Polyimide Cutting
Polyimide Cutting
Is polyimide the same as Kapton?
It’s not an apples-to-apples comparison of Kapton brand material and polyimide. They are very close and could be cousins in the family of polyimides but there are some differences to be made aware of before any project requiring Kapton sheet or polyimide cutting is done. First let’s review what polyimides are. Technically, Polyimides (PI) are high-performance polymers of imide monomers. They contain two acyl groups (C=O) bonded to nitrogen (N). They have characteristics such as chemical resistance, dielectric properties, mechanical durability, and high thermal threshold of (>500°C). There are more subcategories, but this is the basis of what a Kapton sheet or polyimide film would be made of. How they differentiate from each other is in their production and final chemical makeup.
Kapton brand material is a registered product of Dupont corporation. It was developed back in the 1960’s. As it has its own specific chemical formula. Kapton is trusted for the quality of its product and holding true the characteristics of durability, temperature range, and dielectric properties. Kapton sheets are manufactured in multiple variants and with and without adhesives. Polyimide film is used in many ways but is less costly than Kapton.
Polymerization is the manufacturing process used to make polyimide or Kapton film. Molecules called monomers are linked through a chemical process to create larger molecules called polymers. Polyamic acids initially create long formed chains that are subjected to heat and result in a cross linking of the chains to produce a polyimide film or sheet. Polyimides have the same characteristics as Kapton. But vary slightly by the manufacturer.
The main difference of Kapton cutting of film or sheets over polyimide film is the formula used. Dupont has a trademark consistent process for the manufacturing of Kapton and its variants with adhesive or some other added alloy. Polyimides are the generic form of this wonderful material that is very easily machined through laser cutting technology or die cutting technology. For decades polyimide cutting has been used in electronics, battery technology, aerospace, cryogenics, and any application requiring electrical insulation understand the value of using Kapton or polyimide films and sheets as a durable and well recognized solution. It is recommended to speak with your preferred service provider to understand the minor differences in Kapton cutting and polyimide cutting. Ask them for the MSDS or Material Safety Data Sheets. These documents will review all the chemical properties and review any hazards to use and manufacturing of.
What Is the Best Laser Cutter for polyimide?
We often ask what is the best for this and for that? It seems very apparent especially now with online media that the question of “what is the best restaurant, vacation destination, car, airline etc.? We can’t get away from it and many times what is deemed the best is replaced soon by something else, something trendier perhaps. It’s all fun and good to see others’ opinions. For technology and manufacturing this too holds true, especially if you have ever attended a trade show. Everyone is excited to showcase their technology as the best. Can it all be true? That really depends on the technology and the type of projects that best fit within each manufacturer’s capabilities. When presented with a project using Kapton or polyimide laser cutting technology can have an advantage over methods. Systems like die cutting do very well in processing Kapton films or polyimide films, but this is not laser technology which can be the better fit depending on the project details. In brief, a Kapton sheet is manufactured by Dupont. Polyimides are the generic name for basically the same chemical makeup. Kapton is produced to standards that Dupont has. The chemical formula can vary per other manufactures producing a polyimide film or sheet. Together these characteristics of high thermal range, dielectrics properties, chemical resistance, and durability are found in each. Often the choice to use one over the other is a preference by the end user.
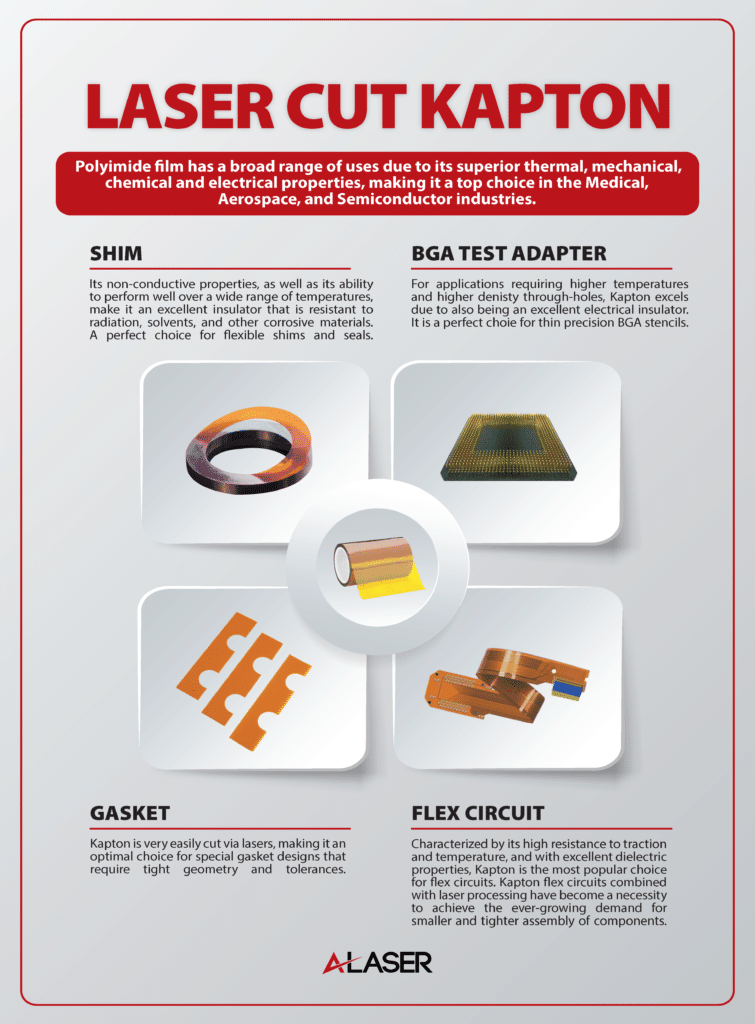
Regarding laser technology, there is the best laser system type to cut Kapton or polyimide and that is ultraviolet laser technology or sometimes referred to as UV lasers. UV lasers with a 355nm wavelength are recommended for Kapton cutting or polyimide cutting of sheets and films. Polyimides in general in sheet or film form absorb ultraviolet light energy. This results in heat conversion of the UV source and the cut path ablates the material away. With a very small beam diameter, UV lasers can produce very fine and intricate geometries. C02 lasers have the ability to process Kapton cutting or polyimide cutting but can result in charring and rough edges of the profile. Since Kapton sheets or polyimides are often manufactured into precision parts to support a critical industry, utilizing ultraviolet laser technology has become the system type of choice. Further information is available by reviewing the MSDS sheets, before any Kapton cutting or polyimide cutting is done. These Material Safety Data Sheets describe in detail the chemical make-up of each and will highlight any potential hazards to use and for the manufacturing of.
The best UV laser technology available is debatable and you will find many manufacturers promoting the capabilities along with the bells and whistles their laser systems have. In general, the base technology of 355nm wavelength will provide you with premium edge cut quality and good to very high throughput. Laser cutting Kapton films and or polyimide films or sheets has a long record of success, and many laser service providers will be happy to review and support your next project.
How do you laser cut and engrave polyimide?
Laser Cutting Kapton: Precision at its Finest
- Selecting the Right Laser Parameters: Achieving optimal results begins with setting the right laser parameters. Fine-tune power, speed, and frequency settings to ensure precise Kapton cutting without compromising material integrity.
- Material Preparation: Ensure a clean, flat surface for the Kapton sheet. Secure it firmly onto the laser bed to prevent any movement during the cutting process.
- Vector Cutting vs. Raster Engraving: Determine whether your project requires vector cutting for precise shapes or raster engraving for intricate designs. Adjust laser settings accordingly for optimal results.
- Minimizing Thermal Impact: Kapton’s thermal sensitivity demands careful attention. Optimize laser settings to minimize heat transfer, preventing warping or distortion of the material.
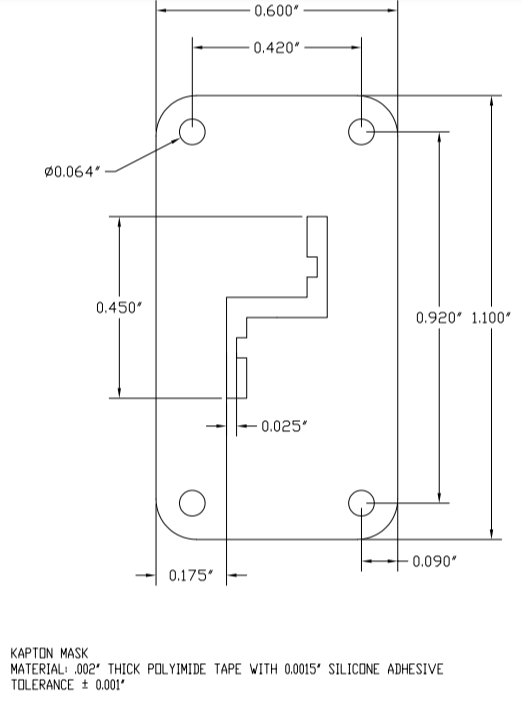
Polyimide Cutting: Unveiling Perfection
- Precision Calibration: Calibrate your laser system meticulously to accommodate the unique properties of polyimide. Fine-tune focal length and beam alignment for pinpoint accuracy.
- Masking Techniques: Employ masking techniques to protect critical areas from laser exposure during cutting and engraving processes. This ensures clean edges and precise results.
- Ventilation and Extraction: Adequate ventilation is crucial when working with polyimide materials. Implement efficient extraction systems to remove fumes and prevent any potential hazards.
- Quality Assurance: Regularly inspect cut edges and engraved surfaces to maintain quality standards. Adjust laser parameters as needed to achieve desired results consistently.
Mastering the art of laser cutting and engraving polyimide (Kapton) opens a world of possibilities for your projects.
What Are the Alternatives to Polyimide Film / Kapton for Laser Cutting?
Exploring Kapton Cutting Alternatives
- Mylar Film: Mylar, a polyester film, shares similarities with Kapton in terms of flexibility and durability. Explore its suitability for laser cutting projects where high tensile strength and chemical resistance are essential.
- PETG Sheets: Polyethylene terephthalate glycol (PETG) sheets offer excellent transparency and impact resistance, making them ideal candidates for laser cutting applications requiring optical clarity and structural integrity.
- Polycarbonate (PC): Known for its exceptional toughness and heat resistance, polycarbonate sheets provide a robust alternative to Kapton for laser cutting projects in demanding environments.
- PTFE (Teflon) Film: PTFE films exhibit superior non-stick properties and thermal stability, making them suitable for laser cutting applications where low friction and high temperatures are prevalent.
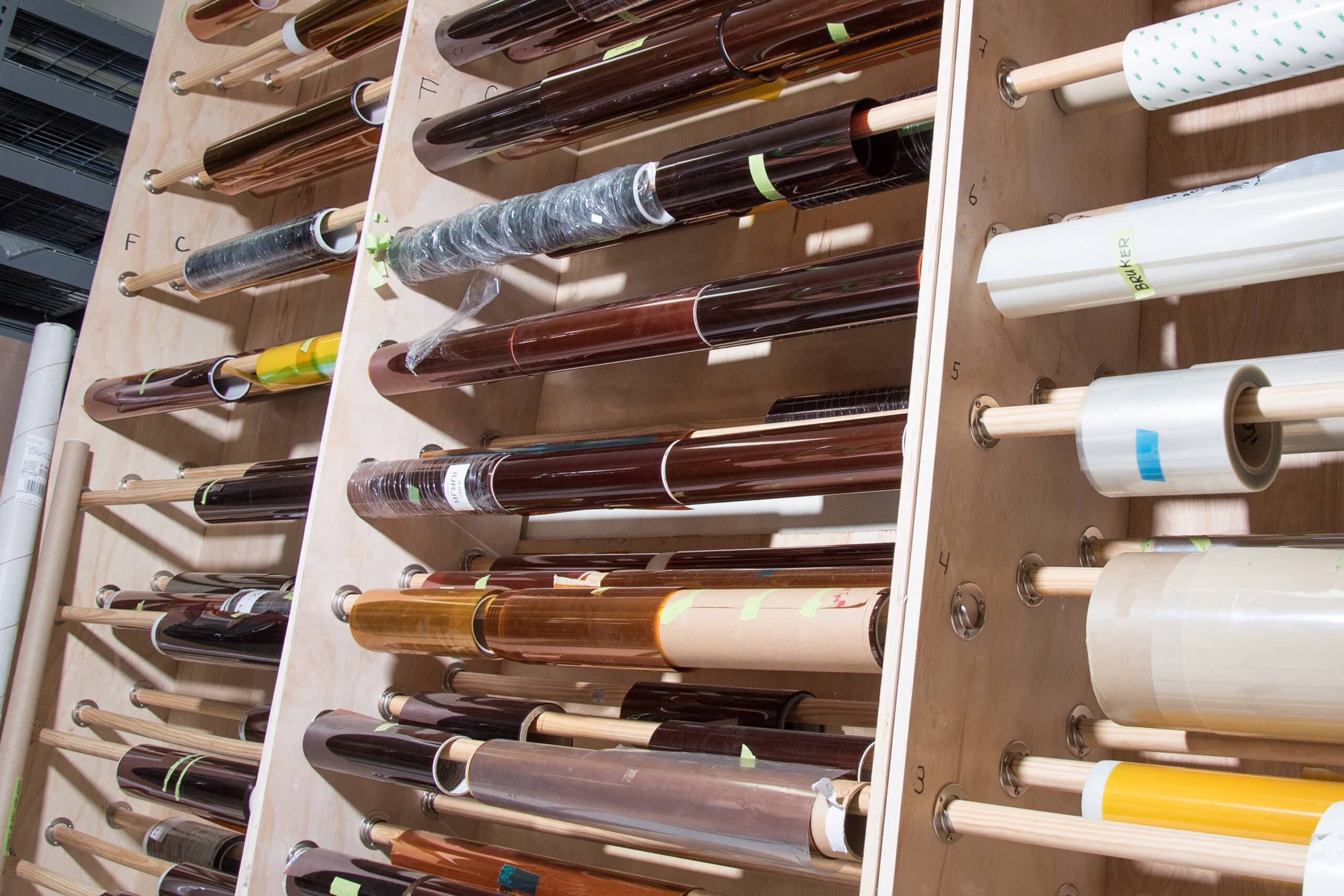
Selecting the Right Alternative
- Material Properties Comparison: Evaluate the properties of each alternative material against your project requirements, considering factors such as thermal stability, chemical resistance, and mechanical strength. Will the polyimide have an adhesive layer that will be kiss cut too?
- Laser Compatibility: Ensure compatibility with your laser cutting system by testing each material’s response to laser energy, adjusting settings as necessary to achieve optimal results.
- Application-Specific Considerations: Tailor your material selection to suit the unique demands of your application, whether it involves aerospace components, electronic substrates, or industrial gaskets.
Exploring alternatives to Kapton sheets opens doors to innovative solutions for your laser cutting projects. By considering the properties and performance of alternative materials, you can make informed decisions that align with your project goals and requirements.
Discover the possibilities with A-Laser’s expertise in polyimide cutting and materials science. Contact us today to explore customized solutions tailored to your specific needs.