Laser Drilling Services from A-Laser
Laser drilling is increasingly replacing mechanical drilling methods. With the benefits of speed, accuracy, cleaner cuts, and less debris — not to mention reduced mechanical stress on delicate components — laser drills offer huge advantages for electronics manufacturers.
Before laser drilling, manufacturers relied on mechanical drill machines for all of their hole-making needs, whether it was drilling cooling holes or creating tiny microvias in PCBs.
As products and components became smaller, however, the drawbacks to traditional mechanical drilling grew. These included mechanical stress, messy debris to clean up, rough edges, and limitations on how small the holes could go.
In short: the industry needed a hero. This is where laser drills come in to save the day.
Why Laser Drilling Beats Other Methods
With laser drilling, you never have to worry about drill bit wear or break off. The process is clean and free of debris. Edges are consistently sharp, which allows for ideal copper plating, and most importantly, the sheer speed of laser drilling is much faster than mechanical drills.
Lasers also drill small holes very precisely and can be used with hard-to-cut materials, such as ceramics and gemstones, as well as most metals. They’re also ideal for drilling vias as small as 40 microns in diameter.
Our Laser Drilling Process
When you’re choosing a laser cutting partner to work with, consider your project’s demands in terms of beam quality, wavelength, intensity, pulse duration, and pulse repetition rate. Our engineers can take a look at your project and help you make an informed decision.
With our new LPKF Microline laser system, we can give you the best quality drills with phenomenal lead times. LPKF lasers are able to drill in the following materials:
Solder mask:
This is the layer that you see typically as green. It is placed over the top of the copper layer as a way to insulate the copper traces. This prevents accidental contact with other metals or conductive bits. This ensures that the right places are soldered properly. Typically, you will see green or red solder masks.
Silkscreen:
This is the white layer that you see on top of the solder mask. This is what allows your board to have symbols like letters and numbers. This is added in as a way to better understand the different areas of the board.
Substrate or FR4:
This is the base material of the board, often being fiberglass. This is how the board stays rigid yet flexible. Printed circuit boards can have different thickness levels, but generally will be about 1.6mm. If you have a cheap PCB board on your hands, it will smell when you try to solder to it and it will not be flexible at all.
Copper:
The next layer is a thin copper foil which is laminated to the board using heat and an adhesive. PCBs can have anywhere from one to sixteen layers of copper and the copper thickness may vary.
We know how critical tolerance is to high-end medical, aerospace, and military applications. We meet this need by providing laser cut parts within .0005″ (12 micron) tolerances.
The motion system used on our UV laser systems is second to none in the industry, remaining stable year after year to ensure that the last batch is just as accurate as the first.
Laser Drilling as an Alternative for Via & Microvia Drilling
Much like actual cities where streets and roads connect buildings together, ICs on a board are connected to each other with copper traces. And just like any metropolitan city, urban expansion tends to move vertically instead of horizontally, but instead of multi-story buildings, we get multilayer boards.
Vias are copper-plated holes spanning through the different layers of a given board or panel. They are the entrance locations to the subway stations, if you will. Having those multilayer boards has enabled electronic design to minimize the size of boards immensely without compromising on the complexity.
The holes for component leads and contact points are drilled into the board using “via drilling”. This type of drilling was traditionally done using a drilling machine, but more and more manufacturers are turning to laser machines.
Prior to automated computer software, the board was made using point-to-point wiring and a drill press, which was not only tedious to design and wire but led to a lot of short circuits and wire junction failures. With the advent of automated laser drilling machines, the thousands of holes that are in each board, are drilled at a rapid rate without the need for point-to-point wiring.
Vias can go through all layers of a certain board, or they can be between certain layers only and not through the entire stack up (blind vias). Since the signals move horizontally through the copper traces and vertically throughout the different layers through vias, you can think of vias as the Mario Bros tunnel entrances.
There are three ways that a board can be drilled through:
1.Through-holes
These connect all of the alternating layers of the board. This means that both the top and bottom layers, as well as the middle layers, are completely drilled through.
2. Buried vias
These connect the internal layers in a multi-layer printed circuit board. These drilled holes only connect the inner layers, never the exterior surfaces.
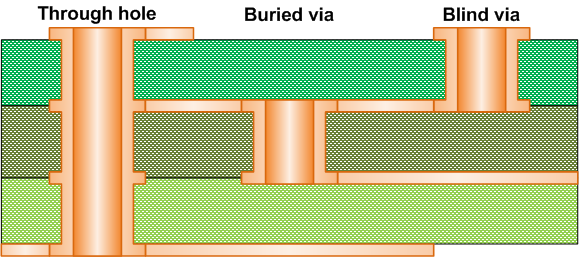
Image Source: ALLPCB
3. Blind vias
Lastly, these connect the top and bottom layers of the board to the internal layers but will not penetrate through the entire board.
The Challenge with Drilling Vias
The challenge with via drilling is that the laser must drill through the first layer without damaging the layer underneath. This is why automatic computer-aided drilling is such a popular option for PCB design. Because our laser machines work directly from CAD data, you can rest assured that the results will be accurate.
Although laser via drilling has a lower drill speed when compared to traditional mechanical drilling options, it has several advantages in that it can drill holes in circuitry that has a dense design and it allows a printed circuit board to be stacked in multiple layers reducing the need for one large single layer.
Additionally, lasers can be controlled in a precise manner so that the internal copper layers are not touched. Finally, when a laser is used via drilling, the positional accuracy of the laser and thus the holes are significantly better than other forms of traditional mechanical drilling.
For those who are interested in via drilling lasers, the UV Laser can drill through two hundred drill holes per second, whereas the UV Laser can do eighty drill holes per second. Typically companies will use the UV Laser combination as it has high flexibility when it comes to opening up the Cu surface of the board while maintaining a high drilling speed.
How can we help you?
Our customers not only save on product costs but also receive lower emissions tests, improved fuel efficiency and noise reductions. Laser cutting Kapton and other typical flex materials on UV lasers yields a virtually carbon free cut and burr-free edges that will ensure your contacts are clear and plating will take.
UV lasers operate at a very high power density, allowing us to vaporize the material in micron increments with a beautifully collimated beam of less than 20 micron diameter.
A-laser runs three shifts to make sure we stay ahead of capacity and are able to be responsive to the most demanding turn-around times. Our ability to support our entire laser cutting service customer base is a direct result of the team’s commitment to excellence in all aspects of the work from data prep to quality control.