How to Select the Right Laser Cutting Machine for Your Project
Choosing the right laser cutting technology is crucial to ensuring precision, efficiency, and cost-effectiveness for your project. Different materials and design requirements call for specific laser types and post-processing techniques. This guide will walk you through the decision-making process, using the Technology Decision Tree infographic as a reference.
Understanding Laser Cutting Technologies
Laser cutting is not a one-size-fits-all solution. Various laser types—Fiber, CO₂, UV, and IR—offer distinct advantages depending on material composition, thickness, and finishing needs. Below, we break down the key considerations when selecting a laser cutting machine.
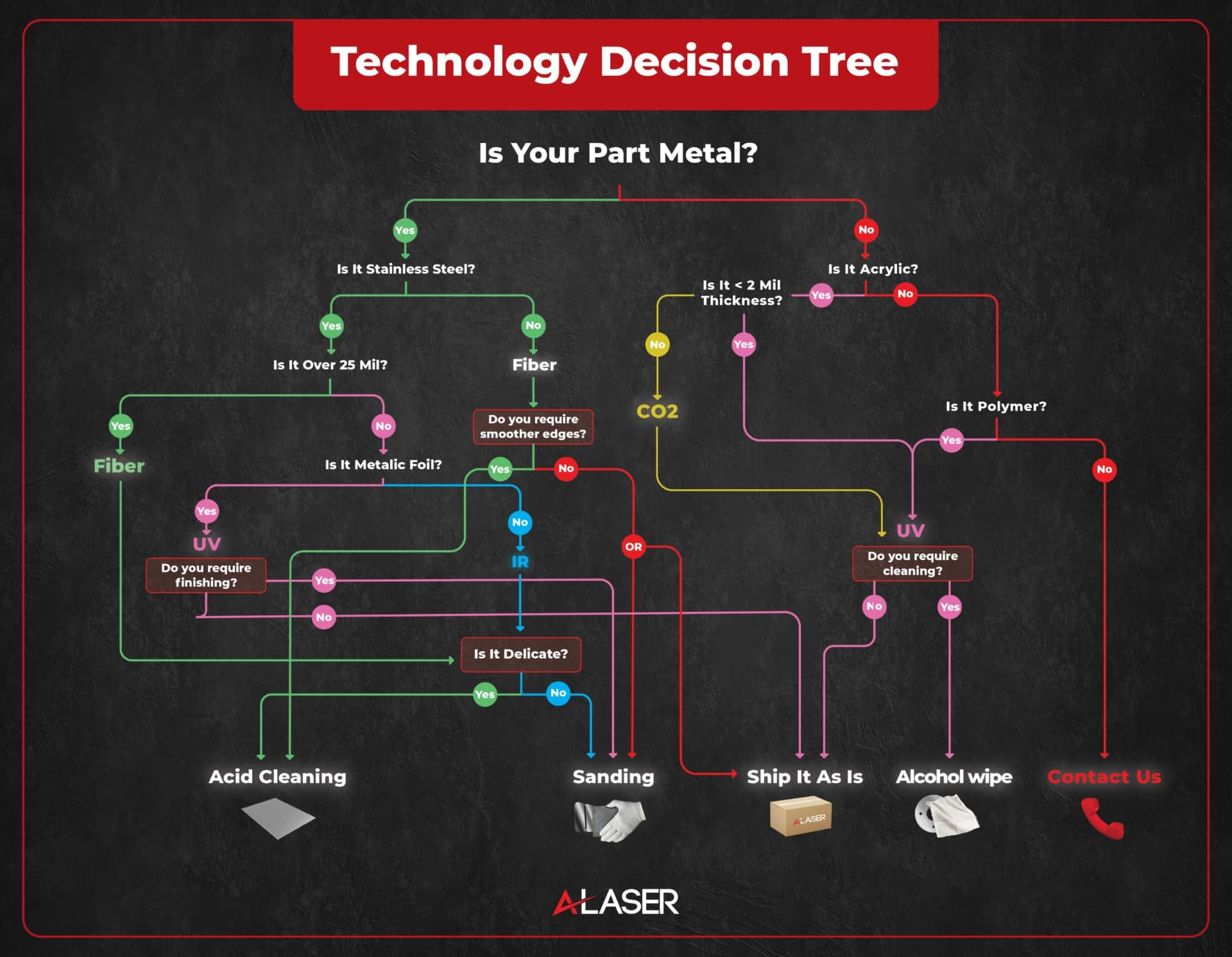
Step 1: Is Your Part Made of Metal?
Your first decision point is whether your material is metal or non-metal.
If Yes (Metal)
Stainless Steel & Thick Metals (Over 25 Mil)
- Best Laser: Fiber Laser
- Why? Fiber lasers are ideal for cutting metals due to their high power and efficiency. They provide excellent precision and speed, especially for stainless steel and thicker materials.
Thin Metal Foils & Smooth Edge Requirements
- Best Laser: UV or IR Laser
- Why? If your part requires a finer finish, an IR laser may be preferable for smoother edges. If it’s metallic foil and requires post-processing, UV lasers may be necessary for finishing.
Delicate Metal Parts
- Best Laser: Fiber Laser (Sanding Post-Process if Needed)
- Why? If the part is fragile, additional finishing like sanding may be needed to remove burrs without damaging the material.
Cleaning & Finishing for Metal Parts
- Acid Cleaning: If the metal part requires additional post-processing.
- Sanding: For delicate metal parts that need a refined finish.
If No (Non-Metal)
Thin Non-Metallic Materials (< 2 Mil Thick)
- Best Laser: CO₂ Laser
- Why? CO₂ lasers work well for cutting thin non-metal materials with high precision and minimal heat distortion.
Acrylic & Polymers
- Best Laser: UV Laser
- Why? UV lasers are highly effective for cutting and engraving acrylic and polymer materials due to their shorter wavelength, which minimizes material degradation.
Cleaning & Finishing for Non-Metal Parts
- Ship As-Is: If no additional cleaning is required.
- Alcohol Wipe: If post-cutting cleaning is necessary.
Material Type | Best Laser Type | Thickness Consideration | Post-Processing |
---|---|---|---|
Stainless Steel | Fiber Laser | Best for >25 mil | Acid Cleaning if needed |
Thin Metal Foil | UV or IR Laser | Thin & Delicate | Sanding if required |
Thick Metal (>25 mil) | Fiber Laser | Thick & Durable | No extra finishing required |
Thin Non-Metal (<2 mil) | CO₂ Laser | Must be under 2 mil | Ship As-Is or clean with alcohol wipe |
Acrylic | UV Laser | Any thickness | Alcohol wipe if needed |
Polymer | UV Laser | Any thickness | Cleaning with alcohol wipe if required |
Key Takeaways
- Fiber lasers are best for metal, especially thicker materials.
- UV lasers are effective for finishing and cutting delicate materials like foils and polymers.
- CO₂ lasers excel at cutting thin, non-metallic materials.
- Post-processing like acid cleaning, sanding, or alcohol wiping may be necessary depending on material type.
Selecting the right laser cutting machine is essential for achieving high precision and efficiency in manufacturing. By following this decision tree and table, you can ensure the best cutting process for your project.
Need expert guidance on laser cutting solutions? Contact A-Laser today!