Laser Cutting vs Punching
Cutting Process
1. Deadmove – laser head moves to a soon to be scrapped area of the work material.
2. Plunge – the laser activates and begins to cut through the workpiece.
3. Path cutting – here the geometry of the part is followed by the motion control system. During this process, a “cutter comp” is applied to correct for the beam width (kerf) allowing or more precise dimensions.
4. Exit – the laser returns to the dead zone to avoid further heat affecting the vital edges.
5. Release – once the full geometry is complete the part is liberated from the surrounding material.
6. Laser switches off – begin the cycle again in the next instance.
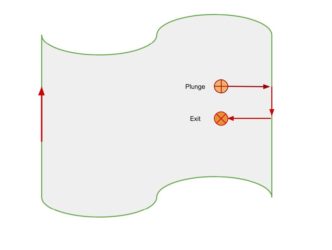
Punching Process
1. Impact – the initial stage where contact is made between the punch and material. On impact, the punch is subject to a level of shock which can cause internal damage and wear.
2. Penetration– this is where the material contacted begins to deform and pull away from the surrounding material and the shear begins.
3. Break – here the shear makes its way through the workpiece.
4. Snap through– the liberation of the punched section from the workpiece.
5. Bottom– punch tool extending beyond the workpiece to ensure the pressed area is released.
6. Withdrawal
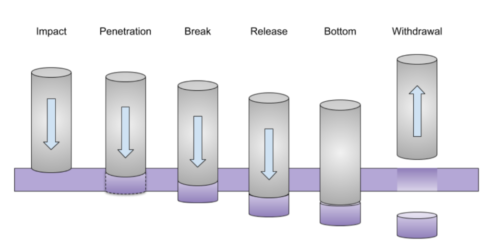
Laser Cutting | Punching | |
---|---|---|
Machine setup time | Minimal - for most instances laser systems are setup to accept sheets of material mounted to frames. The parameters affecting the output of the laser can be manipulated easily and quickly. | Medium - punching operations involve loading one or more punch presses to a machine, aligning and securing. |
Batch processing | Laser batch processing involves a linear scale. The time taken to manufacture 10,000 parts will generally be 10 times longer than 1000 parts. | Punch press systems are designed for batch processes. When increasing the number of parts produced the time for each batch remains roughly similar independent of batch size. Meaning 100 batches of 10 parts are somewhat comparable to 100 batches of 100 parts. |
Edge quality | Excellent - Somewhat dependant on the material and laser settings but generally the edge remains | Punching edge quality can often create a level of drag |
Tool wear | Non existent* | Proportional to the design, load and material strength used. Often hardened steel or tungsten-carbide is used. |
Tool cost (monetary) | Zero | The creation of punch tools can be extremely expensive as the manufacture of high strength tools is reliant on supporting specialized machinery. This causes an issue where custom punch presses can only exist in areas with supporting businesses. |
Tool cost (time) | Zero (unless rare specific needs are found to be essential) | High - depending on other companies/department producing the tool and die. |
Surrounding area | Heat affected zone - this varies between differing materials. The most important factor to consider is the materials light absorption rates at specific frequencies. | Impact affected zone - the area immediately surrounding the punched area will often be deformed during pressing. For soft materials, the top surface can experience a type of drag that deforms the material. This is especially detrimental to fine pitch components. With harder materials, such as stainless steel, the internal grain structure can be altered unintentionally but the press. |
Complex geometry | Laser systems adapt very well to complex shapes. This is due to the extremely low/non-existent downward acting on the workpiece. Small apertures with ‘arms’ or ‘peninsulas’ can be cut with relative ease. | Punch presses often struggle when complex geometries are required. For example, a bespoke part which includes a ‘peninsula’ would require a Boolean subtraction below the work piece as support. |
Iterative design | One of the key advantages of Laser systems is the ability to iterate designs within a batch without the need for retooling. | Each design iteration would require a new punch tool to be manufactured. |
Nested apertures | Like a Russian doll, laser cutting systems can easily cut internal shapes to a part before cutting the outline. This eliminates an entire process when compared to traditional manufacturing. | Only possible with complex presses or dual processes. |
Cost-Effectiveness
Above certain batch sizes, sheet metal punching becomes much more economical. Getting to this stage requires certainty over design choice and material type. One of the benefits of laser cutting allows for an immediate change of design with minimal extra cost.
*The quantities given in the graph are only for illustration.
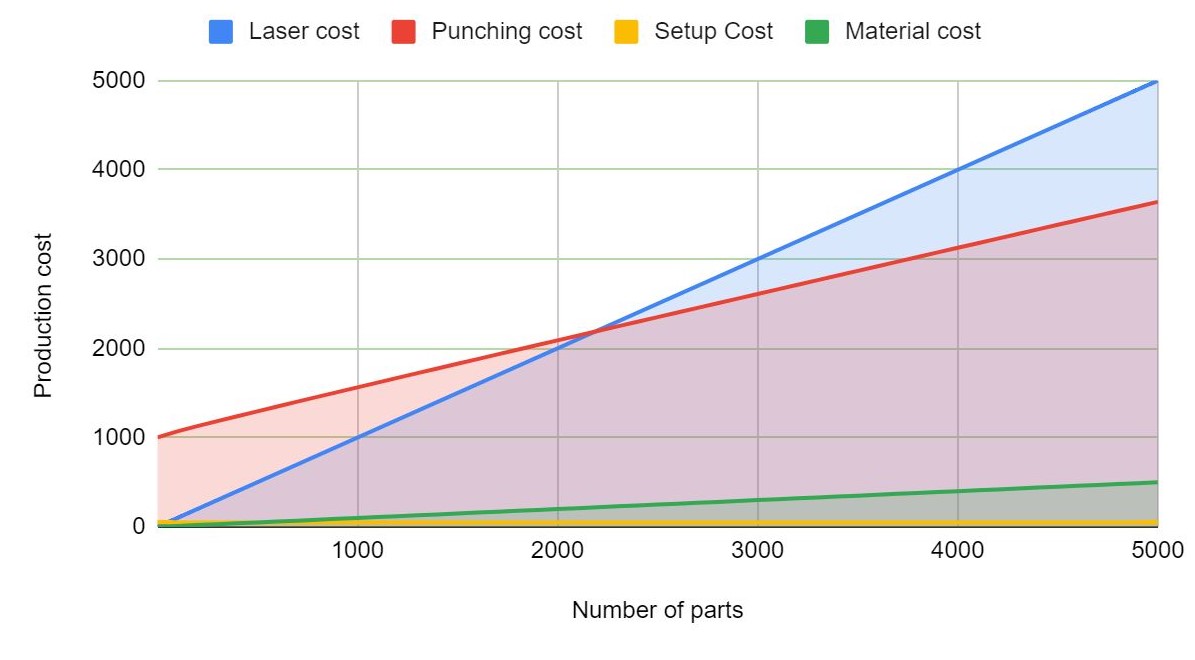
Tolerance
As a general rule, the smallest diameter of the hole that can be punched in a sheet of metal is equal to the thickness of that sheet. With laser cutting operations we can reach tighter apertures which can often be less than half of the sheet thickness. With fine-pitch components, for example, an array of 50μm holes punching would require a sheet 50μm thick whilst on a laser this can be formed from 100μm thick material. This results in a much stronger part.
Minimum Aperture Size
This is largely dependent on material thickness and strength. In theory, Punches could be made to extremely small diameters but there would be a massive trade-off in strength and accuracy (subject to vibration).
Which is Right for You?
For most use cases the main factor affecting production choice is batch size. Laser cutting is ideal for prototyping and smaller batch size. Second to that complex aperture lean towards laser cutting as an optimal solution for reduction in failed parts. Get in touch with our exceptional team of engineers to discuss the best option for your next project!