Laser Cut Kapton
Laser Cut Kapton Polyimide from A-Laser
If you’ve dealt with product design, especially products that involve electronic and electrical circuits, then you have probably dealt with Kapton. Kapton polyimide cover layers are prized for their strength and durability. Cutting through these cover layers requires a high level of precision, which is why we at A-Laser rely on LPKF’s UV laser systems.
What is Kapton?
DuPont’s Kapton polyimide (PI) films are amber-colored films known for durability and dependability. They are frequently used for their:
- Durability
- Chemical resistance
- Resistance to extreme temperatures
DuPont’s Kapton is the most widely known PI film, but there are many other brands, such as Envex, Kerimid, Pyrolin, Skybond, and Vespel.
Why is Kapton widely used?
This synthetic polymer is extremely versatile due to its remarkable physical properties. The thermal stability of Kapton allows for using it in various environments from electronic Flex Circuit Boards to insulation on space crafts and even medical devices.
How is Kapton Cover Layer Cutting Different?
The characteristics that make PI films so useful (durability, plus chemical and heat resistance) make them challenging to work with. They’re resistant to many traditional methods of cover layer cutting.
PI films are chemical-resistant, so only harsh, flammable chemicals can loosen the coating. It’s a dangerous, imprecise process. And techniques like soldering irons can be just as problematic. Additionally, mechanical cutting methods may damage components and leave debris.
This material usually comes in rolls of thin film in its stock form, you will need some sort of fabrication process to cut it to your desired design.
While die cutting and mechanical CNC routing may work for crude projects, nothing will beat the precision and cleanliness of laser cut Kapton.
For applications that require Kapton cutting with minimal processing strain, like routing and de-paneling flexible circuit boards with sensitive components, using UV lasers is definitely the way to go. Kapton can also come with an adhesive backing, that many laser cutting projects process as a “kiss cut“, use in numerous applications.
Laser cut Kapton is proven through rigorous testing to be virtually vibration free which will keep your solder joints stress free and sensitive chipsets safe. There are many advantages to laser cut Kapton, but cleanliness will have to be far up that list.
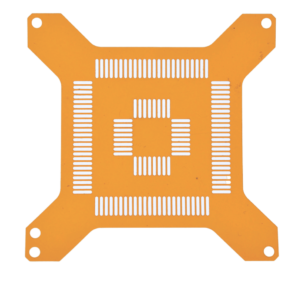
It’s well known that with any industrial fabrication process, cleaning of the fabricated products will have to follow. And though you may not consider it too much during your design stage, it can end up costing more than the fabrication process itself.
Using UV Lasers for Kapton Cutting
During cover layer cutting, holes are cut through the Kapton PI film before it’s laminated on a circuit board. The process demands accuracy and control, especially as the final result is often used on tiny boards without much tolerance for imperfections.
The LPKF UV lasers we work with are ideal for this intricate process. Laser ablation gives us the control we need to create detailed cut-outs.
For example, we might use an LPKF laser to cut squares out of PI film to expose copper pads so that they can have components soldered to them later. (In such a case, the PI film is acting as a solder mask to prevent the solder joints from shorting between the copper pads.)
UV lasers make fine cuts with high accuracy. Because they avoid problems caused chemical, heat, and mechanical methods, they allow us to complete the project to your exact specifications.
Our Other Laser-Cutting Services
We offer a wide range of laser-cutting services, including laser skiving, laser depaneling, laser ablation routing, and more. We work with both UV lasers and infrared lasers to give you the choice of the best method for your project.
Find Out How We Can Help
Our technical engineers walk you every step of the way through the manufacturing process. We’d be happy to talk more about your project and how we can help.
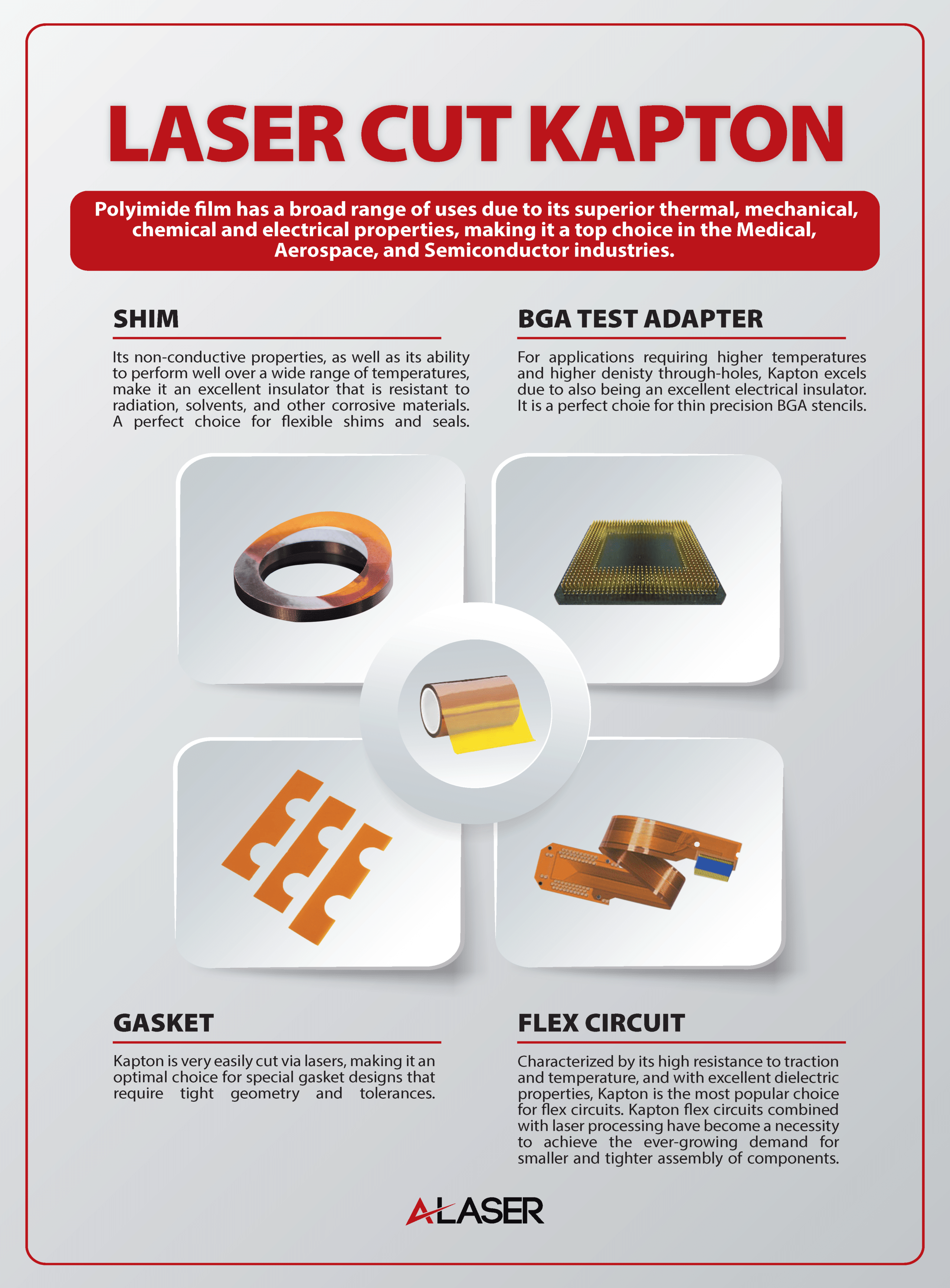