Laser Ablation
Precision Material Removal for Advanced Manufacturing
What is Laser Ablation?
The term “ablation” refers to the controlled removal of material, and in the case of laser ablation, this occurs at the microscopic or even nanoscopic level. The laser’s energy disrupts the molecular bonds in the material, causing the outermost layers to disintegrate and be ejected as vapor, plasma, or particulate debris. Laser ablation is a cutting-edge process that acts as a solution for advanced manufacturing. This process involves intense energy directed at a very small area, causing rapid vaporization, sublimation, or melting of the material. The key advantage of laser ablation lies in its non-contact nature, meaning no physical tools are used to remove material, making it ideal for applications that require precision and minimal mechanical stress.
How Does Laser Ablation Work?
Laser ablation is a sophisticated process based on the precise interaction between a laser beam and the material surface. Here’s a step-by-step breakdown:
-
Laser Beam Emission:
The process begins with the emission of a focused laser beam composed of high-energy photons. These photons are delivered in extremely short pulses, typically in the range of nanoseconds (10^-9 seconds) to femtoseconds (10^-15 seconds), ensuring that the energy is concentrated in a small area for maximum impact. The pulse duration is critical, as shorter pulses reduce heat diffusion into surrounding material, preventing unwanted thermal effects. -
Photon Absorption and Material Heating:
When the laser beam hits the material, its wavelength plays a crucial role in how the material absorbs the light. Materials absorb specific wavelengths differently, so the laser is fine-tuned to match the material’s absorption properties. For instance, metals typically absorb shorter wavelengths more effectively, while polymers may require longer wavelengths. Once absorbed, the material’s surface rapidly heats to extreme temperatures.
- Vaporization or Sublimation of Material:
As the laser’s energy continues to focus on the material’s surface, it heats up beyond the material’s melting and boiling points, causing the material to vaporize or sublimate (transition directly from solid to gas). This phase change happens in a localized region, allowing for highly controlled and precise removal of material without affecting the surrounding areas. This can be done on a wide variety of materials, including metals, polymers, ceramics, semiconductor, and more.
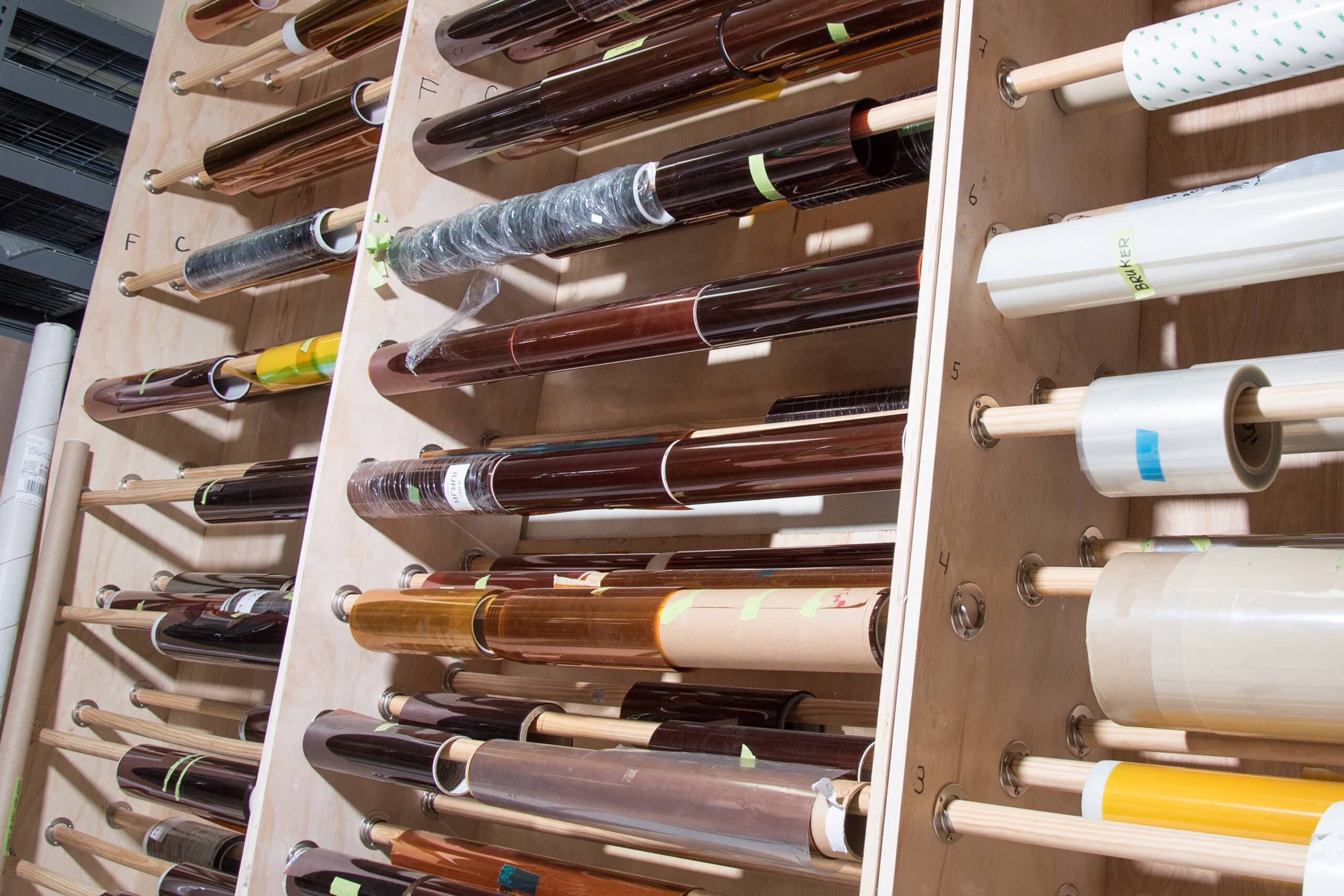
- Controlled Depth and Beam Diameter:
One of the advantages of laser ablation is its ability to control the depth of material removal. By adjusting the beam diameter, operators can fine-tune the area affected. For extremely detailed applications, the laser beam can be focused to a diameter of just a few micrometers, allowing for microscopic precision. The depth of ablation can be controlled by adjusting the laser’s energy density (also known as fluence) and the number of pulses delivered to the same area. -
Fine-Tuning via Wavelength, Pulse Rate, and Power:
The laser’s wavelength, pulse rate, and power are adjusted based on the type of material and the precision required. For example, short wavelengths (like UV lasers) are often used for fine ablation on delicate materials, while longer wavelengths may be more effective for metals or ceramics. A high pulse rate ensures smoother ablation, whereas a lower rate might be used for rougher material removal.
By manipulating these parameters, laser ablation can achieve remarkable precision, making it ideal for industries that demand fine tolerances and minimal material waste.
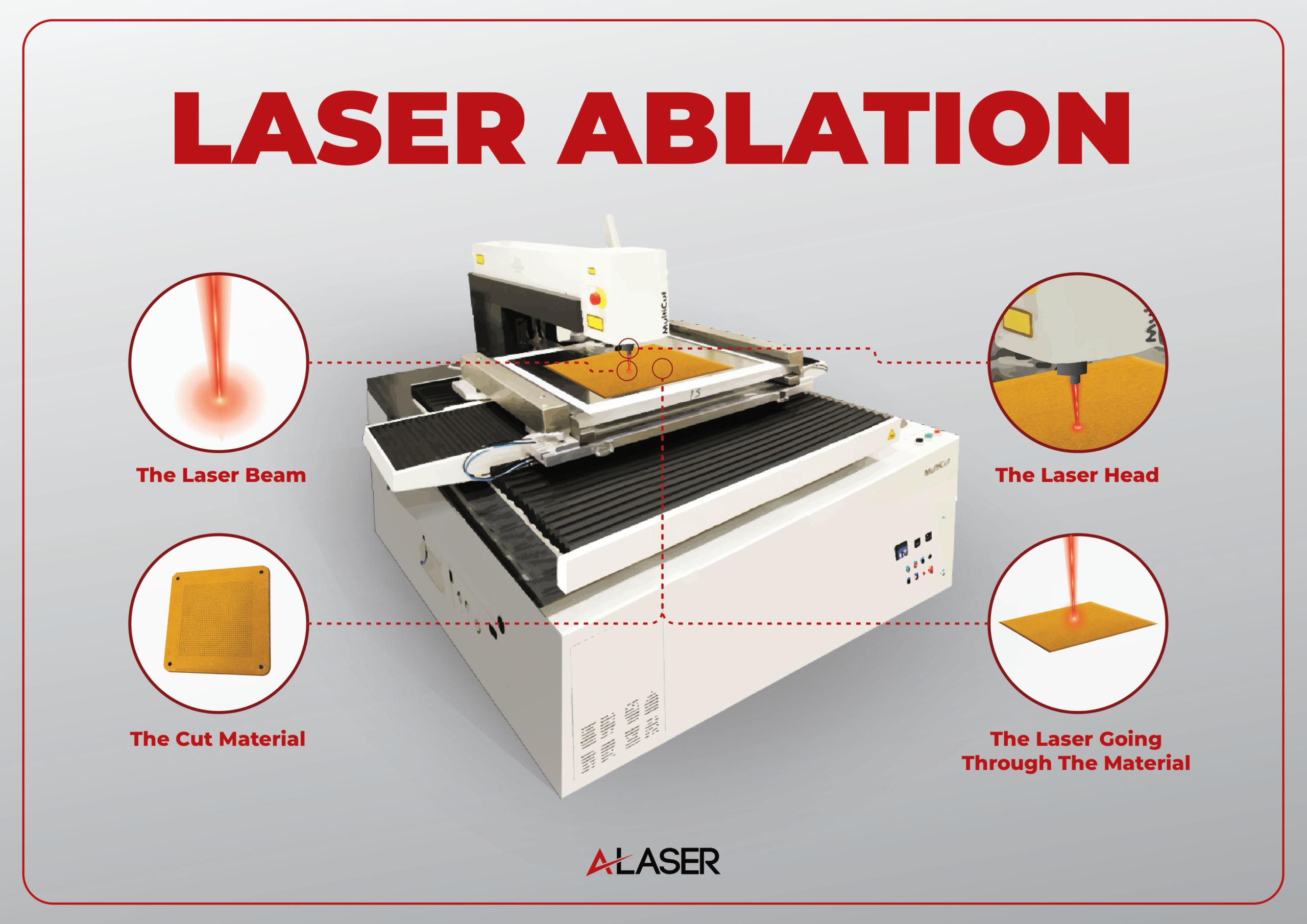
Laser Ablation vs Laser Skiving vs Laser Engraving
Laser Ablation:
Process | Purpose | Depth of Material Removal | Typical Materials | Common Applications |
---|---|---|---|---|
Laser Ablation | Complete material removal | Varies from shallow to deep | Metals, ceramics, polymers | Micro-machining, medical devices, aerospace |
Laser Skiving | Selective layer removal (thin layers) | Thin layers (fractions of a mm) | Laminates, composites, polymers | Flexible circuits, multi-layered composites |
Laser Engraving | Surface marking or shallow etching | Shallow (fractions of a mm) | Metals, plastics, ceramics | Branding, part identification, aesthetic designs |