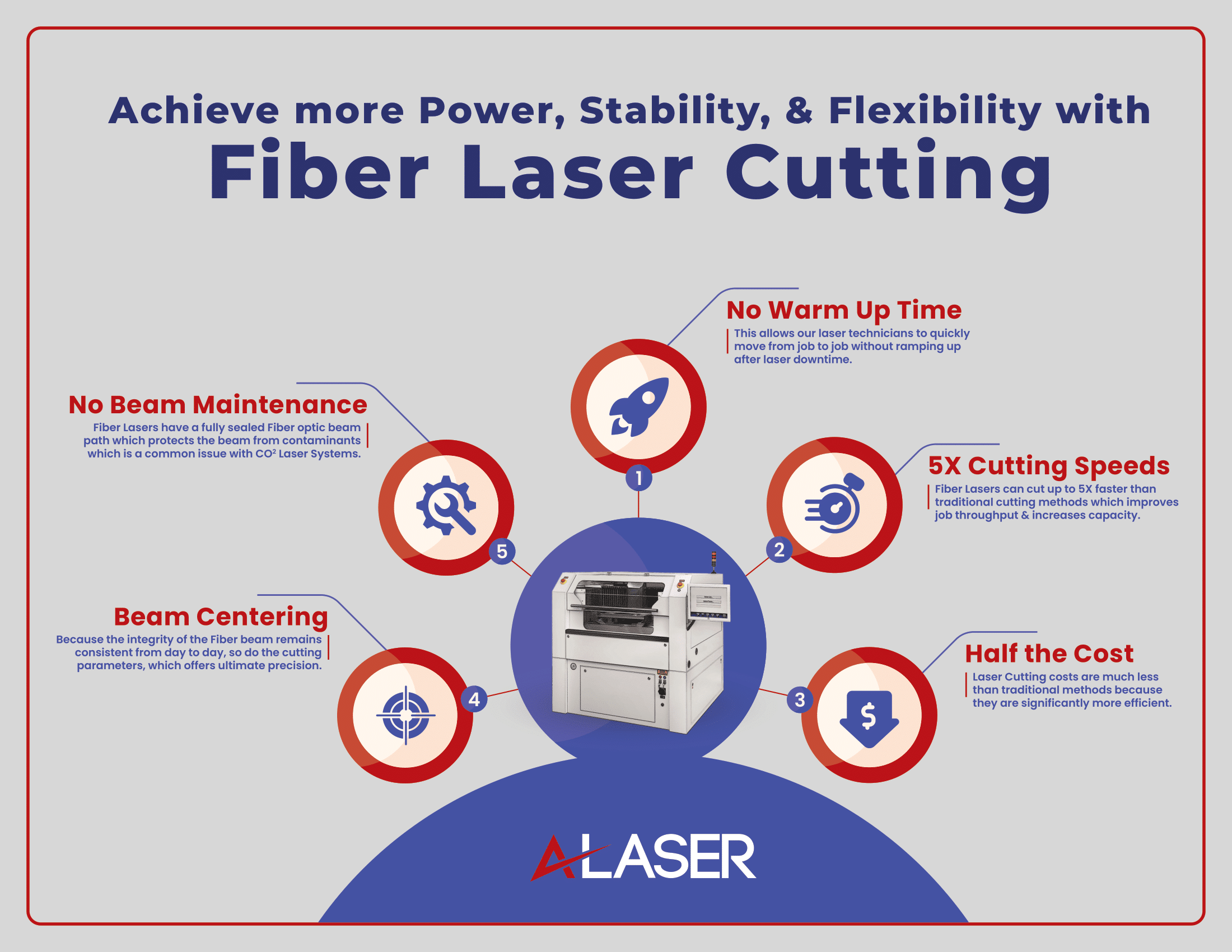
Tailored Solutions: UV and Fiber Laser Technology
UV Precision: For intricate designs and tight tolerances, A-Laser offers UV laser technology. This precise method is ideal for projects (typically under 20 mil), demanding the utmost accuracy, ensuring your copper creations are a cut above the rest.
Fiber Flexibility: When versatility is key, our fiber laser technology takes the stage. For projects dealing with copper sheets with complex designs, A-Laser adapts to the unique demands of your copper cutting needs.
The Power to Transform: Cutting Thicknesses with Precision
Fine Tuning for Success: A-Laser recognizes that not all copper is created equal. Our technology adjusts its power to cut through different thicknesses with precision, providing optimal results without compromising efficiency.
Powering Through: From thin foils to substantial sheets, A-Laser has the power to transform copper into the masterpiece you envision. Trust in our technology to handle the spectrum of copper cutting requirements.
Optimizing the Process: How to Successfully Laser Cut Copper
Fine-Tuning for Success: The heart of successful copper laser cutting lies in meticulous optimization. A-Laser provides a guide to the essential parameters ensuring optimal results:
-
Laser Power: Tailor the power to the copper thickness to ensure efficient cutting without compromise.
-
Cut Speed: Maintain a cut speed of 85-90% of the maximum allowed to keep the workpiece heated and non-reflective, ensuring continuous, uninterrupted cutting.
-
Point of Focus: Optimize the focal point for maximum energy density, achieved through different optical lenses and adjustments to the distance between the lens and the worktable.
-
High-Pressure Oxygen Gas: Elevate efficiency by using pressurized oxygen gas (100-300 psi), creating copper oxide that lowers reflectivity.
A-Laser Advantage: Where Expertise Meets Innovation
Comprehensive Expertise: Navigating the complexities of copper cutting demands more than technology; it requires expertise. A-Laser’s team of dedicated experts ensures that every project, regardless of intricacy, is met with the highest standards of precision.
Innovation at its Core: A-Laser doesn’t just adapt; we innovate. Our commitment to staying ahead of industry challenges places us at the forefront of technology, ensuring you experience the best in copper cutting innovation.
Elevate Your Copper Cutting Experience with A-Laser
Whether it’s overcoming thermal challenges, conquering reflectivity issues, or mastering the intricacies of different thicknesses, A-Laser stands as your partner in precision. Choose A-Laser for Laser Cutting Copper and witness the seamless fusion of expertise and innovation.