How Does Surface Finish Impact the Performance of Machined Parts?
The intricate realm of surface finish, a factor that can dramatically dictate a component’s performance and longevity, goes far beyond mere dimensional accuracy. In pursuit of perfectly machined parts, surface finish machining delves into not just about how a part looks, but how it functions. Surface finish, that often-overlooked detail, can be the difference between a part that performs flawlessly and one that fails prematurely. Fine-detail machining demands materials that can hold sharp edges, maintain dimensional stability, and withstand the rigors of delicate cutting operations. Some materials are better suited for intricate designs and this must be kept in mind for the interplay between surface roughness vs smoothness in cutting processes. Determining the challenges ahead of manufacturing is essential for optimizing performance, extending tool life, and achieving desired part quality. Understanding how different finishing techniques translate to tangible performance improvements is crucial for engineers and designers alike, as it directly impacts the reliability and efficiency of everything from delicate medical devices to robust aerospace components.
Surface Finish in Manufacturing
Surface finish, in both traditional machining and laser manufacturing, can profoundly influence a machined part’s function and performance. In machining, techniques like grinding, honing, Tumble deburring and polishing remove material to minimize surface irregularities, reducing friction, wear, and stressed areas. A smooth surface will enhance fatigue resistance for components subjected to cyclic loading. Conversely, in laser manufacturing, such as laser cutting or ablation, the heat-affected zone, (HAZ) and material re-deposits can create unique surface textures. Controlling laser parameters, like pulse duration and power, passes and speed are vital to minimize roughness and produce the desired finish. Without such controls, corrosion resistance, optical esthetics, and performance will be diminished.
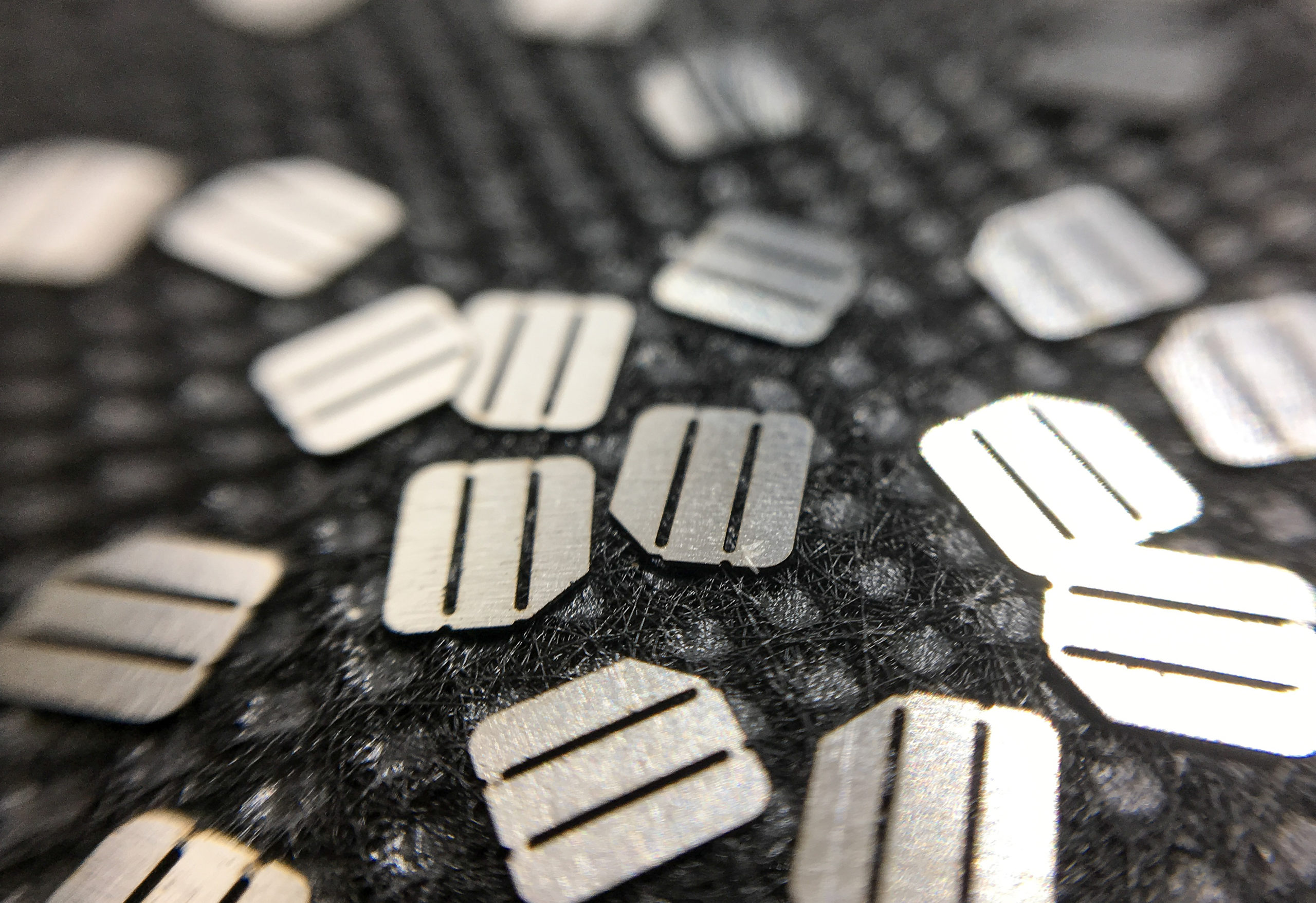
Roughness vs Smoothness in Manufacturing
The interplay between roughness and smoothness in manufacturing precision parts using CNC and laser technology involves a delicate balance. In CNC machining, achieving a desired surface finish often entails controlling the cutting tool’s feed rate, depth of cut, and spindle speed. A smoother finish typically requires slower feed rates and finer cutting tools, while a certain level of roughness might be desirable for applications requiring increased friction or surface adhesion. In laser manufacturing, the focus shifts to controlling the laser’s energy density, pulse characteristics, and scanning strategy. While laser polishing can achieve ultra-smooth surfaces, laser texturing can create controlled roughness patterns for specific functional requirements, such as improved fluid flow or enhanced bonding. For example, a CNC-milled mold for plastic injections might require a highly polished surface to ensure smooth part ejection, while a laser-etched surface on a surgical instrument might incorporate micro-roughness to improve grip. Essentially, the required balance between Roughness and Smoothness is dependent upon the desired application of the finished part. Some other examples such as in aerospace applications, a highly polished turbine blade, achieved through precision grinding, minimizes air friction and maximizes efficiency, however while a laser-textured surface on a medical implant can promote osseointegration, which promotes bone growth on the implant.
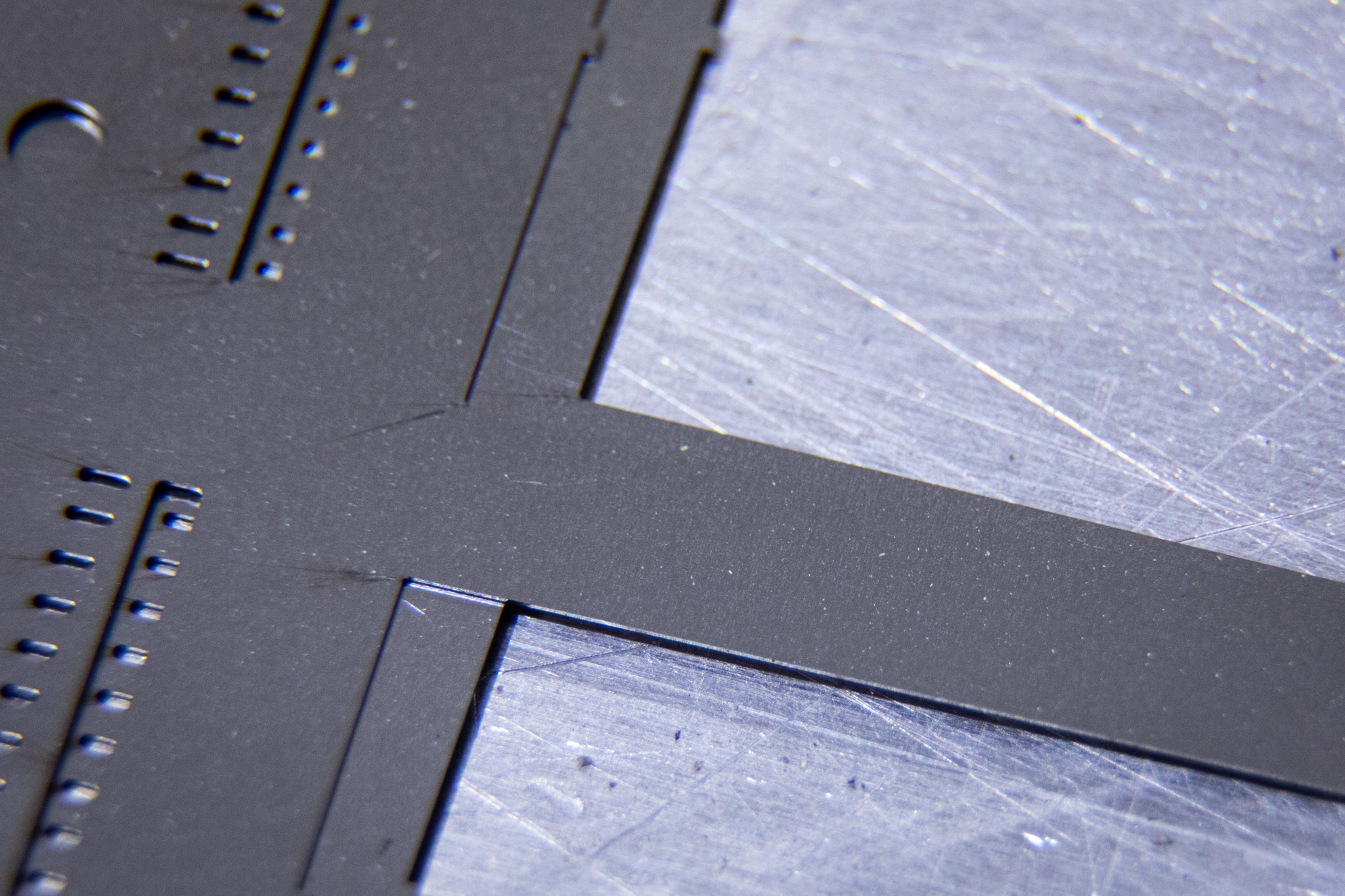
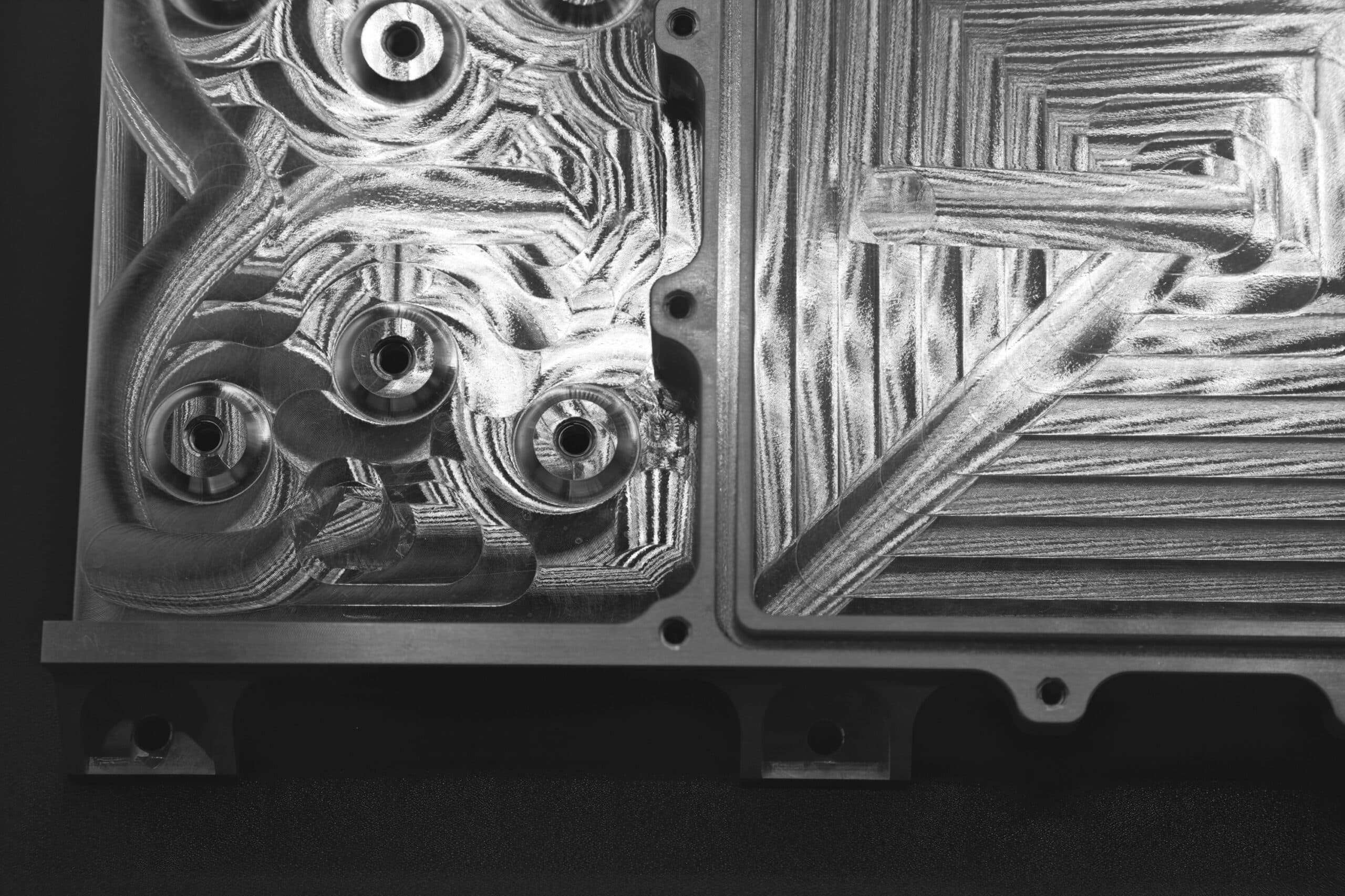
Laser Cut Surface
CNC Milled Surface
Conclusion
In conclusion, a manufactured precision components surface finish is an important element of manufacturing. It’s a critical determinant of a machined part’s ultimate performance, affecting applications in industries world-wide. CNC machining, advanced laser techniques, and other precision manufacturing methods control surface roughness and texture to meet the requirements of critical components. From enhancing the efficiency of aerospace turbines to ensuring the biocompatibility of medical implants, the strategic manipulation of surface finish unlocks a spectrum of performance enhancements. Ultimately, understanding and mastering the intricacies of surface finish is essential for maximizing the potential of any precision-manufactured part, regardless of the method employed.