What Factors Influence Surface Roughness in Different Cutting Methods?
Surface finish in machining, laser cutting, waterjet cutting and other methods all have contributing factors affecting surface roughness. These factors can affect characteristics of precision parts like corrosion resistance, durability, aesthetic appeal and overall performance in a positive or negative way. These important specifications are found on technical drawings by surface roughness annotations, such as Ra (arithmetic mean height), Rt (total height) or Rq (root mean square height). The factors that influence surface roughness in different manufacturing methods are numerous, but some prominent ones seen in CNC technology are the machine tools settings of power, speed, tool material, geometry, and material selection. For laser technology, factors such as geometry, material thickness, laser power and cutting speed. Based on the requirements for the machined component, manufacturers determine the best cutting technology to achieve the necessary result.
A Deeper Dive into Surface Roughness
It can be a very complex set of factors that influence surface roughness in manufacturing. As complex as it can be, each methods used to produce high-quality precision components, focuses on its strengths in controlling surface roughness. Examples of surface roughness factors in manufacturing are:
- Tool selection- with tool angle, insertion point and exit point.
- Tool speed-How fast is the tool cutting.
- Edge Preparation– which can include chamfer, rounded, beveled.
- Chip Control- controlling this and how chips are expelled.
- Coolant Type- Proper temperature range and resistance to friction.
- Material Type- The thickness and hardness of material determines much of the planning for manufacturing. Once the surface annotations are known, this directs much of the processing factors.
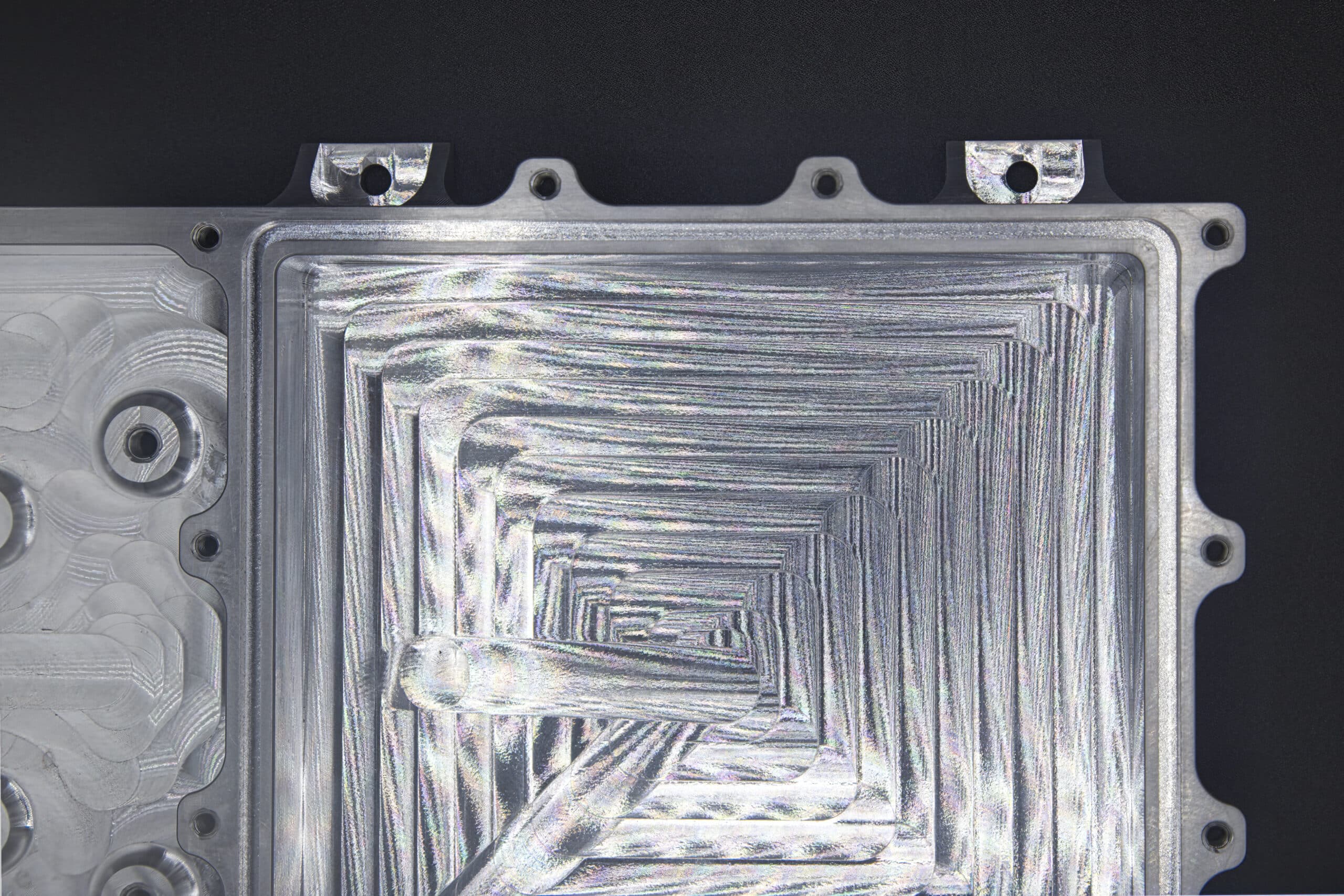
- Material type– Material selection for laser cutting is critical. Not all materials can be laser cut and some can be harmful if fumes and particulates are not filtered.
- Material Thickness- Laser cutting is primarily suited for flat, 2D cutting. Materials thicker than the laser capability are best done by other methods.
- Cutting Speed- Slower cut speeds produce less HAZ.
- Geometry – Simple geometry cuts fast, less time on the laser.
- Laser Power (Wattage)- Thicker materials or harder substrates require more power to cut through. This can affect surface roughness.
- Heat-Affected Zone– HAZ can affect the surface roughness by introducing thermal stress to the cut area.
- Water Pressure- The key to cutting is using high pressure of water through nozzles.
- Abrasives- Abrasives like silica sand, garnet, silicon carbide, and aluminum oxide are combined with high-pressure water to erode the materials.
- Standoff Distance- The distance from the nozzle to the cutting surface is a factor in controlling pressure and the speed of the cutting, which affects the surface quality.
- Traverse Speed- The speed at which the cutting tool moves from one point to another, can affect the surface roughness (Ra) and waviness (Wa) values. Also the depth of the cuts and material are factors that need to be adjusted too.
- Materials- In stamping, the density of the material and cutting tools does affect the surface roughness.
- Tool Parameters- Settings such as deviation angle, tool tip arc radius and trimming amounts, all can be adjusted lower or higher accordingly to reduce surface roughness.
- Vibration- Friction can be a culprit in stamping and by adding cutting fluid and also having some metal alloys heat treated before processing.
- Mold Design- An improper mold design or fabrication of the mold can add to excessive stress and poor surface quality.
In Conclusion
The factors that influence surface roughness in various cutting methods are multifaceted and interconnected. Waterjet cutting relies heavily on parameters such as water pressure, abrasive type, standoff distance, and traverse speed to achieve the desired surface quality. Each of these factors must be meticulously controlled to minimize irregularities on the cut surfaces. Conversely, metal stamping is influenced by the material properties, tool parameters, vibration control, and mold design. The proper handling of these elements can significantly reduce surface roughness, thereby ensuring a smoother finish. Understanding and optimizing these factors are crucial for achieving high-quality surface finishes in manufacturing processes, leading to improved product performance and compliance with stringent industry standards.