The quest for the perfect fabrication method is ceaseless, but laser cutting complex shapes, is taking on the challenge where intricate geometries and tight tolerances reign supreme. While traditional techniques like machining and stamping have long been the methods to use, laser technology, using light as its scalpel, has become a preferred method for many industrial and tight tolerance demanding applications. This transformative technology transcends mere material removal, offering a level of refinement and adaptability that other methods struggle to replicate, particularly when faced with the challenge of manufacturing complex parts. The ability of a focused laser beam to navigate intricate contours, produce sharp edges, and minimize material waste makes it a frontrunner for precision parts. There are several factors why laser cutting consistently outperforms its counterparts in the creation of highly complex 2D components and a review of these will give more clarity.
Intricate Geometries, Sharp Corners and Fine Detail
Laser cutting is not the only manufacturing method available to industries, but it does carry its share of precision support for 2D profiles, especially in thin gauge cutting and processing. How laser technology can outperform in this key area is shown in the following table.
Feature/Capability | Laser Cutting | CNC Machining | Metal Stamping | Waterjet Cutting | |||||||||||
---|---|---|---|---|---|---|---|---|---|---|---|---|---|---|---|
Intricate Geometries | Exceptional. Very fine cuts, sharp internal corners, complex contours. Ideal for micro-features. | Precise, but tool radius limitations restrict sharp internal corners. Complex geometries increase programming/tooling complexity. | Limited to relatively simple 2D shapes. Complex internal cuts are extremely difficult. | Capable of complex shapes, but kerf width and stream divergence can limit fine detail. | |||||||||||
Material Versatility | Wide range: metals, plastics, polymers, composites, ceramics, graphene, nitrile and silicon rubbers, and adhesives. | Versatile, but material hardness and brittleness can pose challenges. Heat generation can distort some materials. | Limited to ductile materials. | Cuts almost any material, but porous materials can absorb water. Better for thicker grades. | |||||||||||
Prototype Efficiency | Highly efficient. Software-based changes allow for rapid design iterations. | Longer setup and programming times slow down design changes. | Design changes require costly and time-consuming die modifications. | Setup can slow rapid prototyping. | |||||||||||
Heat Affect (HAZ) | Minimal to none- depends on material and systems used. | It can be high and must be controlled by coolant and programing of the cutting routine. | Minimal to none. | No heat affect. | |||||||||||
Set-Up/ Cutting Costs | Minimal to no physical tooling, reducing setup costs. | Requires specialized cutting tools, which wear and need replacement. | High cost of custom stamping dies. | No tooling, but abrasive materials increase operating costs. |

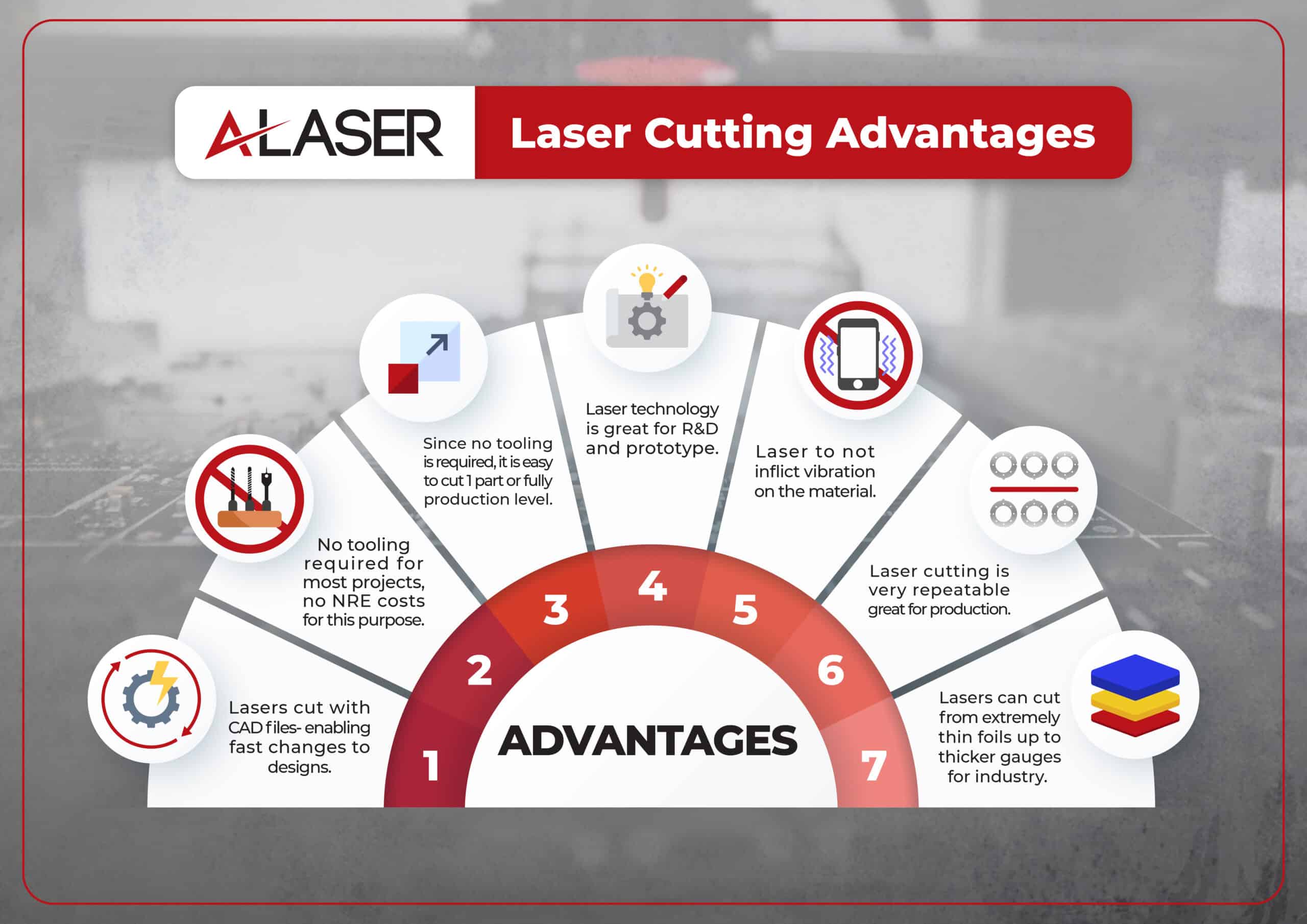
Providing integration and experience to support the vast network of technologies, laser cutting complex shapes does not need physical tooling thus reducing setup costs and eliminating tool wear. Nesting software optimizes material usage, minimizing waste. Support for start-ups and producing a limited run of custom designs without investing in expensive stamping dies or other tooling costs.
The Focus of Laser Cutting Machines
The ability to reproduce an intricate custom shape out of a metal alloy, a polymer, or perhaps a gasketing material, is just one of the great advantages to using laser technology. Laser cutting methods excel in manufacturing 2D profiles and industries have come to recognize this capability in pursuit of advancing technology and product design. To keep up with demand and be a competitive source for countless applications, laser technology covers materials and capabilities that other manufacturing methods cannot match. Each laser system type, available for precision machining, focuses on what they do best such as the following examples:
- Ultraviolet (UV): Versatile in cutting precision parts, greatly enhanced by the capability of cutting many different materials. UV laser cutting is known as a work horse for R&D, prototyping and production laser manufacturing. Specialized in thin gauges of materials like copper, aluminum, stainless steel, nitinol, Kapton, PEEK, FR4, graphene, Soma Black, K-Pad and so many more. These YaG lasers are nanosecond pulsed systems and produce geometries as tight as +/- 12.5um.
- Fiber Laser: Regarding the precision cutting of metal alloys, fiber laser technology is the big brother to all other laser systems. The systems use amplified fiber technology to cut through metal alloys like tungsten, titanium, aluminum, stainless steel and also hard materials like ceramic. With a tolerance of +/- 25um, for many profiles, fiber technology produces extraordinary custom shapes.
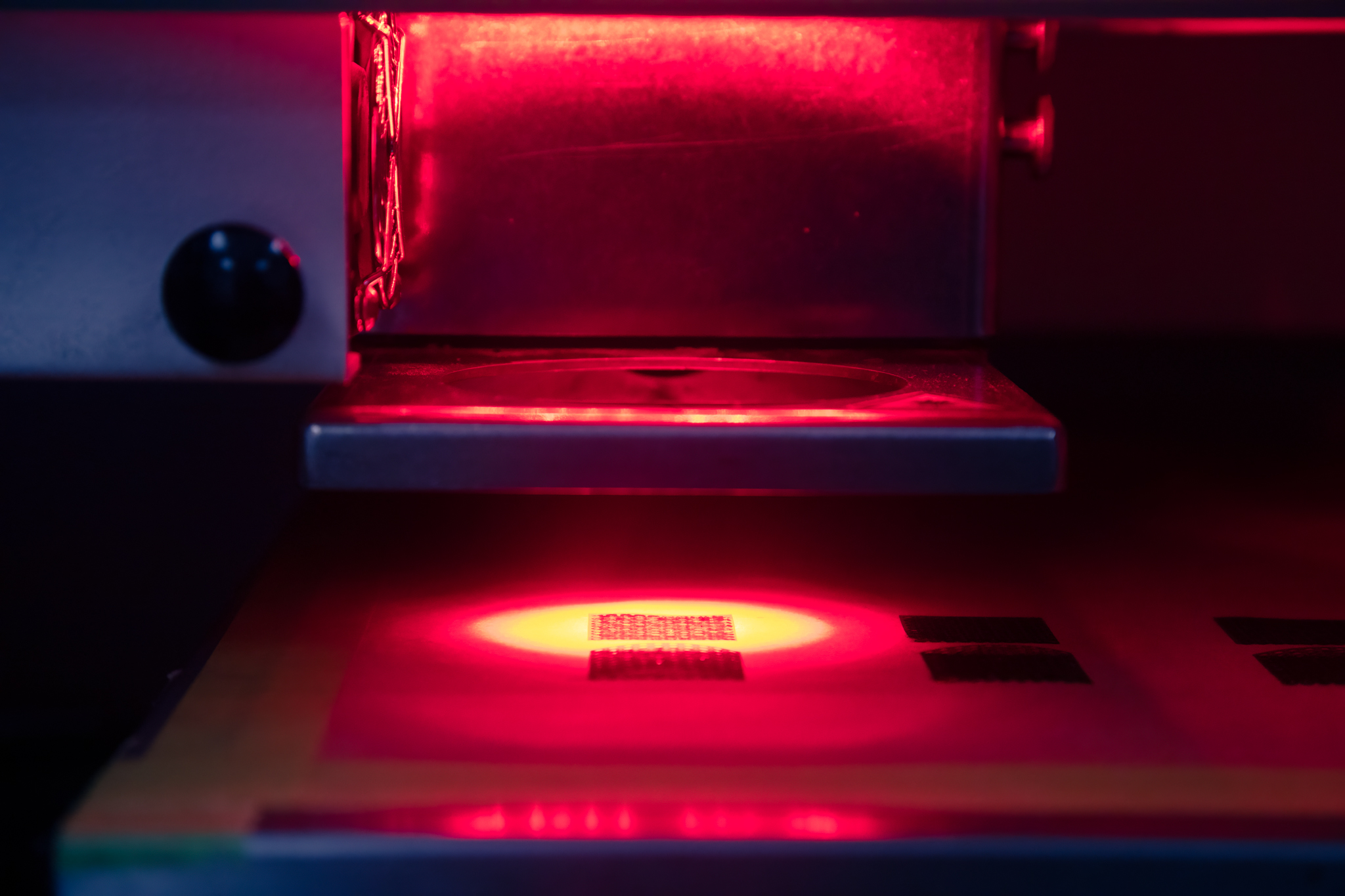
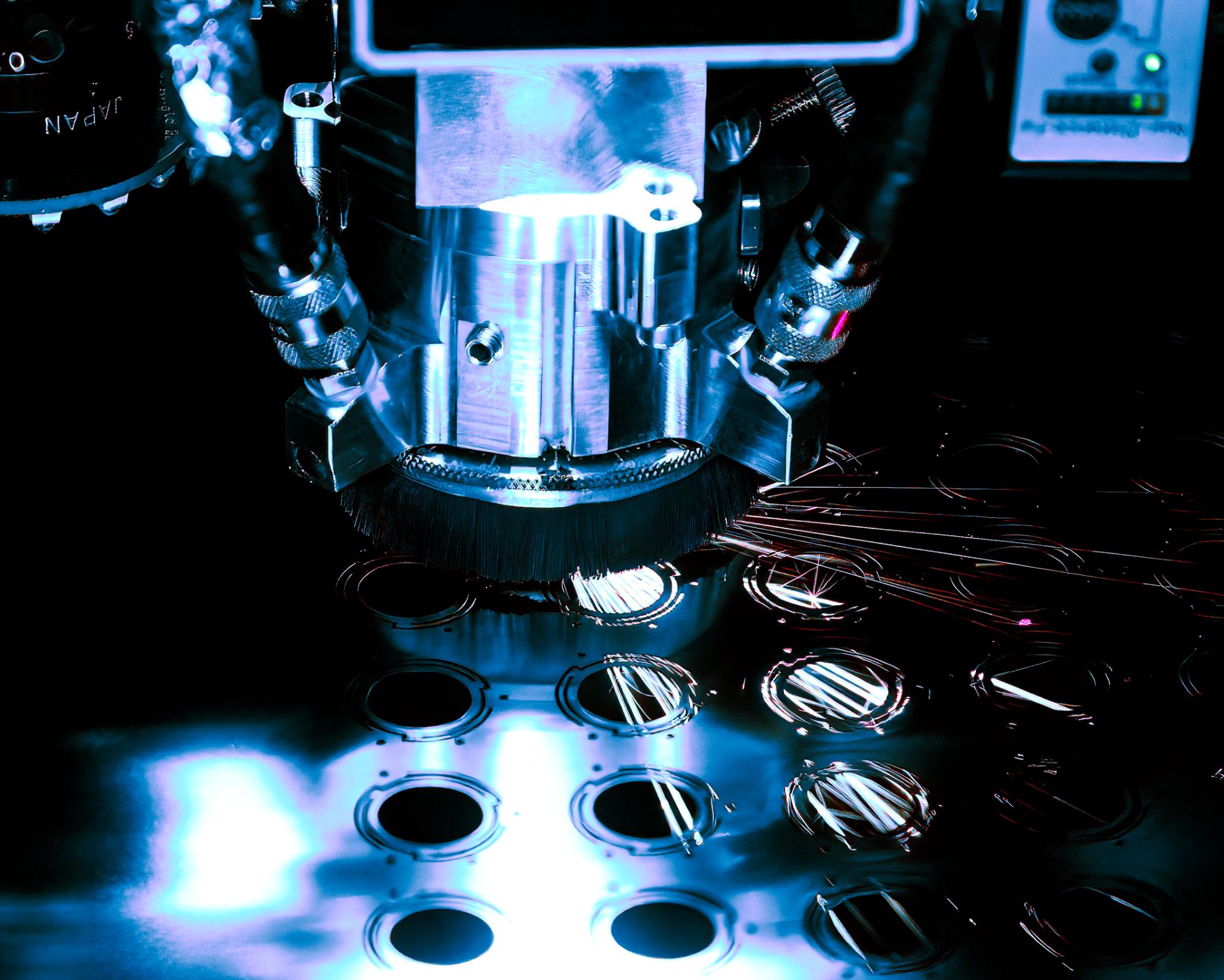
- Femtosecond and Picosecond lasers: Femtosecond lasers deliver extremely short pulses, minimizing heat-affected zones (HAZ). This allows for very precise cuts with minimal thermal damage to the surrounding material, which makes them ideal for micromachining. Cutting ultra-thin foils, creating complex and intricate designs within a tolerance range of +/- 3-5um.
- CO2 Laser: Greatly admired for the capability to cut non-metallic materials like paper, plastics, wood, cardboard, CO2 laser technology can be used in commercial and home use systems. Much higher-powered CO2 laser systems can cut metal alloys and specific manufacturers will use this technology as needed to a tolerance of +/- 100um to 125um.
Conclusion
Using focused beams of light energy to transform metal alloys, plastics, polymers and other highly used materials in support of electronics, communications, medical devices, optics and aerospace applications, is what laser cutting of precision components has become to the success of those industries and many more. Cooperation between manufacturers is a constant part of the process and seeking out technological support can bring many benefits and value to their customers. Laser cutting complex parts does excel in many areas and integrating such systems directly or in partnership with other service providers brings along quality, and versatility for high precision projects