Tumble Deburring
Metal parts often undergo a variety of processes to achieve the desired finish and functionality. Among these, deburring plays a crucial role in ensuring the quality and performance of metal components. At A-Laser, we understand the importance of precision and efficiency in deburring, which is why we’re here to shed light on the different types of metal tumbling and deburring processes.
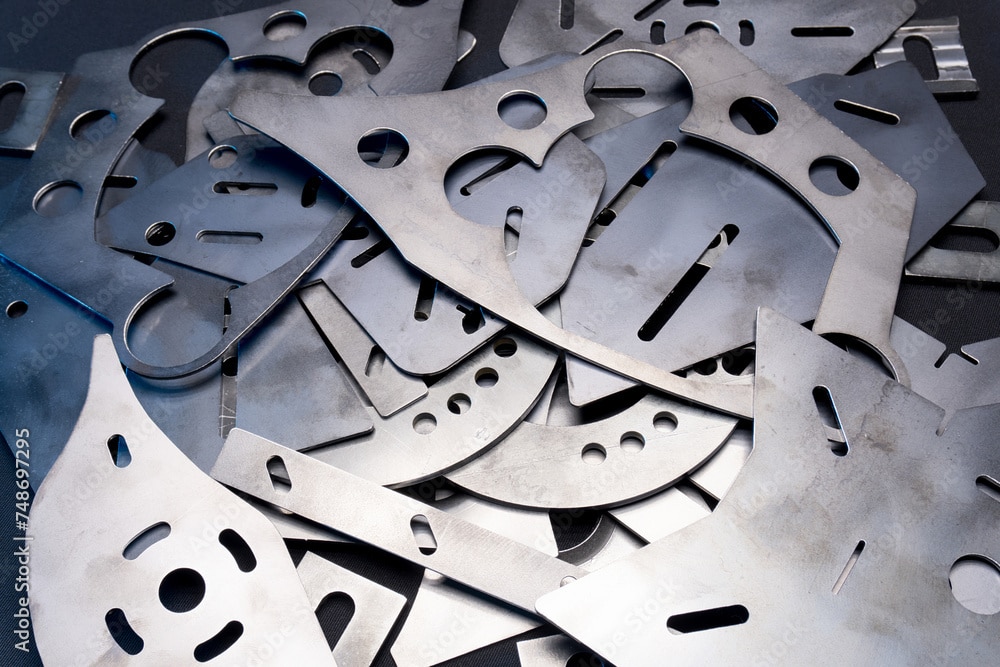
What is Deburring?
Deburring is a machining process used to remove unwanted burrs or sharp edges from metal parts, resulting from manufacturing processes such as cutting, machining, milling, drilling, or stamping. These burrs not only compromise the aesthetic appeal of the parts but can also affect their functionality and safety. Deburring helps in achieving smooth surfaces, precise dimensions, and improved overall quality.
Types of Metal Tumbling and Deburring:
Barrel Tumbling:
- Barrel tumbling is one of the most common methods used for deburring metal parts. In this process, the parts are placed inside a rotating barrel along with abrasive media, such as ceramic chips or abrasive stones. As the barrel rotates, the abrasive media continuously rub against the parts, removing burrs and imparting a smooth finish.
Advantages of Barrel Tumbling:- Suitable for small to medium-sized parts.
- Cost-effective for large production runs.
- Provides consistent results with minimal manual intervention.
- Can be used for a wide range of metal materials and shapes.
- Applications of Barrel Tumbling:
- Deburring edges and surfaces of machined components.
- Smoothing out rough surfaces on stamped or punched parts.
- Preparing parts for further finishing processes such as coating or painting.
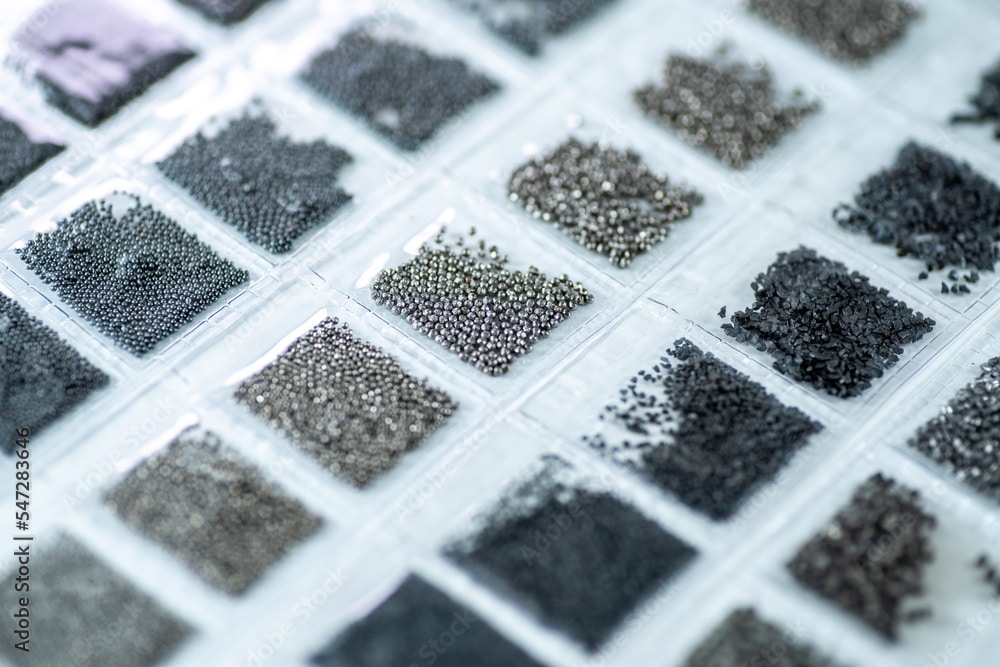
Vibratory Tumbling:
- Vibratory tumbling employs a similar principle to barrel tumbling but uses a vibrating tub or bowl instead of a rotating barrel. The vibration causes the abrasive media and parts to move in a tumbling motion, effectively deburring the surfaces.
Advantages of Vibratory Tumbling:- Ideal for delicate or intricate parts.
- Provides faster deburring compared to manual methods.
- Offers greater control over the deburring process parameters.
- Can achieve smoother surface finishes.
- Applications of Vibratory Tumbling:
- Deburring small, intricate parts with complex geometries.
- Polishing surfaces to improve aesthetics.
- Removing rust or corrosion from metal components.
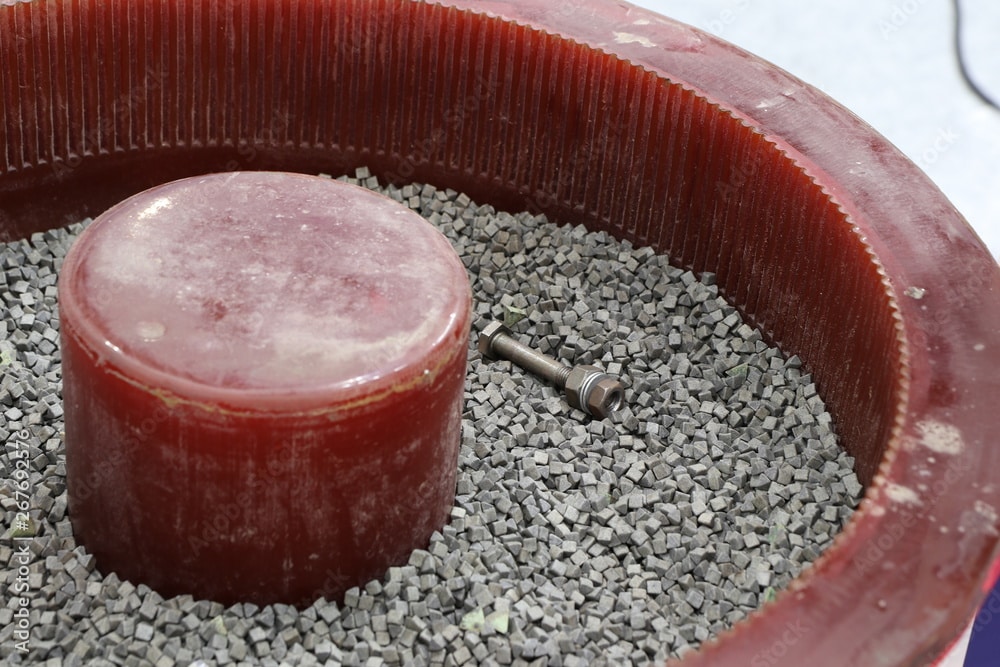
Centrifugal Tumbling:
- Centrifugal tumbling involves placing the parts and abrasive media inside a rotating drum or bowl, which spins at high speeds. The centrifugal force generated during rotation forces the abrasive media against the parts, resulting in efficient deburring.
Advantages of Centrifugal Tumbling:- High-speed deburring for increased productivity.
- Suitable for parts with deep recesses or internal features.
- Can handle heavy burrs or thick coatings.
- Uniform deburring across all surfaces.
- Applications of Centrifugal Tumbling:
- Deburring precision components in aerospace or automotive industries.
- Removing scale or oxidation from metal surfaces.
- Achieving consistent surface finishes on mass-produced parts.
Metal tumbling and deburring processes such as barrel tumbling, vibratory tumbling, and centrifugal tumbling play a vital role in enhancing the quality, functionality, and aesthetics of metal parts. This is one of the final steps in manufacturing precision parts. If you have inquiries about laser cut parts and the finishing processes, please reach out to our team to discuss!