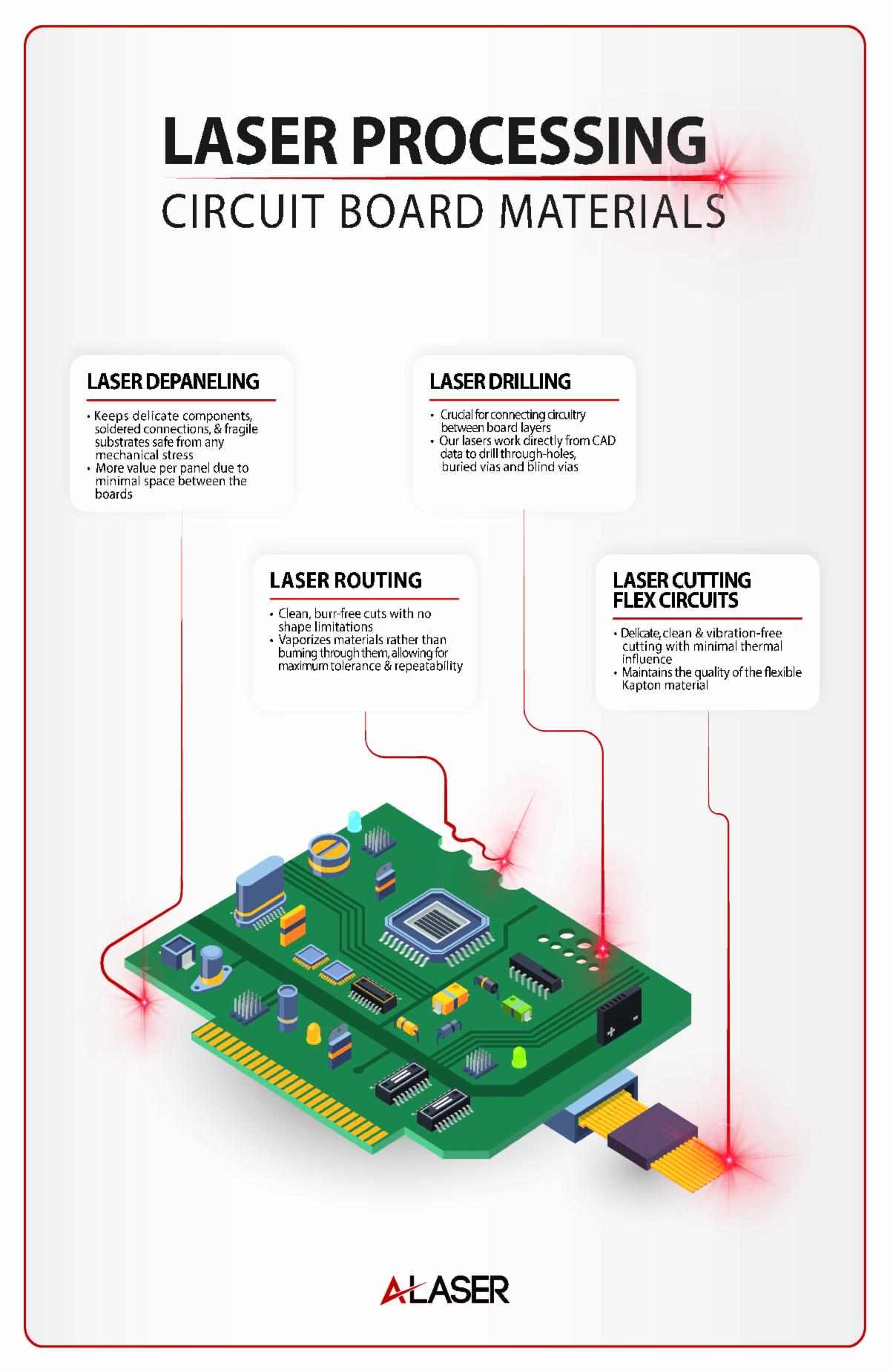
The Use of Light To Create Circuitry
Laser etching of a PCB is a process to produce the conductive traces by ablation and exposing the intended copper traces. Before going further we must state that the manufacturing process of producing a printed circuit board, is highly complicated involving many steps including chemical processing, plating, ink printing, screen printing and mechanical steps as well. The creation of the circuit paths that will carry the electrical signals to various components really is near the last of these multitude of steps. Laser etching creates these electrical traces, but its not the only method. Laser technology used in the etching of the PCB is a relative newcomer to industry and not only can provide a unique aspect in creation of the traces but can also be used in singulation of completed board panels. The removal of unwanted copper from the printed circuit board creates the circuit paths and more traditional methods were used for many years such as wet etching that includes acidic etching and alkaline etching. Other methods include dry etching or plasma etching and last, but not least, laser etching. The use of laser technology is being acquired not only by laser service providers, but by printed circuit board assembly companies to further their capabilities in a very demanding and competitive market.
The Technology of Laser Etching
Light energy is a wonderment and a wonderful thing and learning to harness light energy has been a quest for humankind for millennia. In today’s world, using lasers is very common unlike 40-50 years ago, when laser technology was still very much in it infancy. Today, laser technology is in communication, navigation, optics, surveying, medial application, space, aeronautics and defense, just to name a very few. In manufacturing of all sectors, laser technology has become mainstream for numerous tasks and systems. When used in the process of printed circuit board manufacturing, laser technology uses mostly a wavelength of ultraviolet light or UV laser technology. Lasers use ablation which is obliteration of the materials that the laser beam hits. UV systems have characteristics such as:
- Small Beam Diameters: Beams diameters can be smaller than 20umn microns, promoting higher accuracy.
- Controlled Power: Laser systems vary in the power they have. The higher the power, generally the greater the ability to cut through and process faster. All systems, however, can control power to incremental levels of wattage.
- High Precision and tolerance: Using CNC controls, lasers are highly accurate when etching to +/- 0.0254mm to 0.0508mm.
How is laser etching different from the other methods?
If you can imagine walking through a laser services manufacturing floor, you will notice first the relatively quietness of these machines. Though mechanical, many newer systems are enclosed and the only way you can tell of their being in operation is seeing the laser beam moving. There are no tools and no smell of coolant or chemistry. For printed circuit board manufacturers, first you will notice the environment being dramatically different, with each process needing to be secluded from each other due to noise, smell and potentially caustic chemicals. These environmental differences can be dramatic but also the etching processing between laser etching and non-laser methods. In essence, etching is a removal process and in the case of printed circuit boards, the process is to remove copper and tin that results in circuitry that runs and controls electronics from consumer goods to medical implants, communications, autonomous vehicles, missile guidance systems, flow controls and so on. A laser etched PCB, as mentioned, is just one method of removing copper from the PCB substrate to create the desired circuitry paths. For each new PCB, there will be a method used that is best. The differences between each are demonstrated on the following table:
PCB Etching Methods | Etching Process | Used For |
---|---|---|
Acidic | Wet etching: using typically Hydrochloric acid (HCl) and hydrogen peroxide (H2O2), | PCBs with smaller feature sizes, as it allows for better etching resolution and finer line widths. |
Alkaline | Wet etching process: using typically sodium hydroxide (NaOH) and potassium permanganate (KMnO4) | PCBs with relatively simple and larger feature sizes. Results in uniformity of the circuitry. |
Plasma | Dry Etch: In plasma etching, reactive gases of oxygen (O2) or chlorine (Cl2) are introduced into the chamber, and the plasma generated breaks down the copper molecules. | high-density PCBs with smaller feature sizes. Control over etching profiles. Good for fine-line circuitry and microelectronics applications. |
Laser | Sometimes referred to as LDI or laser direct imaging. Vaporizes the copper material using ultraviolet wavelength. | PCBs for microelectronics, high density boards and where precision is needed. |
The industry of printed circuit board manufacturing and assembly is fast paced with an ongoing pursuit of new production runs keeping all the parties involved with new deadlines replacing the most recently completed. It is a cooperative endeavor between multiple vendors supporting the process with raw materials, chemistry, tooling machines, etching services and others. Together, they create the base to which the electronic components are assembled onto.
What’s the Difference?
As a laser service provider, we specialize in technology from laser etching to laser depaneling to laser cut precision components, and additional services. Our experience in working with contract PCB assemblers and printed circuit board manufacturers has given us a good perspective on the industry and how best we can adjust to support. Why laser technology is chosen over other methods is project specific but often includes the precision and accuracy of the laser. The cleaner environment in the process and the reduced risk of damage with little to no vibrations on the board. The following video highlights one process, but all are done in similar fashion.
Conclusion
Electronics are an integral part of our lives for elevating our quality of life with better healthcare diagnostics and treatments, to devices that monitor our food and water supply and of course to consumer goods. Unless you’re living “off the grid”, it’s hard to imagine being separated from some kind of electronic device. To support this demand and need for better products, the printed circuit industry is vast incorporating a series of suppliers and vendors to process their part of the assembly and production lines. Laser technology, through laser etching and other services, play a key part when other methods cannot provide the desired accuracy and geometric profile. Laser etching has become a tool that manufacturers can count on for the designs of today that are challenging and complex, but we rely on so heavily for.