Innovation Culture
As a major owner of A-Laser and the other FCT companies (Florida CirTech, FCT Water, FCT and FCT Solder) since 1993, I get to participate in quarterly meetings to review ideas. The excitement and energy around pushing the limits and problem-solving that is brought to the table within these companies makes me grateful to be a part of it.
In having only been peripherally involved in A-Laser, I’m going to write this with a slightly different perspective. The company culture at A-Laser carries throughout this family of companies. So, I want to switch gears and talk about innovations from A-Laser’s partners and provide some insight into the values and ideas that set us apart. Let’s start.
Immersion Tin
This project started over twenty years ago. At that time, the exposed copper on a finished printed circuit boards were primarily coated by conventional solder in a process known as Hot Air Level or HASL, with the idea being to protect the surface of a “bare board” prior to final assembly solder. During this time, there was a new Electroless Nickel Immersion Gold process known as ENIG but this process was cumbersome, not well understood and expensive. We spent a good five years developing our Immersion Tin process by refining and getting a better understanding of the role intermetallic Tin/Copper plays in overall solderability and the solder reflow process. Our company at this time was much smaller and this effort was our first real work involved in developing a process while working intimately with both printed circuit board manufacturers, assemblers, and OEM’s. In contrast to some of our more conventional products we developed, this project really energized everyone in our organization.
Lead Free Hot Air Surface Levelling
One of our next projects was started over ten years ago and involved a collaboration with a Japanese soldering company Nihon Superior and their SN100C patented lead-free solder alloy. We started selling this alloy for both wave and hand soldering but wondered if it could be used as the alloy for Hot Air Leveling or LF HASL on a bare printed circuit board. Prior to our work, many larger companies attempted LF HASL with their own proprietary lead-free solder alloys with very little success due to excessive oxidation of the solder, etching of the copper substrate and even attack on the solder pot itself. In working with Nihon Superior, we were able to come up with a process that enabled SN100C to be the de-facto standard for LF HASL.
NanoSlic
My next example deviates from the previous examples in that this chemistry had nothing to do with a printed circuit board. NanoSlic is a product that is coated both on the under-side and inside the apertures of a stencil to both reduce solder bridging and enhance the printing of solder paste for high aspect ratio apertures. This project started by developing a high contact angle oleophobic coating that is thin and uniform and does not clog apertures. We continued developing this process by enhancing adhesion through novel laser structuring, something unheard of in the industry. We have also leveraged our knowledge and expertise in Oleophobic and Hydrophobic chemistry by developing quasi permanent waxes for cars, trucks, boats, and other applications where ceramic coatings provide a protective benefit.
Next Generation Solder Pastes
The last product I wanted to touch on has to do with our solder pastes. We have deployed our resources and focus in the past five years in taking solder paste to the next level. We started by developing solder pastes with lower viscosity that do not slump, as this could improve printing. We have also developed solder pastes that are both Halide and Halogen free and can be pin tested, thereby providing greater reliability, particularly when the circuit board is exposed to a variety of environments “in the field.”
The development of these various products and advancements are typically initiated by Mike, me, and other valuable members of our team. The research itself is applied with a narrowing of focus, in many cases, due to both our understanding of the industry we are in plus conversations with customers and others in our market.
Not all projects bear fruit, and many projects take longer than expected with obstacles that need to be overcome; but then again, that is the nature of R&D.
Over the years, I have seen our industries change. In particular, the way in which business is conducted and the large role the internet has in marketing. And yet, the core of R&D remains dependent on the commitment of management, dedication of talented individuals with a passion for creating and developing products and the resources to carry this out. Reflecting on the problems we’ve solved and lessons we’ve learned throughout the past several decades has me excited for what’s to come.
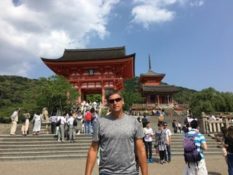
About the Author
Tom Scimeca has been a major owner in FCT Assembly since nearly the inception. Tom’s insight and experience has been critical to the success of this group of companies. He currently resides in California. Since joining as an FCT partner in 1993, Tom has also started and built up two other companies: EFT Fast Quality and JD processing. Tom’s hobbies include playing pickleball, ping pong, mountain biking and travel.