How Do Different Cutting Technologies Affect the Accuracy of Small Features?
Different cutting technologies have distinct impacts on accuracy, which can affect the overall performance and durability for small features. As precision components continue to be a necessity of modern and future technologies, demand for smaller and more accurate geometries has become the norm. The vast array of countless designs and applications are taken from the concept stage through manufacturing from a variety of precision manufacturing methods. Each method available today encompasses tremendous capabilities and focuses on the area of expertise and industry needs. Maintaining accuracy is the common factor between service providers and there are challenges that complex geometry manufacturing work continuously on to meet specifications. Here’s a breakdown of how various methods influence accuracy of small features:
Precision MFG Technology | Accuracy of Small Features | Factors Affecting Accuracy | Strengths/Limitations |
---|---|---|---|
Laser Cutting | Ranges from +/- 5um to 25um depending on system | Beam diameter, pulse rate, frequency, non-contact cutting. Material properties, micro burrs. | Cutting of thin materials excellent, low vibration, repeatable process. Some systems are prone to heat affect. |
CNC Machining | Accuracy as close as 10um | Cutting tool diameter, speed, vibration, Heat affect, Forces can cause distortion. | Great for 3,4,or5 axis. Thicker materials are good. Heat affect can occur. Rapid machining. |
Waterjet Cutting | Accuracy for many projects at +/- 25um | Abrasive type, size, water pressure, cutting speed, nozzle diameter, material properties. | No heat affect. Wider kerf width compared to laser cutting, potential for moisture absorption in some materials. |
Wire EDM | Accuracy as tight as +/- 2um to 5um. | Electrical parameters, dielectric fluid, electrode shape and material, material conductivity. | Machining hard materials, intricate shapes. Conductive materials, slower process than some other methods. |
The table is an indication of some of the factors that can affect accuracy in complex geometry manufacturing, but each project is specific with specifications and challenges. Through experience in machining small features, the industries involved in the manufacturing processes take great care in preventing non-conforming products. However, when challenges arise, there are multiple avenues taken to bring in the tolerance to nominal with sustained accuracy and repeatable quality.
Key Considerations of Different Manufacturing Methods:
- Material: The type of material being cut significantly impacts the accuracy of any cutting technology along with the thickness. Harder materials tend to take longer as more power, but a slower cut speed or rate is applied.
- Machine Precision: The quality and calibration of the machine play a crucial role in achieving accurate results. Maintenance schedules are a requirement for high end precision and can be administered under ISO certification standards.
- Application: The specific requirements of the application will determine the most suitable cutting technology. Industries like medical devices, aerospace and defense applications are stringent in fine detail machining of components. Precision cutting of small parts is synonymous with applications and having consistent accuracy is a key factor.
- Environmental factors: Temperatures, and vibrations in the surrounding environment all can affect the accuracy of small feature machining. Parts manufactured in a controlled climate can shrink or expand during shipping or while in inventory. Discussions on how materials are stored, shipped and received can aid in preventing issues.
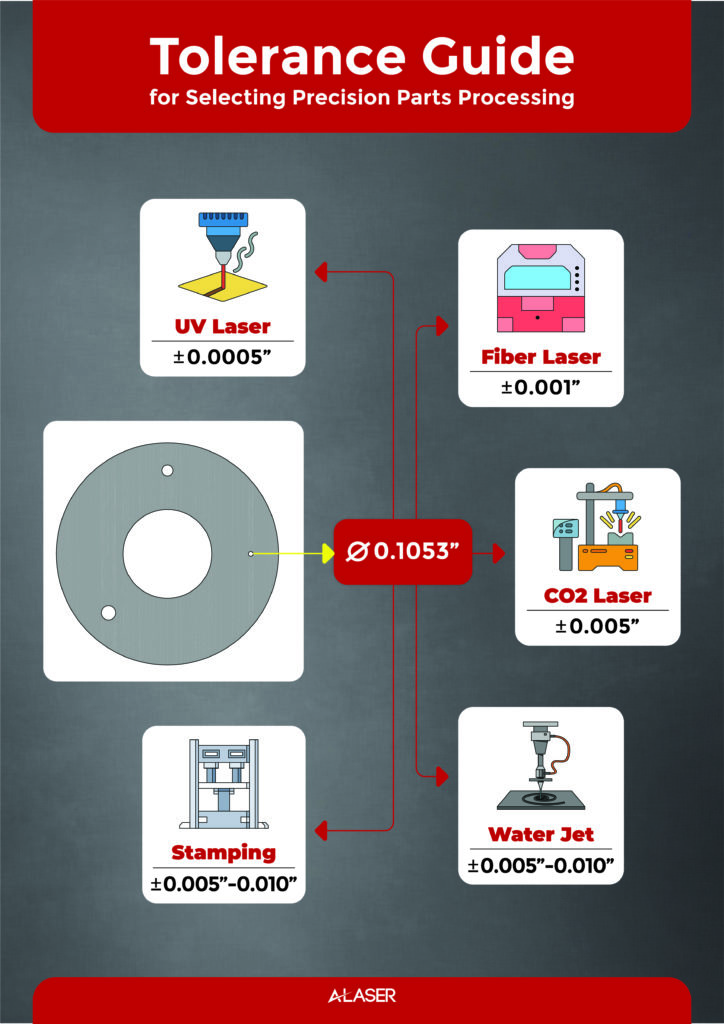
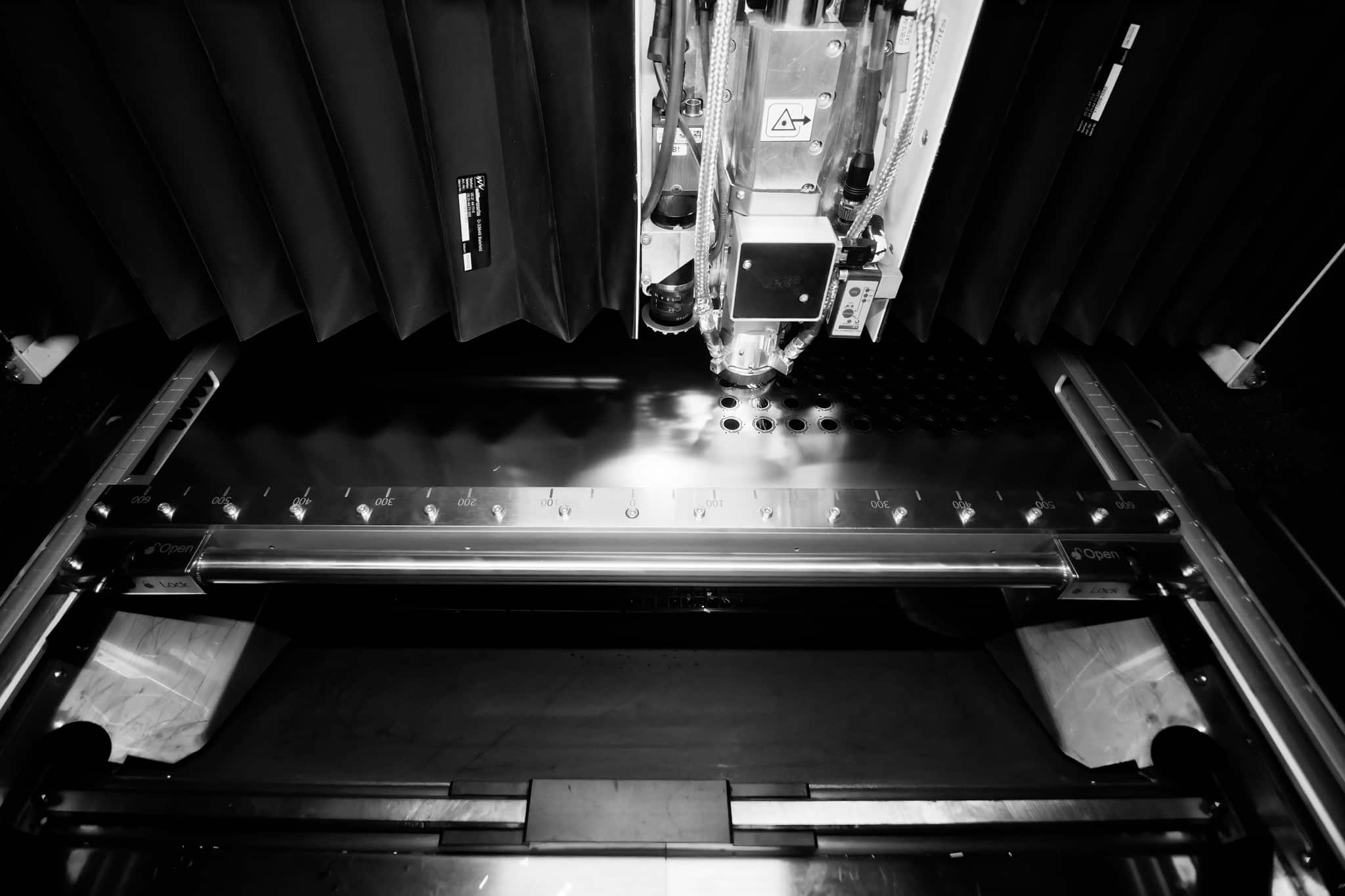
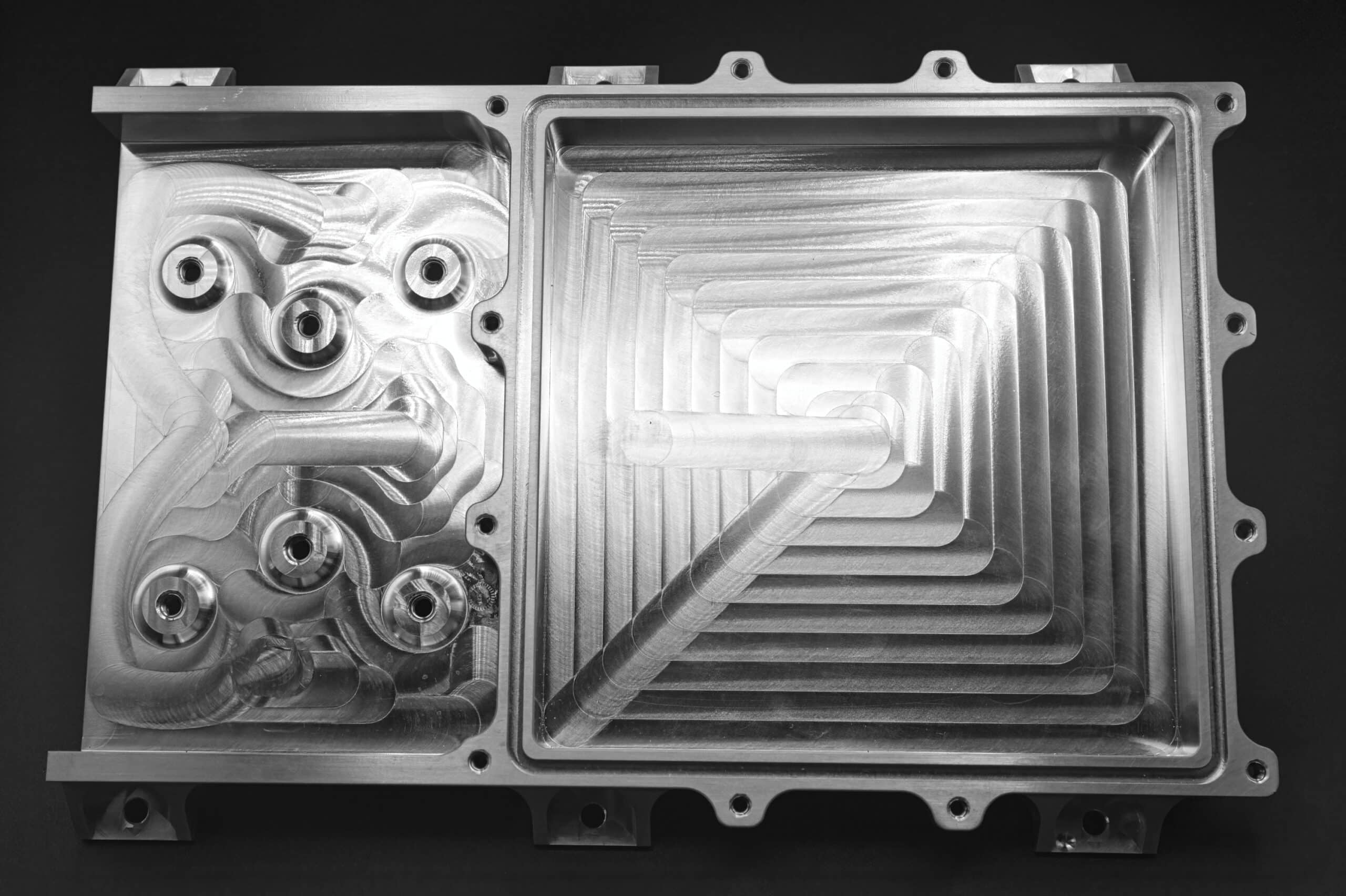
Ultimately, the choice of cutting technology for achieving accuracy in small features is influenced by a multitude of factors, including the material type, machine precision, application requirements, and environmental conditions. Each method, whether it be Wire EDM, laser cutting, or another technique, brings its own set of advantages and limitations. Ensuring consistent accuracy involves careful consideration of these variables and diligent adherence to maintenance and quality standards. By understanding and addressing these key considerations, manufacturers can optimize their processes to produce high-precision components that meet the stringent demands of industries such as aerospace, medical devices, and defense. The ongoing advancements in cutting technologies and methodologies continue to enhance the precision and reliability of manufacturing small features, paving the way for innovation and excellence in various fields.