CO2 Lasers
Advancing Medical Treatments Through CO2 Technology
CO2 laser technology means that carbon dioxide gas is used to produce a concentrated beam of light. Prior to 1964 there were no CO2 laser systems until Dr. Kumar Patel, working for Bell Labs, invented the laser system. Initially the laser system produced was in the infrared wavelength of 10.6 nanometers and most CO2 laser in use today operate at wavelengths between 9.4µm to 10.6µm band. Many challenges needed to be overcome before Dr. Kumar could get a laser system to work such as how to inject energy into the CO2 molecules and be in a closed system that could control this energy. Through multiple tests and experiments, the solution was finally made. This new technology would be used to ablate human tissue in treatments. Over the next two decades as advancements in medical procedures moved along, CO2 lasers were refined for broader and more precise use in surgical procedures. By the 1980’s pulsed CO2 lasers were being developed to further control the laser beam for medical ablation of tissue at shallower depths and by the 2000’s Fractional CO2 laser technology was developed. This method splits the laser beam into microbeams and offers even greater control for numerous treatments of the skin for scars, wrinkles, that do not damage any surrounding tissue. CO2 laser technology has a great foundation for being a tool in the medical industry.
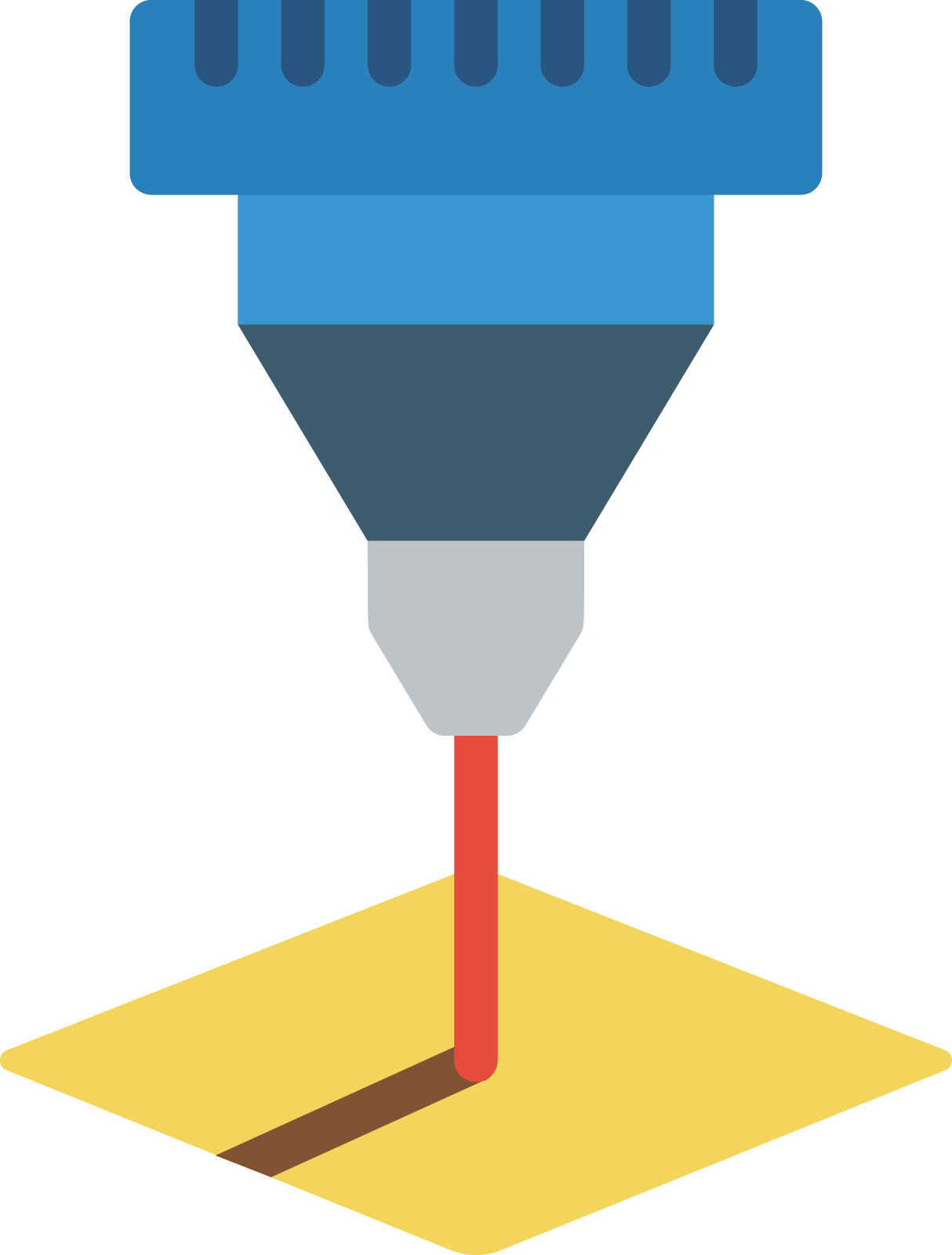
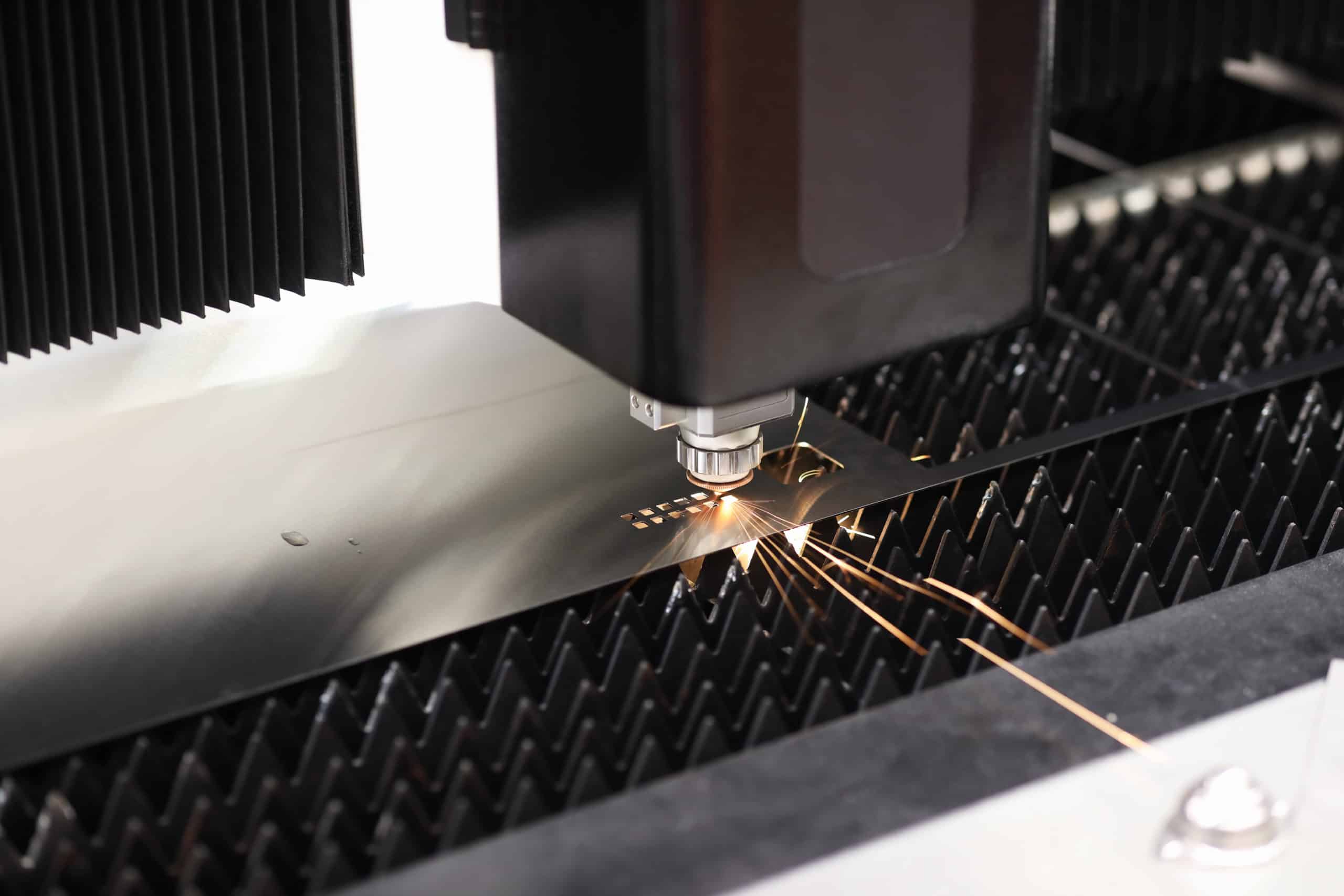
Manufacturing Industry Discovery of CO2 Laser Technology
It does not take long before any new technology to be harnessed by other industries and the same is true for CO2 lasers. As initially developed for medical procedure in treating cervical intraepithelial neoplasia removal, the manufacturing industry became aware of the laser technology that opened many more doors to discovery. By the late 1960’s, use of CO2 laser technology was limited due to the amount of power. The beam quality and the control systems allowed cutting, but in thinner materials, with less accuracy. The power source used was a mixture of CO2, nitrogen, and helium. This mixture would be contained in a vacuum tube which would hit with an electrical discharge to excite the molecules to produce the laser beam. The CO2 laser technology back in the late 1960’s to early 1970’s was crude by today’s standards, but these early systems resulted in new ways of cutting and engraving materials for the automotive, aerospace and electronics industries.
Over the decades, CO2 laser technology has undergone significant improvements, with advances in power, beam quality, control systems, and optical components. However, CO2 laser technology is heavily relied upon for the cutting and marking of non-metallic materials. There are CO2 laser systems with high power, but when compared to Fiber laser technology, the difference is dramatic. For example, a 4KW CO2 cutting16 GA Mild Steel using N2 as a cutting gas has a recommended cutting speed of 260 IPM. A fiber laser of equal power has a cutting speed of about 1,417 IPM. The significance in speed puts the advantage towards fiber laser technology. The inverse in this is that fiber lasers cannot cut non-metallic materials, they process with too much energy and burn and melt plastics. CO2 laser systems are made with powered by systems from 40 watts to ones in the kilowatt range. CO2 lasers are typically provided with an output power rating by the manufacturer. Some are classified as high-power lasers, with emitting continuous 60 kW (6000 W) beams for example. The laser’s power typically determines its application; for example, a high-power laser is most suitable for cutting and welding, while a lower power device can be used for marking barcodes and labels.
They can be categorized into three groups such as:
- Low Powered: Suitable for fine engraving, marking, and micromachining tasks.
- Medium Powered: Hundreds of watts to a few kilowatts are commonly used for cutting and engraving a variety of materials, including wood, acrylic, and some metals.
- High Powered: Several kilowatts or more can cut thicker materials, such as metals and composites, and are often used in industrial settings for large-scale production.
Regarding laser safety, the Center for Devices and Radiological Health (CDRH), which is a division of the US Food and Drug Administration (FDA), has classified CO2 lasers as Class 4.
- High powered lasers (visible or invisible).
- Acute eye and skin hazard intrabeam, specular and scatter conditions.
- Non-beam hazard (fire, toxic fumes, etc.)
The beam diameters of CO2 lasers can range from 1-5mm, and then are focused down to diameters of 0.025mm to 0.25mm using special focused techniques and lenses. With a wide range of capabilities, CO2 laser technology has given manufacturers the ability to specialize in providing laser engraving, laser ablation and cutting of a host of materials for countless applications.
Diverse Industry Applications
To better understand how CO2 lasers have grown in popularity over the past 5 decades, the following table highlights applications of this diverse technology.
Industry | Material | Component Type |
---|---|---|
Aerospace | Sheet metal, plastics: acrylic, ABS, polycarbonate, nylon | Laser Marking, interior components, cutting of sheet metals and welding. |
Medical | Plastics: ABS, polycarbonate ,PEEK, and other non-metallic materials | Laser Marking of part numbers and nomenclature. |
Textiles | Fiber materials, paper, plastics | Cutting and surface treatment of materials. Microperforations. |
Automotive | Sheet metal, plastics like ABS, polycarbonate, metal. | Engraving of part numbers, micro perforations on materials. Cutting and welding of sheet metals. |
Food Industry | Plastics, food products like eggs, fruit, cheese and cured meats | Engraving of nomenclature on eggshells, cheeses, laser peeling of fruits and vegetables. |
Packaging Industry | Cardboard, paper, plastics | Laser welding of plastic bags, logo marking on products, microperforation of plastic bags |
CO2 laser technology has come a long way regarding plastic cutting machine technology from its invention back in 1964. With the growth of electronics that support controllers, sensors, power regulators and so on, have allowed CO2 laser technology to adapt to the needs of manufacturers. There are other laser system types available to manufacturers such as fiber lasers, YAG lasers and excimer laser technology. Like CO2 technology, these also have capabilities that best suited for. For CO2 laser systems, the ability to cut and engrave on plastics is foremost in processing. Bringing reliability with precision and efficiency has made this laser technology a cornerstone of industries such as automotive, aerospace, electronics, medical, and textiles. As technology continues to advance, laser manufacturing will continue to have a significant role in shaping the future product design and innovation.