How Does HAZ Impact Edge Quality in Thermal Cutting Processes?
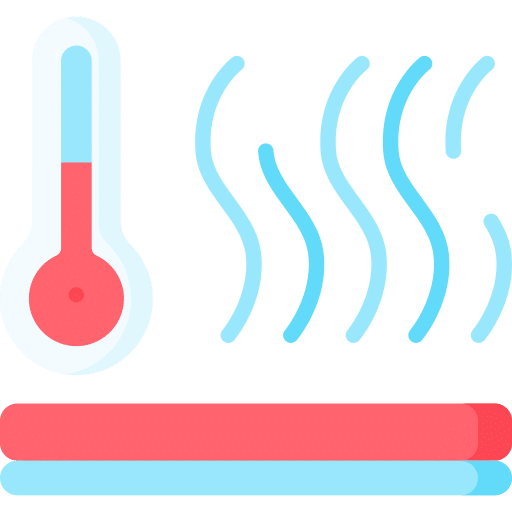
Thermal cutting can result in HAZ or heat-affected zone, that can drastically hinder the function and performance of any precision component. HAZ is a concern for precision cutting methods such as laser technology and CNC machining. Any manufacturing method that can induce thermal stress into the material will need to control these potential heat-affected zones. Micro-manufacturing is especially sensitive to HAZ as it can affect the edge quality in machining. Through methods such as process optimization and post finish processing, components can be made by virtually burr-free manufacturing. Methods applied are both mechanical and chemical and provide the best in surface finish optimization. First, let’s learn the factors that can cause HAZ.
The Effects of HAZ
Metal alloys come to mind when heat-affected zones are of concern. However, metal alloys are not the only vulnerable materials, as heat incurred during the manufacturing process can also affect polymers, adhesives, plastics and rubber-based substrates. Not all laser manufacturing systems cause HAZ. Picosecond and femtosecond laser technology operate at a extremely high pulse rates so that no heat affect occurs. This is a plus for specialized projects, and these lasers are incredibly accurate and have their niche in manufacturing, however they are limited to cutting ultra-thin materials. HAZ can develop on many different manufacturing methods. For instance, on laser systems such as fiber, ultraviolet and infrared (not femtosecond), and CO2. In CNC machining, the technology can add friction during CNC Milling, CNC Lathe and other similar systems where high speed tooling is in contact with the raw material. Generally, you will see the following effects of HAZ on edge quality such as:
- Slag and Burrs: Laser energy needs to pulse through several runs or laser passes. Metals can heat up especially in concentrated areas where the cutting is occurring. The process of laser ablation can create redeposits of molten material.
- Warping or Oil Canning: Heat-affected areas can warp and deform, producing an edge that does not lay flat. To adjust this, programing with lower power and added laser passes, can negate or minimize warpage.
- Discoloration: For metals and non-metallic materials, HAZ can result in discoloration on the cut edge and surrounding area. For cosmetic reasons this may not be favorable and may also be an indication of possible warping and melting of the cut edge.
- Delamination: Excessive heat-effect can lead to delamination of laminates including adhesive. This will be noticeable under examination and render components non-conforming.
Controlling Heat-Affected Zones
Concerns about heat-affected zones are a constant for CNC machining, laser cutting and any other method that can produce thermal stress to the material during the manufacturing process. CNC technology is widely used for its versatility and capabilities to form 3,4, and 5 axis shapes from metals and plastics. It uses cutting tools called spindles, similar to drill bits, that are spun at high revolutions to remove material from the raw source, such as a metal block or plate. Friction is the culprit that can damage and or deform the cut edge of the component. This is controlled by using lubricants applied during the milling process with additional controls of the feed rate and speed of the cutting tools. Without control, HAZ issues can occur in laser technology in the form of burrs, deformation, and discoloration. By adjusting the laser power, speed and wavelength, are just some of the techniques used to eliminate HAZ. Knowing the characteristics of materials aids in making adjustments to all manufacturing methods that can produce thermal stress. When done correctly, the reduction or elimination of a heat-affected zone is part of challenge to producing the best possible edge quality in machining.
Conclusion
The process of precision manufacturing brings constant oversight into new projects. There is neither one way nor one set of rules that can be applied for precision cutting methods that result in burr-free manufacturing. Through experience and gained hands on knowledge, professionals in manufacturing start every project with a review of the details including the material, the geometry, the use and environment that the component will be subjected to and many other factors including surface finish optimization. Heat-affected zones are one factor that service providers deal with, but there are others. It is a constant challenge in manufacturing, but the goal for every manufacturer is to provide high quality and at an agreeable cost. Controlling their processes with procedures and the ability to find solutions keeps technology moving forward.