What Post-Processing Methods Improve Edge Quality in Machined Parts?
The edge quality in machined parts can be improved by acid cleaning, tumble deburring, electroplating, electroless plating, and others. Precision cutting methods produce extraordinary parts with precision down to microns while holding extremely tight tolerances. Industries have long known that in order to keep costs down and prolong the lifespan of mechanical systems, precision parts must have repeatability and reliability. These factors are key to technological success in many aspects of our lives. Over the past 60 years development of CNC technology, laser cutting, stamping, die-cutting, plasma cutting and waterjet cutting have become the backbone of many of the precision components in use today. Along with this tremendous responsibility comes challenges for burr-free manufacturing and to improve the edge quality in machining.
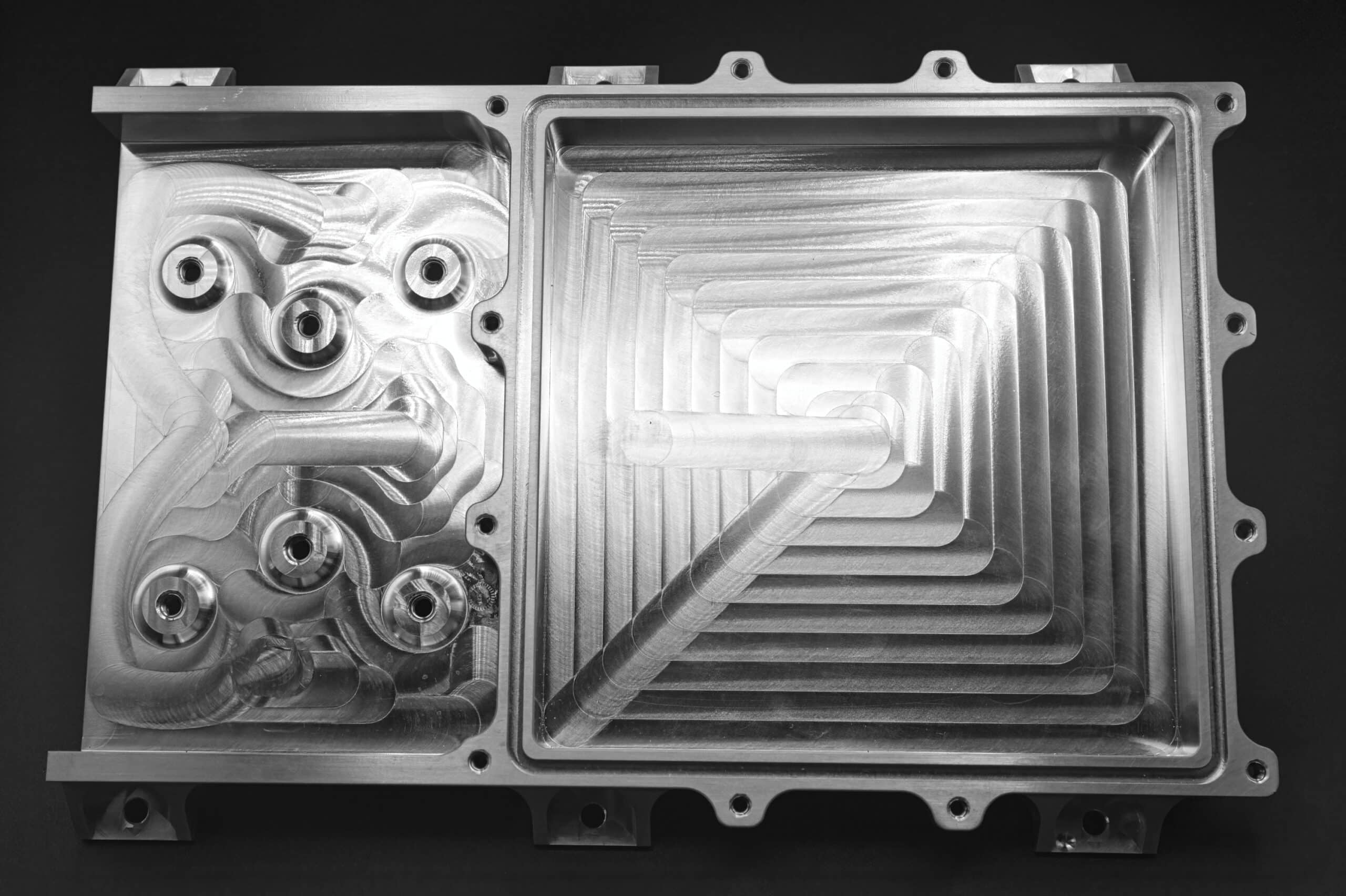
Factors Affecting Edge Smoothness and Burr Formation in Machining
The edge quality in machining can make or break a parts performance. Small burrs in metal parts can cause friction and rapidly wear down mated components. A roughened edge can affect the geometry and tolerance of very critical spacing. Factors that affect the smoothness of any cut or machined edge are subject to material, design and the manufacturing method used. Recurring obstacles that must be overcome are:
- Material Properties:
- Ductility: More ductile materials tend to form larger, more pliable burrs.
- Hardness: Harder, more brittle materials may produce smaller, sharper burrs or even fracturing.
- Cutting Parameters:
- Cutting speed: Higher speeds can generate heat, which affects material deformation and burr formation.
- Feed rate: The feed rate influences chip thickness and cutting forces, both of which affect burr size.
- Depth of cut: Deeper cuts can increase cutting forces, leading to larger burrs
- Tool Settings: CNC machining and laser cutting are good examples of manufacturing where burrs can form. Making the incorrect choices where the cutting begins and stops and how many passes a cutting tool makes, affects edge quality.
- High Thermal Energy: Metallics especially are prone to slag and burr formation. High direct energy as from laser cutting can redeposit slag or form surface burrs on the cut edge. CNC machining can also form burrs during the milling process.
- Other Factors: Power used (wattage), vibration, coolant used, and cut program, all can affect the overall cut edge quality.
Post Processing Methods in Use
When it comes to enhancing the edge quality of machined parts, several post-processing methods can be employed. These techniques aim to remove burrs, smooth rough edges, and improve the overall surface finish. Listed are some methods you can consider for your next project:
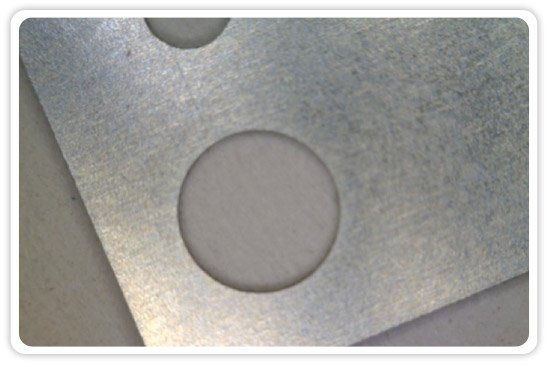
Mechanical Methods: These processes involve removing burrs (raised edges or ridges) created during machining/manufacturing:
- Manual deburring: Using hand tools like files, scrapers, and knives.
- Tumble deburring: Placing parts in a vibrating container with abrasive media.
- Abrasive blasting: Using pressurized air to propel abrasive particles against the part.
- Grinding: This process uses abrasive wheels to remove material and achieve a smooth surface. It’s effective for removing sharp edges and refining surface finishes.
- Polishing: This method involves using fine abrasives to create a smooth, glossy surface. It’s often used for aesthetic purposes and to improve surface integrity.
- Sanding: Using various grits of sandpaper to smooth out the surface of the machined part. Grits can range from 600,800, 1000 to 2000 grit or higher.
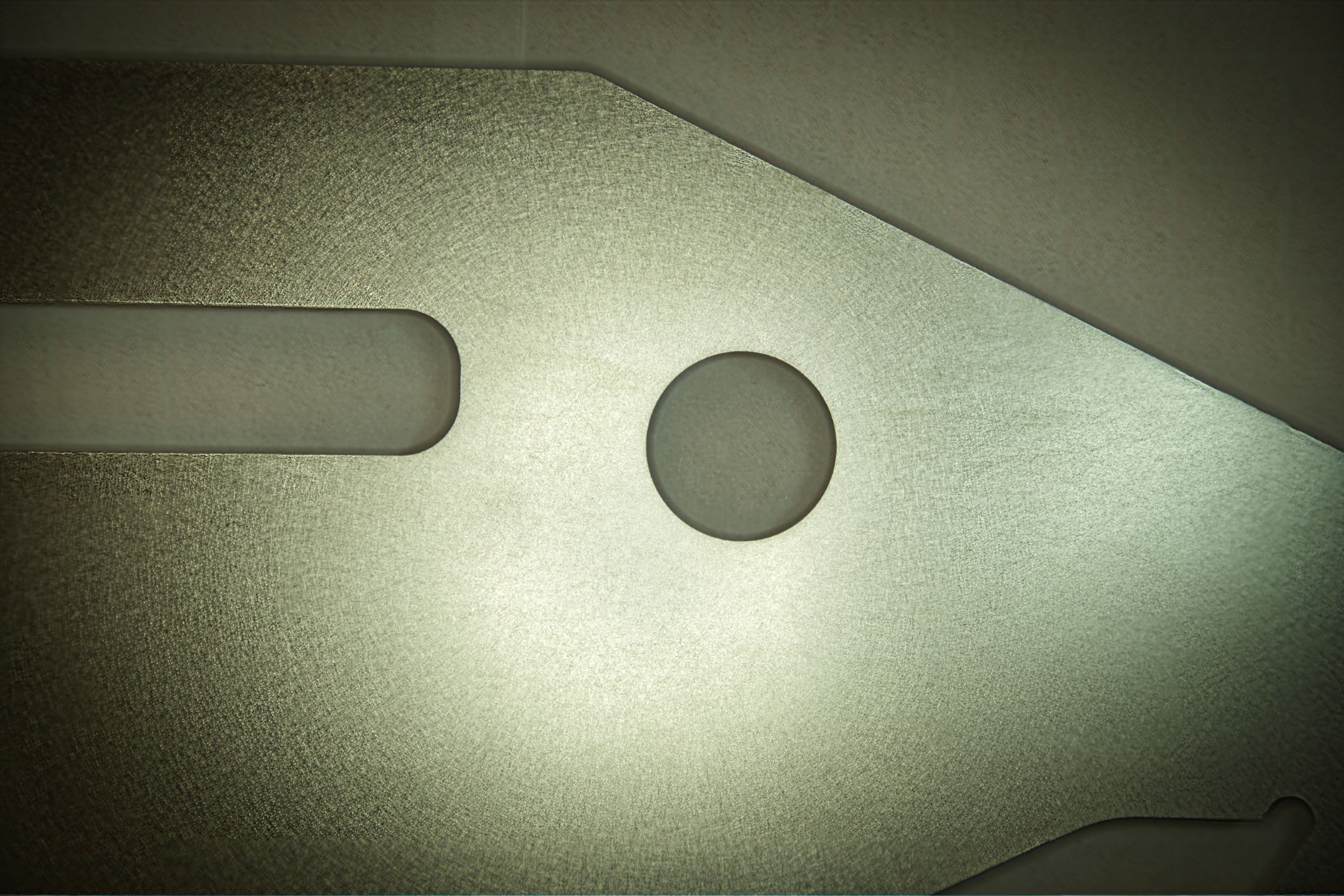
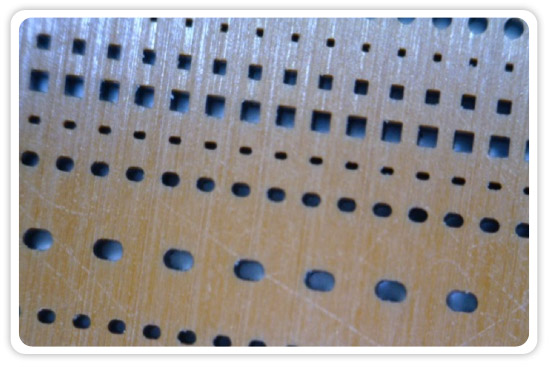
Chemical Methods:
- Acid Etching /Chemical Deburring: This process uses chemical solutions to dissolve burrs and smooth edges.
- Electropolishing: This is an electrochemical process that smooths a metal surface by removing material.
The methods used to deburr and create the premium edge quality in a machined part takes great skill and often collaboration between manufacturing disciplines. There is no best method, but there is the right method for every project. The knowledge and technology employed by precision cutting methods is complimented by the same dedication post processing providers have. Their skills literally polish the final details to achieve a high-quality precision component.