Can All Materials Hold a Tight Tolerance?
Not all materials can be manufactured to a tight tolerance. Manufacturing to tight tolerance takes great knowledge of materials and skill in dialing in parameters that will meet as closely to the desired specifications while adjusting to characteristics of the chosen material. Additionally, holding a tight tolerance is subject to the manufacturing method, and application for the manufactured part. The correct tolerance for manufacturing must consider the physical properties of the selected materials and then determine if the chosen manufacturing technology can produce the required geometry. Manufacturing in general terms is taking raw materials or pre-manufactured materials and converting them into tangible objects. This is true for manufacturing methods including CNC machining, waterjet cutting, laser cutting, stamping and die-cutting, for example. These methods all convert in some way that block of titanium or the sheet of polyimide, or perhaps rolls of nitrile rubber, into precision components. That is why it is important in planning a manufacturing project to know a material’s expected tolerance.
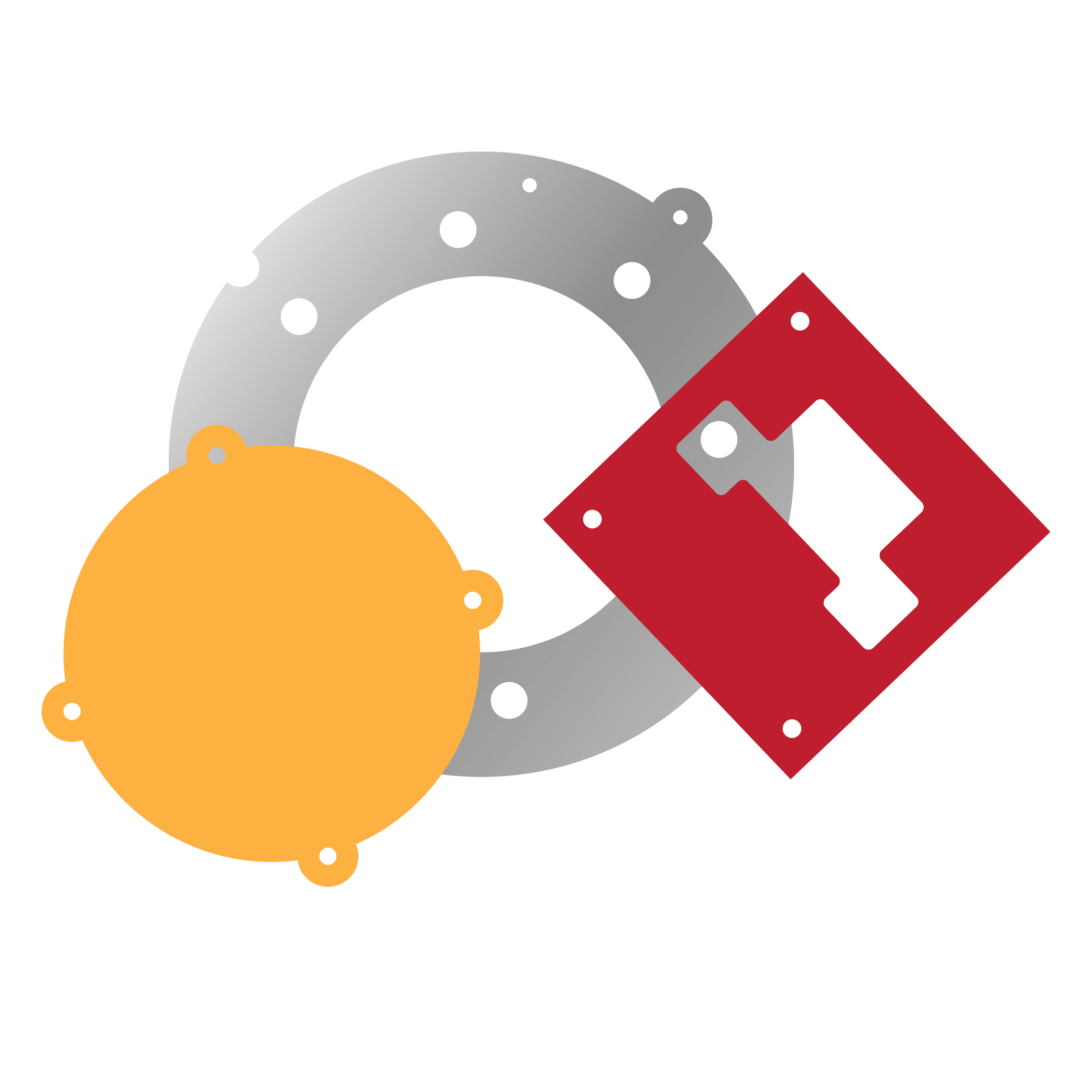
It Is Not Apples to Apples
A tight tolerance means different things to different industries. For heavy industry, a tight tolerance may be a +/0 0.5mm, within another industry, a tight tolerance may be +/- 0.0120mm, and these results are perfectly fine and are possible with the same material, like stainless steel, for example. This metal alloy is versatile in strength, longevity and machinability, and is a solution for many precision components. But stainless steel cannot solve every challenge nor be effective in every application. Nitrile rubber is another widely used material from communications to electronics. It is, however, prone to fluctuations over time due to the environment and it is subjected to how the material is stored. Let’s take laser technology as a demonstration of manufacturing materials with the capability of holding a tight tolerance in the form of a washer. Stainless steel, as mentioned earlier, is stable and can be manufactured with high precision and for this example is made at 20mil thickness to a tolerance of +/- 0.0250mm. A nitrile rubber washer made of the same thickness cannot be compared. The material has a larger tolerance in its raw form. So, it may be +/- 0.0500mm in thickness already. The material when laser cut can expand or retract over time, therefore a minimum tolerance may be +/- 0.050mm to 0.0760mm.
The Role Of Materials In Tolerance Control
Tolerance and materials are a continuing challenge for manufacturers and new methods and processes are developed to achieve the tightest tolerance possible. There will be differences from one material type to the next that the manufacturing method chosen will have limits to want is achievable in a measured tight tolerance such as:
- Metal Alloys: These are very stable and result in tolerance ranging from +/- 5 microns to +/- 0.0120mm depending on the alloy thickness and manufacturing method used. Alloys like copper, aluminum, titanium, tungsten and stainless steel are commonly used in manufacturing. Metal alloys can expand at high temperatures, so the choice of alloy for its function is crucial.
- Polymers: Polymers are used widely for industries in electronics, medical device applications, defense and aerospace uses. Numerous precision components made from materials like Kapton, PEEK, mylar are made to tolerance of +/- 0.0127mm to 0.0254mm. However, A polyimide, like Kapton, can absorb moisture, if exposed prior to manufacturing or during its component’s lifespan, thus affecting it tolerance.
- Graphene: Many fluidic and gas systems rely on the integrity of the gaskets made from Grafoil. The tightest tolerance that can be achieved is subject to thickness and geometry. All things being the same on the design, thin Grafoil of .005” mils or less can hold a tolerance of +/- 0.0127mm while thicker sheets of 30-60mils will have a tightest tolerance of +/- 0.0762mm.
- Rubber Based Materials: Rubber materials, whether silicon, nitrile or some other formulations, are pliable as part of their characteristics. They come in different levels of hardness called durometers. Parts manufactured from laser cutting, die-cutting, molding or extrusion, all have tolerance variation for design and thickness. In general, a rubber thickness of 0.001” mil can have a tolerance of +/- 0.102mm and 1.0” thick rubber may have a tolerance of +/- .203mm.
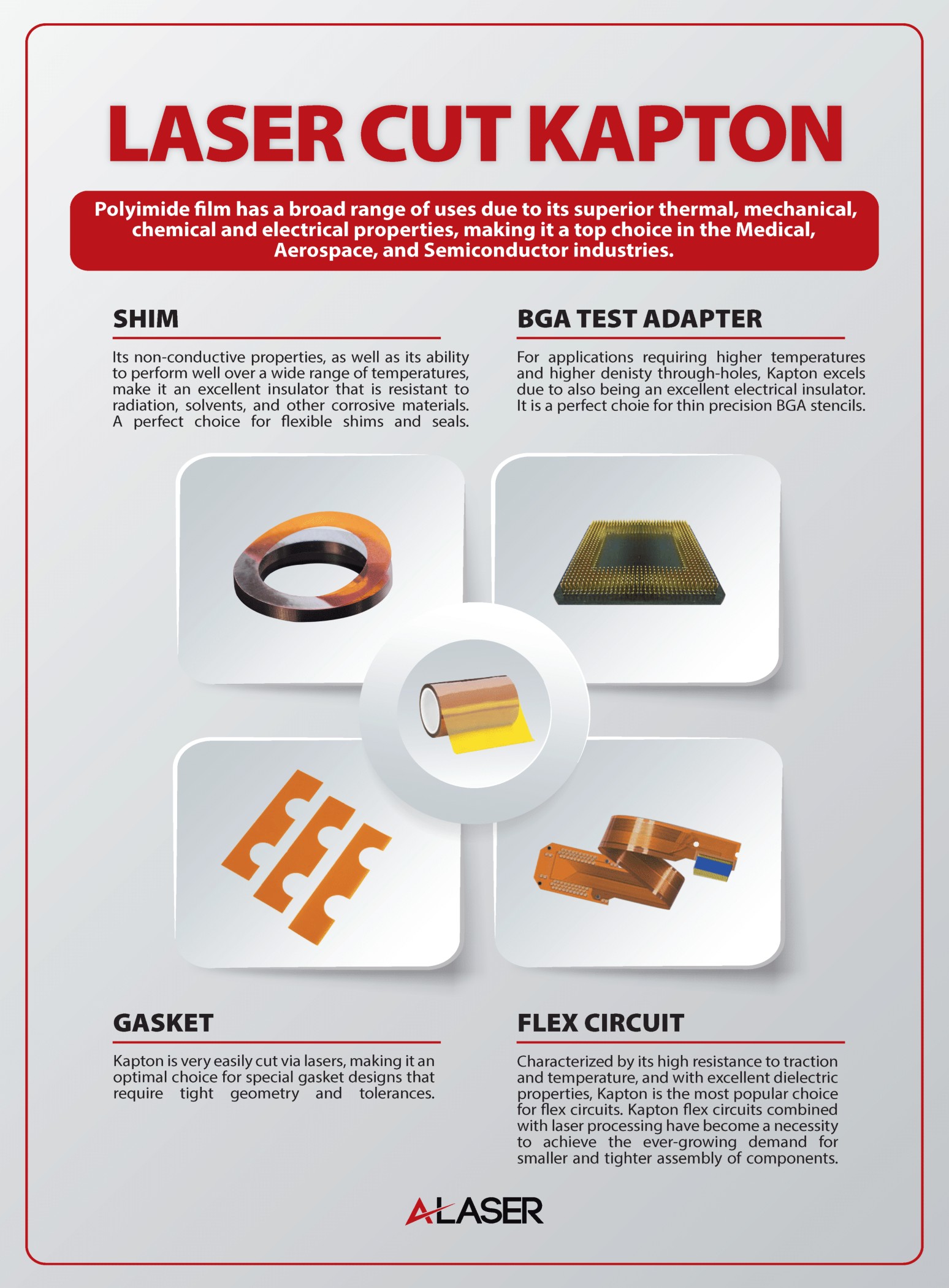
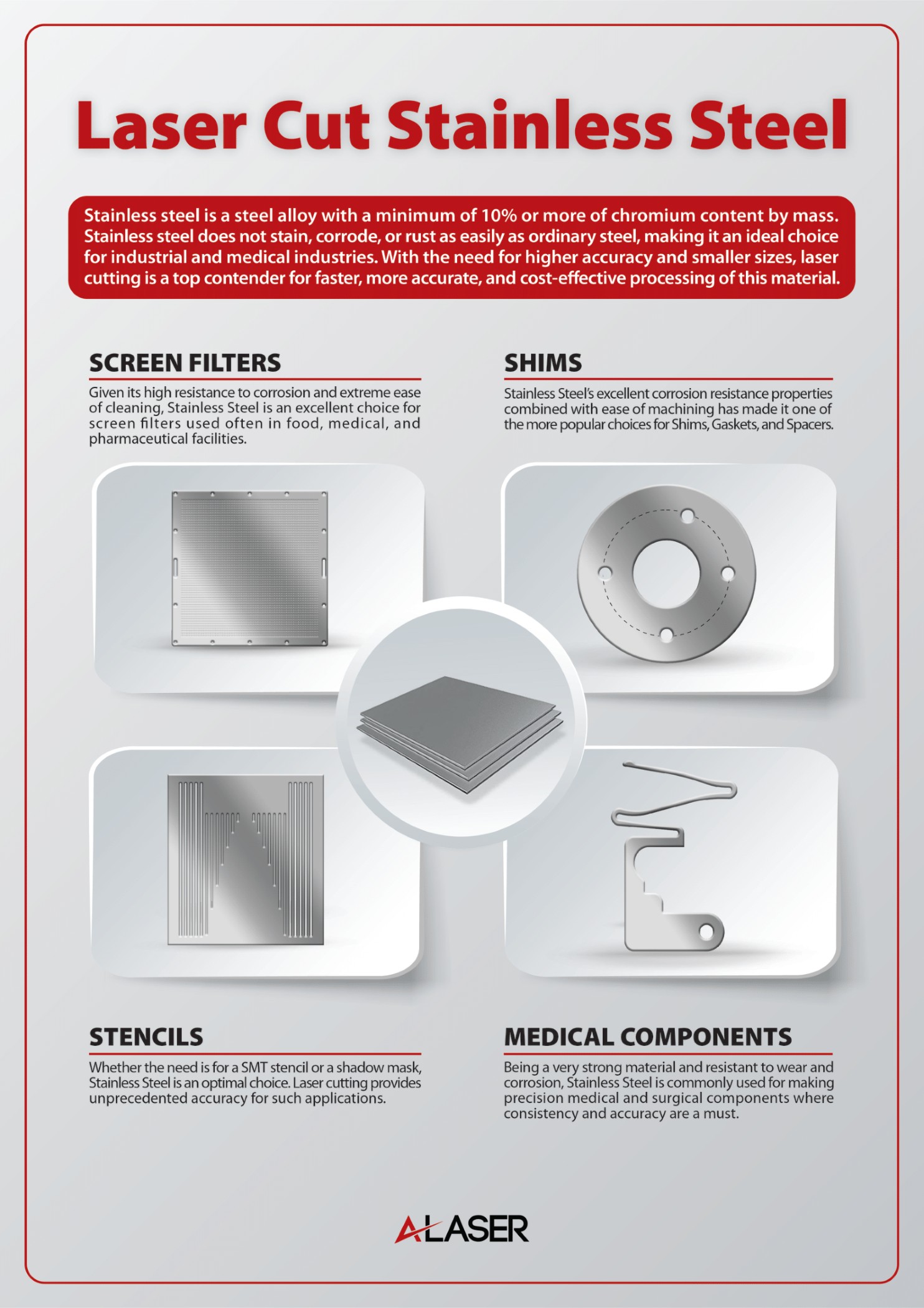
In conclusion, the ability of different materials to hold tight tolerances when manufactured into precision components is inherently variable. Metals like stainless steel and other metal alloys exhibit stable properties under controlled conditions, enabling the achievement of micron-level tolerances. On the other hand, polymers and rubber-based materials are subject to environmental factors such as moisture absorption and temperature variations, which can cause significant changes in their dimensions over time. Graphene, though capable of holding tight tolerances, also depends on its thickness and specific application constraints. Consequently, not all materials can attain the same level of tight tolerance, making it crucial to consider the unique properties and limitations of each material when planning a manufacturing project. Understanding these differences ensures the selection of the appropriate material and manufacturing method to meet the desired precision and functionality.