Stainless Steel Passivation
In the realm of metal finishing and surface treatment, passivation stands out as a crucial process, particularly for materials like stainless steel. Let’s dive into what passivation entails and why it’s important for stainless steel applications.
What Does it Mean to Passivate Metal?
Passivation is a chemical process aimed at enhancing the corrosion resistance of metal surfaces, primarily by forming a protective oxide layer. This layer acts as a barrier, preventing further oxidation and corrosion of the underlying metal. Typically, passivation involves immersing the metal in an acidic solution, such as nitric acid, which facilitates the formation of this protective oxide layer.
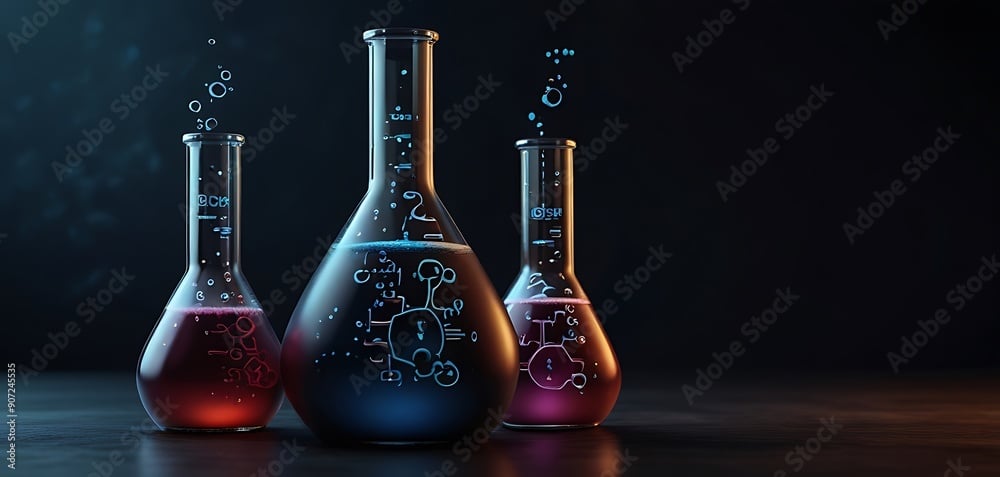
Why Does Stainless Steel Require Passivation?
Stainless steel is known for its resistance to corrosion, but it’s not impervious. During manufacturing processes like machining, welding, or forming, stainless steel surfaces can become contaminated with foreign particles or iron residues. These contaminants can compromise the inherent corrosion resistance of stainless steel by initiating corrosion sites.
Passivation of stainless steel is crucial to remove these contaminants and restore its protective oxide layer. By immersing stainless steel components in a passivating solution, any surface contaminants are dissolved, and a clean, homogeneous oxide layer is formed.
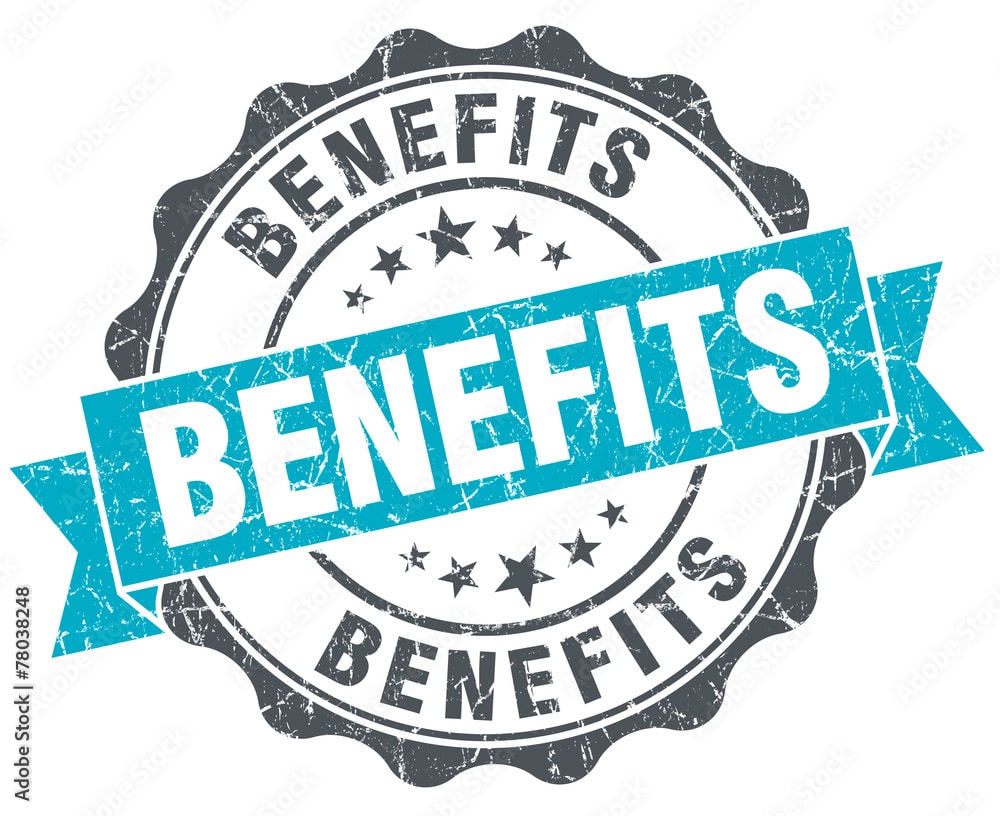
The benefits of the process include:
- Enhanced protection: This oxide layer not only enhances the aesthetics of stainless steel but also significantly improves its resistance to corrosion, ensuring longevity and performance in various applications that can compromise it, like fabrication (welding, grinding, cutting) and exposure to environmental factors (chemicals, extreme temperatures).
- Improved product quality: Passivation removes surface contaminants like free iron, which can contribute to rust formation. This ensures a cleaner and more uniform surface, enhancing the overall quality and appearance of the stainless steel product.
It’s important to note that passivation is not always necessary for stainless steel. However, it is often recommended for applications where corrosion resistance is critical, such as in:
- Medical equipment
- Food processing equipment
- Chemical processing equipment
- Marine environments
By understanding the concept of passivation and its role in enhancing the corrosion resistance of stainless steel, professionals can make informed decisions about when and how to utilize this process for optimal results.