How Tight Can Tolerances Be in Precision Machining?
Understanding Tight Tolerance Machining
Tight tolerance machining is essential for industries requiring extreme precision, such as aerospace, medical devices, and semiconductor manufacturing. But how tight can tolerances realistically get?
Tolerance Level | Measurement | Common Applications |
---|---|---|
Standard Machining | ±0.005” (5 mil) | General metalworking, structural parts |
High-Precision Machining | ±0.001” (1 mil) | Aerospace, automotive, precision fittings |
Ultra-Precision Machining | ±0.0005” (0.5 mil) | Medical implants, semiconductor components |
Extreme Precision | ±0.0001” (0.1 mil) | Optical lenses, microelectronics |
Factors That Impact Achievable Tolerances
Material Properties –
Harder materials require different tooling to maintain precision. Softer metals, like aluminum, may deform slightly under pressure, while materials like titanium resist wear but require specialized tooling. Composites, depending on their fiber structure and resin composition, can also present unique machining challenges such as delamination or fiber pull-out.
Environmental Factors –
Temperature changes can cause material expansion, affecting precision. Even slight fluctuations in workshop temperature can cause microscopic shifts in material dimensions.
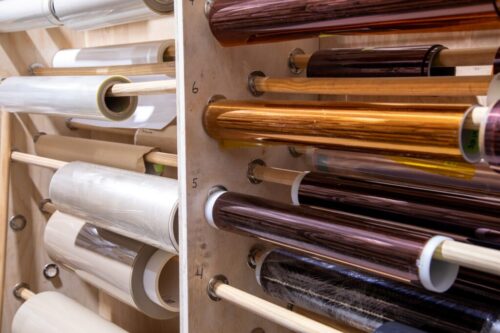
Machine Capability –
Advanced CNC machines, laser cutters, and EDM systems provide varying levels of accuracy. Multi-axis CNC machines allow for more complex cuts with higher precision. At A-Laser, we utilize UV and Fiber laser systems, which offer extremely fine feature resolution and minimal heat-affected zones, making them ideal for high-accuracy cutting of thin metals, plastics, and delicate substrates.
Tool Wear –
In CNC machining, tool wear is one of the primary causes of dimensional drift. Continuous cutting generates heat and friction, causing tools to gradually lose their sharpness, leading to increased cutting forces and reduced accuracy. Diamond-coated tools or ceramic tooling can extend longevity and maintain precision.
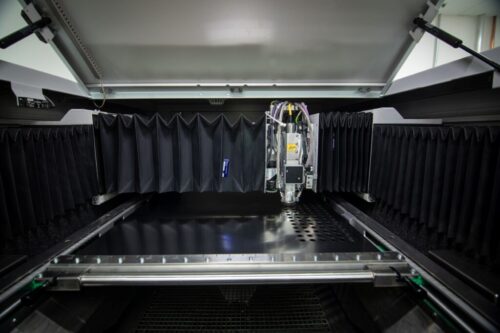
Achieving Sub-Mil Tolerances
-
Advanced CNC Machining: Uses computer-controlled movements for extreme accuracy, with advanced positioning systems maintaining consistency.
-
Laser Cutting & EDM: Ideal for high-accuracy cutting with minimal material distortion. EDM is particularly useful for materials that are too hard to machine conventionally.
-
Temperature-Controlled Environments: Regulating workshop temperatures ensures parts don’t expand or contract unexpectedly.
-
In-Process Metrology: Real-time measurements help adjust machining parameters to maintain consistent tolerances.