Laser Cut Alumina Ceramic
Alumina Ceramic and Laser Technology
One such material that is gaining recognition by use of laser manufacturing is alumina ceramic. Alumina ceramic is not a material many people readily think of regarding laser cutting technology. Often materials like stainless steel, copper, polyimides and graphene come to mind regarding the manufacturing of precision laser cut components. The non-contact nature of laser cutting minimizes the risk of material stress and deformation, crucial for maintaining the integrity of high-performance components. This attribute is part of the intriguing part of laser cutting services where many materials are utilized in the manufacture of precision parts. The list of materials that are cut by laser technology continues to grow as new composites and polymers are made, or established materials are brought forward to be processed in new ways. Alumina ceramics origins can be traced back to the early 20th century, pursued by the needs of the burgeoning automotive
and aviation industries. Limitations of existing materials like porcelain in high-temperature environments pushed researchers to seek a more robust and heat-resistant alternative. The development of alumina ceramics by Siemens Halske in Germany applied it to automotive spark plugs around 1931. The electrical insulating and thermal properties of alumina proved superior and vital for ignition in internal combustion engines. This reliability was a significant milestone in automotive technology. Today, alumina ceramic is used in electronics, telecommunications, medical devices, defense, automotive and many more industries.
Key Characteristics of Alumina Ceramic
The use of any material in today’s manufacturing world undergoes much scrutiny and evaluation to ensure public safety and keep the integrity of the systems and processes these devices support, free from failure and malfunction. Laser manufacturing with alumina ceramic is key to many applications that we will review, but to know why it is used is important to the application. Key characteristic factors about alumina ceramic are:
- Chemically Stable: Components made from alumina ceramic can function in chemical environments without degrading over time.
- Dimensionally Accurate: Alumina has a smooth finish resulting in highly accurate profiles and geometries to be made with tight tolerances.
- High Dielectric Strength: For electronics, this allows alumina substrates to be withstand high voltages ensuring reliable function for electronics.
- Low Dielectric Constant: This characteristic means there is low distortion and interference with electronic signal strength, thus gaining stronger signal integrity.
- Wide Temperature Range: Alumina can withstand temperatures up to 1750°C.
- High Hardness: Alumina hardness gives it strong resistance to wear thus enhancing its durability and increasing lifespan of manufactured components.
These characteristics of alumina ceramic make is favorable for industries requiring exceptional hardness, chemical stability and dielectric strength while being dimensionally stable and accurate. To produce such components, laser technology has proven to be a great pairing of material to manufacturing technology.
Laser Processing of Alumina Ceramic
Laser cutting alumina ceramic can be processed by two distinctly different laser technologies such as ultraviolet or fiber laser systems. Ultraviolet laser technology is a relatively low wattage system in the range of 10-20 watts but can be higher. They are extremely accurate producing components with tolerances as tight as +/- 0.0005mil. UV lasers use very small beam diameters as small as 20-micron and cut a wide spectrum of materials from polymers, metal alloys, rubbers, composites and hard materials like alumina ceramic. They are however limited to thin and ultra-thin thicknesses of these materials in most cases. For alumina ceramic, the upper range of thickness would be about 0.010mils. However, femtosecond lasers can cut alumina ceramic up .020 to .030mils, depending on the system and project. With a small beam diameter, very fine details can be cut, including sharp corners and small radius. Fiber laser technology is a the more robust technology, designed to cut metal alloys at thicker grades than the ultraviolet systems along with harder materials such as alumina ceramic.
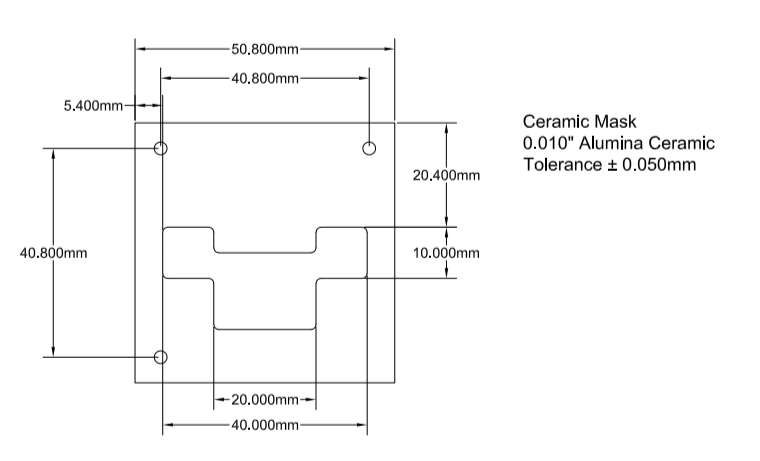
Some fiber lasers come with dual laser heads encasing either an 18-micron beam or 38-micron beam, for example. The thickness range of a fiber laser does vary depending on the wattage of the system and be from 100 watts to 4000 watts or higher. Fiber lasers will cut materials like stainless steel, titanium, copper, alumina ceramic (up to 1mm thick or higher), aluminum and other alloys. The accuracy of these systems is excellent with a tolerance for many projects at +/- 0.002 mils.
By using laser technology, the precision components made will be a flat 2D profile and can be a simple shape as a square or disc to complex designs. The applications of alumina ceramic are specialized to the industry applications applied to. To further examine these applications the following segment will give more insight.
Applications of Alumina Ceramic
Alumina ceramics will be found in electronics, to medical and mechanical engineering applications to name a few. The following table will illustrate some of the more prominent industries and uses for.
Industry | Application | Used For |
---|---|---|
Chemical | Filtration, chemical reaction storage. | Resistance to chemicals and stability. |
Medical-Dental | Stents, filters, artificial joints, dental implants. | Biocompatible, strength and durability |
Electronics | Integrated circuits, capacitors and resistors. | Excellent thermal conductivity, heat dissipation, strength. |
Research | Ceramic heaters, filters, storage vessels. | Resistance to chemicals and extreme environments, durable. |
Alternative Energy | Solid Oxide Fuel Cells. | Mechanical strength, electrical insulation and stability during lifespan. |
Mechanical | Gears, sliders, nozzles, seals and bearings. | Strength, durability, smoothness, keep systems operating and at lower maintenance cost. |
Advances in technology drive all industries forward along with new materials and new ways to harness materials currently available. Alumina ceramic has a role in providing the necessary characteristics mentioned above to established industries and to undoubtedly will be harnessed for new approaches to technology for many years to come.
Exploring More About Alumina Ceramic
The use of alumina ceramic dates back decades, first gaining prominence in the mid‑20th century as industries sought materials stronger and more durable than traditional metals and plastics. Today with alumina ceramic becoming indispensable in fields ranging from aerospace, medical devices, electronics and energy systems, the manufacturing of precision parts from it, can still be unknown and come with numerous questions. Let’s review some questions about alumina ceramic material:
Controlling Tolerance
What are the tightest tolerances your laser cutting process can maintain when cutting alumina ceramic:
With UV or femtosecond lasers, alumina ceramic can typically be cut with tolerances as tight as +/- 0.001 mil to .002 mils. This is far exceeding mechanical methods for fine features that many precision applications now require.
Technology VS Technology
How does laser cutting of alumina ceramic compare to die-cutting, waterjet, or CNC machining for this material:
Laser Cutting: Best for microfeatures using a femtosecond laser with high precision, and minimal mechanical stress and excellent for thin sections. Ultraviolet lasers can cut alumina ceramic well with a slightly range.
Die-Cutting: Not applicable — alumina ceramic is too brittle.
Waterjet Cutting: Good for thicker parts, but lower precision at about +/- .004 mils and potential for microcracks.
CNC Machining: Achieves fine detail but slow, tool-wear prone, and induces mechanical stress.
Edge Quality Factor
What edge quality can be expected when laser cutting alumina ceramic? Are burrs or heat-affected zones (HAZ) present:
Laser cutting yields smooth, chip-free edges with no burrs. Heat-affected zones (HAZ) are minimal with ultrafast lasers; with CO₂ lasers, microcracking or slight discoloration can occur if not optimized.
Material Characteristics
How do material characteristics like reflectivity, softness, or thermal conductivity affect edge quality and tolerance control in alumina ceramic:
Alumina’s high hardness and brittleness favor non-contact cutting methods. Its low reflectivity at UV/femtosecond wavelengths aids precision, while low thermal conductivity makes controlling HAZ crucial — hence short-pulse lasers excel in tolerance and edge quality.
The Benefits of Laser Cut Alumina Ceramic
What are the benefits to laser cutting alumina ceramic:
Laser cutting offers non-contact precision, micro-scale feature capability, clean edges, minimal waste, and reduced risk of cracks compared to mechanical methods, making it ideal for medical devices, electronics, and aerospace components.
Conclusion
Laser cutting has revolutionized the processing of alumina ceramic, enabling precise and intricate part fabrication unattainable with traditional methods. This technique leverages the laser’s focused energy to efficiently cut through the hard and brittle material, resulting in clean edges and minimal material waste. These advantages, combined with the inherent properties of alumina ceramic such as high strength, excellent wear resistance, and biocompatibility, make laser cutting an indispensable tool in industries ranging from aerospace and electronics to medical and automotive, driving innovation and enabling the creation of advanced, high-precision components.