Exploring 3D Printing
With a new toy and a curious mind, A-Laser Engineer Robbie Devennie created a 3D printed phone stand in the shape of the A-Laser logo. Rather than throwing a label on an existing product, our team of innovative minds provides promotional materials that solve a problem and are designed and created in-house. Our goal is to continuously take our services and capabilities to the next level.
A new year brings new ambitions and ideas. To provide the most cutting-edge products, we need to continually consider advancements in technologies. Both 3D printing and laser cutting offer unique advantages to improve your manufacturing process. Laser cutting and 3D printing are essentially the direct opposite of each other, but the two processes complement each other nicely. The subtractive process of laser cutting allows for extremely intricate and precise designs on flat parts. For larger projects, laser cutting can also offer affordability. 3D printing is an additive process that can provide solutions from prototypes to your final product while minimizing material waste. 3D modeling software offers limitless creativity in designing complex three-dimensional plans.
Recognizing the various pros and cons of 3D printing services alongside laser cutting, we plan to continue to explore this option in 2021.
Internal meetings regarding possible expansion into the world of 3D printing sparked an interest in Robbie. Back in May, he began designing and working on the new laser system we installed in Guadalajara. Before this, he had only dabbled in 3D design. He set out a few challenges that he knew would help him further down the line. His first step was to imagine a shape and do his best to create it virtually. The second was to take an existing shape and recreate it. Always up to test his problem-solving abilities, he enjoyed the process and satisfaction that came with working through rough data and getting something clean in the end. He took the new A-Laser logo from the website and loaded it into Fusion 360. From there, he broke it down into its main parts and drew it in a native format. Happy with the outcome, he exported it into CAD to make a 3D part. After that, he moved on to designing the machine.
The logo was a good part to print to push the boundaries of his new 3D Printer, seeing how thin it could be and remain strong. Five to ten designs and three failed prototypes later, he went back to the basics and investigated a simple cut through feature on a solid part. After a couple of iterations, he had something useful.
Our valued employees have shared before how working with lasers shapes both their professional and personal lives. We pride ourselves on the fact that our team embodies our culture. The talented and motivated individuals that makeup A-Laser are willing to go the extra mile and test their abilities inside and outside of the office. Robbie purchasing a 3D Printer and exploring the possibilities is a perfect example of that.
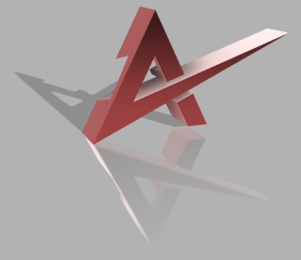