Why Do Some Projects Require Tight Tolerance?
The Rise of Tight Tolerance Control
Functionality, performance, safety and reliability are some of the factors why projects will require a tight tolerance. Manufacturing tolerances are extremely important to the integrity of the precision parts geometry, function and lifespan. This was not always the case back in the first half of the 20th century, when mechanical methods used measuring devices to the best of their abilities. However, inconsistencies made mass production challenging as parts were not always manufactured to exact dimensions. With a push to develop more stringent guidelines and processes, manufacturing turned to computer technology that in turn would form the base of highly sophisticated and precise manufactured parts. This technological move has embedded in all industries from optics, pharmaceuticals, electronics, energy, aerospace and many more with countless applications. Questioning if need you need a tight tolerance for your project and why some always seem to require it, depends on the industry and parts function.
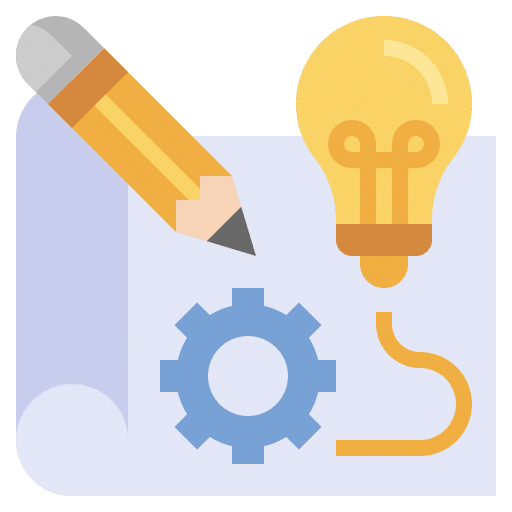
Designed Focus
We rely on experts in manufacturing to produce the goods and services used almost exclusively without ever thinking of the quality and how tight the tolerance must have been during the manufacturing process. We do notice greatly a reduction in performance when things do not work or function at diminished satisfactory levels, resulting in negative feedback on products. This pushes manufacturing to solve the issue or risk loss of revenue and perhaps public sentiment. Designing products or precision components with a tight tolerance is focused on diminishing flaws that could ultimately hinder public safety or adversely affect the reliability. Examples of industries and applications that demand tight tolerances and high quality are:
- Medical Industry: Safety in the use of surgical tools, syringes, diagnostic machines. Sterile bandages, gloves, and the systems that regulate gases and fluids all demand tight tolerances.
- Optics: Glasses, contacts, laser optics, cameras, all use optics in some way. These products can be exposed to harsh environments or function in clean rooms. They all are made to dimensions with demands for tight control.
- Defense Industry: Applications of defense related manufacturing are sensors for heat, temperature, and sound. Electronics for communications, weapons, ammunition, guidance.
- Oil and Gas Industry: This industry is highly dependent of use of flanges, gaskets, sensors, gears and monitoring electronics. Components such as these can be exposed to harsh environment’s and require continuous operation. Reliability and safety is key.
- Automotive: Components for all the moving parts must be made to be replaced if needed. Without having off the shelf uniformity, repairs would require more time and possible additional components. Aesthetics also are important for consumer satisfaction and brand loyalty. Tight tolerances ensure exposed parts look as great as they function.
To Maintain high quality manufacturing standards, industries work to be certified under ISO Standards, with ISO 9001-2015, as the most common. ASTM is another body of industry regulations, focused on safety and quality. The listed industries are a microcosm of the vast manufacturing world, all working to have their products and services held to highest levels possible.
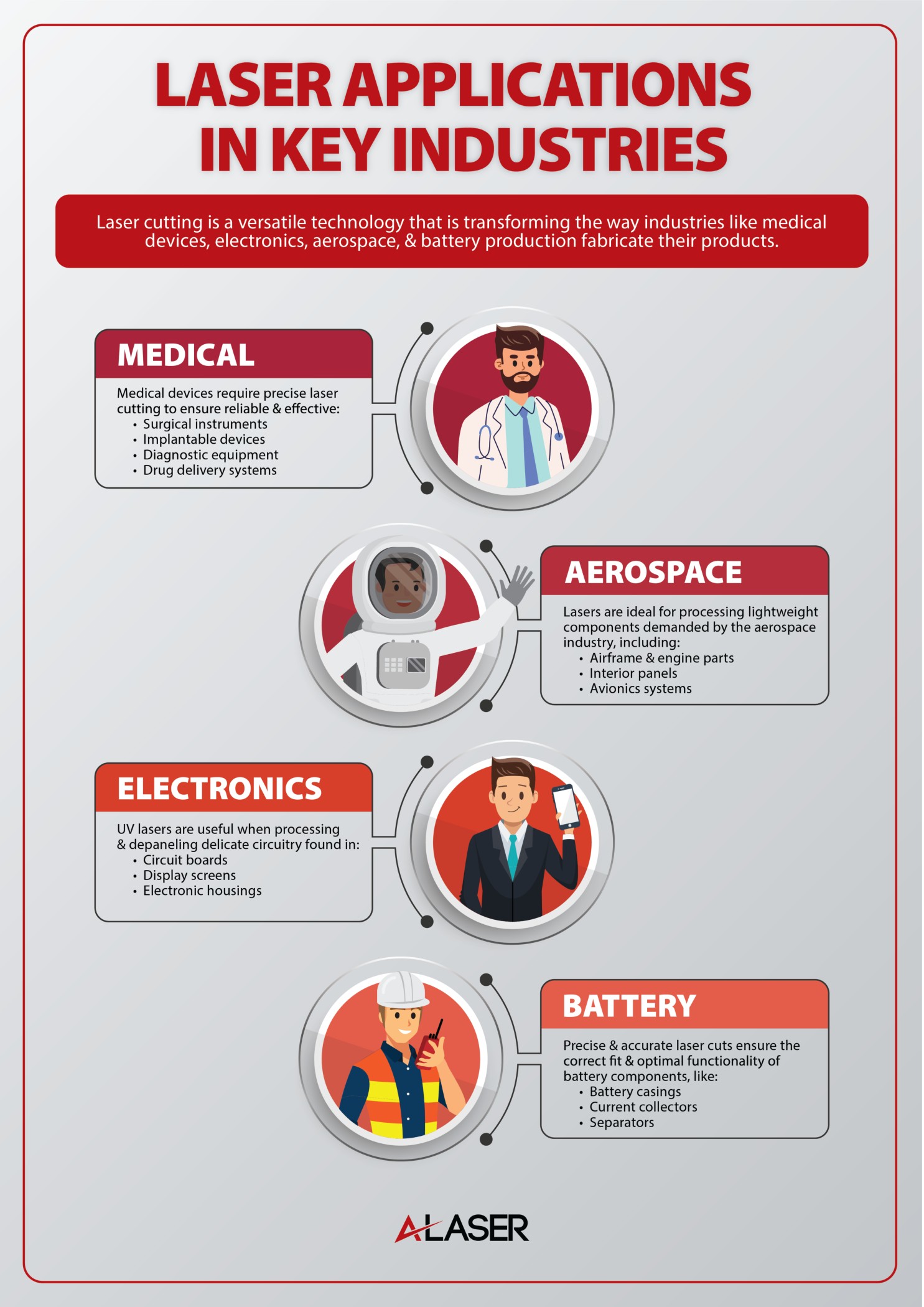
Do I Need Tight Tolerance?
If you work in a critical industry or perhaps developing a new technology, chances are you will need a tight tolerance. There are stages in manufacturing however where tight tolerance is not needed and this would be in R&D, prototype, and proof of concept. Your ideas and concepts can proceed at a rapid manufacturing pace, without the regulations of higher quality and tolerance controls. Developing new ideas and concepts require evaluation and testing and can take many months, with a multitude of iterations. In general, the idea of this rapid pace is to “see if it works”. Results, both negative and positive will allow for more testing or perhaps conclude to what was a good idea. Additionally, holding a tight tolerance is subject to the project and function of the manufactured component. A shim or gasket, requiring a tolerance of +/- 0.5mm may be entirely fine for the use and industry. While another similar project may require a tolerance of – 0.0127mm to +/- 0.0254mm. In manufacturing, the consensus is that a tight tolerance requires more cost and more time. Machines must be serviced more often and calibrated. Personnel must be trained, and practices demand higher levels of Quality Control. An open tolerance or a tolerance that the manufacturer deems larger than standard controls, generally will take less time to manufacture and require less quality control, resulting in lower cost.
In conclusion, while some manufacturing projects require tight tolerances due to the critical nature of their applications—such as in the medical, defense, optics, oil and gas, and automotive industries—there are also projects where such precision is less crucial. Critical projects necessitate stringent quality control measures, frequent machine calibration, and comprehensive personnel training to ensure that the components meet exact specifications for safety and functionality. These controls are vital for maintaining the integrity of products that could impact public safety or the reliability of essential systems. Conversely, not all projects demand such rigorous standards, especially during the R&D phase or in proof of concept stages, where rapid production and iterative testing are more important than precision. The balance between cost, time, and tolerance levels must be carefully considered based on the specific requirements and end-use of the product, ensuring that resources are allocated efficiently without compromising the overall quality and purpose of the manufacturing project.