Laser Cutting Aluminum
Aluminum’s versatility, lightweight nature, and excellent strength-to-weight ratio make it a popular choice for various applications. When it comes to precise and efficient cutting, laser cutting reigns supreme. But how thick can you go, how much does it cost, and what are the best practices? This guide answers all your questions about laser cut aluminum.
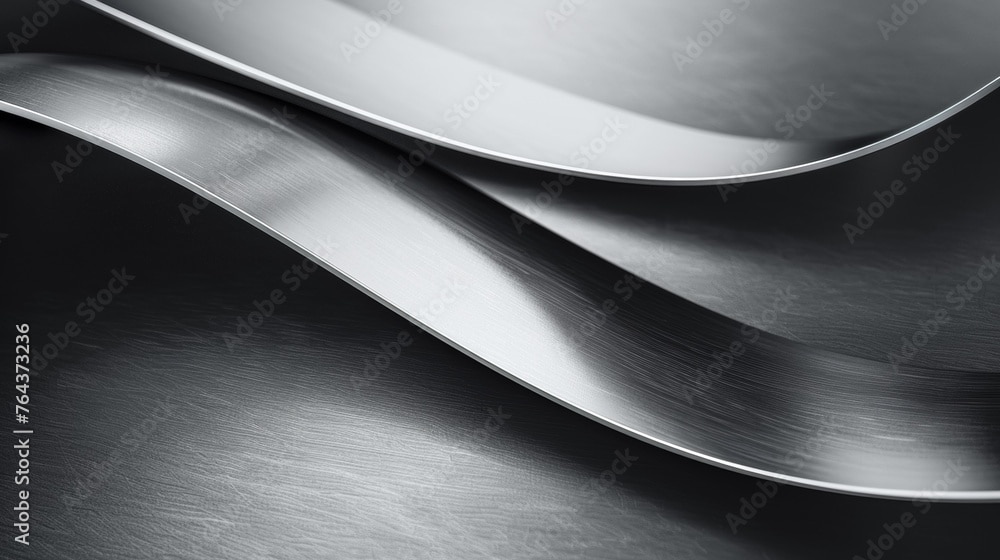
How Thick Can You Laser Cut Aluminum?
The maximum thickness achievable depends on several factors, including:
- Laser wattage: Higher wattage lasers can melt and vaporize thicker (greater than ¼ inch) materials.
- Aluminum alloy: Different alloys have varying melting points and heat conductivities. For instance, 5052 aluminum is commonly cut up to 1/2 inch, while 6061 can reach up to 3/4 inch with high-powered lasers.
- Cut quality requirements: Thicker cuts may have wider kerfs (the material removed by the laser) and rougher edges. For critical applications, thinner sheets with tighter tolerances are preferred.
How Much Does It Cost to Laser Cut Aluminum?
Laser cutting costs depend on several factors:
- Material thickness and size: Thicker and larger sheets require more laser power and time, increasing the cost.
- Complexity of the cut: Intricate designs with tight curves and small features take longer to cut, impacting the price.
- Volume and turnaround time: Larger quantities and faster turnaround times often qualify for discounts.
Examples:
- Simple shapes cut from 0.025″ thick 5052 aluminum sheet might cost around $0.50 per square inch.
- Complex designs cut from 0.25″ thick 6061 aluminum sheet could range from $1.50 to $3.00 per square inch.
However, for a more accurate quote tailored to your specific project, feel free to reach out to our team.
Tips for Laser Cutting Aluminum:
- Provide high-quality vector files: Ensure your designs are in a format compatible with laser cutting software, like DXF or AI.
- Choose the right aluminum alloy: Consider the required strength, corrosion resistance, and other properties for your application.
- Optimize your design for laser cutting: Minimize sharp corners, small features, and unnecessary details to reduce cutting time and costs.
- Material Preparation: Ensure the aluminum sheet is clean and free from any debris or contaminants to achieve the best cutting results.
- Optimize settings: Adjust laser power, speed, and frequency settings according to the thickness and type of aluminum being cut.
- Use assist gasses: Utilize assist gasses like nitrogen or oxygen to improve cut quality and prevent oxidation on the cut edges.
- Regular maintenance: Keep the laser cutting machine well-maintained, including cleaning the optics and replacing worn-out parts, to ensure consistent performance.
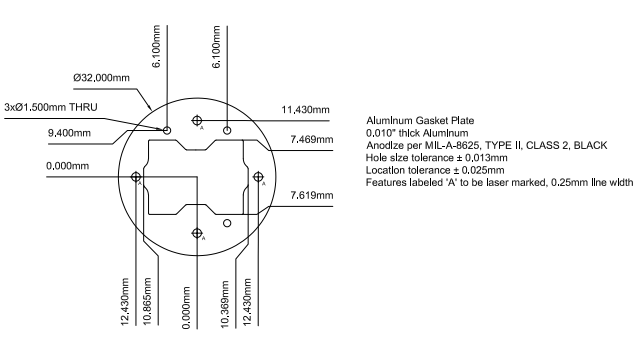
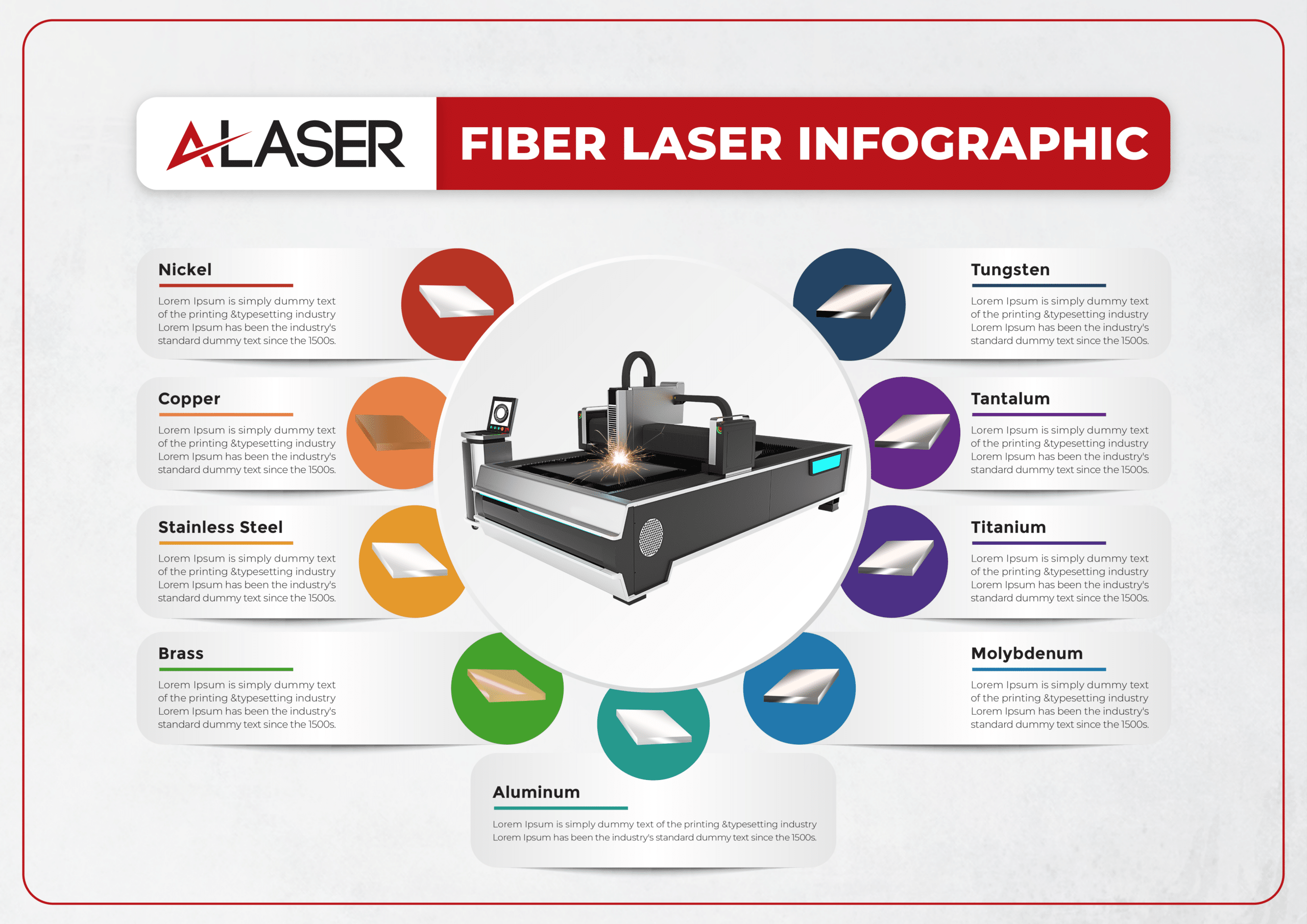
What is the Best Laser to Cut Aluminum?
The “best” laser depends on your specific needs and budget. Generally:
- CO2 lasers: Ideal for thinner aluminum sheets (up to 1/4″) and offer good cutting speeds at competitive prices.
- Fiber lasers: Excellent for thicker aluminum (up to 1 inch) and offer superior edge quality and cutting speeds, but come at a higher cost.
Laser cutting aluminum offers unmatched precision, efficiency, and versatility. By understanding the factors influencing thickness, cost, and best practices, you can make informed decisions for your project. A-Laser’s expertise and diverse laser options ensure you achieve the desired results at competitive prices.