Waterjet vs. Laser Cutting for Precision Parts: Which One Wins?
Laser cutting wins hands down, regarding the manufacturing of precision parts, when compared to waterjet technology. The reality, however, is all in the details of what material is being cut, the tolerance required, and for what purpose. Waterjet cutting is synonymous with cutting all sorts of materials, including metal alloys and plastics of much greater thickness than laser cutting technology. Visually, waterjet vs. laser cutting can look very much the same, especially as the thickness of materials is thinner and the geometries of flat 2D profiles are produced. There are two clear winners, it seems regarding both of these manufacturing methods depending on the circumstances of the project.
What Makes the Difference Head-to-Head?
Technology used for waterjet cutting is about as far from laser cutting as it can be. Waterjet systems use two primary materials to cut: water and abrasive media. Combined and forced through nozzles with high pressure at levels up to 90,000 psi. This process creates a tool capable of cutting thick aluminum blocks or perhaps plates of stainless steel. Industrial gears, shims, tubing, supports, and other high precision components are made by waterjet methods. There are different types of waterjet cutting systems such as abrasive flow cutting, high pressure water cutting and abrasive jet machining. In all, water is the main cutting tool. For laser cutting, it too has different system types, capable of focusing on materials and capabilities, providing precision parts like connectors, aperture stops, gaskets, nozzles, surgical tools, and other micro-machined components. Lasers are harnessing light to act as the cutting tool and with these amplified beams of energy provide precision components with systems such as ultraviolet, femtosecond, picosecond, CO2, and fiber laser technology. Visually, on a scale of thinner material thickness and smaller component size, laser cut parts can look like waterjet cut parts and vice versa.
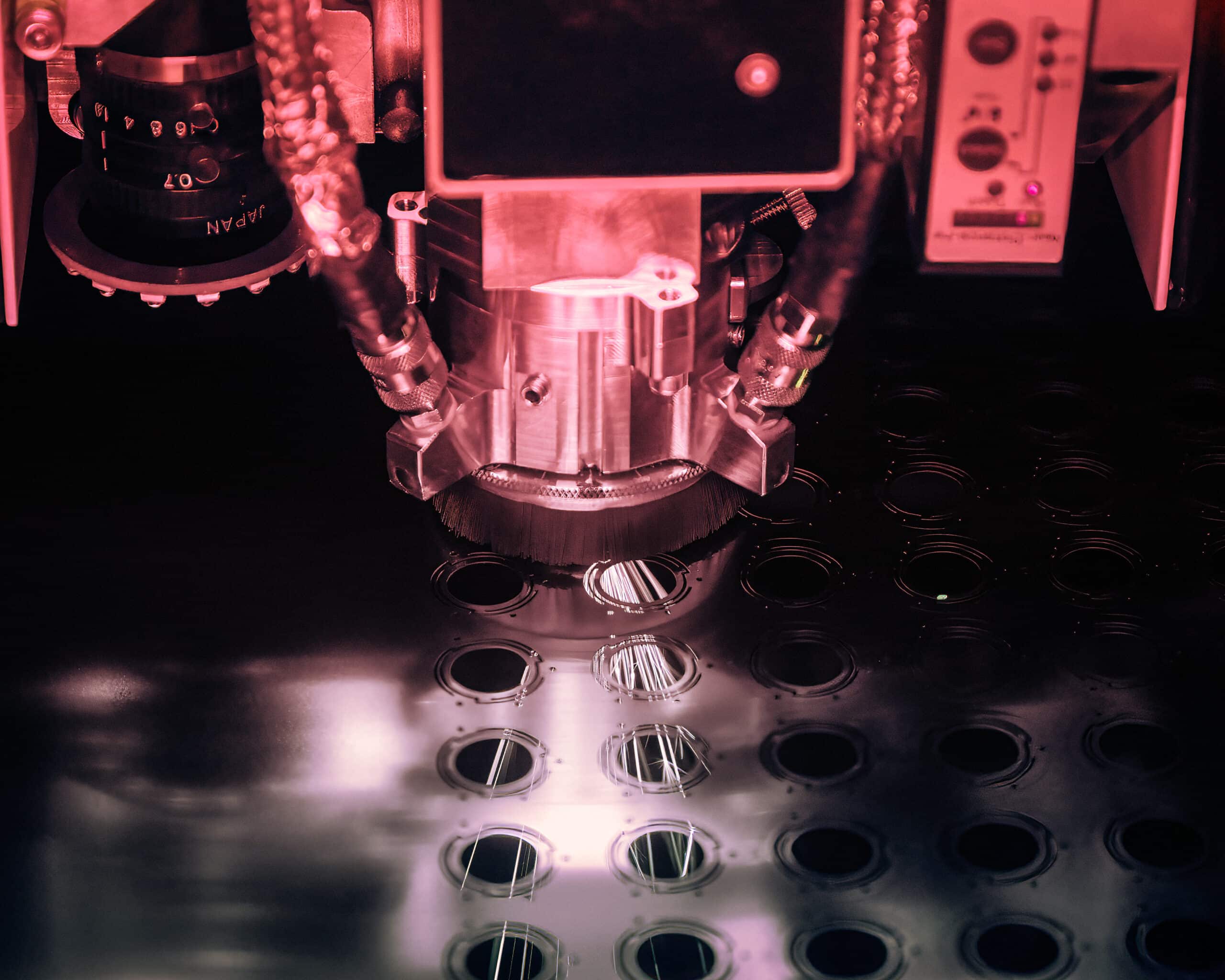
Laser Cutting
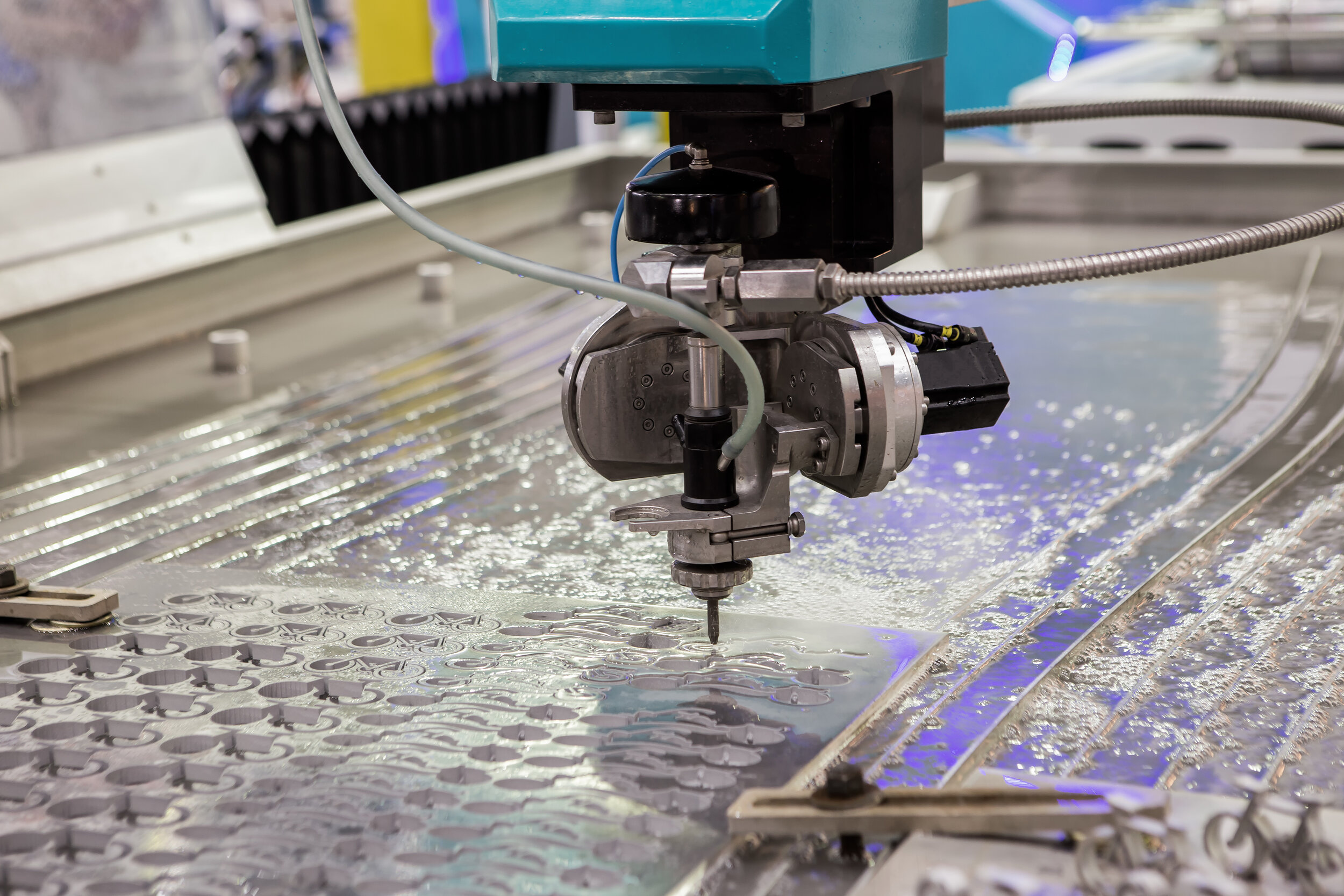
Waterjet Cutting via www.acpwaterjet.com
Beyond A Visual Comparison
What sets waterjet cutting and laser cut parts is the niche aspect that each manufacturing method holds. Laser cutting will win every time for micromachining projects. These often require ultra-thin and thin gauges of metal alloys such as copper, nickel, stainless steel, aluminum and nitinol to be cut into complex 2D shapes with tight tolerance restrictions from a +/- 3um up to, 100um, depending on the laser system used. Thin plastics, polymers, rubbers and other composites are processed by laser technology as well for highly projects sensitive to accuracy and tolerance control. When waterjet cutting is used, the purpose often is to cut thicker plates and blocks of metal, plastics, wood, ceramics, tiles and more. A better understanding of how each method would be chosen is to imagine a new machined gear needed for industrial use, with the material needing to be 40mm thick titanium. Waterjet cutting can fulfill this need flawlessly, while laser technology would find it challenging and only permitted by exclusive machines. On the other hand, a titanium component of 0.127mm thickness would readily be done using laser technology. The force of waterjet cutting stream would damage the thin sheet of titanium. It is not a fair comparison between these two remarkable methods of cutting precision components since each supports designs that only the technologies can produce. Is there a factor that gives the edge for one over the other?
Tolerance Control: The Final Factor?
Precision manufacturing is constantly being challenged to push current methods beyond what they can do. This creates new ventures and ideas to overcome what customers are asking for. In the battle of waterjet vs. laser cutting precision, each project is unique and therefore hard to give a final lean to which is best. Both waterjet cutting and laser cutting can be highly accurate and many times each capable of a tolerance of +/- .025mm. However, laser systems such as femtosecond and picosecond can hold tighter tolerances of +/- 3um to 12.5um, but the materials being cut will also be in thickness of 150um or thinner. Waterjet cutting can cut metal alloys up to 300mm thick, going far beyond laser technology and hold tolerance of +/- 0.100mm to 150um at these thicknesses. The larger tolerance for this waterjet project will more than sufficient for the application. Thickness, geometry, and the settings used are important factors that affect precision, surface roughness and the overall appearance of high technology parts, cut by waterjet or laser cutting machines. The differences in capabilities that waterjet and laser cutting have between each method, negates any clear winner. The true beneficiaries are really the fantastic applications being made for use in industries like oil and gas, defense, battery technology, textiles, aerospace, medical devices, nuclear science research, electronics, semiconductors and the list could go on and on.
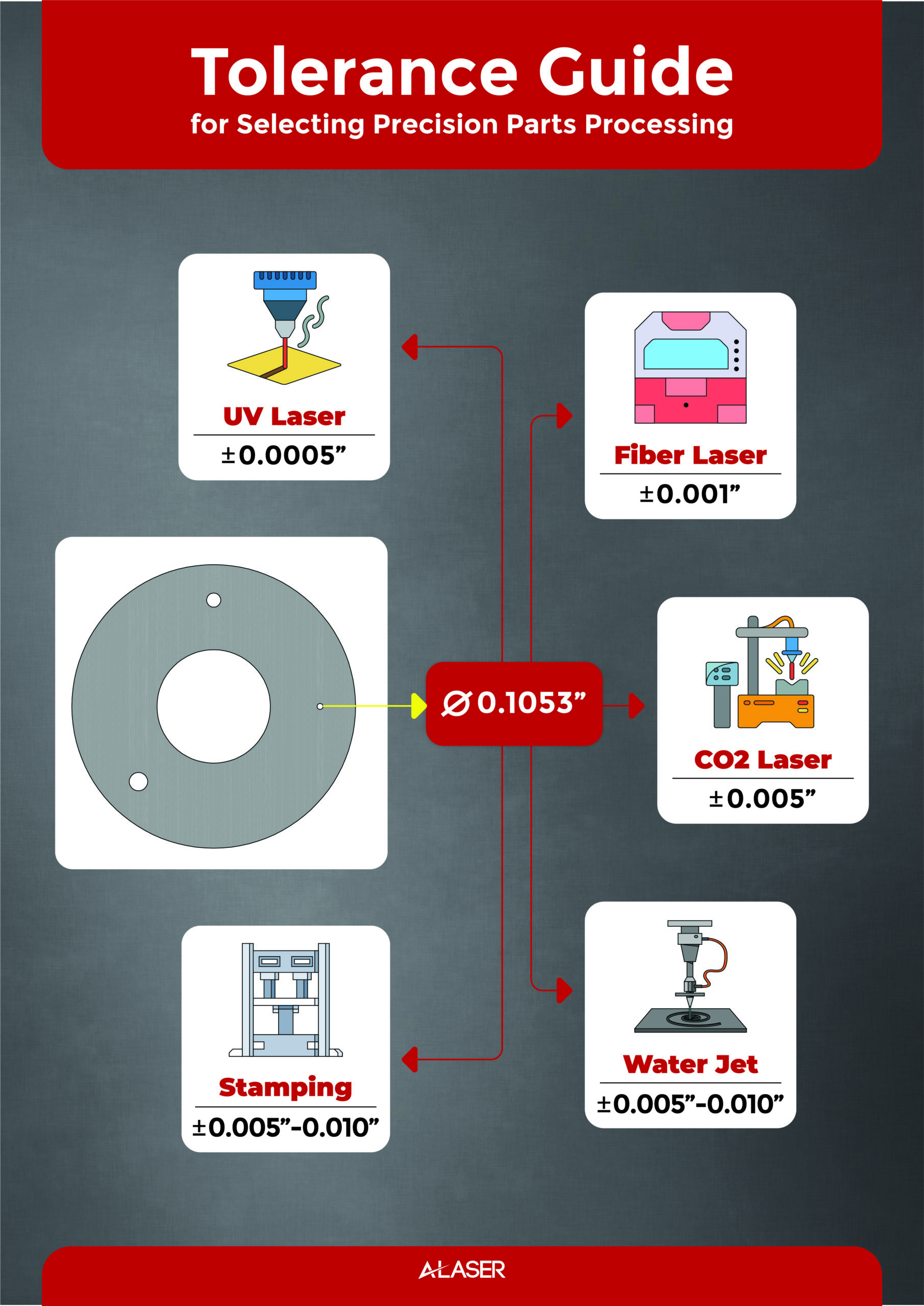
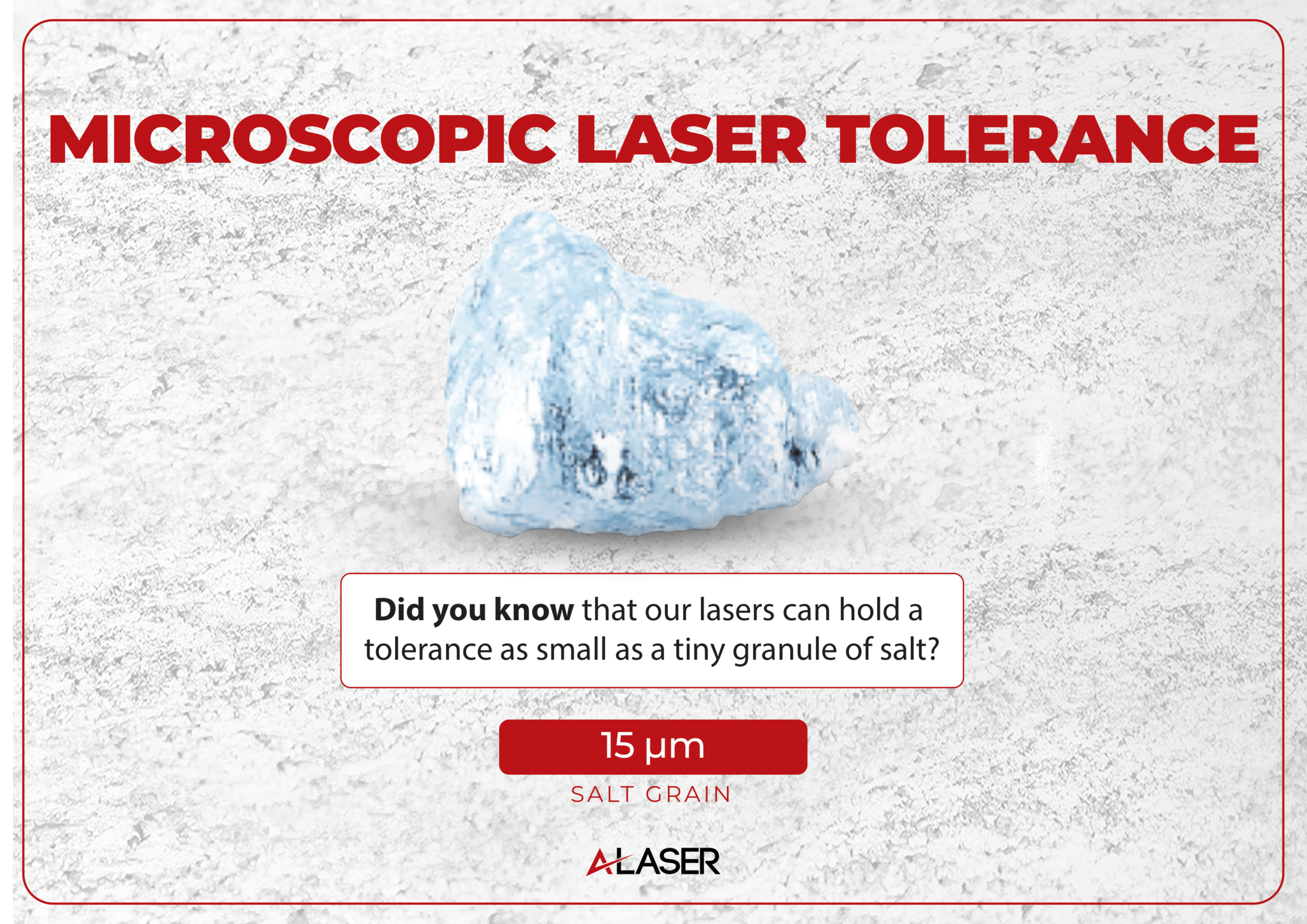
Conclusion
Ultimately, waterjet and laser cutting technologies are not merely rivals but can be partners in the realm of precision manufacturing. When employed together, they complement each other by handling diverse projects with unique demands. Waterjet excels at cutting thicker materials and achieving results with high-pressure water and abrasive streams, while laser cutting shines in micromachining applications, delivering unmatched precision for ultra-thin components, by using focused beams of light energy. The synergy between these methods ensures that manufacturers can meet the stringent requirements of industries like aerospace, medical devices, and electronics, creating products that uphold the highest standards of accuracy and quality. It is the harmonious integration of these technologies that truly drives innovation and excellence in modern manufacturing.