The Benefits of Precision Laser Cutting for Alumina Ceramic Parts
In the ever-evolving world of modern manufacturing, laser cutting technology has emerged as a game-changer, especially for applications that require high precision. This cutting-edge technique utilizes concentrated laser beams to deliver unmatched accuracy and efficiency in material cutting processes. When it comes to alumina ceramic parts, known for their remarkable hardness and thermal stability, precision laser cutting presents an array of advantages. From crafting intricate designs to minimizing material wastage, this technology ensures that each component consistently meets the highest standards of quality and performance. Laser technology has been used for the manufacture of components for over 40 years and continues to gain a broader reach as new ideas and directions for technology take hold and advancements in materials are further researched and developed. Although not the newest material available, alumina ceramic possesses characteristics that are ideal for many applications.
Alumina ceramic is primarily composed of aluminum oxide (Al2O3), a highly versatile and widely used ceramic material. It’s known for its exceptional hardness, high strength, and excellent resistance to wear, corrosion, and high temperatures. When paired with laser technology, the combination of the two can be beneficial to the end user and in turn the industries harnessing such technology and material. Some key advantages to laser cut alumina ceramic are:
Key Advantages of Laser Cutting Alumina Ceramic:
- High Precision: Laser cutting offers exceptional accuracy and can create intricate geometries with minimal material loss.
- Flexibility: Enables the production of complex shapes and patterns that would be difficult or impossible to achieve with traditional machining methods.
- Reduced Material Waste: Minimal material is wasted during the cutting process, improving efficiency and reducing costs.
- Non-Contact Process: Eliminates the risk of tool wear and tear, ensuring consistent part quality.
- Rapid Manufacturing R&D and Prototype: The laser process can expedite research and development by having a quick set-up process that does not require any tooling. One of the main factors in laser cutting is the design file or CAD file, which comes directly from the customer. This is used to program the laser cutting machine to create the exact part from the digital design.
- Laser Volume Manufacturing: Laser Volume manufacturing provides support for all industry disciplines and can transform from a low volume service provider to a member of the supply chain. Coordination ensues as with all manufacturers of material supply and production to meet demand schedules.
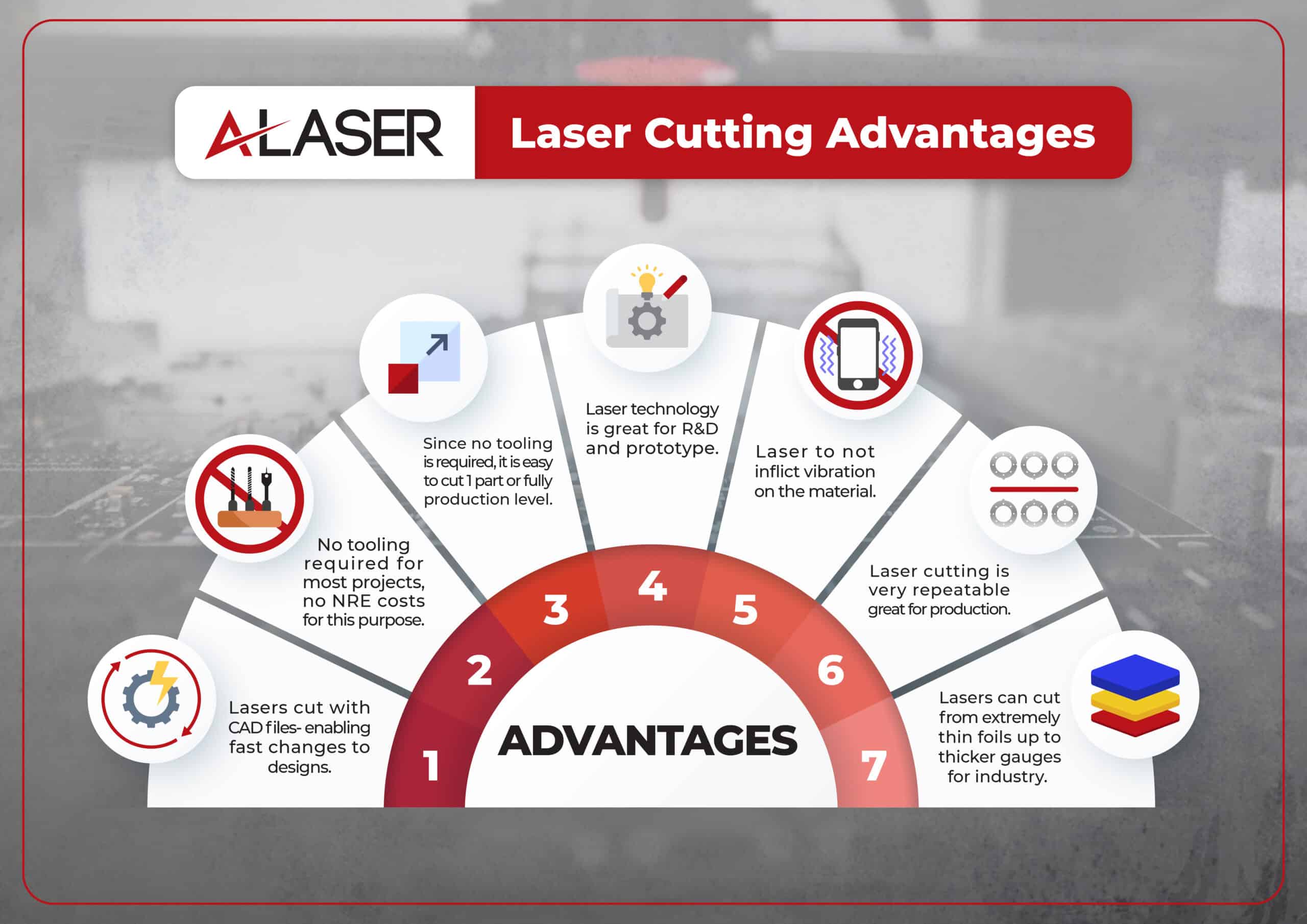
Laser Technology and Alumina Ceramic
Another advantage to laser cutting technology is the variety of laser systems available to manufacturers. Laser cutting machines harness different wavelengths of light and are made from low wattage (15 to 20 watts) to high powered (400 to 4000 watts) , for examples. Some types are: pico-second, femto-second, nano-second, fiber, CO2, ultraviolet, and infrared are amongst the most popular. For alumina ceramic applications, the best laser technology is determined per the details of the project, including the thickness of the alumina, the geometry of the designed component, the volume of the project. Each laser technology varies in the materials they can cut and the capabilities each can offer. In choosing one over the other in cutting alumina ceramic the following factors should be considered:
- Material Properties: The specific properties of the alumina ceramic (e.g., purity, grain size) can influence the laser cutting process and the resulting part quality.
- Laser Parameters: Careful selection of laser parameters (e.g., power, pulse duration, focus) is crucial for achieving optimal cutting results.
- Heat Affected Zone (HAZ): It’s important to minimize the HAZ to avoid material degradation and maintain the desired mechanical properties.
Where Can You Find Alumina Ceramic Parts?
For those in industry, it may be obvious to how alumina ceramic is used, but for many the applications may not be so well known. The world we live in is complex and over the past 125 years industrial processes have changed to keep up with the demands of technological advancements. This desire to push for enhancements has changed the quality of life by providing goods and services and helped increase the world’s economy through new materials and manufacturing methods that transform them into products for industrial uses to medical, electronics and other commercial and consumer needs. Alumina ceramic is one of those materials that has become crucial in applications like:
Micro-electro-mechanical systems (MEMS) components:
- Tiny gears, nozzles, sensors, actuators.
- Stents, orthopedic implants, dental components.
- High-precision nozzles for rocket engines, intricate parts for aircraft engines.
Electronic components:
- Substrates for integrated circuits, high-frequency components.
Wear-resistant parts:
- Precision bearings, seals, cutting tools.
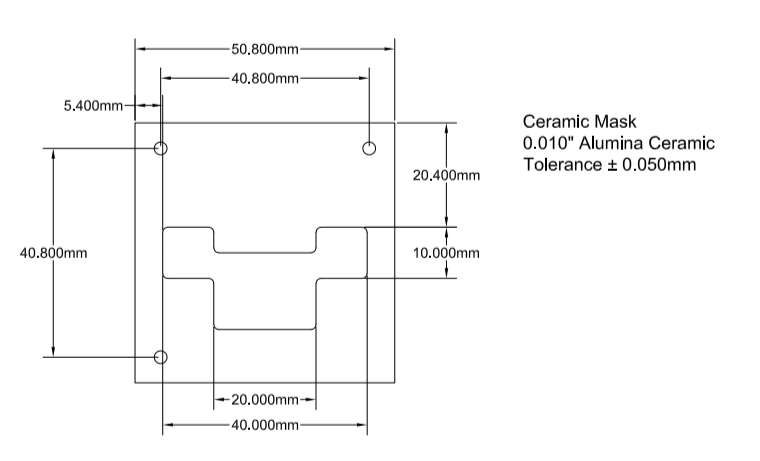
In conclusion, the use of laser cutting for alumina ceramic materials offers unparalleled precision and efficiency, making it an invaluable tool across a wide range of industries. From micro-electro-mechanical systems to medical implants, aerospace components, electronic substrates, and wear-resistant parts, the ability to achieve high-precision cuts with minimal thermal impact is transformative. This advanced technology not only enhances the quality and reliability of the finished products but also significantly reduces production times and costs, ensuring that industries can meet the demands of modern engineering and innovation with confidence and excellence.