Complimentary Manufacturing
Laser cut sheet metal technology in conjunction with both sheet metal and laser manufacturing have formed a synonymous relationship over the past decades. Sheet metal is categorized as a thin metal alloy that is about 6mm in thickness or less. This definition is demonstrated when it comes to laser technology’s influence on manufacturing as it continues to grow not only in the technology to harness different wavelengths of light, but how laser technology changes the way materials are used in highly technical applications. Sheet metal is one of those materials that has seen a growth in applications supporting uses in shims to electrical contacts, for manufacturing of cathodes, to supporting wireless communications. We rely on it for structural support in aircraft and for the guiding of threaded materials in textile fabrication. Sheet metal and the laser cutting process has formed this strong relationship benefiting industries and products related to consumer goods to space exploration.
High-Tech Push for Precision
Laser cut sheet metal is produced across an array of metal alloys from precious metals to stainless steel and aluminum. Prior to the development of laser technology, precision parts were manufactured by methods like metal stamping, CNC technology, which includes CNC Milling and routing, and mechanical sawing and forming. Along with other methods, sheet metal parts supplied the industries to the highest levels afforded by those technologies. From the technology boom of Silicon Valley and the rapid upswing of computer chips and related devices, progress in all areas of innovation ensued. Electronics became more powerful in capacity and the transfer of data. This improved the inner workings of devices and opened the door of opportunity to design smaller and precise components. Laser cut sheet metal was a great benefactor in this progress of technology and a forefront provider of precision cut components. The requirement for tighter tolerances and design features such as sharp corners and smaller and smoother radius, prompted manufacturers to look for alternative manufacturing methods. Laser cutting in many ways was just the right tool for this boom in electronics and the development of high technology. With versatility of materials processed and capabilities to process them by laser ablation, laser etching and laser skiving, has given OEM’s and start-ups new avenues to take advantage of in pursuit of advanced technology in medical diagnostics, electronics, sensors, consumer electronics, medical devices, communications and so many more.
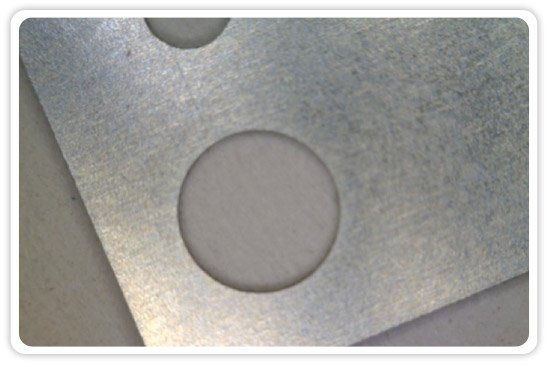
An Array of Sheet Metal Applications
Going back to earlier days of laser manufacturing, it was discovered that these systems, in using different wavelengths of light, could focus on specific materials. For instance, in printed circuit manufacturing, flexible circuits were made from Kapton, a trademark of Dupont Corporation. This polyimide is well known for its stability in use in electronics and was being precisely laser cut by ultraviolet light laser systems. Services providers wanting to seek new opportunities, realized these ultraviolet or UV laser systems could also cut very thin foils of metal alloys in thickness below 0.254mm. The was dramatically increased opportunities for manufacturing and prospective customers that now had a method to produce smaller and more efficient designs out of thin metal foils. They found that laser cutting these thin sheets of metal was not damaging costly materials and promoted further research and discovery by using laser technology. To better understand this contribution the following table gives a glimpse of sheet metal alloy components produced by using laser technology.
Component Type | Sheet Metal Used | Used For industries | Laser Systems |
---|---|---|---|
Shims | Stainless steel, aluminum, copper, titanium | Medical Device, Battery Energy, Oil and Gas | Ultraviolet, Fiber, Infrared, |
Electrical Contacts | Copper | Battery Tech, Aerospace, Automotive, Electronics, Science | Ultraviolet, Fiber |
Flat Springs | Stainless Steel, Nitinol, Spring Steel | Medical Device, Consumer Products, Optics, | Ultraviolet, Infrared, Fiber |
Mesh Screens | Copper, stainless steel, aluminum, | Oil & Gas, Automotive, Thermal Management, | Infrared, Fiber, CO2, Ultraviolet |
Shutters/Apertures | Steel, Stainless Steel, | Optics, Firearms, Defense, Science | Ultraviolet, Infrared, Fiber |
Washers | Spring Steel, Stainless Steel | Electronics, Medical Device, Vibration Management, Optics | Fiber, Infrared, Ultraviolet |
Structural Supports | Aluminum, Titanium, Steel | Aerospace, Automotive, Consumer Products | Fiber, Infrared, CO2 |
Sorting Through Your Options
Sheet metals are produced mostly in rolls of raw material in various lengths and widths. From this many manufacturers or distributors cut the rolls into smaller sheets depending on their customer base needs. As much of precision laser cutting is done in a 2D axis, this is where you will find many of the applications and services provided using laser technology. The options you’ll encounter are the various laser systems available and what will be the best to use for a particular project. Details such as the material, geometry, tolerance and quantity are some of the factors reviewed. Thicker sheets of metal will require higher power. More fragile alloys would be better processed on a lower powered system. In designing your precision part with a particular metal alloy in mind, some research upfront can be very helpful. Not all metal sheets are made to the grade of alloy needed or made to the required thickness for the intended design. Manufacturers may offer production of custom sheet metal, but the cost can be extremely high. Laser services providers can be very helpful in determining the feasibility of your project, so it is recommended to reach out and discuss to determine the best sheet metal and direction for your project.
The Laser Cut Sheet Metal Advantage
Sheet metal alloys are increasingly favored for laser cutting due to the numerous advantages over traditional manufacturing methods. Laser cutting offers unparalleled precision and accuracy, allowing for intricate designs and complex shapes that are difficult to achieve with other techniques. This technology minimizes material waste, as it can cut precise shapes without the need for additional machining or tooling like costly dies and fixtures. Additionally, laser cutting is a non-contact process, reducing the risk of material damage and improving overall product quality. By doing so, the material surface is cleaner and not marred with slag and debris. This versatility, coupled with its ability to handle a wide range of metal alloys, makes laser cutting an indispensable tool for modern manufacturing.
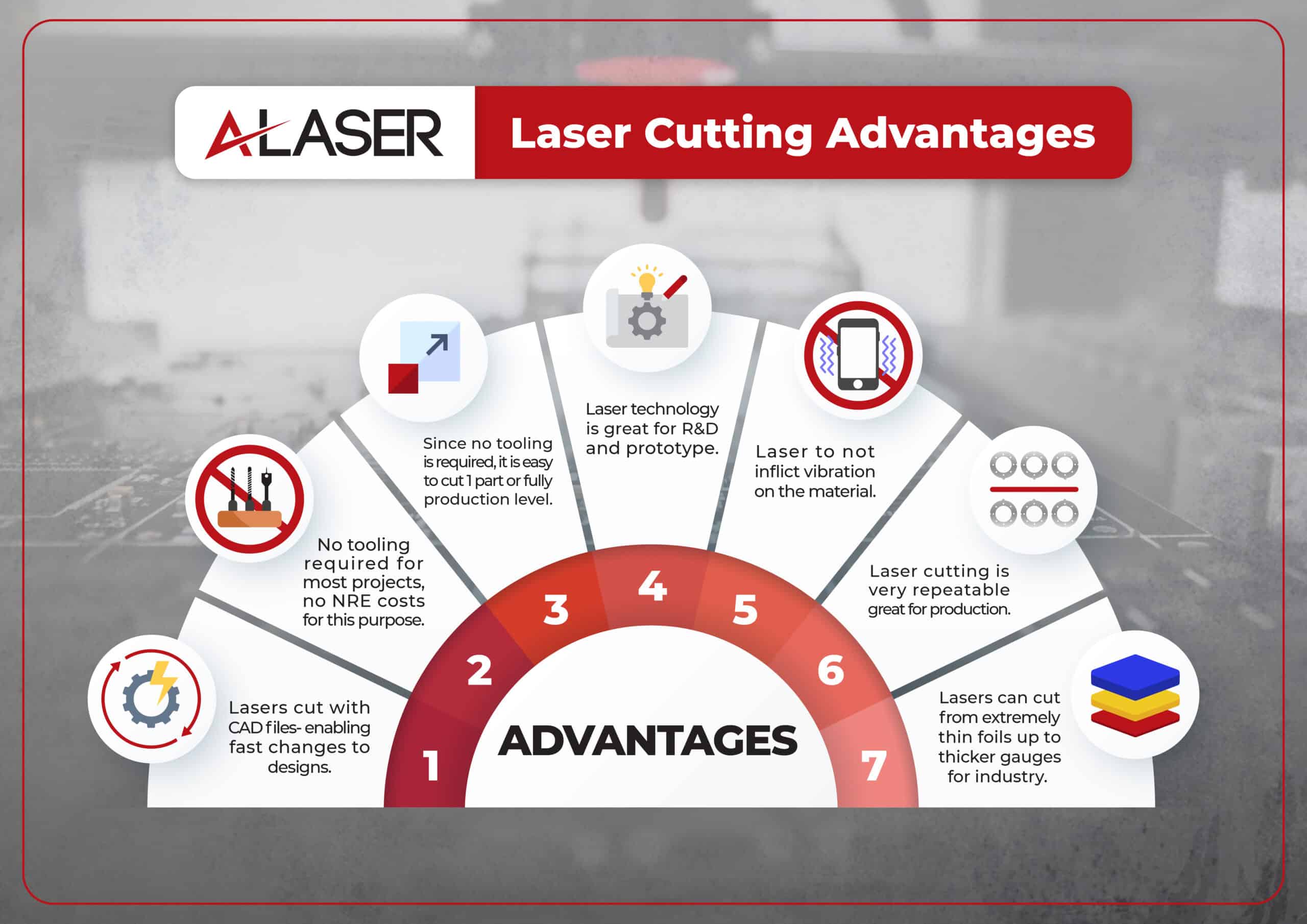