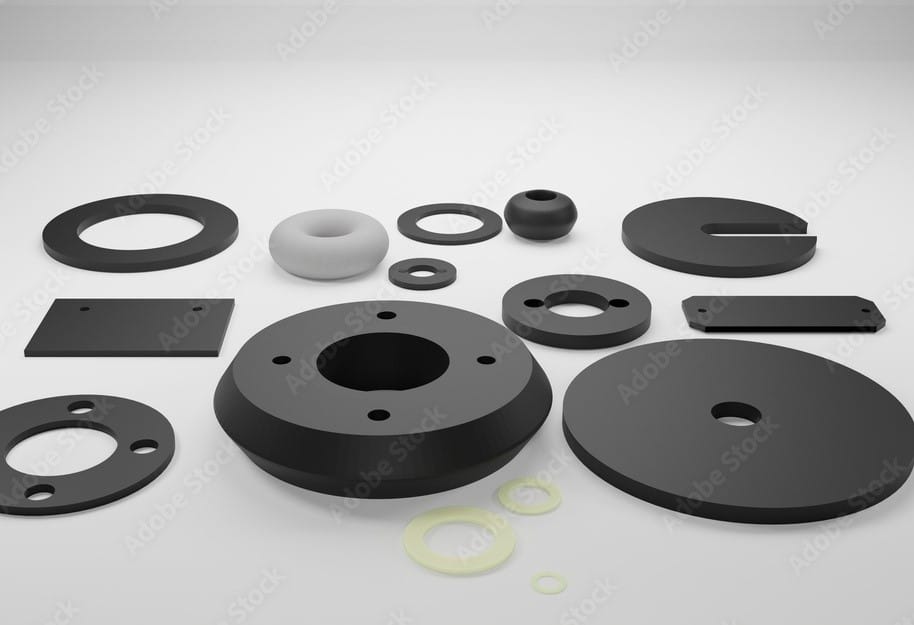
Sealing Its Place in Manufacturing
For gaskets and seals that are resistant to chemicals and extreme temperatures while being flexible, silicone rubber is a perfect solution. Laser cut silicone rubber is being utilized in numerous ways for industrial system integrity to supporting products and devices for medical use, automotive and other sectors. It’s kind of funny to think about walking on the beach and that the sands could potentially become silicone rubber. The process in brief involves extracting silica from sand, rocks or other natural sources and combining the silica with other chemicals in a complicated process to form the base material that can be molded into products or into raw forms for additional processing and manufacturing needs. It is this raw form of silicon rubber that laser manufacturing transforms the blank sheets or rolls into laser cut components. Before discussing the different types of laser components that are made through laser technology, there are factors to consider what type silicone rubber will be best for your project.
Choosing The Right Silicone Rubber
By using laser technology, cutting silicone rubber will result in very high accuracy and durability for the use it is intended to support. Choosing the best type for your project will be assisted by answering the following questions:
They Grade of Silicon Rubber: Silicone rubber comes in different grades. For example, 40A durometer or 60A durometer. A durometer refers to the hardness of the material. A softer durometer may be prone to melting with higher laser power. A harder durometer may cut easier, but not best for an application requiring more flexibility.
Thickness of the Silicone Rubber: Laser technology is greatly affected by the thickness of the material that is being cut. Thinner grades of silicone rubber from 0.127mm to 1.0mm thick, will be a good fit for diode laser systems, like the ultraviolet wavelength. Thicker grades will be a better fit for CO2 laser systems.
Laser Manufacturing-Taking Design to Reality
There is a great amount of information on this website and others on laser cutting in general, but for materials like silicone rubber there are factors that laser service providers keep in mind and adjust accordingly to the project in process like:
- Laser Power: Depending on the make-up of the silicone rubber, laser power can be adjusted to the proper wattage needed to achieve a clean-cut edge. Factors affecting power include material thickness, geometry and tolerance.
- Laser Speed: Laser speed refers to the duration of time the laser cycles during the cutting process. Laser speed can be adjusted in millimeters per second. This can directly affect the laser cost, as longer laser time costs more and affects the throughput time.
- Laser Passes: Laser often operates in passes of the laser to the material, rather than cutting or ablation in one single pass.
- Project Goal: Proof of concept projects to R&D to full production volume manufacturing can and do occur with laser manufacturing as well as other platforms. Laser settings, set-up and preparation with R&D and proof of concept may change when it comes to production volumes. What works as a concept may need additional laser time to dial in parameters best fit to support a production schedule.
Assuring The Integrity of Systems
Seals, gaskets, O-rings, all are used in some way to keep the integrity of the systems they are applied to. This is a major use of silicone rubber material because of the characteristics it has in being flexible, durable, chemically resistant, and able to withstand great fluctuations in temperature. The following table demonstrates some of frequently used applications of silicone rubber:
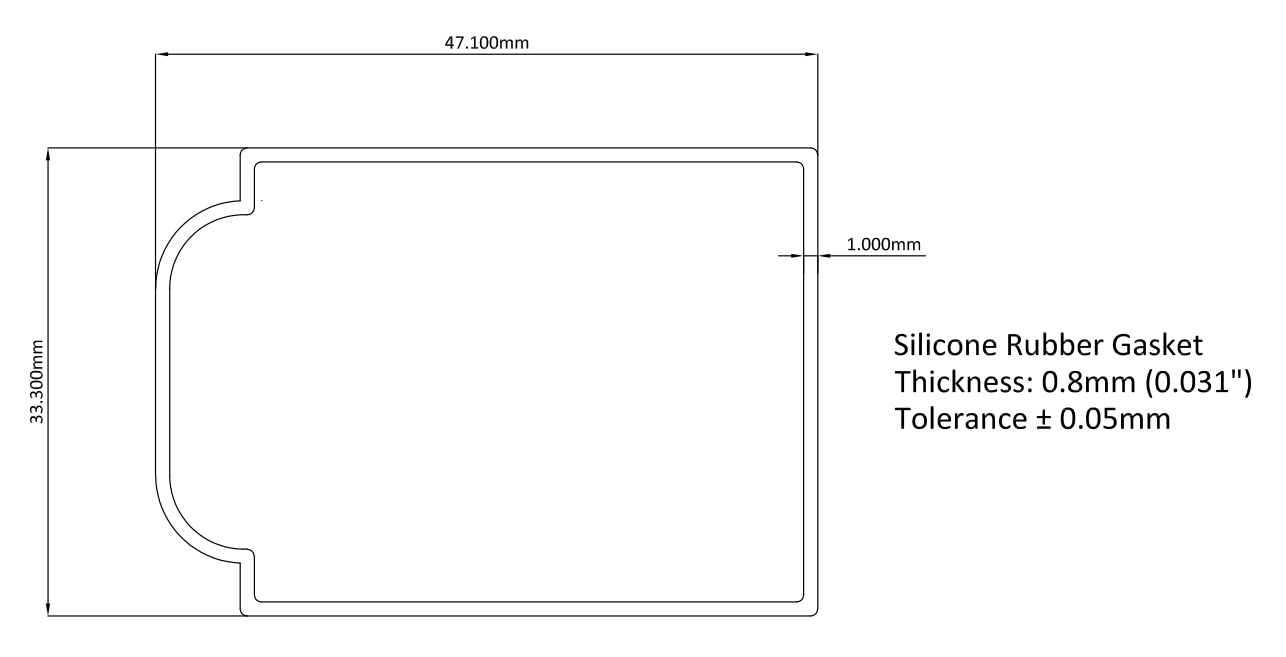
Industry | Application | Benefits of Silicone Rubber |
---|---|---|
Food and Beverage | Seals for food processing equipment, gaskets for ovens and refrigerators, seals for beverage containers. | FDA-approved, non-toxic, resistant to food acids and oils, withstands high and low temperatures. |
Electronics | Seals for electrical enclosures, gaskets for electronic components, insulation for wires and cables. | Excellent electrical insulation, resists ozone and UV radiation, flame-resistant options available. |
Automotive | Engine seals, gaskets for engine blocks and heads, transmission seals, door and window seals, HVAC system seals. | Withstand high temperatures, resist oils and fluids, provide good weather resistance. |
Medical | Medical implants (pacemakers, catheters), surgical tubing, seals for medical devices, drug delivery systems. | Biocompatible, non-toxic, resistant to sterilization methods, excellent chemical resistance. |
Aerospace | Seals for aircraft engines, fuel systems, hydraulic systems, and landing gear. | Excellent temperature resistance for extreme conditions, lightweight, good resistance to chemicals and ozone. |
The applications of silicone rubber are vast, and the above list is a glimpse of uses in industrial and commercial applications. In laser cutting manufacturing, the types of components are mainly flat, 2D profiles. 3 Axis or greater types of components are made through technology like injection molding.
Concluding Thoughts
Laser cutting offers a precise and efficient method for processing silicone rubber, enabling the creation of intricate and complex shapes with minimal material waste. By carefully selecting the appropriate laser type (such as CO2 or diode lasers) and optimizing parameters like power and speed, manufacturers can achieve high-quality cuts with clean edges and minimal heat-affected zones, ensuring the integrity and functionality of the final silicone rubber product.