Laser Micromachining Services Utilizing Infrared and UV Lasers
Developments in pulsed laser technology have made it possible to use micromachining on tiny devices, such as medical devices, with minimal damage to the surrounding material. With the rapid scientific advances in the laser field, A-Laser’s laser micromachining expertise is essential.
A-Laser specializes in the complex process of utilizing both infrared and UV lasers. Infrared lasers focus a beam on the surface of a material, which then converts to heat and melts the material. Ultra-violet lasers operate using ablation, which instantly removes materials by breaking the bonds directly. This process evaporates the material instantly with minimal heat effects. High-precision micromachining requires exact harmonization. Both the laser pulse train and a linear stage must be synchronized to ensure a precise control that is on target.
Laser Micromachining Services:
Laser Depaneling
rigid and flex boards
Laser Cutting
using customer provided designs
Laser Processing
Tubes, reels, and flat material stocks
Laser micromachining is the use of lasers for cutting, drilling, welding, or to make other material modifications to achieve features on the single or double-digit micrometer level. Laser machining can be done in three ways: direct writing, mask projection, and interference.
Pulsed vs Continuous Wave Mode
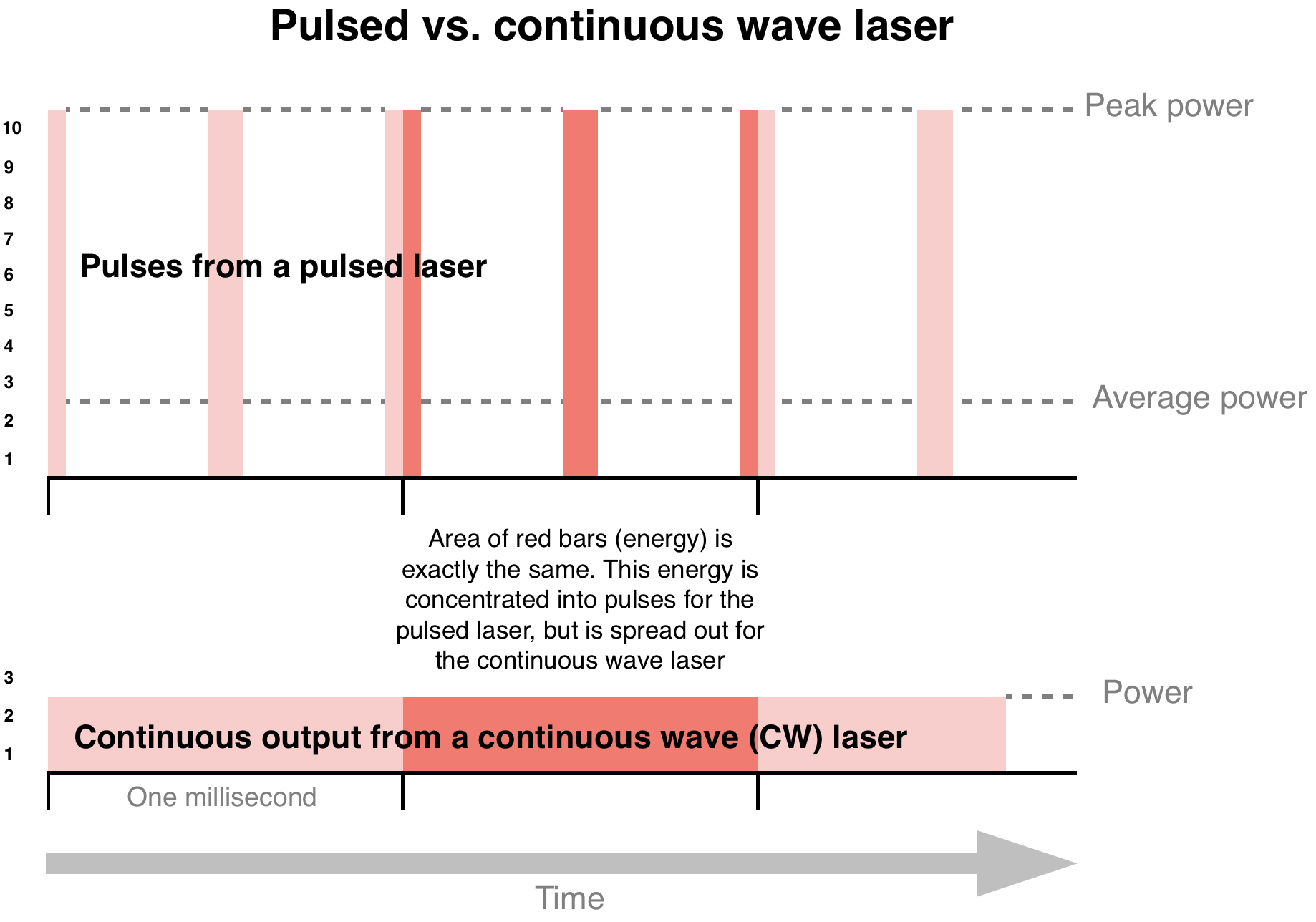
Image Source: ILDA.com
A vital part of laser micromachining is minimizing heat transfer to the area of the substrate that is adjacent to the micromachining material. Lasers can function in either the pulsed mode or continuous wave mode.
In the continuous wave mode, laser output is essentially constant with time.
In the pulsed mode, the laser output is concentrated in small pulses. Pulsed mode laser devices provide pulses with sufficient energy for micromachining a given material and small pulse durations. The small pulse duration minimizes heat flow to surrounding material.The length of the laser pulse can vary from milliseconds to femtoseconds.
The peak power is correlated to the duration of the laser pulse, so pulsed lasers can attain much higher peak values than continuous wave.
Laser machining primarily involves interaction that leads to ablation of the substrate material. The energy transfer that occurs is dependent on both material and laser properties. The laser properties that are factors include peak power, pulse width, and emission wavelength. Material considerations are whether or not it can absorb laser energy either by thermal and/or photochemical processes.
Why do pulse widths matter?
A-Laser cuts are clean and precise. The demand to make smaller, faster, lighter and lower-cost devices requires lasers that meet the challenge. Pulsed lasers are used for precision micromachining of various materials. The ability to produce varied pulse widths is key to precision, throughput, quality, and cost-effectiveness.
Nanosecond lasers use the same average power with a higher rate of material removal and therefore higher throughput than picosecond and femtosecond lasers.
Picosecond and femtosecond lasers melt material in order to remove it, through the processes of evaporation and molten material expulsion. This melting effects the precision and quality of machining since the material removed clings to the edges and re-solidifies.
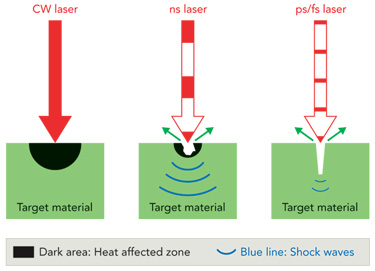
Image Source: Industrial-Lasers.com
Nanosecond vs. Picosecond vs. Femtosecond
Power vs. Precision vs. Price
The aim of laser processing in many cases is selective removal of material. Laser technology allows us to focus high amounts of energy in small areas. This is what leads to our precision processing. When removing material we must first over come the materials threshold. This threshold must be overcome by each pulse of the laser. Advancements in diode technology have enabled lasers to reach such energy levels in shorter pulses. These can be loosely banded into groups named Nanosecond, Picosecond and Femtosecond lasers. These names are representative of the units uses to measure the pulse period.
Why would this be a benefit?
There are a few reasons. One of the main ones is that with longer pulses the laser spends more time below the threshold. Thus adding more energy without doing the work of removal. This excess energy can alter the state of the material. This could be grain structure, physical state (solid or liquid), shape, flatness, or many more. These changes can lead to differences in reflectivity and absorption rates which greatly affect laser processing.
As the period decreases the frequency increases. This means more pulses at this high energy level. This generally leads to increased quality when cutting however does mean a relatively higher cost due to the advanced technology.
Power | Precision | Price | |
---|---|---|---|
Nanosecond | High | Medium | Medium |
Picosecond | High | High | High |
Femtosecond | High | Very High | Very High |
Laser Ablation
Laser machining primarily involves interaction that leads to ablation of the substrate material. The energy transfer that occurs is dependent on both material and laser properties. The laser properties that are factors include peak power, pulse width, and emission wavelength. Material considerations are whether or not it can absorb laser energy either by thermal and/or photochemical processes.
In thermal ablation, absorption of laser energy causes rapid heating. This increase in temperature results in melting and/or vaporization of the material. Thermal ablation may cause a large heat-affected zone, and is commonly observed with long wavelength and continuous wave lasers.
When the laser photon energy is greater than the bond energy of the substrate material, photochemical processes are observed. This occurs as the substrate material is vaporized because of bond disassociation that is induced by photon absorption.
If the substrate material is able to absorb higher amounts of laser energy, the laser ablation process is more efficient. Materials that are micromachined using shorter (femtosecond) laser pulses exhibit fewer thermal effects than those processed with longer pulse lasers.
Why A-Laser?
Lasers are effective in that they are extremely versatile and accurate, which allows our laser systems to reach a level of precision with the cleanliness of cuts like never before. Pulse width is also important to note as they can affect throughput and quality. Our lasers are equipped to deliver speeds of up to several hundred features per second. Before designing a tool, we conduct studies to ensure the best laser fluence. We are able to determine the ideal speed for each material and design, with minimal carbon redeposit. Our individual laser tool designs are unique for each material to assure the cleanliness and accuracy of each cut.
With the ever-changing and high-speed scientific developments in the laser field, A-Laser’s micromachining is crucial. Micromachining pulse laser technology protects the integrity of the substrate material while producing the desired results.