Working with Lasers
Laser beams. These innocent beams of light have a lot going for them. Many think they are complicated, but in reality, they are pretty coherent. Whilst we may not actually have “Sharks with frickin laser beams,” we still have some cool toys at our disposal.
Working in the laser industry opens up your eyes to creative solutions that you wouldn’t otherwise think of. It’s not uncommon for an engineer to stay late and laser cut a template to hang that bathroom shelf perfectly. Or to bring a widget from home to etch some design or message into. The non-contact nature of laser systems enables so many applications that the list is truly endless.
About a year ago, I was working on my car. The turbo wastegate actuator was sticking and had to be replaced. Many engineers have had the infuriating experience of losing a circlip deep inside an engine bay. These little devils seem to defy Newtonian mechanics when one is at the most desperate of times. They will invisibly spring through the air and make a little noise on the surface closest to you, only to be found a week later in the back pocket of a different pair of jeans. After going through this ordeal when it was late and dark, I had no option but to get creative. Use what you’ve got. By chance I had access to an infrared laser and a ton of stainless steel sheets.
The concept is simple. Fit something round into a slot on an axle to stop things from falling off. First I attempted to recreate the circlip exactly. How hard could it be? Outer diameter, innerdiamter and thickness add a couple holes to load it and you are good, right? The first was too strong and wouldn’t go on. The next, too soft and wouldn’t hold. The third was almost perfect, but still sprung away from me in my moment of need like the bizarro version of Tigger.
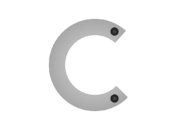
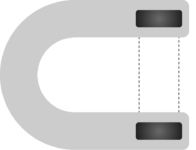
Looking at the design, I realised I was chasing someone else’s idea of the solution. Without the right tools and correct dimensions, I had to go simple. In the end I cut an open “C” shape to slide over the axle. However, rather than using structural strength to hold the clip in place, I utilised the go-to fastener for anyone who needs a quick fix: the trusty cable tie. Adding a couple slots for a cable tie to fit once the part was in place saved me a world of hassle.
The resulting design was simple, unique, and did exactly what I asked of it. One year on and the part holds, with no sign of coming off. It is in no way an improvement from the norm, but the satisfaction of designing, iterating, manufacturing, testing, and fitting my own solution was just so satisfying.
Working with lasers opens up a world of possibilities. When asked what I do for work, I can always feel my face light up with joy when I get to respond “I work with lasers.” The endless capabilities laser cutting can accomplish makes them the best choice for almost any project. Lasers offer a great balance of high accuracy, customization, and the actualization of a concept in rapid time.
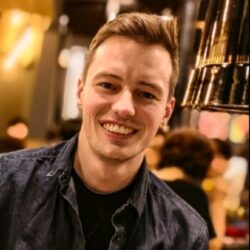
About the Author
Robbie is a motivated, focused, and dedicated Laser Engineer at A-Laser. Robbie studied Manufacturing Systems Engineering at Glasgow Caledonian University, graduating in 2013. He then took a graduate role at Tannlin Technology in the UK where he worked on the systems team. His role included product improvement, customer assistance, system building, and engineering analysis. His five years of experience working at Tannlin, often in the field, required thinking on his feet and working with limited resources. Outside of engineering, Robbie enjoys photography, as he likes to keep a part of his life in a creative field so that he can work that muscle when he needs to. Robbie excels in roles that combine technical expertise and project coordination and strives to deliver value to customers. Robbie is highly appreciated for his client-centric approach and his ability to build strong client relationships. If you have questions or want to discuss laser technology, please reach out to Robbie!