How Do You Inspect and Verify Parts with Extreme Precision Tolerances?
High accuracy cutting and manufacturing require the support of advanced technology for inspection of precision components. Coordinate measuring machines, laser scanners, digital calipers, and other advanced methods and devices confirm that extreme precision tolerances are produced within spec. It is of enormous importance that precision manufacturing processes follow industry guidelines like ISO certification, that embed a Quality Management System or QMS. Inspection of tight tolerance machining methods not only relies on the inspection devices, but the series of protocols put in place along the manufacturing line, from input of data to the shipment of final products. Inspecting and verifying parts with extreme precision tolerances requires a combination of advanced metrology equipment, meticulous processes, and a deep understanding of measurement uncertainty. Here’s a breakdown of the key steps and technologies involved:
Understanding the Tolerances and Specifications
- Geometric Dimensioning and Tolerancing (GD&T):
- Precisely interpret the engineering drawings and GD&T specifications. This defines the acceptable variations in form, size, orientation, and location of features. Understanding GD&T is crucial because it goes beyond basic dimensional tolerances and addresses complex relationships between features.
- Tolerance Stack-Up Analysis:
- Analyzes how individual tolerances contribute to the overall assembly tolerance, by using software and trained technicians to interpret and verify the data.
- Measurement Uncertainty Analysis: This defines the uncertainty associated with each measurement, ensuring that measured values are within the specified tolerances.
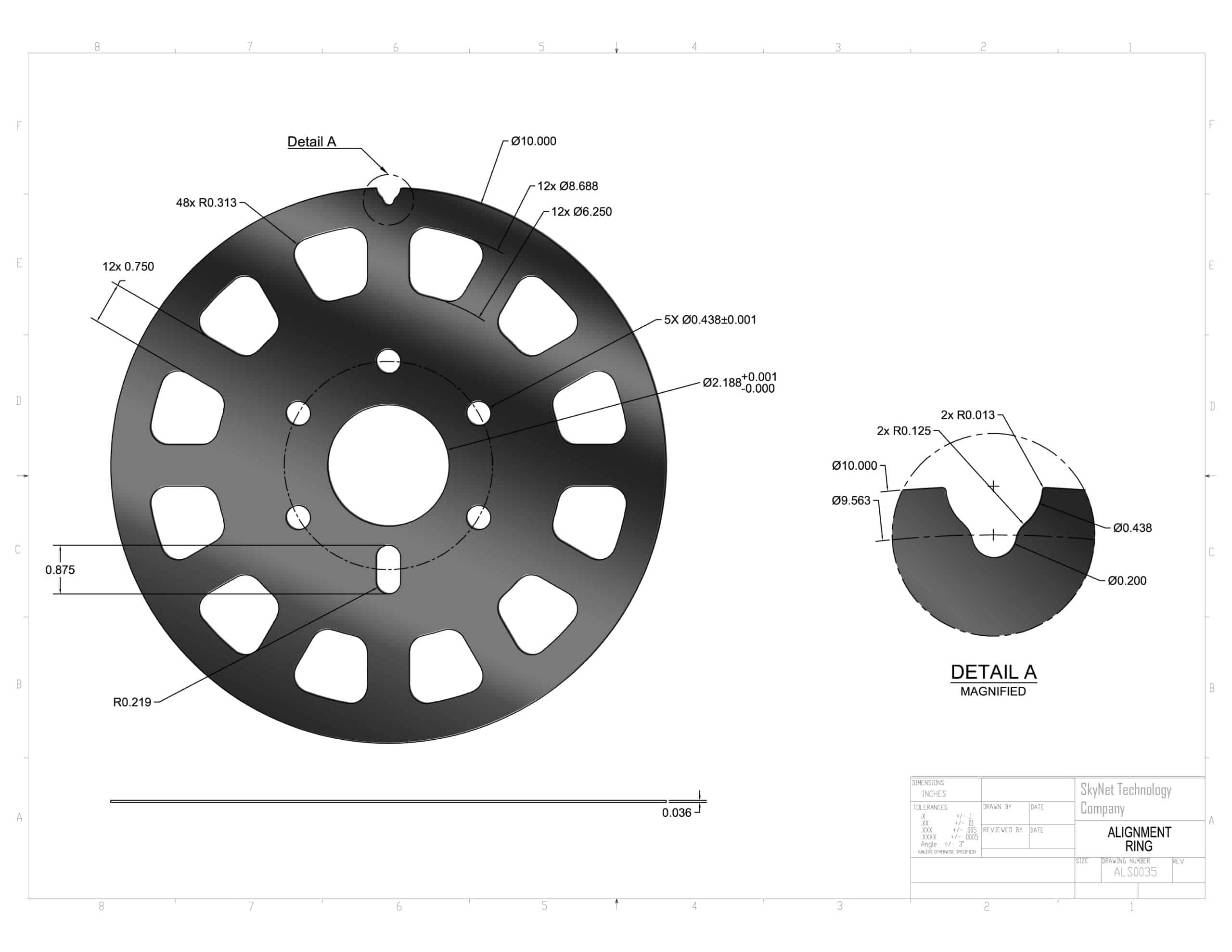
Metrology Technology
It is hard to believe that the level of goods and services, especially those from the medical, dental, optical, aerospace, energy and automotive industries evolved from more mechanical and uncontrolled manufacturing processes. It is common to see today that much of what we take for granted comes from ultra-precision engineering designs and processes. The finer and smaller we go with consumer goods and critical industries as mentioned, the level of inspection increases. To facilitate the need for certification of manufactured products, there is an array of inspection systems to confirm tolerance, geometry, surface roughness and overall quality. The following table highlights many of the inspection technologies in use today.
Inspection System | What Is Measured | Technology/Process | Used For |
---|---|---|---|
Coordinate Measuring Machines (CMM) | Measure the geometry of 2 and 3 axis compionents . | Uses optical and scanning probes. | Highly complex components and tight tolerances. |
Laser Scanners | Surface roughness of a 2D or 3D part. | Technology creates a model that can be compared to the actual CAD model. | This is a contactless process recording small variations of the surface. |
Interferometers | Measuring micron level or even smaller variations of surface roughness. | Use light interference measuring extremely small distances and surface variations. | Two or more light waves interact to create an interference pattern. Used to also in the sciences. |
Prolifometers | Measuring the surface roughness and profile of the part. | Contact type uses a stylus to record the variation. Contactless uses optics and light for measurement. | For parts that have strict surface roughness requirements, aspects of glossy, smooth, wear resistance. |
Optical Comparators | Visually comparison of selected area. | Magnifies an image of the component | Good for in-process verification, with CMM type of system for final inspection. |
Gauge Block/Calipers | Measuring distance, diameters, thickness of material. | Calibrated gauges and tools mechanical device with digital readout of data. | The lesser of inspection, bit good for rough check or parts where the tolerance is larger. |
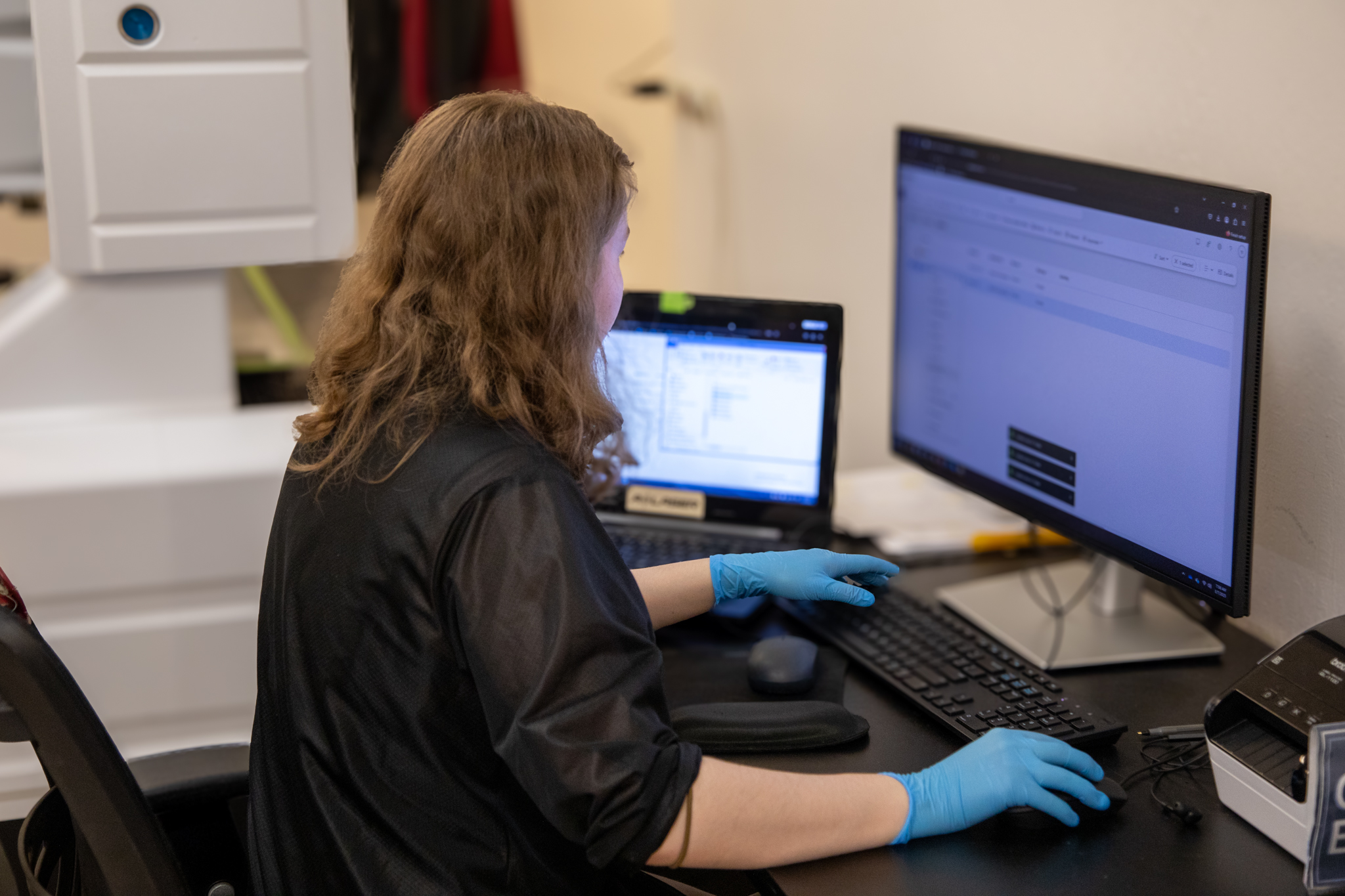
The Inspection Process Can Be Rigorous
Inspecting components made by ultra-accuracy cutting or tight tolerance machining does not occur without a full quality process implemented. This process includes inspection of thin and delicate metals to non-metallic materials. The process entails that from the start of communication through the manufacturing process and concluding with delivery, that each phase is focused on procedures to ensure the tight tolerances are met. Achieving precise inspection requires a controlled environment, meticulous handling, and rigorous equipment calibration. Maintaining stable temperature and humidity minimizes material distortions, while thorough cleaning and careful handling prevent contamination and damage. Regular calibration using traceable standards and verification with reference parts ensures measurement accuracy. Detailed, documented procedures standardize the inspection process, and specialized software enables comprehensive data analysis and reporting, highlighting any deviations from specifications.
Furthermore, implementing Statistical Process Control (SPC) allows for real-time monitoring of process variations, enabling proactive identification and resolution of potential defects through control charts and capability studies. First Article Inspection (FAI) verifies that initial production meets all specifications, and continuous improvement through process review ensures ongoing accuracy and efficiency. These combined practices guarantee the integrity and reliability of precision parts.
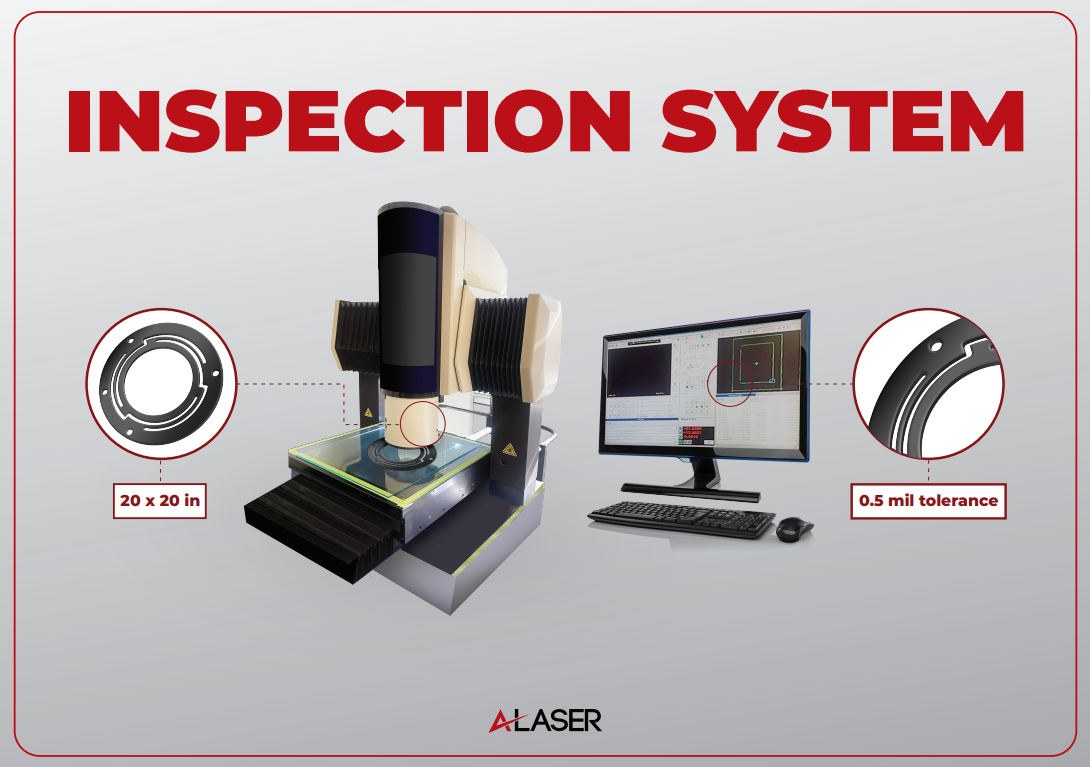