Laser Process Steps The A-Laser Appraoch
Each project that we receive here is unique, and each one offers us a glimpse of the technical advances that our customers continue to make. The process and teamwork behind our high-quality satisfaction are integral to our success as a service provider and the high level of customer satisfaction that we provide. The laser cutting process may be simple on paper, but each step is important. It all begins from the moment we receive an inquiry and continues through to the shipment of the manufactured parts.
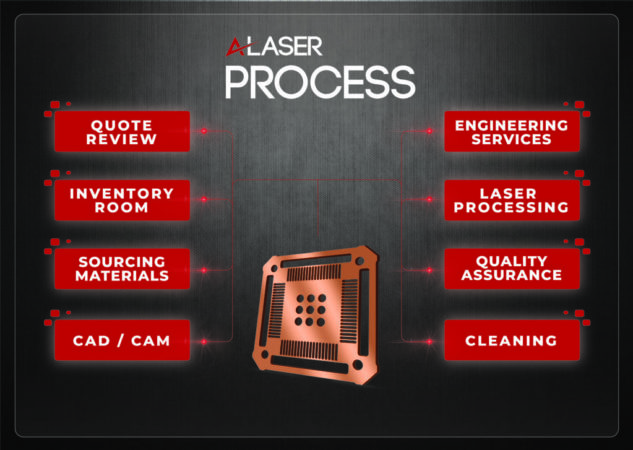
Quote Review
The first step of the Laser cutting process begins with a request. Any new RFQ (Request For Quote), goes through a Quote Review by CAD and Engineering staff. These teams carefully consider the geometry of the proposed project and how it will be cut, cleaned, inspected, packaged, and shipped, and flag any concerns they might have so that the A-Laser team can address them with the customer and determine the best way to move forward.
Material Selection
At A-Laser, we provide materials store in a controlled location at our inventory room as well as material sourcing. Although some customers may supply materials for a project, many cannot. Our account managers are very knowledgeable of the benefits and detriments of a wide variety of materials and can offer up materials and sometime alternative materials to best suit the customer’s needs.
Check out the extensive list of materials we process.
Laser Engineering & CAD
Our laser engineering allows for an in-depth evaluation of challenging projects. Our team’s expertise brings confidence and a creative approach to solving new material requirements and use of intricate geometries. Laser Engineering works in parallel with CAD and customer input, offering tremendous flexibility. Many of our customers’ growth has begun with support from our engineering team.
Laser Processing
Once an order is approved, the next laser cutting process step is a UV or IR laser system. The quote review will determine which system to use well before the project is scheduled and placed in the queue. These lasers are Class 1, NdYag UV or IR and are the technology used to cut very thin gauge materials from .0005” to .120”, from polymers to SS to FR4. Highly accurate to a +/- .001” mil, and depending on the size and geometry a +/- .0005” mils can be held.
The UV lasers have an extremely broad range of material types that they can cut while the IR lasers are great for cutting SS alloys from .004” up to .025”.
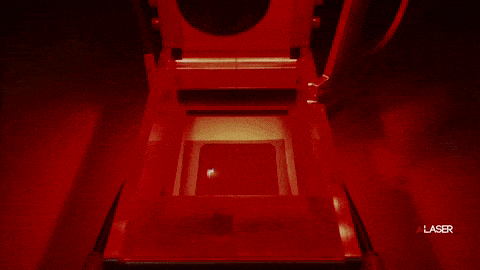
Quality Inspection
A-Laser is certified under ISO 9001-2015 and ITAR regulations and backed by our QMS. Our ability to measure and inspect up to 300x magnification is done by our use of OGP systems. Because .0125mm – .0254mm tolerances are often requested, our systems are designed to allow for critical inspection. Any non-conforming measurement is flagged and adjusted. This in turn is verified to ensure no errors have occurred. Providing these services has allowed A-Laser to support full production of AQL level projects.
Cleaning & Packaging
Finally, the laser cutting process is rounded out with cleaning and packaging. There are multiple levels of cleaning and packaging to make sure the final product is shipped safely and according to customer preference. Guidelines are needed per customer agreement. Included in this final process is packaging to quoted and agreed standards. Customer provided packaging is accepted but not required.