What Are Common Measurement Techniques for Surface Roughness and Edge Quality?
Surface roughness and edge quality are measured and qualified by several methods that confirm all specified notations on the dimensional print are met. Finish and roughness are defined as roughness, waviness, and lay. A non-conformance will result with further review and work stoppage of any further quantities until a resolution is locked. To better understand the three main aspects of defining surface are:
- Surface Roughness: Surface roughness is away to quantify the total amount of high and low irregularities on the metal surface. When a lower number is counted these results with a better surface finish, meaning there were less irregularities found.
- Waviness: Waviness is caused by deflection or vibration and is a larger irregular deviation. Measurements of the space between irregularities are impacted negatively by waviness.
- Lay: The orientation of surface textures is what lay indicates.
Although there are numerous industries manufacturing precision parts, the surface finish in machining is just as important as the overall geometry. Factors such as material selection for precision parts is important when considering the best materials for fine-precision machining. For determining the exact surface outcome of any manufactured component, it is not a battle of roughness vs smoothness in cutting. It is a quantified measurement that is guided by the specifications of the designed entity. By measuring surface roughness, the determination is made and certifies each custom manufactured component meets the required surface qualities. The following table are some of the most common measurement methods:
Measurement Method | Process/Technology | Characteristics |
---|---|---|
Contact Measurement | Using probe or stylus that is moved up and down the surface. The deviations are recorded. | Running stylus on fragile materials is more challenging. |
Contactless Measurement | Light-based tools such as lasers and X-ray systems to measure surface roughness and are non-contact. | Ultrasonic impulses are directed to the material surface. |
In-Process Surface Measurement Assessment | Control and monitoring techniques allow assessment of surface finish parameters at intervals during machining process. | Gives real time data and does not disrupt the majority of manufacturing time. |
Comparative Measurement | Comparative/measurement- a product’s surface is compared to a standard roughness. | Manufacturers can compare the appearance of their product’s surface both by sight and by touch. Good for batch evaluation. |
Inductance Measurement | Uses electromagnetic energy to determine the inductance distance of the pickup from the surface. | Measures the roughness of magnetics surfaces. |
The Vocabulary of Surface Roughness
Surface roughness can be better understood by key parameters, that have been developed for the methodology of such an important factors that engineers and manufacturers rely on. It is no wonder that surface finish in machining is just as important to having the correct material used and machined features held to a specific tolerance. These key parameters are:
- Ra: Roughness Average, this factors the average height of surface peaks and valleys of the analyzed area. It can be referred to as the Center Line Average (CLA)
- Rz: Meaning, Average Roughness Depth, this calculates the mean of five largest and five smallest peaks or troughs. Indication of roughness is made by this method and is considered a good indication.
- Rp: Peak Height, the highest peak value to the average line over the measured area.
- Rv: Valley Depth, indicates the lowest point of the surface profile about the mean line within the measured area.
- Rmax: Maximum Profile Height. The Rmax parameter determines the greatest vertical difference within the measured area by measuring the highest peak above and the lowest valley below the centerline values.
-1.png)
Source of Graph: Premium Parts.com
.png)
Source of Graph: Premium Parts.com
Edge Quality
Edge quality is determined by the smoothness and precision of the cut or machined edge and can dramatically influence the function and reliability and overall performance of the part. Having the correct edge quality can optimize the device in which the component is placed. A non-conforming edge quality, if not addressed, can potentially damage the system that the key components are designed for. Factors affecting edge quality are material properties, the technology used to manufacture precision components and post processing methods. Cutting processes, such as laser cutting, CNC routing, and waterjet cutting, offer different levels of precision and edge finish. Although some of the same methods used to measure surf ace roughness can be used to measure edge quality, there are some additional methods used for this such as:
- OGP: Optical Gaging Products can measure geometry but also use magnification to review the cut edge and measure irregularities.
- Optical Laser Scanning: This method can provide precise measurement and is a contactless method.
- Optical Profilometers: Produce 3D measurements of the desired area and can be as accurate as 1um.
Material Matters
It is important to mention the role in choosing the right material for your project. This ultimately is a choice between the manufacturer and what best method is there for achieving the geometry and the edge and surface roughness qualities required for the precision component. Examples include CNC Milling of a stainless-steel block. This is a common machined material, but care must be taken to reduce the chips and heat-affected zones (HAZ). You would not want to cut stainless steel with a thickness of 0.254mm or less on a CNC, as too much force would damage the sheet. Conversely, ultraviolet laser technology is versatile because it can cut a wide array of materials, including stainless steel, but only at ultra-thin foils or sheets. Surface roughness can be affected by HAZ as these lasers concentrate energy and do cut slower. Molten metal or slag can form on the cut edge and surface. Ultimately, there is no best material for fine-detail machining, but there is the right choice for each custom project.
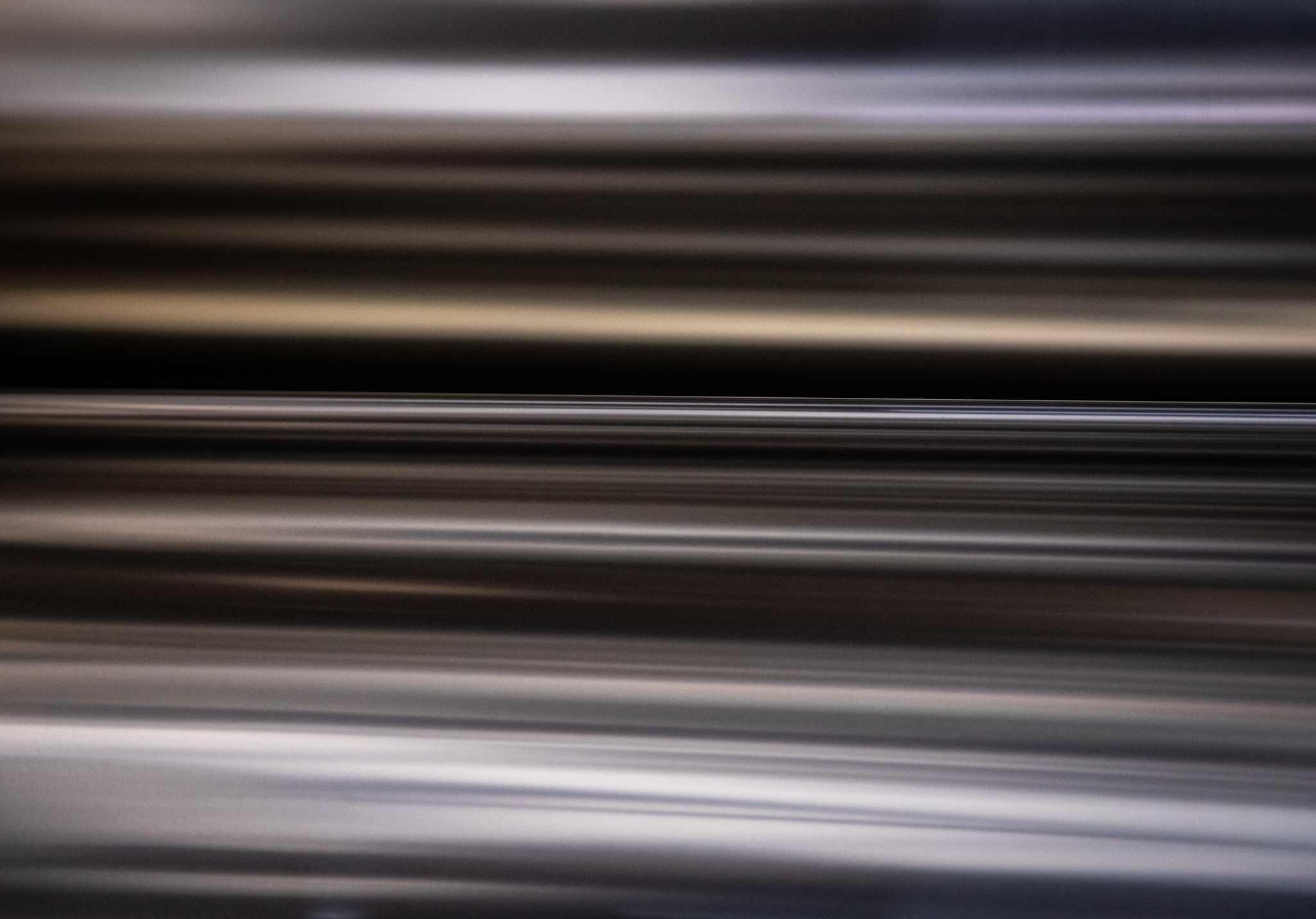
In conclusion, the common measurement techniques for surface roughness measure to the parameters of Ra, Rz, Rp, Rv, and Rmax, as these are essential for determining whether a surface meets specified requirements. These parameters provide a comprehensive insight into the texture and quality of the surface, ensuring that it adheres to the necessary standards for performance and functionality in various applications. Edge quality is also important in terms of the function and performance of the designed component. Using industry measurement devices accurate data gives service providers a clear picture of the completed manufacturing process to the design restrictions. Accurate measurement of surface roughness and edge quality is crucial in manufacturing and engineering, as it directly impacts the efficiency, durability, and aesthetic appeal of the final product. Hence, mastering these techniques is fundamental for achieving optimal surface finish and maintaining the integrity of machined components.