Precision Laser Cutting Plastic
The use of plastic is everywhere; in food packaging, in electronic devices, even in the clothes we wear. Where and how plastic is used can play a huge role in determining how it is manufactured. Much of plastic is molded in some way and then proceeds down the supply chain. Plastics like acrylic and ABS are called commodity plastics. Acetyl and polycarbonate would fall under engineered plastics because they are designed and developed to have specific attributes. The list of plastics is long but includes notable materials such as:
- HDPE
- Teflon
- Polycarbonate
- Mylar
- ABS
- As well as many, many more
Manufacturing precision parts from plastics is challenging due to its characteristics, which include reactions to heat and abrasion. The cutting of plastics is done in multiple ways:
One common method used for plastic manufacturing is die-cutting. It allows for many plastics to be cut into shapes and in large quantities, allowing for plastic pieces to be mass-produced.
Benchtop, band or circular saw cutting is often used for thicker plastics like acrylic
For materials like HDPE, Teflon, Polycarbonate, Mylar or ABS, a CO2 laser is usually a good choice if seeking a laser cut profile. There are many manufacturers of CO2 laser systems and they are often put to use on thicker grades of materials. A tolerance of +/- .004 to .005” mils is common.
UV laser systems are most often used for thinner plastics and offer tighter tolerances of +/- .001” to .003” mils.
Laser cutting plastics is challenging because the material is relatively soft and prone to heat-affected zones. Friction and laser energy will both add some undesirable discoloration to the cut edge. It is also not the most cost-effective method to produce a precision plastic part, but in some cases, it may be the best or only method. Laser systems such as UV technology can be a great fit for thinner and more precise requirements. Heat affected zones can be adjusted for minimal effect, and tolerances will be much tighter than die-cutting or CO2 laser technology can offer. Non-critical parts can always be made by the other means as mentioned as well, so that only the most critical or precise parts are laser-cut. These alternate methods are faster and will offer a lower cost of manufacturing in most cases. Precision laser cutting of plastic is limited but certainly has its place, especially when precision is a major manufacturing factor.
Cost is often a factor when determining whether or not this technology is the correct choice for the direction of a given project. For some projects, the need for the benefits of laser cutting does justify the cost. The ability to provide precision plastic parts is a great value. Determining the way in which one Achieves a precision laser cut plastic part will depend on the project’s requirements and the material being used. Qualified service providers will need all of the information on the project’s desired material, the quantity, the requirements for the tolerance of the part’s features, and more in order to make an informed decision about which technology might be best suited to the goals of the project. With this in mind, a collaboration between customer and vendor is always necessary to produce a quality precision plastic part.
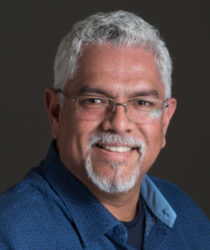
About the Author
Joe has been part of the A-Laser team for over 10 years and has extensive experience with laser cutting technology, sales, and customer service. Joe was born and raised in San Jose, CA and has resided with his family in Gilroy, CA since 1997. The unique projects he gets to learn about and the industries they support, keep everyday new! His hobbies include photography, he is a member of the Morgan Hill Photography Club, hiking, model building and collecting vintage camping lanterns and stoves. His favorite places include Mount Lassen Volcanic National Park, Portland OR, and Boston MA.