What Are Common Challenges in Achieving and Maintaining Ultra-Precise Tolerances?
Challenges in Ultra-Precision Engineering
Achieving ultra-tight tolerances isn’t just about having the right equipment—it requires precise control over multiple factors throughout the precision manufacturing process. Even the smallest variation in material properties, tooling, or environmental conditions can impact the final accuracy of a component.
Challenge | Impact | Solution |
---|---|---|
Thermal Expansion | Material expands/contracts with temperature changes | Climate-controlled machining environments |
Tool Wear | Worn tools reduce precision over time | Frequent tool maintenance & replacements |
Material Stress & Warping | Internal stresses cause dimensional changes | Pre-machining stress relief processes |
Machine Accuracy | Vibrations and misalignment cause deviations | Use of high-precision CNC and EDM machines |
Best Practices for Long-Term Tolerance Stability
To maintain ultra-precise tolerances across production runs, manufacturers must optimize every aspect of the machining process:
- Use the Right Material – Selecting low-expansion alloys such as Invar or titanium helps maintain precision by reducing thermal distortion.
- Monitor Environmental Conditions – Even a 1-2°F temperature change can cause material shifts. Climate control and thermal compensation strategies help counteract this.
- Implement In-Process Metrology – Using coordinate measuring machines (CMMs), laser scanners, and real-time monitoring systems ensures continuous accuracy adjustments during machining.
- Utilize Non-Contact Machining – EDM (Electrical Discharge Machining) and laser cutting eliminate mechanical stress, providing finer detail and more stable tolerances.
- Optimize Fixturing and Workholding – High-precision vises, vacuum holding systems, and zero-point clamping reduce part movement and improve repeatability.
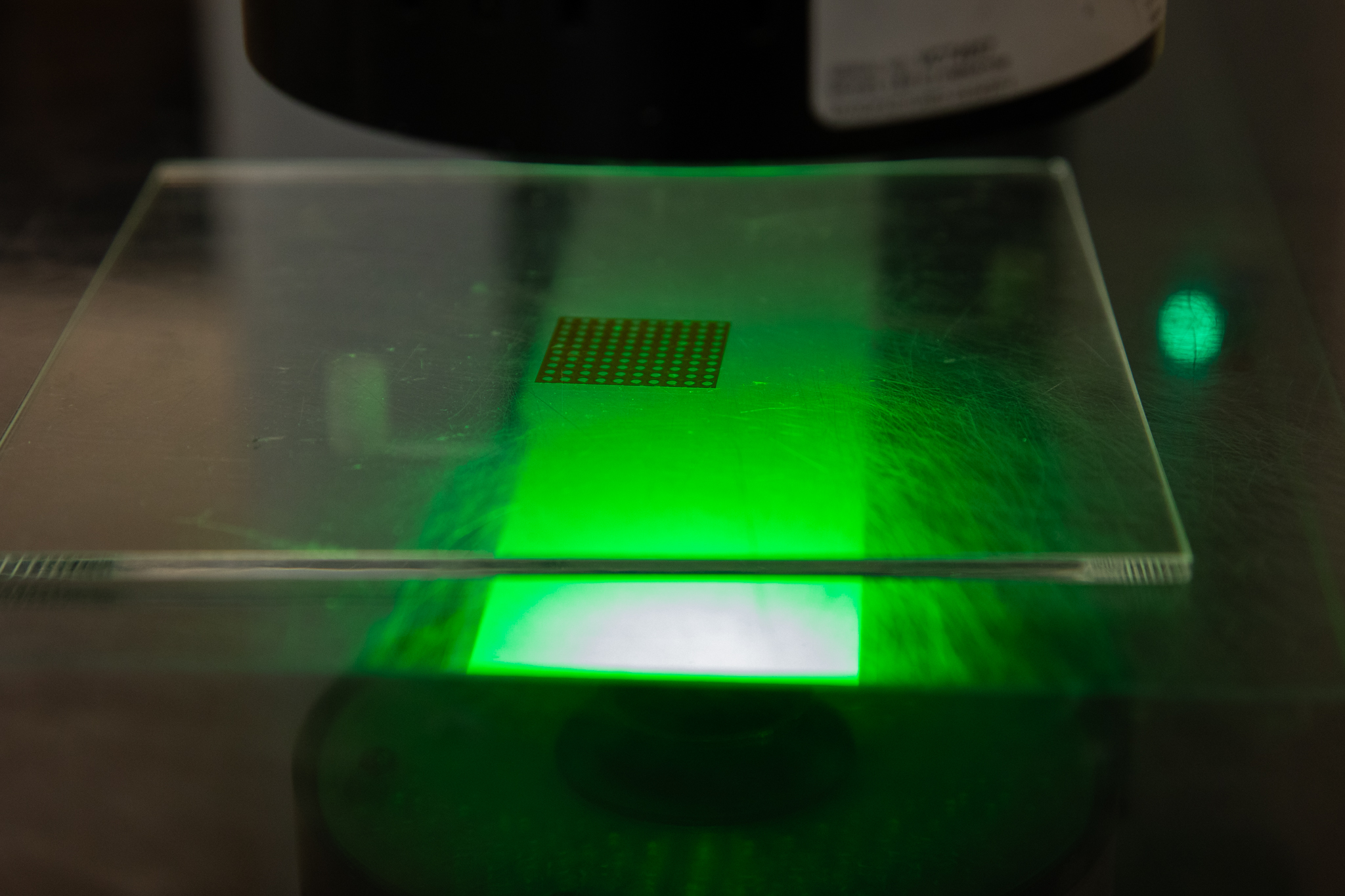
For industries requiring high-accuracy cutting and tight tolerance machining, A-Laser delivers cutting-edge solutions that push the limits of precision, ensuring the highest level of consistency and quality in every part.
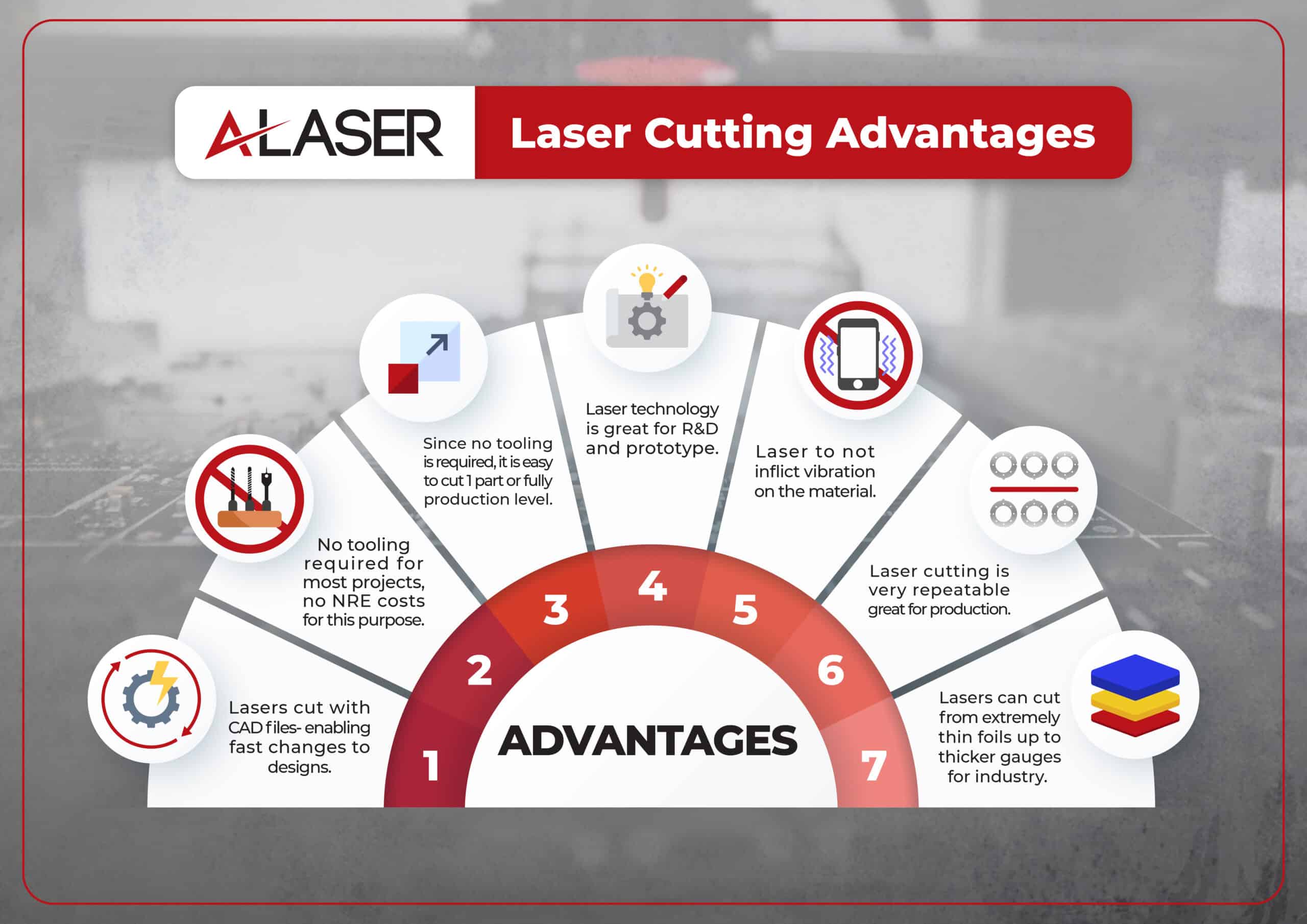