Fiber Laser Applications
Laser Operating Modes and Use Cases
Fiber laser technology can be used to achieve different goals, and several factors can be changed for different purposes. In this section we will discuss operating modes of fiber lasers, as well as some fiber laser applications and use cases.
Operating Modes of Laser
Aside from wavelength the laser source can be generated in different ways. Namely these are:
- CW – Continuous Wave
- Pulsed
- Phase Shifting
CW – Continuous Wave
This term indicates that the beam is continuous or constant. More specifically the rate of photons produced per unit time is uniform.
The term wave here should not be confused with wavelength. These are two separate parameters.
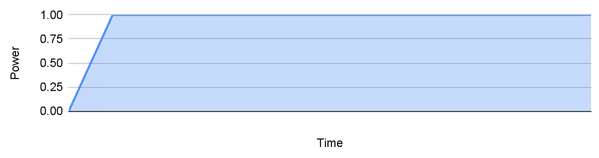
Pulsed
Pulsed laser sources are more common and cheaper than CW systems. As the name suggests the laser source is “pulsed” resulting in peaks and troughs in photon output.
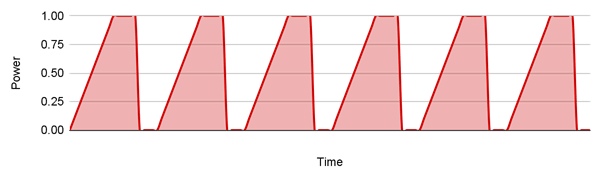
The graph shows power against time. In pulsed laser systems it is common to refer to “Pulse energy” as a variable. This will normally be set in Joules (J). Less common but not unheard of is to set this in volts (V) which will be combined with the wattage of the laser to create the true energy value.
Ramp Up Time
In each of the above examples there is a gradual increase in power at the beginning which tops off at the desired value. This is known as “ramp up” time or “Rise time”. This is due to multiple factors however most systems will have this measured and it will be taken into account when feeding back calculations of total power, pulse energy or the like.
Pulse Length
Pulse length or pulse width will be denoted in units of time. This is the length of time between the start and end of a pulse.
Period
The period is the time between the start of one pulse and the start of the next.
Threshold
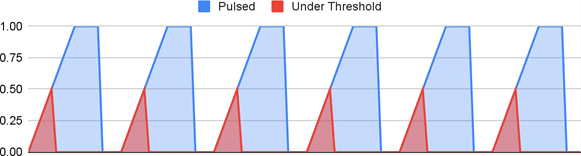
In practice the pulse is only effective when the energy rises above a specific level. As shown above. The blue area will be considered active whilst the red is inactive.
Continuous Wave is like a fluorescent bulb where the light is continuously generated due to current passing through the element. Whereas a pulsed source is more like an LED bulb that rhythmically fires bursts of light.
Why?
The option to use CW or pulsed outputs depends on a few factors. Heating
Due to overheating issues, it is important to maintain adequate temperatures inside the laser diode. The internal temperature must remain a threshold determined by the manufacturer.
This temperature is proportional to the average power of the laser. Therefore, in many instances prolonged use of a laser will require its output to be pulsed rather than CW to allow for cooling.
Optics Stability
The optics within a system can often be victim to heat. In older systems mirrors can become distorted if a laser is continuously reflected off as there will always be a little absorbance.
Focusing optics can also become damaged over time especially if there is any contamination on the lenses or windows in line. Pulsed outputs reduce this risk significantly.
Use Case
The aforementioned effects are not the only reasons to pulse a laser. In some circumstances defined patterns can be created by pulsing at frequencies paired with the motion of the beam. This can be used in the following:
- Laser welding
- Laser surface structuring
- Laser marking
- Laser cutting*
When it comes to laser cutting a rule of thumb would say that the ideal cut is maximum power maximum speed. In real life this is difficult to achieve whilst holding tolerances. If a CW laser is used to cut whilst moving relatively slowly the heat affected zone will increase drastically. Pulsing allows for control of the energy being absorbed by the cutting medium thus reducing the heat affected zone.
Cutting with a CW laser can result in a consistent cut but this is largely material dependent. CW can also offer strong welded joints in both plastic and metal parts.
Fiber Laser Applications
Fiber lasers applications range from beauty treatments, surgery or communications to manufacturing. This document will focus on manufacturing.
When to Choose IR or UV
There are no set rules for choosing one technology over the other. Rather there are many overlapping factors that will determine which is best.
Power
When it comes to a question of Power IR can generate massive amounts of power capable of cutting through tough thick materials. This does however cause subsequent effects on the material being cut. In general one would find that the heat affected zone (HAZ) will be much larger when using IR compared to UV.
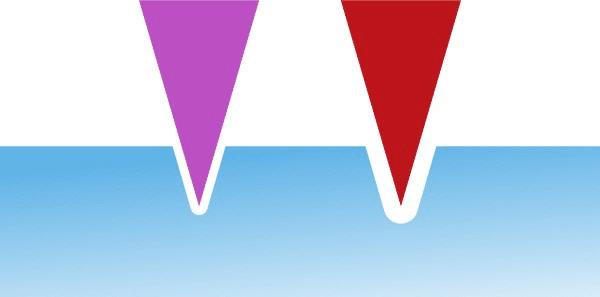
Both lasers interact with the cutting surface in different ways. IR is effectively a very high density heat transfer mechanism. When the beam interacts with a material it burns a very small section (assuming the presence of oxygen). It is this action that separates the material resulting in the desired shape.
Pulse Length
There are a few colloquial terms for lasers which have a pulse length output within certain time ranges.
Name | Symbol | Base 10 | Decimal |
---|---|---|---|
yotta | Y | 24 | 1,000,000,000,000,000,000,000,000.00 |
zetta | Z | 21 | 1,000,000,000,000,000,000,000.00 |
exa | E | 18 | 1,000,000,000,000,000,000.00 |
peta | P | 15 | 1,000,000,000,000,000.00 |
tera | T | 12 | 1,000,000,000,000.00 |
giga | G | 9 | 1,000,000,000.00 |
mega | M | 6 | 1,000,000.00 |
kilo | k | 3 | 1,000.00 |
hecto | h | 2 | 100.00 |
deca | da | 1 | 10.00 |
0 | 1.00 | ||
deci | d | -1 | 0.10 |
centi | c | -2 | 0.01 |
milli | m | -3 | 0.001 |
micro | μ | -6 | 0.000001 |
nano | n | -9 | 0.000000001 |
pico | p | -12 | 0.000000000001 |
femto | f | -15 | 0.000000000000001 |
atto | a | -18 | 0.000000000000000001 |
zepto | z | -21 | 0.000000000000000000001 |
yocto | y | -24 | 0.000000000000000000000001 |
Material Selection
The 1064 nm wavelength is well suited to cut metals. Mostly stainless steel however many systems can also cut Carbon steel, Silicon steel, Aluminum, Titanium, Galvanized steel, Zintec, Brass, Copper, Alloys, Electrolytic Plate and many more. The exact materials vary depending on the make and model of the laser.
Case Studies
SMT Solder Paste Stencils
Solder paste stencils were originally created with photo etching. A process which involved adding a layer of light sensitive chemicals to the metal surface. These chemicals would be activated in select areas by a light source. Once activated the chemical would begin to etch through the metal resulting in a void being left.
To improve on this process laser cutting was introduced. Looking at the selection process the final choices were mostly driven by the materials being used, namely stainless steel. Based on the absorption rate of different wavelengths of laser with regard to stainless steel there is a peak around the 1064nm wavelength. This points towards Nd:YAG fibre lasers being ideal.
Soon after fiber laser stencil production systems were developed, they became the standard.
Solid State Battery Masks
For the same reasons as the stencil industry the material choice drove the laser choice. This time with Molybdenum. An element metal that has very rigid properties but still absorbs IR radiation peaking around the 1064nm length. This material requires high power density to cut through effectively.
Paper Cutting
Cutting so called natural materials such as paper, cardboard or wood. The best laser choice is likely UV or Far IR. Far IR being a CO2 laser as opposed to a fiber. At the 1064nm (near IR) range paper is very difficult to cut. It is due to this nature that Masking tape is an effective tool for blocking low power fiber laser beams aiding in small part manufacture.
Human Soft Tissue
Looking at developments in surgery soft tissue can be accurately cut with CO2 Lasers. Whilst in this case UV would also cut through it is widely known that UV causes further damage to human skin.
Laser Metal Deposition of Copper on Diverse Metals
Investigations to the use of a green laser source to enable copper deposition on differing bases was investigated by Prasad et al. By investigating the absorptivity of different lasers and materials the team determined that deposing onto Aluminum or Titanium alloy were ideal when combined with a Green (515nm) laser source.
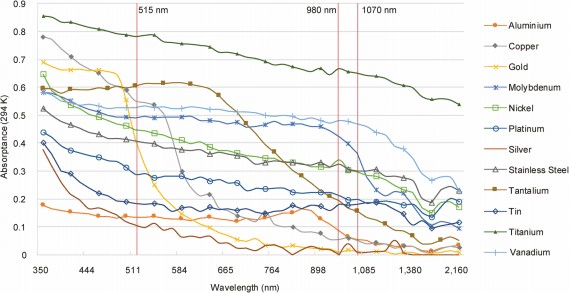
Warnings
PTFE
PTFE (polytetrafluoroethylene) is a commonly used polymer in many industries. There is a danger when cutting with IR (and UV) that poses the laser operator to a risk of “polymer fume fever” or “fluoropolymer fever”. This is an inhalation fever caused by the fumes that are released when laser cutting this material. These chemicals are released when the polymer reaches temperatures of 300 to 450 °C. Exact methods of isolation and fume extraction vary from country to country and state to state in the US.
PVC
Cutting PVC with an IR Laser releases hydrogen chloride gas. This in turn reacts with latent moisture to produce hydrochloric acid. This can ruin a laser system completely.