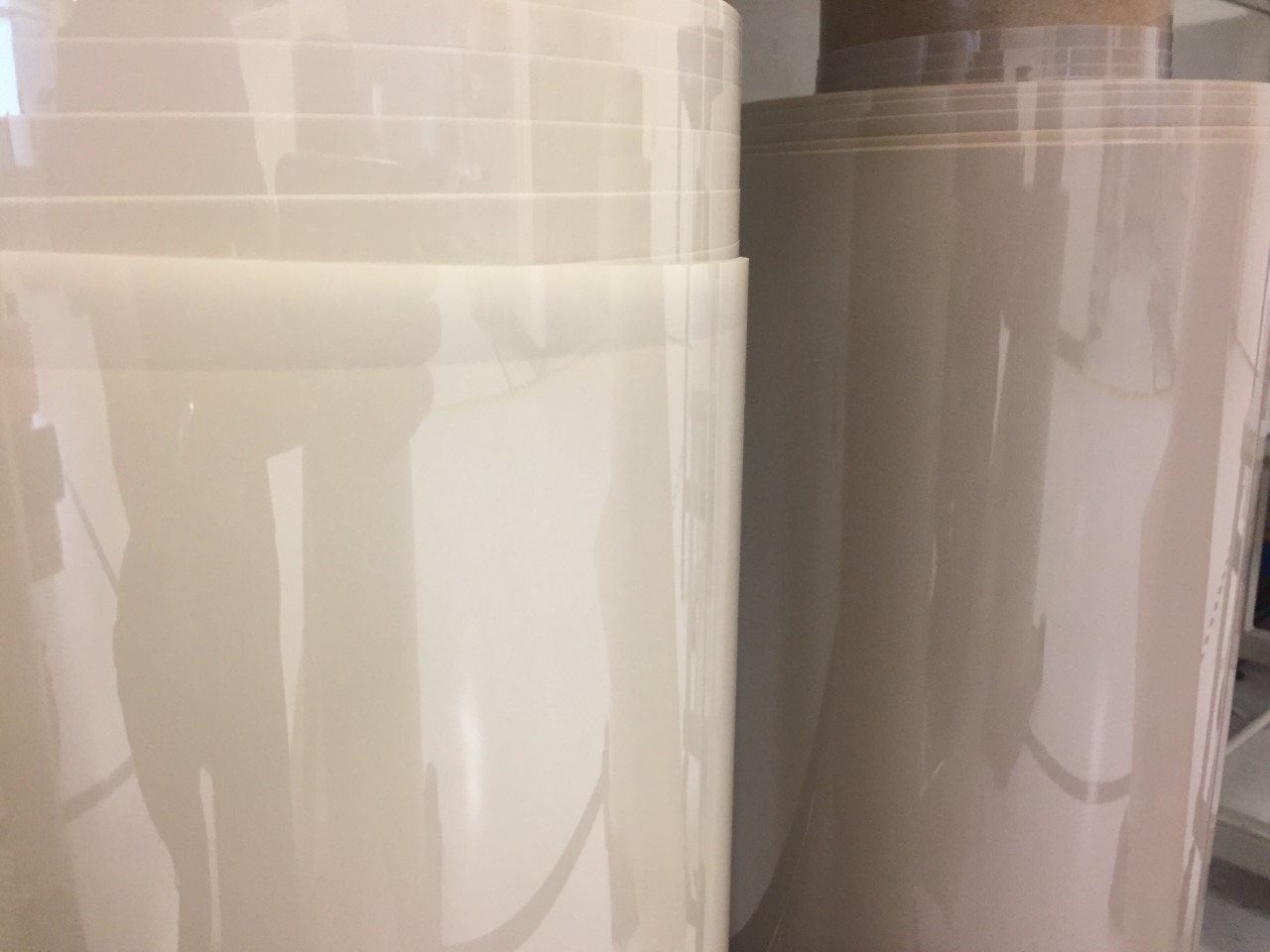
PEEK Plastic Advantages
Imagine you’re an engineer designing a cutting-edge medical implant. You need a material that’s strong, lightweight, and can withstand the human body’s internal environment. PEEK seems like the perfect fit, but conventional machining methods struggle with its unforgiving nature.
So, what exactly is PEEK? PEEK stands for Polyetheretherketone, and it is a popular thermoplastic polymer. Its exceptional thermal stability, chemical resistance, and mechanical strength make it an excellent solution where compromise is not an option. Let’s take a deeper look into this material – What are its applications, and why does its versatility present such a challenge on the machining front?
What is PEEK plastic used for?
PEEK plastic stands as a cornerstone material in the realm of advanced engineering, offering a wealth of applications that span across industries and disciplines. Its versatility is truly remarkable, allowing it to seamlessly integrate into a diverse array of cutting-edge technologies and innovations.
Consider its role in aerospace engineering, where PEEK components serve as the backbone of mission-critical systems. From lightweight structural elements to intricate components within propulsion systems, PEEK’s exceptional thermal stability and resistance to harsh environmental conditions ensure optimal performance in the most demanding of aerospace applications.
In the realm of medical technology, PEEK’s unique properties take center stage, driving innovation in life-saving devices and surgical instrumentation. Its biocompatibility makes it an ideal candidate for implants and prosthetics. Furthermore, its electrically insulating nature makes it invaluable in medical devices such as MRI machines, where precision and reliability are essential for patient care and diagnostics.
Beyond aerospace and medicine, PEEK continues to revolutionize industries such as automotive engineering, electronics manufacturing, and beyond. Its lightweight yet robust nature makes it an ideal choice for reducing weight in automotive components without sacrificing durability, leading to improvements in fuel efficiency and performance. Similarly, in electronics manufacturing, PEEK’s exceptional electrical insulation properties make it an indispensable material for high-performance electronic components, ensuring reliability and longevity in demanding environments.
In essence, PEEK’s wide-ranging applications are a testament to its remarkable versatility and adaptability. From the depths of space to the inner workings of the human body, PEEK plastic continues to push the boundaries of what’s possible in modern engineering and design, driving innovation and shaping the future of countless industries.
Is PEEK Difficult to Machine?
It’s a question that often arises in the manufacturing world, particularly among those tasked with shaping this high-performance polymer. The answer? Yes, PEEK can pose challenges in machining. The very qualities that make PEEK unique and highly desirable also render it challenging to work with. Its exceptional strength, coupled with a high melting point, sets it apart from conventional materials and demands specialized approaches.
- High Melting Point: Unlike some plastics that soften under a drill or milling bit, PEEK boasts a high melting point. This can be problematic. The heat generated during machining can cause the PEEK to melt around the cutting area, leading to unwanted deformation and compromising the final part’s precision and overall quality.
- Abrasive Nature: PEEK is quite abrasive on cutting tools. This can cause them to wear down quickly, reducing their lifespan and potentially causing inconsistencies in the machined part.
Machining PEEK using traditional methods may result in issues like tool wear, heat-induced deformations, and surface irregularities. These hurdles can frustrate machinists striving for precision and efficiency in their processes.
But what can be done about it? Thankfully, there are solutions. Machinists and engineers have devised specialized tools and techniques tailored to the unique properties of PEEK. By understanding its behavior under different machining conditions, they can optimize cutting parameters and tool geometries to mitigate challenges and achieve desired outcomes. Additionally, advancements in machining technology continue to offer innovative solutions, pushing the boundaries of what’s possible with PEEK.
So, where does this leave us? The difficulty in machining PEEK underscores the need for creativity and problem-solving in manufacturing. Rather than viewing it as an obstacle, manufacturers can see it as an opportunity for innovation. By embracing the challenges posed by materials like PEEK, they can discover new techniques and technologies that enhance efficiency. While PEEK can be traditionally machined with the right expertise and considerations, laser cutting offers a more efficient and precise alternative.
What is laser cut PEEK?
Laser cut PEEK refers to the process of shaping or fabricating PEEK plastic using laser technology. In this method, a high-powered laser beam is precisely focused onto the surface of the PEEK material, causing localized heating and vaporization. This controlled application of heat allows for precise cutting, engraving, or marking of the PEEK material, with minimal risk of damage or deformation.
Laser cutting offers several advantages for working with PEEK. It allows for intricate designs, tight tolerances, and clean edges, making it suitable for producing complex components with high precision. Additionally, laser cutting is a non-contact process, meaning there is no physical tool contact with the material, reducing the risk of contamination and minimizing material waste.
Overall, laser cut PEEK represents a versatile and efficient method for shaping PEEK plastic into various forms and configurations, enabling manufacturers to harness the full potential of this high-performance material in their applications.
In the ever-evolving landscape of manufacturing, PEEK continues to captivate with its versatility and resilience. While its unique properties present challenges in machining, laser cutting technology offers solutions where precision and innovation converge seamlessly. With each precise cut and intricate design, laser cut PEEK propels us forward, reshaping industries and inspiring new frontiers of possibility.
What are the Advantages of Peek?
Often when speaking of materials used in industrial applications we think of metallic materials like steel, aluminum, titanium, tungsten and so on.
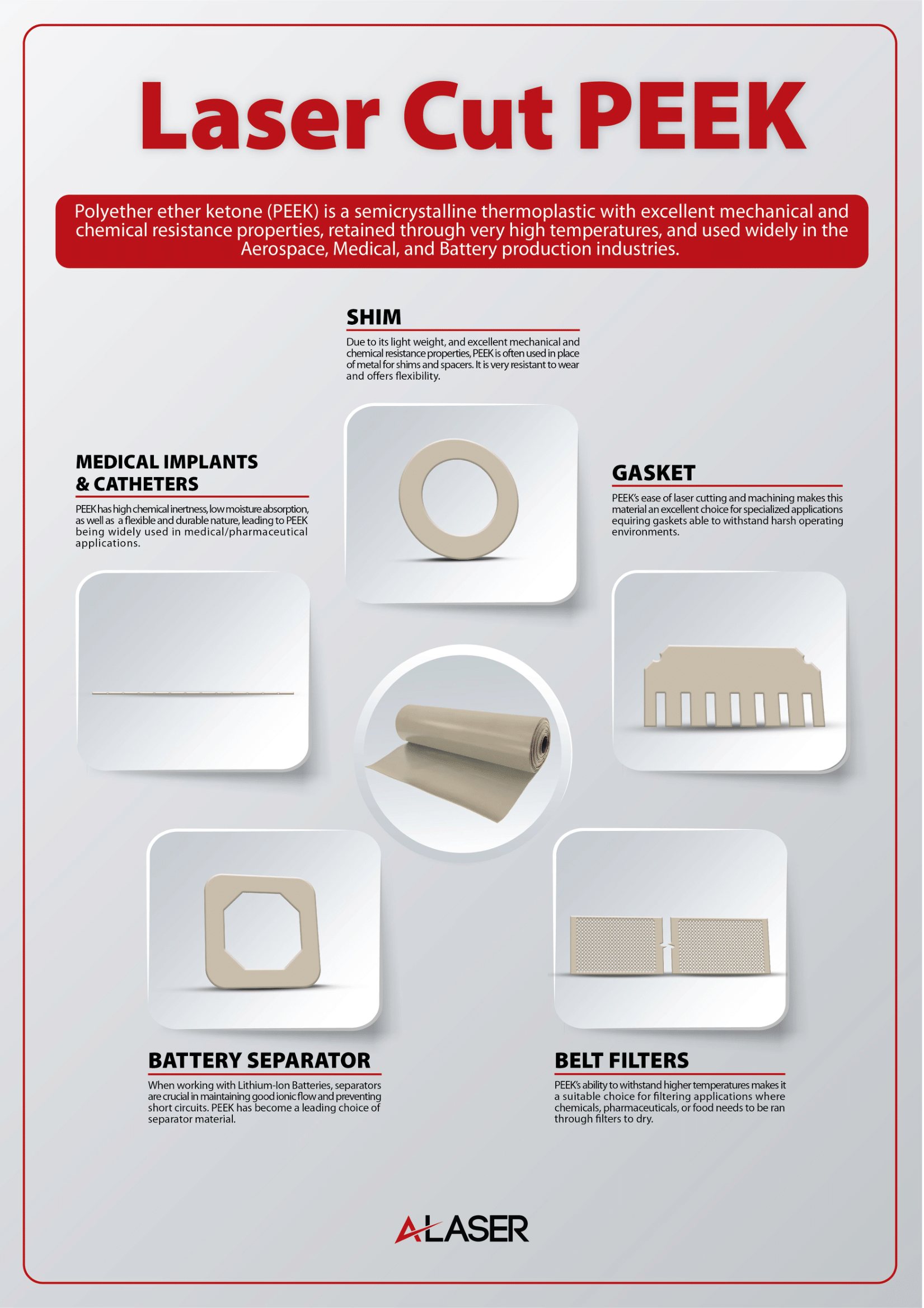
However, polymers like PEEK are used for industrial seals and gaskets to use in the medical industry. PEEK or Polyetheretherketone, is a material that can be laser cut well under the UV laser spectrum and chosen for characteristics such as chemical resistance and mechanical properties that make it an excellent candidate for numerous applications. PEEK plastic has a melting point of (343 °C / 649.4 °F) compared to most other thermoplastics. This enables PEEK to be laser cut into fine precision components. PEEK can also be molded and formed into PEEK sheets, raw blocks, rods, and tubes. This versatility gives PEEK advantages to its use such as:
- Chemical corrosion resistant: PEEK is resistant to bases, organic solvents, and acids. Use of PEEK precision parts in these types of conditions would be ideal.
- Great strength and durability are advantages to using PEEK as it has a strength to weight ratio like aluminum and thus 70% lighter than steel
- PEEK precision parts have reduced friction and are a good choice for sliding applications of components. Complemented with the strength to weight ratio, this improves efficiency and keeps costs down during manufacturing.
- PEEK plastic is also biocompatible and is a favored material for medical implants and device housings that are in contact with human tissue.
- PEEK is resistant to peeling and compared to other thermos plastics has very good flame-retardant qualities.
- It can be used in application for imaging because of its radiolucency.
- As mentioned with a melting point of (343 °C / 649.4 °F), PEEK precision parts will retain their integrity and stability in conditions where physical or chemical harsh conditions would affect metallic alloys.
PEEK plastic was invented back in 1978 and was introduced to industry in the early 1980’s. Since then, the use of laser cut PEEK sheets, rod and tubes has brought many advantages to industries requiring a non-metallic material with high strength, machinability, and biocompatibility for medical, automotive, alternative energy and other industries. Laser cut PEEK plastic manufactured into gaskets, shims, bearings, medical implants and other precision components are advancing the demands of technology in partnership with qualified manufacturers.