Precision Perfected: Laser Manufacturing for Tomorrow’s Demands
Why Choose Laser Manufacturing?
Welcome and thank you for taking time to review the precision world of laser manufacturing. Lasers have always been synonymous with advanced technology, from the early portrayals in movies and comics to uses of today. Lasers used in manufacturing are “cutting edge” technology, being utilized in so many unique ways that other methodologies just cannot match. Though there are other very competent methods to produce flat, 2D geometries, laser cutting machines excel in this area, especially tuned to supporting the most challenging sectors of industries.
The Laser Advantage
Understanding that time is a valuable commodity to us all, let’s jump right in to review some of the characteristics that make laser cutting a prime solution:
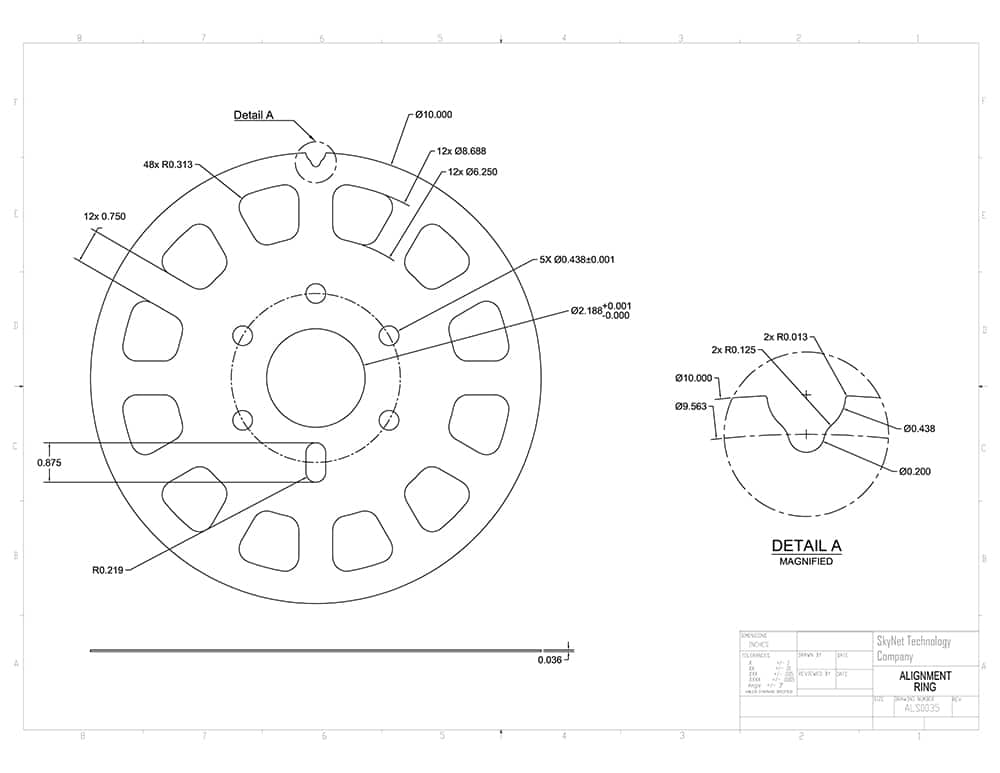
- Precision at the Micron Level: Consistently tight tolerances that traditional tools can’t match. Laser cutting for many projects holds a standard tolerance of +/- 0.0254mm.
- Non-Contact Process: Ideal for fragile, delicate, or ultra-thin materials. Cutting delicate gaskets and shims for the semiconductor industry or busbars for EV batteries, control of the process is paramount.
- Repeatability You Can Rely On: Every part meets exacting specs, every time. To be a supplier to industries requiring exceptional quality and accuracy. Components are made to be exact and interchangeable. This provides the ability to increase throughput demands.
- Design Freedom: Enables complex geometries and micro-features for innovation-driven sectors. Cutting with light is fascinating. The cutting beams are small and constant, providing tight radius and sharp corners with straight walls.
- Controlled and Scalable: Perfect for prototype, R&D and production environments. Laser manufacturing is often contacted to support R&D and prototype projects. With most projects not requiring fixtures or tooling, this saves cost for iterations. However, customers soon realize the accuracy and quality achieved is transferable to supporting supply chains.
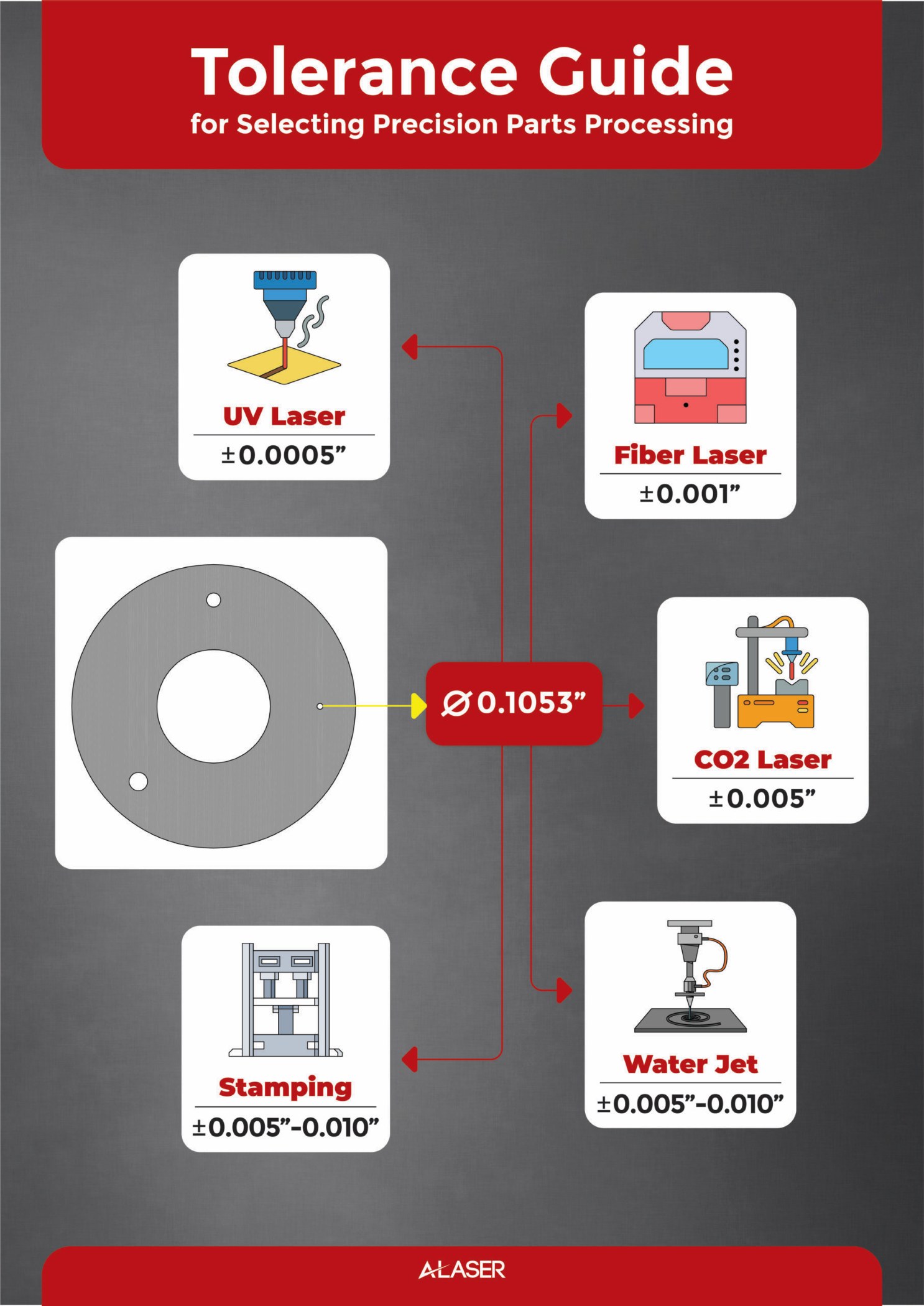
Built for the Demands of High-Performance Industries
Since most manufactured components are proprietary, specific examples of laser cut parts cannot be shared, but we can generalize the impact to industries that laser cutting provides, such as:
Electronics:
- Laser depaneling, drilling, and marking for PCBs and micro components.
- Solder mask removal for exposing copper pads, traces, vias.
- Benefits: No mechanical stress, burr-free edges, ESD-safe.
- Ideal for miniaturized, high-density board layouts. Complex board profiles.
Aerospace:
- Micro-cutting and etching of exotic alloys, thermal barrier materials.
- Benefits: High precision, reduced weight, exact airflow control.
- Used in turbine blades, sensors, shielding components.
Medical Technology:
- Manufacturing of stents, surgical tools, microfluidic channels.
- Benefits: Sterile process, no contamination, bio-compatible material support.
- Enables innovation in implantable and diagnostic devices.
EV Battery Technology:
- Manufacturing of busbars, tabs, thin film circuits.
- Benefits: Precision components with no slag or debris.
- Fosters rapid prototyping and supports high volume of custom parts.
Materials and Laser Technology
If there is going to be one key characteristic that differentiates laser cutting from other methods is the capability of manufacturing parts out of so many different types of materials. Different laser systems specialize in cutting different materials and thicknesses and by doing so, cover a wide range of cutting capabilities. Here is a breakdown of materials and laser technology:
- Ultraviolet Laser: General cutting ranges from 0.0127mm to 0.254mm.
- Metal Alloys: stainless steel, copper, brass, aluminum, titanium, nitinol, tungsten, nickel.
- Non-Metallics: Kapton/polyimide, PEEK, Mylar, Q-Psd, Berg K10, Berg K40, FR4, Nitrile Rubber, Silicon Rubber, Alumina ceramic.
- Fiber Laser: General cutting ranges from 0.254mm to 10mm thick.
- Metal Alloys: Titanium, tungsten, stainless steel, copper, nickel, carbon steel, aluminum.
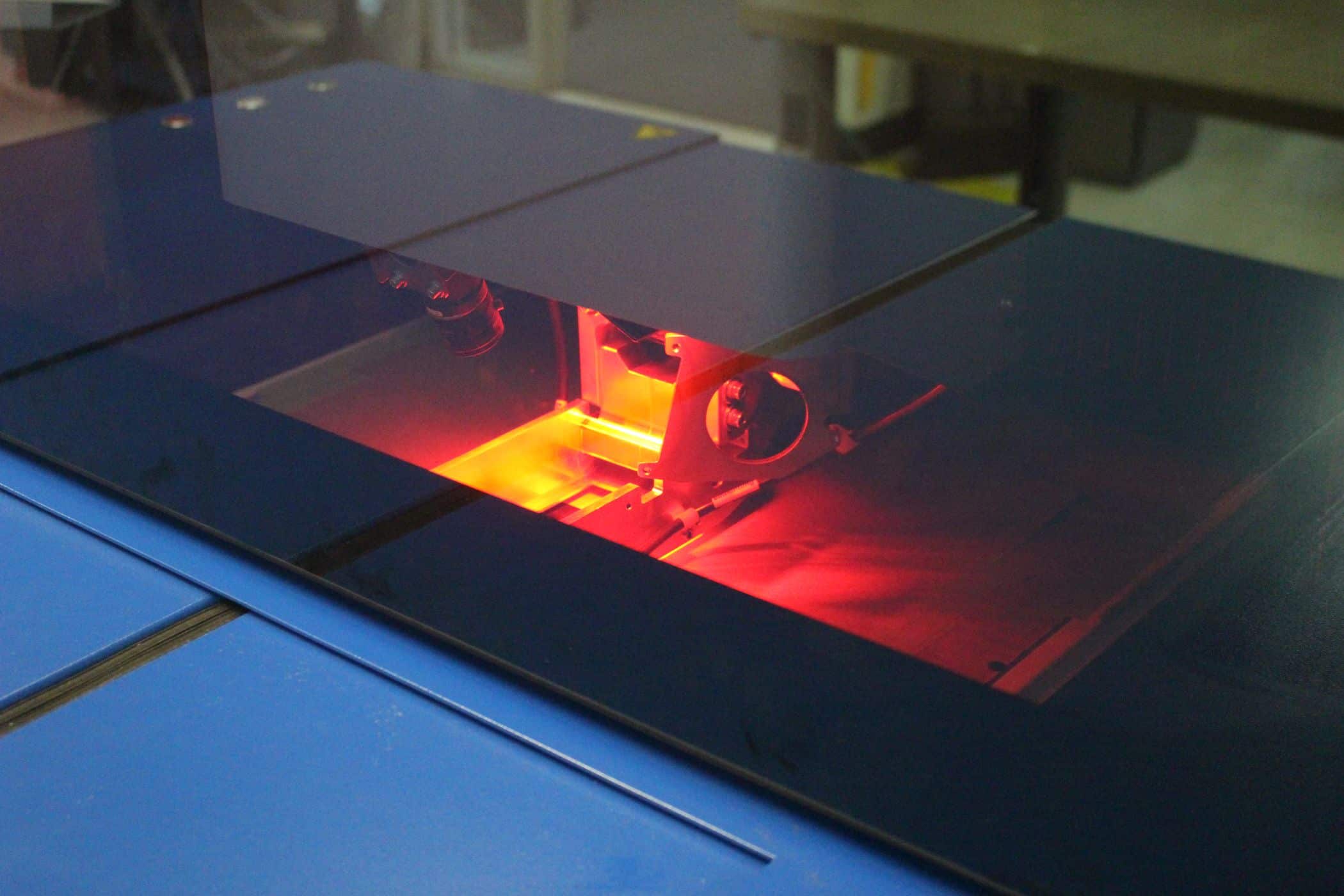
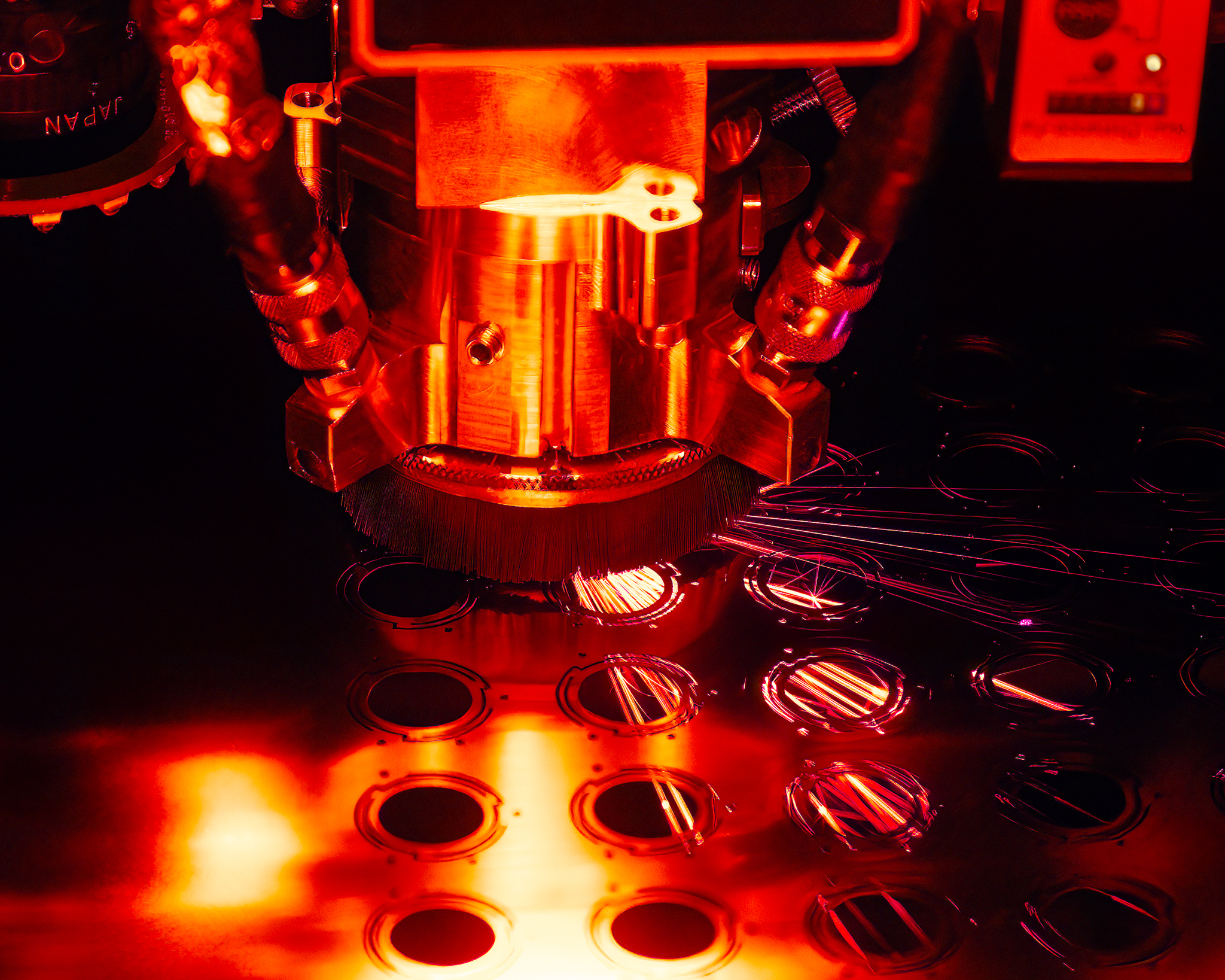
- CO2 Laser: General thickness of 0.254mm to 30mm.
- Plastics like Delrin, acrylic, ABS, polycarbonate.
- Wood, paper, cardboard, cork.
- Leather, leather, foam, polyester.
- Metals: Generally, not suitable for metals, but some high powered machines can.
- Femtosecond and Picosecond Lasers: Cold cutting, best for ultra-thin materials.
- Metal Alloys from 2-15 µm for stainless steel, 200-500 µm for titanium alloy, 1000 µm for tungsten carbide and others.
- Non-Metallics: sub .1mm to 3mm polymers and plastics.
Each project of course is specific and the adjustment to the best laser cutting technology will be used. For new laminates and combinations of materials, laser cutting provides development runs to create the “cutting tool” for material choice.
How Laser Technology Works
From receiving the design to delivery of new precision components, this focus of laser manufacturing is culture driven by the expertise of those professionals who provide the expertise to make parts being used in applications as mentioned earlier, but in so many others too. There is no big mystery to getting your next project moving forward and when ready this is the general process.
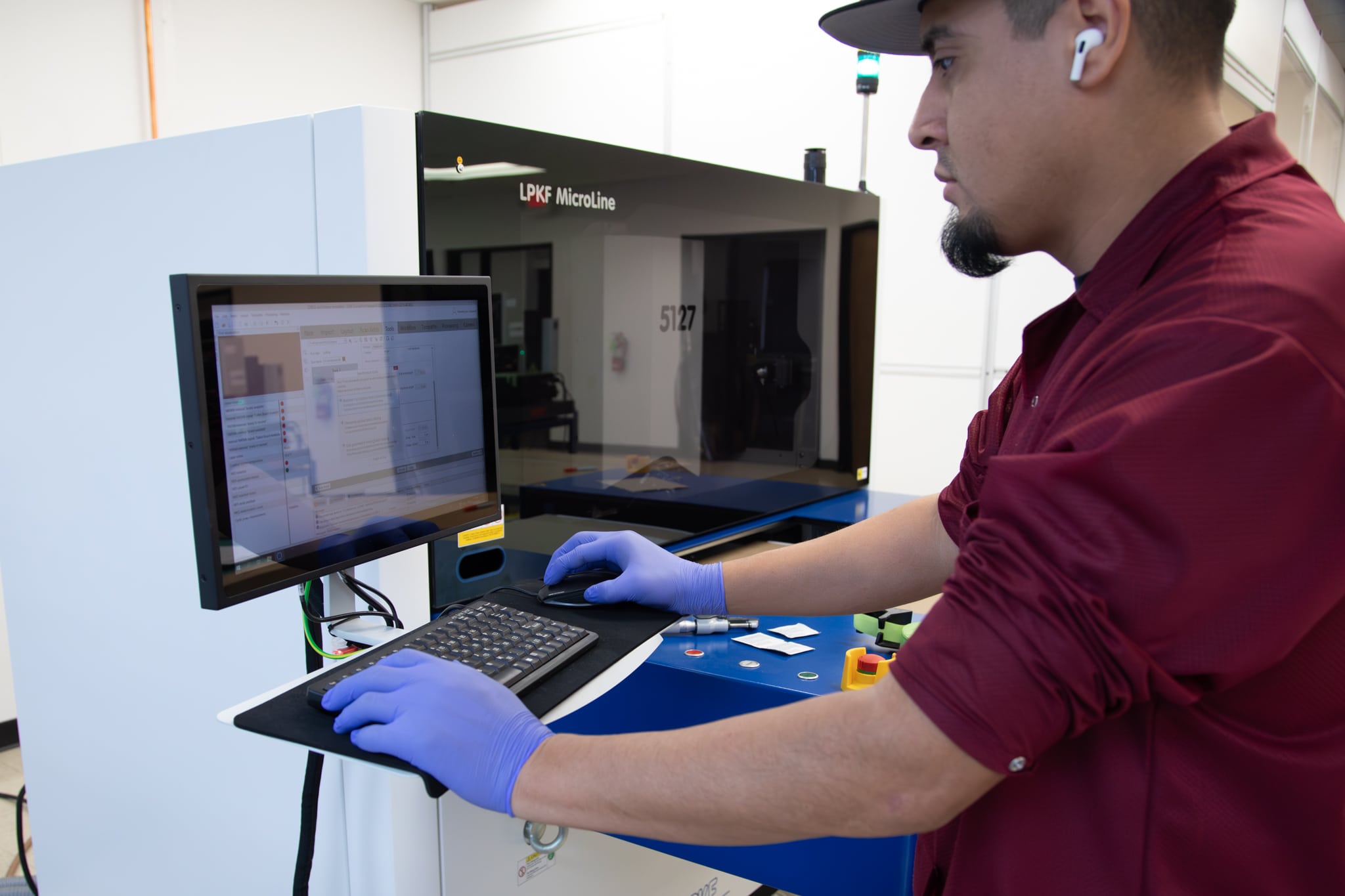
- CAD Data: Seamless data-to-part workflow using formats such as dxf, Gerber, AutoCAD Step.
- Quality Assurance: Tightly controlled process parameters verified by OGP measurement and other metrology.
- Flexibility In Manufacturing: Supports prototyping and full-scale production- One-time needs, production support, or exploratory runs can all be done on the same machines.
- Process Control: Laser service providers wishing to take on the challenges of high technology and government defense contracts will be registered under industry guidelines like ISO standards (International Organization for Standardization and certified by ITAR (International Treaty in Arms Regulations). ISO and ITAR work together by providing manufacturers with complementary guidelines—ISO focuses on quality management and process consistency, while ITAR enforces strict controls on defense-related data and part handling; together, they ensure precision, compliance, and security in manufacturing.
- Conquering the Materials Challenge: Capabilities in cutting metals, polymers, ceramics, and coated materials. This is a great benefit that laser manufacturing uses to advance many industries.
Conclusion
There are many characteristics of laser manufacturing that make it ideal for multiple industries, including aerospace, medical devices, and electronics. These industries and many others have discovered the benefits of using laser cutting methods that include precision systems like ultraviolet, fiber, CO2 and other technologies. The capabilities of material versatility for cutting metal alloys and quickly transition to cutting polymers or rubber-based materials. The standard precision of laser cutting machines excels with many other methods. Having the understanding of the needs for start-up companies to test and evaluate protypes and also be part of an OEMs supply chain, show the flexibility of the services laser cutting gives. If you have a question to ask or want to discuss your project, please contact us.