Metal Laser Cutting
Can I Cut Metal with a Laser?
Metal laser cutting has become a relied upon technology for manufacturing precision components. The second question that may be asked is “What is your project and what metal alloy are you considering?”. This question is asked often by laser service providers as cutting metals alloys is always in high demand. The systems available today give service providers many options when considering what laser system type will be the best fit. Fiber laser technology is dominant for many metallic laser cutting projects, but it is not the only solution. Laser cutting methods are used for their ability to process materials and different thickness of those materials. There is a crossover between systems being able to cut the same materials and thickness, but usually one will be the better fit overall. Custom metal laser cutting is covered by the following systems, and each will have its advantages and disadvantages. The trick is communication with a metal laser cutting service provider and how best they can support your project. Here is an overview of the types of laser technology available for cutting metal:
- Fiber Lasers: For industrial metal cutting applications, fiber lasers are the dominant choice. They offer high power, speed, and precision, allowing them to cut through a wide range of metals and thicknesses of aluminum, tungsten, titanium, copper, nickel, stainless steel and more. Depending on the alloy, the range of thickness can be from 0.127mm up to 16mm or thicker.
- CO2 Lasers: CO2 lasers can also cut metal, but they are generally better suited for thinner gauges, typically up to around 1/4 inch (6.4 mm) thick. Additionally, they may struggle with highly reflective metals like aluminum and copper. Sometimes a non-reflective coating must be applied to the metal to allow the CO2 laser to cut. This type of laser is more often chosen to cut plastics, paper and wood-based materials.
- Ultraviolet lasers: Cutting a wide range of materials but mostly at an ultra-thin gauge. Thin metal foils and brazing alloys fit well with UV laser in thickness of 0.0127mm to 0.127mm. UV lasers cut polyimides, graphite and rubber as well and adhesives to name a few.
- Infrared lasers: System such as these good for cutting stainless steel alloys. Thinner range than the fiber laser systems from about 0.127mm to 0.635mm. They might be able to engrave a very shallow marking on a very thin sheet, but for thicker cutting, you’ll need a more powerful laser.
- Picosecond Lasers: Best at cutting materials like glass, ceramics and films, picosecond systems can process specific metal projects requiring micromachining of tiny holes and intricate features in metal sheets of micrometer range.
- Femtosecond lasers: Processing with short pulse rates picosecond lasers can provide high precision with low HAZ or heat affected zone. This system is also used for extremely thin metal alloys.
Additional factors to consider:
- Metal Type: Some metals are easier to cut with lasers than others. Mild steel, stainless steel, and aluminum are commonly cut with lasers.
- Metal Thickness: The thicker the metal, the more powerful a laser you’ll need to cut through it effectively.
- Desired Cut Quality: Fiber lasers generally offer cleaner cuts with minimal dross (molten metal sticking to the edge) compared to other lasers. Some slag or molten debris is still a result of laser cutting for many systems. Slag or burrs are removed by chemical deburr, sanding, electropolishing and other chemical processes. There are adjustments laser technicians use to minimize this by reduction of power but increasing the number of laser passes. Also, the focus and frequency can be adjusted.
Laser cut metal is accomplished with the use of different laser systems. They each have their place regarding custom metal laser cutting and provide manufactures with options to push technology forward. Cutting metal by laser technology is not the only available method, but they do provide the edge especially when it comes to flat 2D parts and components. Laser technology does not need extensive set-up or tooling thus enables support for multiple iterations during R&D and prototype projects, but also can run full production cycles. By searching for “metal laser cutting near me” your next project will be in the hands of experienced and knowledgeable laser experts.
What Laser Is Best for Cutting Metal?
If given one choice, fiber laser technology would be the clear winner, but there are other system types that are used for specific metal alloys and thicknesses. Metal laser cutting is part of the growing precision parts industry providing tight tolerances and repeatable production support for high profile consumer and industrial needs. The best laser technology for cutting metal alloys will consider the type of metal and the thickness. These two factors are key for determining the best technology to use for a specific project. Fiber lasers are generally thought of when custom metal laser cutting is sought after. These types of systems come in varying sizes and wattages to cut metallic alloys.
The following is an overview of different laser technologies that will help guide in searching for a metal laser cutting service:
- Fiber Lasers: Fiber laser technology has the capability to cut metallic materials like stainless steel, copper, brass, titanium, tungsten, molybdenum, aluminum and nickel. Systems can range from 20 watts to 4000 watts or higher and provide very precise laser cut features in tolerance of +/- . 0.0254mm to 0.0762mm. With this technology metal thicknesses can range from 0.254mm to 10mm or higher depending on the system’s power.
- CO2 lasers: These types of laser systems can cut tantalum, stainless steel and other metals but need the metallic materials to be coated to not reflect into the laser and damage the optics. CO2 laser will cut thinner gauges of metals, but not the first choice for such projects. They cut plastics and paper-based material much more efficiently.
- UV -Ultraviolet Lasers: Thin metal foils can be cut by Ultraviolet laser technology. Foils from 0.0254 mm up to 0.254mm can be cut depending on the wattage of the system. Using very small beam diameters of 0.02mm, giving designers options for intricate geometries. UV laser technology also cuts non-metallic materials like polyimides, adhesives, rubber, Grafoil, FR4 and others.
- IR -Ultraviolet Lasers: This type of laser technology is good for thicker gauges of metals beyond what a UV laser can cut, but not the higher thickness of what a fiber laser can. Good for stainless steel, alloys but no good for highly reflective alloys like nickel and aluminum.
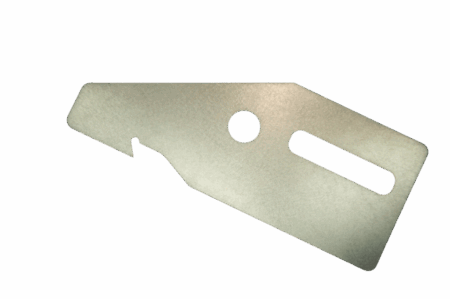
What Is the Metal Laser Cutting Materials List?
A metal laser cutting materials list can provide valuable information about the capabilities that a metal laser cutting service provider has. It’s really a list indicating what metal alloys can be processed by the laser technologies used. Metal laser cutting though it has been around 45-50 years, it’s the younger sibling of other technologies like CNC milling and turning. Together these methods provide numerous solutions for precision metal parts. Regarding laser cutting, it has become the method of choice for many industries needs like surgical instruments, semiconductor gaskets, aperture stops, shims, battery tabs, sensors, electronic probes and so many more. Being made of metal alloys, the precision parts mentioned above, and countless others require metal alloys to be laser cut in to geometries that other technologies cannot provide. The following list are some of the most commonly laser cut metal alloys:
Metal Alloy | Grades | Pros for Use | Cons to Consider | Common Applications |
---|---|---|---|---|
Stainless Steel | 302,304,16-6,17-7 | Good corrosion resistance- multiple grades | Special cutting techniques needed to reduce heat distortion | Automotive, machinery, consumer products |
Aluminum | 5052, 6061, 7075 | Lightweight, strong, machinable | Reflective | Aerospace, Electronics, device enclosures |
Copper | Electrolytic Tough Pitch (ETP) Copper, Oxygen-Free High Conductivity (OFHC) Copper, Deoxidized Copper | Excellent electrical conductivity, good heat transfer | Reflective, may need special set-up to avoid melting | Heat exchangers, electrical connections, decorative |
Tungsten | Pure(W), Tungsten-Carbide (WC), Tungsten-Rhenium(W_RE) | Superior strength, heat tolerance, corrosion resistance | Difficult to machine, high in cost, can be brittle. | Aerospace, structural, jet engine components, Cutting tools. |
Titanium | Grade 2, Grade 5, Grade 9 | Great strength to weight ratio, biocompatible, corrosion resistant, | Cost, difficult to machine, poor electrical conductivity | Medical and dental implants, aerospace components, sporting goods, chemical processing containment. |
Molybdenum | Made into ingots and powder | Good strength, high melting point, good corrosion resistance, added to other metal alloys for strength | Brittle at low temps, oxidizes at high temps, harder to machine, not as common | Electrical applications, alloying agent to other create stronger metals |
Brass | Good machinability, aesthetic appeal | Highly reflective, needs set-up to avoid melting | Plumbing components, decorative | |
Nickel | Pure (Nickel 200) Nickel-Iron alloys like Invar and Inconel | Good magnetic properties, electrical conductivity, ductile with strength, corrosion resistant | Cost subject to supply and demand, health concerns on nickel dust, can cause allergic reactions to some. | Electroplating, electrical connections, chemical industry |
Tantalum | Tantalum, sheets, foil and powder | Exceptional corrosion resistance, high melting point, biocompatible and good electrical conductivity | Rare and costly when sourced, difficult to machine | Used in Capacitors, medical implants, high temp applications, aerospace components |
Laser cut metal is done daily by custom service providers who have the experience and knowledge of what laser technology will be best to process your project. They will determine what laser technology is best such as fiber, infrared, ultraviolet, femtosecond or CO2. Since each project has its specific details including the metal alloy required, metal laser cutting service providers will focus on the right technology for the job. During the manufacturing process, the characteristics of each alloy are accounted for and adjusted to ensure a high-quality laser cut component is produced.
How Thick of Metal Can a Laser Cut?
The thickness of metal that a laser can cut depends on several factors including the type of laser, the power of the laser, and the specific metal alloy being processed. Each laser system has its capabilities and limitations, which must be considered to determine the optimal method for cutting various thicknesses of metal sheets.
Fiber Lasers: Fiber laser systems are the go-to choice for cutting a wide range of metal thicknesses. They excel at cutting materials like stainless steel, aluminum, titanium, copper, and more. For instance, fiber lasers can handle metal sheets as thin as 0.127mm up to 16mm or thicker, depending on the laser’s power and the material’s properties. These systems are particularly efficient for cutting metals up to 10mm thick, but with the right settings and power, they can push the limits further.
CO2 Lasers: CO2 lasers are versatile and can cut metals, but they are typically more effective with thinner gauges. These lasers are best suited for cutting metal sheets up to about 4mm thick. For metals thicker than this, CO2 lasers may struggle, especially with reflective materials like aluminum and copper. A special coating might be needed to prevent reflection and ensure a clean cut.
Ultraviolet (UV) Lasers: UV lasers are designed for precision cutting of ultra-thin materials. They can cut metal foils ranging from 0.0127mm to 0.127mm. While they are not suitable for thicker metals, their ability to cut with high precision makes them ideal for delicate and intricate designs.
Infrared (IR) Lasers: Infrared lasers are capable of cutting metals within a specific thickness range, generally from 0.127mm to 0.635mm. They can handle stainless steel and similar alloys but are not effective for cutting thicker materials compared to fiber lasers.
Picosecond and Femtosecond Lasers: These lasers are specialized for micromachining and cutting extremely thin metal alloys. They are not typically used for cutting thicker metal sheets but excel in applications requiring high precision and minimal heat-affected zones.
Additional Factors to Consider:
- Metal Type: Different metals have varying properties that affect how easily they can be cut by lasers. Mild steel, stainless steel, and aluminum are commonly cut with lasers, but each requires specific settings and considerations.
- Laser Power: Higher power lasers are capable of cutting thicker materials. For instance, a fiber laser with higher wattage can cut through thicker metal sheets compared to a lower wattage laser.
- Cut Quality: The quality of the cut also depends on the laser type and settings. Fiber lasers typically offer cleaner cuts with minimal dross compared to other lasers.
In summary, the thickness of metal that a laser can cut varies widely based on the laser system used. Fiber lasers are the most versatile, capable of cutting metal sheets up to 16mm thick or more. CO2 lasers are suitable for thinner gauges, typically up to 4mm thick. UV and IR lasers, as well as picosecond and femtosecond lasers, cater to ultra-thin and precision cutting needs. Consulting with a knowledgeable laser cutting service provider will help determine the best laser technology for your specific project requirements.