Laser Cut Nickel
When working with high precision laser systems, consistency is key. Many of our customers’ applications require us to custom laser cut one thousand parts just as we make the first. When this requirement is viewed upstream from the end-user it takes a different form. We need to ensure our equipment behaves as expected, that we follow our procedures and that our materials are consistent.
A great option for this is using Nickel for metallic laser cut parts. If you are looking for consistency it doesn’t get better than custom laser cutting metal with stable elements like Nickel.
Nickel is a silvery-white metal that has a slight brownish golden tinge. It’s strong and largely corrosion-resistant. For this reason, it has been used as a protective coating for many other materials often via electroplating. This is a very popular method for protecting Iron and Brass. Nickel is one of only four elements that are ferromagnetic at room temperature along with cobalt gadolinium and iron.
History
Atomic Symbol | Ni | |||
---|---|---|---|---|
Atomic Number | 28 | |||
Element Category | Transition Metal | |||
Density | 8.908 g/cm3 | |||
Melting Point | 2651 *F (1455 *C) | |||
Boiling Point | 5275 *F (2913 *C) | |||
Moh's Hardness | 4.0 |
Although Nickel has been used for millennia with artifacts dating to around 5000BC. Nickel was not known to be an element until 1751. It was identified by Axel Fredrik Cronstedt, a Swedish mineralogist considered by many to be one of the founding fathers of mineralogy. The name “Nickel” came from the original name of the ore in which it was found, “Kupfernickel”. This loosely translates as “the goblins copper” from the German words Kupfer (copper) + Nickel “demon, goblin, rascal.”
Though discovered in the cobalt mines of Los, Hälsingland, Sweden, the vast majority of the world’s Nickel is mined from the following countries:
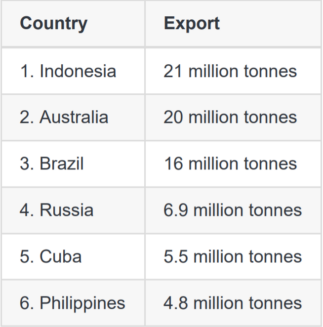
Current Uses
Nickel is most widely a component of stainless steel. Today around 65 to 70% of all Nickel finds its way into stainless steel alloys. The next largest portion of 9% to plating applications, both decorative and protective purposes.
Nickel is also widely used as a catalyst for hydrogenation. Also as a main component in battery manufacturing.
MuMetal®, a material that has the ability to shield from magnetic waves, is largely made up of Nickel.
MuMetal® consists approximately of 80% Ni 20% Fe (Iron) with some traces of Mo (Molybdenum). MuMetal® can be cut very well with IR lasers. This is often used in the automotive industry to protect sensitive areas or instrument clusters.
Structure
Nickel in its crystalline form takes a face-centered cubic structure which gives it its high ductility. Due to this property Nickel is added to steel to increase its weldability.
Laser Cutting
Nickel is an excellent choice as an upgrade from stainless steel laser-cut parts. For solder paste stencils, Nickel offers excellent paste release, smooth geometry, and a very clean finish. Custom laser cutting metal like Nickel does have its difficulties. For example, the highly reflective surface makes the initial laser penetration a little harder and optical scanning much more difficult. Nickel is workable and strong at very low thicknesses. We tend to use 0.5, 1, or 2 mil sheets which are often used for next-gen EV batteries.
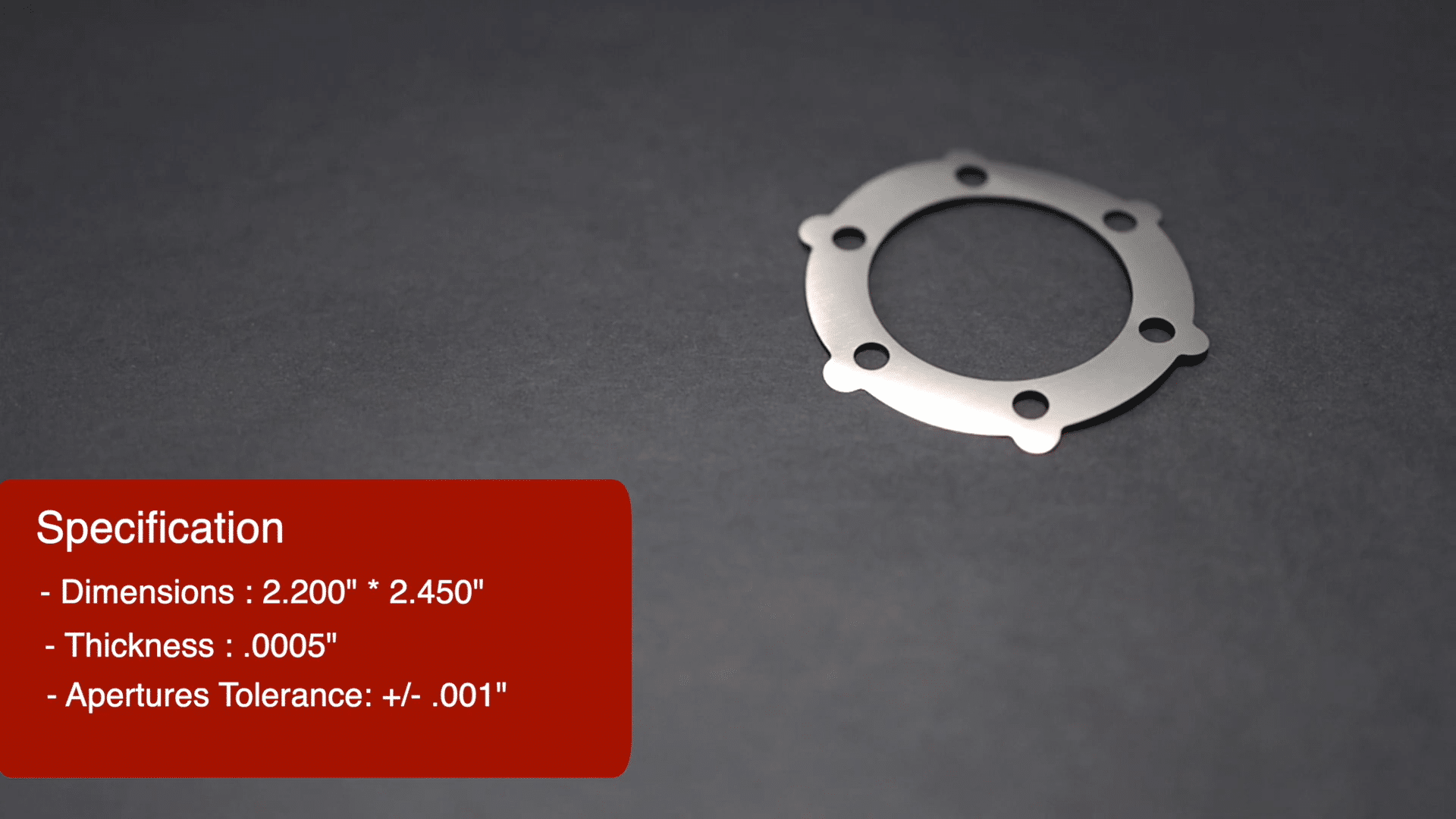
Nickel Foam
Nickel foam is a flexible option for small parts. This form of Nickel is often much easier to custom laser cut for two reasons. The rough surface texture scatters the light entering the material thus reducing the back reflection to the laser source. Also depending on the density much less material needs to be removed in order to have a complete cut. For applications where the surface area in benefits the porosity of nickel foam greatly improves this. With Ni foam being much softer, custom laser cutting metal performs exceptionally well over die punching.
Our Other Laser-Cutting Services
We offer a wide range of laser-cutting services, including laser skiving, laser depaneling, laser ablation routing, and more. We work with both UV lasers and infrared lasers to give you the choice of the best method for your project.
Find Out How We Can Help
Our technical engineers walk you every step of the way through the manufacturing process. We’d be happy to talk more about your project and how we can help.