Taking Stainless-Steel Shims from Prototype to Production
As a leading provider of laser manufacturing services, we are thrilled to share the incredible journey of transforming stainless steel into high-precision laser-cut shims. From the initial prototype stages to full-scale production, this process showcases the exceptional capabilities of laser cutting technology. These precision shims are not merely components; they are the unsung heroes that ensure flawless performance and reliability across a myriad of industries, including aerospace, automotive, and electronics. In the following paragraphs, we’ll review the sometimes-challenging processes, advanced technologies, and innovative solutions that make laser-cutting an indispensable part of modern manufacturing. Join us as we illuminate the pivotal role of precision shims and explore how our expertise drives excellence in every project.
What is a Metal Shim?
Stainless steel is a wonderful material that can be seen from your kitchen cutlery to sophisticated mechanisms in medical devices. Shims and the applications they are used for fall into similar categories from simpler uses to being part of sensitive applications and devices. In brief, a shim made from stainless steel will be a flat manufactured tool used to fill gaps, make alignment adjustments of machinery, to level machines and systems, and refine tolerances in manufacturing. These are some of the most common uses of stainless-steel shims, but often they are customized for industry use. This is where laser manufacturing has excelled in supporting new shim designs and the prototype stage.
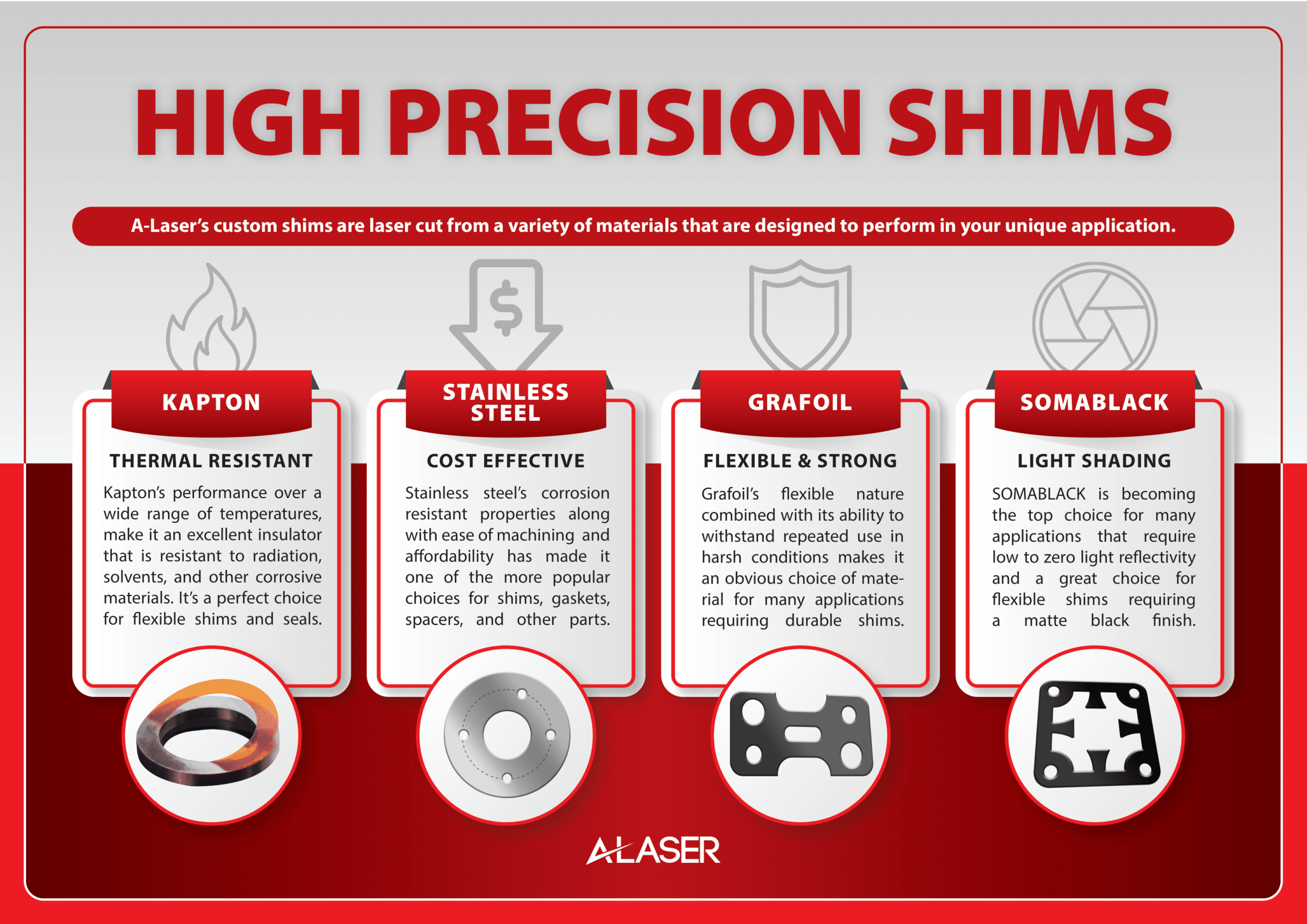
The Value of Prototyping
Laser prototyping services have some great advantages to producing shims rapidly for review, testing and evaluation. The process begins with receiving the CAD (Computer Aided Design) file, that has the digital data of the proposed shim. The customer will provide the type of stainless-steel alloy to be used and the desired thickness of the shim. Based on this information of geometry, material and thickness, the laser manufacturer will decide what laser technology is best for the project with systems such as ultraviolet or fiber laser technology, for example. Using laser technology, there are options to manufacture one single shim, or have multiple iterations done all at the same time. This can speed up the prototyping stage not only in design choices but also for the materials selected. With the approval of a prototype, smaller evaluations may be made and if the shim is destined for production support, laser technology can easily adjust.
Becoming a Partner in The Supply Stream
The business of manufacturing precision parts relies on continuous cycles of orders. There can be numerous smaller runs that include R&D and Prototype and longer production volume manufacturing. As this topic has been reviewed, laser service providers can take the knowledge gained from the prototyping stage to become a preferred supply stream partner. The hard work of testing and evaluation, review and confirmation has been completed in the prototype phase. From this earlier processing, the manufacturer knows the following:
- Material: What is the material and what is the lead time and cost for it.
- Process Time: The prototyping stage allowed the manufacturer to fine tune laser settings and make required adjustments to meet the criteria of the stainless-steel shim.
- Quantities: Quantities and demand schedules are often estimated at the prototype stage. As production moves forward it is important for manufacturers to direct the needed resources of personnel and production time.
- Inspection level: Information from the customer on the level of inspection is added to the throughput estimate. Is it AQL inspection levels, 100% inspection, or some other level? Knowing these will be part of the scheduling process.
- Post Processing: Additional factors such as post processing may be needed to refine the edge quality of the shim. Methods like tumble deburring and electropolishing are option available and should be discussed prior to manufacturing.
Transition or ramp up from prototype to volume manufacturing is the result of coordinated efforts from all parties that include the customer, primary manufacturer, and all supporting subcontractors. This represents the best in supply stream manufacturing.
Conclusion
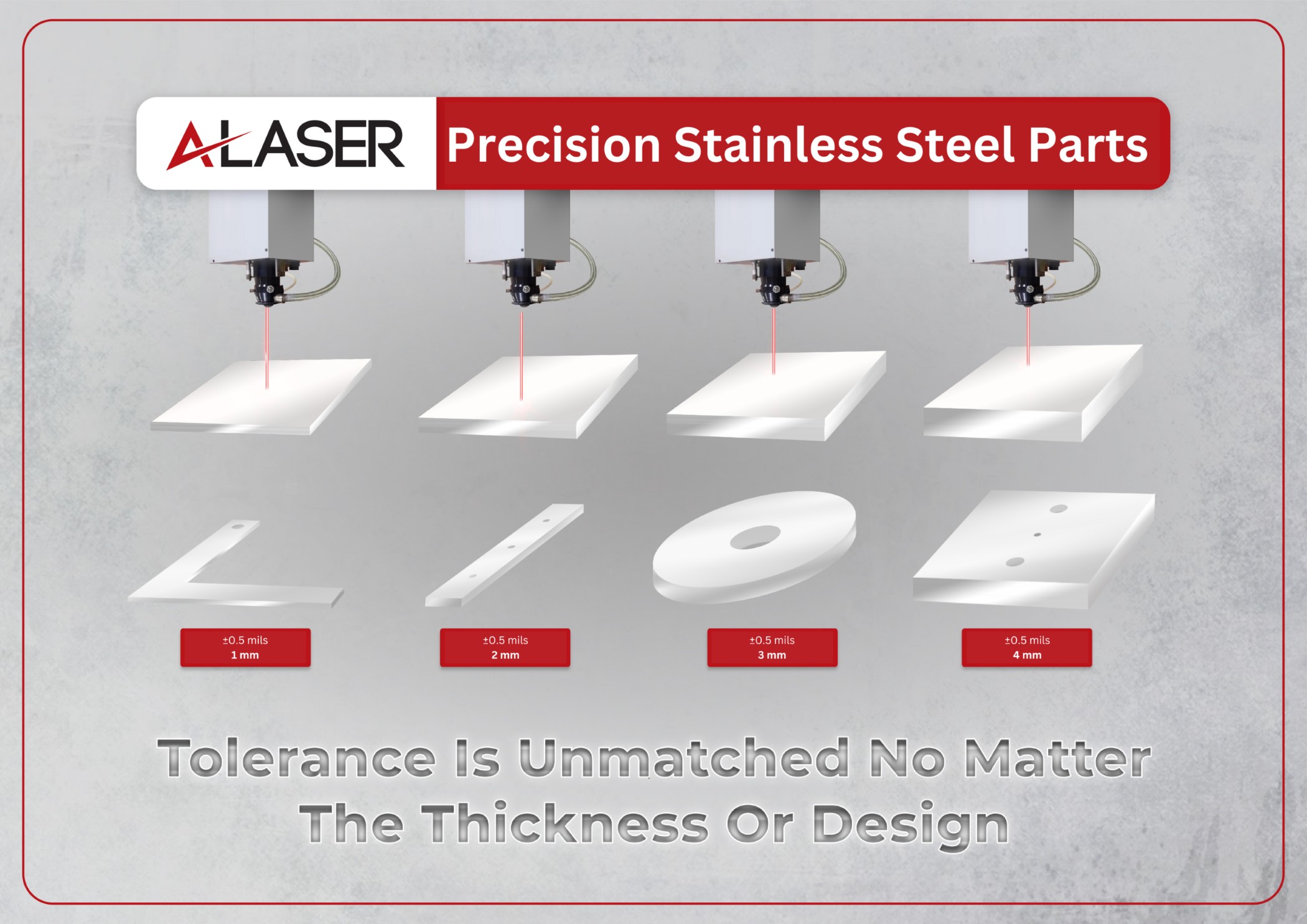
In essence, the transition from prototyping stainless-steel shims to full-scale volume manufacturing is a journey that hinges on precision, collaboration, and adaptability. By leveraging the insights and efficiencies gained during the prototyping phase, manufacturers can seamlessly scale up production, meeting both quality standards and delivery timelines. The ability to refine processes, predict material needs, and adhere to inspection levels ensures that the final product not only meets but exceeds customer expectations. As such, the role of laser technology and strategic planning in this transition cannot be overstated, establishing manufacturers as reliable partners in the supply chain and champions of innovation in the engineering landscape.