The best results for laser cutting thin metal foils and sheets are adhering to manufacturing guidelines and practices. There will be exceptions of course, but there are some foundational strategies that make precision laser cut parts an advantage to other manufacturing methods. Laser cutting in brief is the obliteration of the material through intensified light energy. Visible light is composed of different wavelengths and laser technology has harnessed some such as infrared and ultraviolet for cutting of metallic and non-metallic materials. As metal alloys react very differently from nonmetal materials and present challenges unique to the group, thus requiring careful planning and processing. Laser cutting thin metal materials are both an art form and a highly technical approach and when accomplished results in some of the finest and most accurate precision components that service and enhance heavy industries like oil and gas to textiles, nuclear research to medical implants and consumer goods.
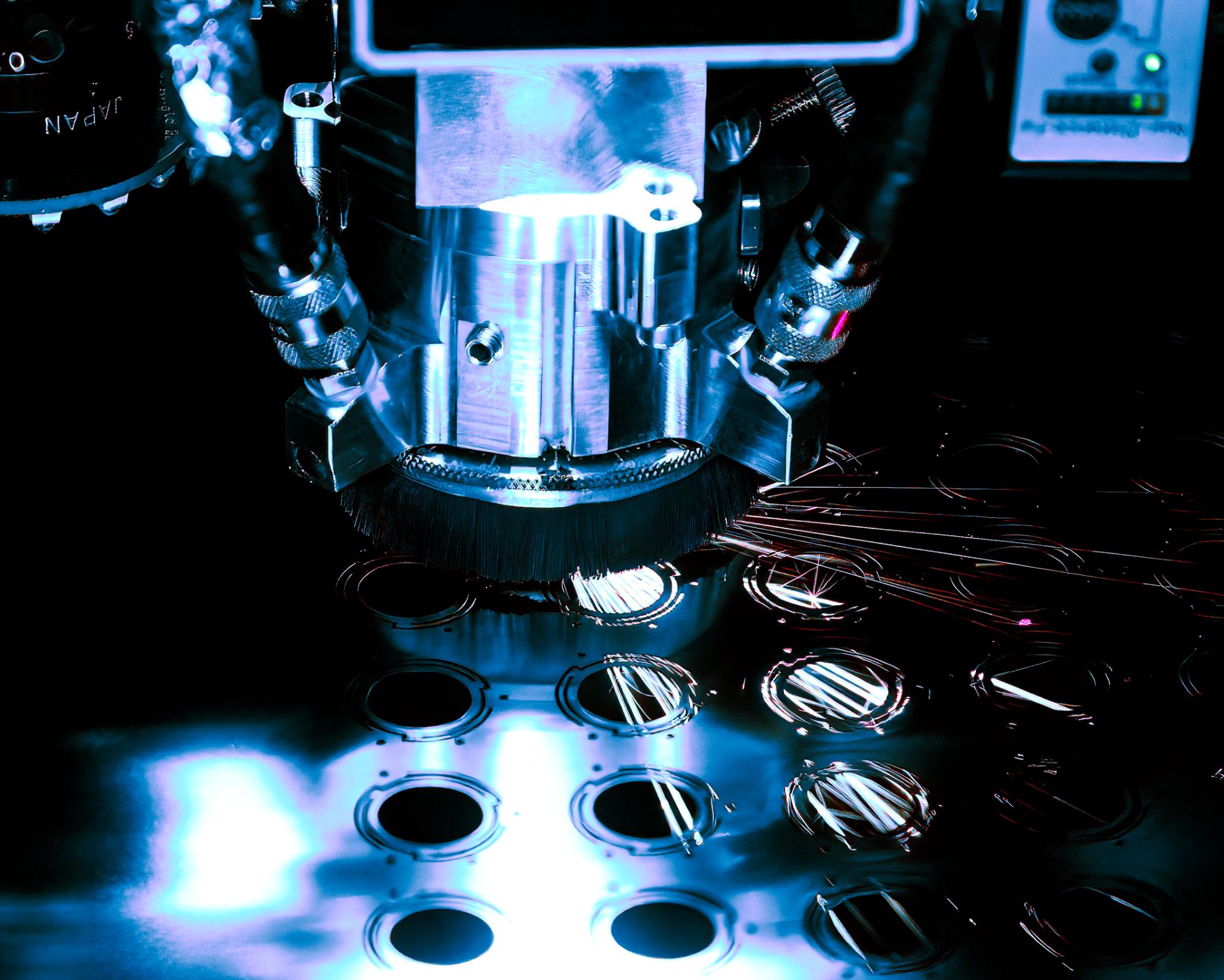
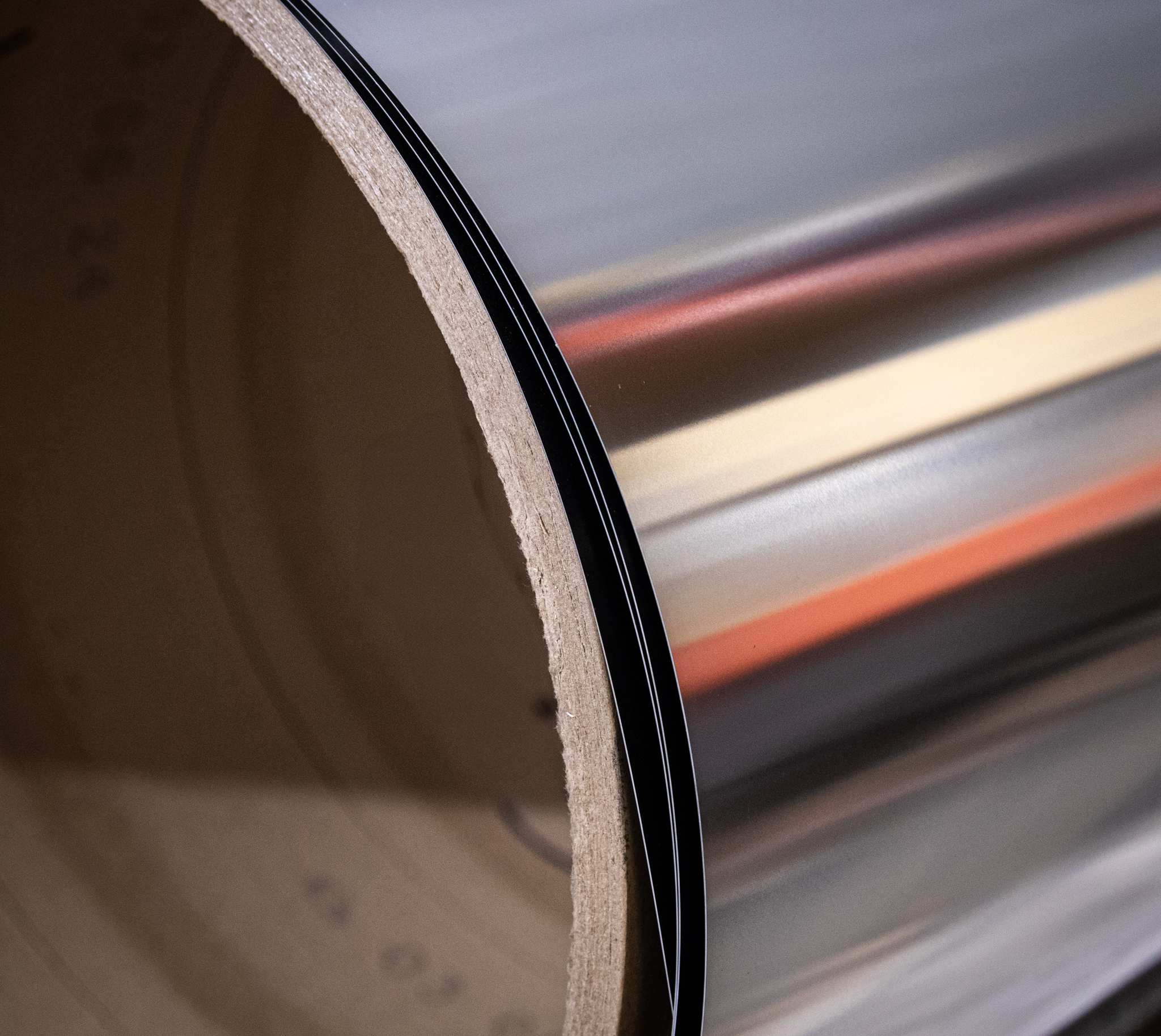
What Defines a Thin Metal?
Cutting a design out of a thin metallic sheet seems simple enough. Foil in your kitchen can be roughly torn or more accurately cut by scissors. For real tight accuracy and tolerance, a manufacturing method is needed. This is where thin and thicker metal manufacturing is specialized. General consideration of what is a thin metal material in precision components is about 1mm thick or less. Below 0.381mm is ultra-thin materials and metal alloys will come in sheets, that are pre-cut or foils which come in rolls of various widths. Foils can be comprised of thickness from as thin as a few microns and many from 10 to 25microns in thickness. The characteristics that such raw forms present to the manufacturing industry are easily damaged, higher cost, limited widths, design challenges. Laser cutting is primarily a solution for flat 2D profiles, that essentially makes it a great fit for this technology over other methods such as stamping, CNC Milling, and waterjet cutting. Success in producing precision parts, however, comes with support practices and considerations for both the engineering side and the manufacturing side.
The Best Practices and Advantages
Advancing and improving technology comes first from the idea that engineering is tasked with. How can this device or system be improved? What materials are needed and how best to produce them? Laser cutting is a great choice for precision components and partnering with a well-established service provider is the first key step. Consultation with and review of past and present work of manufacturers will guide to the better choice of support. Some manufacturers have a broad spectrum of expertise, while others have solid foundations working with specific industries like medical, automotive or aerospace. Once the relationship is established there are considerations to keep in mind such as:
- Material Choice: Metal alloys are produced in sheets and foils from stainless steel, aluminum, nickel, copper, nitinol, titanium, brass, tungsten, gold and brazing alloys. Not all laser cutting manufacturers have the capability to cut them all. Ask if they do handle the material, you need and the required laser cutting machines to produce your parts. Lasers are not all created equal and do have capabilities for cutting specific materials and thickness.
- Design Considerations: Lasers used focused beam of light energy that are small in diameter from a few microns as in Femtosecond or picosecond lasers, to 20um for Ultraviolet, 35um for infrared to 18-35um, for example. The beam diameters are technically the limit to any cut through feature whether a hole or radius, but most often require larger design specifications to meet edge quality and surface roughness requirements. These variables are indeed subject to each manufacturer’s laser cutting machines’ capabilities. For example, a UV laser cutting 1 mil stainless steel, may cut a hole at 20um in diameter but a perfectly round hole is produced at 50 to 75um.
- Material Thickness: With the application requiring small design features but on a thicker foil, for fluidic volume requirements for example, this may need to be to be done on a thinner foil with a larger hole diameter. Laser cutting produces a trapezoid shape where the laser entry side will have a slightly larger opening than the laser exit. This is more noticeable as increased thickness to the specific hole diameter. Working with the laser manufacturing team can assist in the design of features to result in the required feature shape and size.
- Heat Affected Zones (HAZ): Copper is great at dissipating heat and does not show indication of HAZ that other materials may have. Stainless-steel, however, is a wonderful material and used often in applications from cathode manufacturing to medical devices and surgical tools and countless industries. The characteristics however of stainless steel is that it can deform under extreme thermal stress and result in warping or oil canning of the foil or sheet. The density of features can produce HAZ and cause this warpage if not carefully planned both in cutting and the choice of materials.
Manufactures Adjustments
Laser manufacturing can make adjustments to the laser cutting process in multiple ways that will result in components intended for industries requiring high quality and repeatability. Each project is specific, but the focus of precision laser manufacturing is to achieve levels of manufacturing excellence for each job by making adjustments to:
-
- Laser Parameters: These include laser wattage, laser focus, wavelength, laser passes, dwell time, nesting of parts to efficiently save material. Programming of the laser cut path to reduce or negate any HAZ.
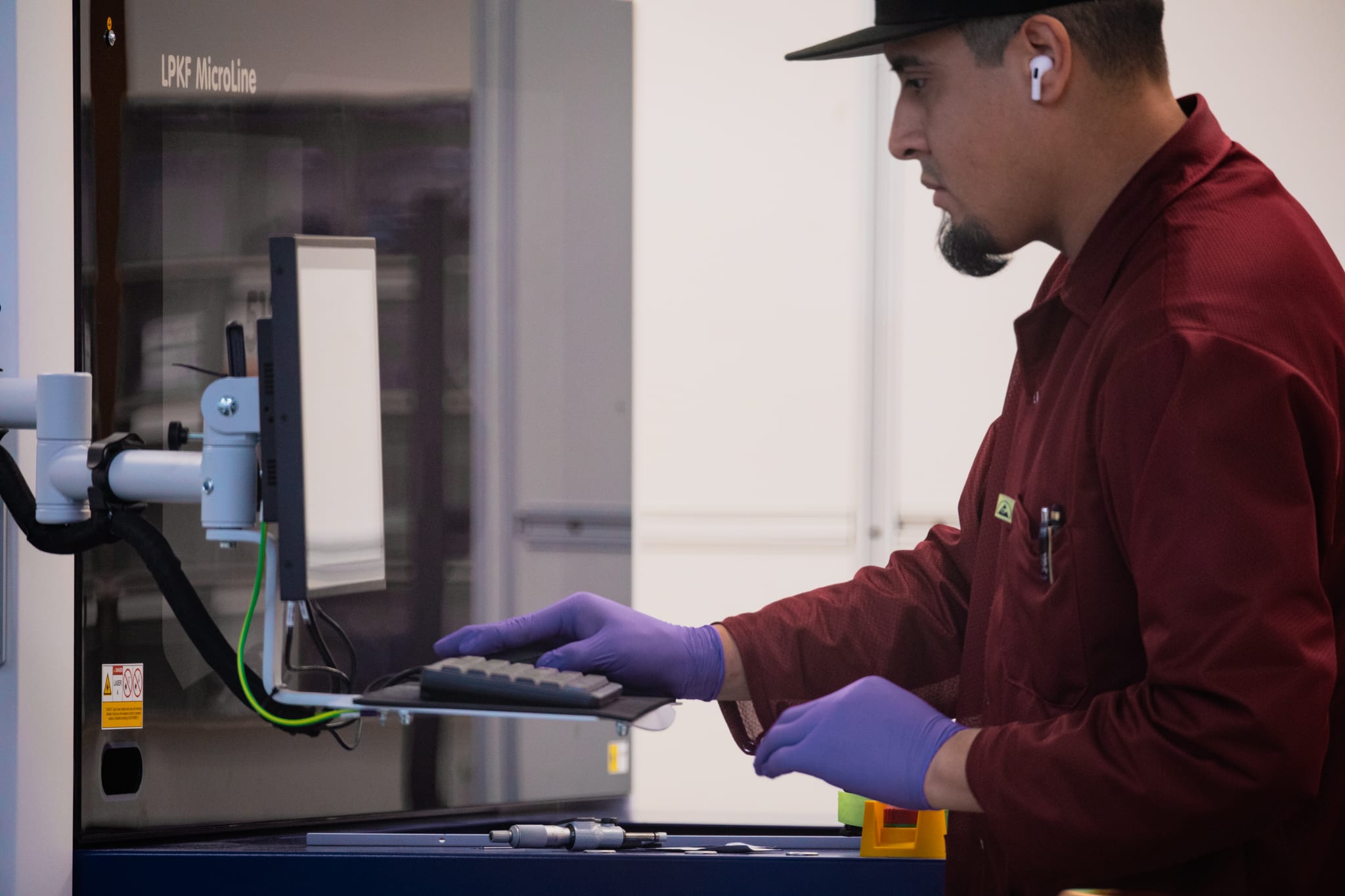
-
- Flagging Potential Manufacturing Issues: Laser service providers cannot design your component, but they should advise of potential challenges in the manufacture of the intended design. Flagging areas that can be prone to stress and non-conformance during the manufacture should be noted. Examples of this will be as mentioned, potentially HAZ, feature size and shape, structural integrity and surface roughness issues. Though laser cutting is a non-contact method, pressure from the gases used can be strong enough to damage delicate features during the process. This can be reduced by lower pressure and power but can increase throughput and cost.
- Material Recommendations: What materials will work best for the intended design and what characteristics does the selected material have that will need adjusting too. Being able to recommend materials is an advantage to every potential customer and project. Example. Using 304 stainless-steel, may produce HAZ, but using Invar metal, which has more nickel content, may be better, if approved to use.
- Post Processing: Laser cutting metal alloys even in thin form can produce slag or micro burrs. This is handled post laser by mechanical methods such as sanding or tumble deburring or can effectively be done by chemical etching or polishing. These processes improve the edge and surface quality and effectively enhance performance, durability and prolong the life of components.
- Multiple Iterations: One of the big advantages to laser cutting is the flexibility of the technology to cut multiple iterations of a design that is in early development. This can save time in evaluating and testing what features work best and where changes may be needed. With no tooling required for laser or set-up, this is a cost saving advantage.
These recommendations adjustments are called the “laser cutting tool” and are saved for current and future use of a specific project. Once dialed in, the repeatability of laser cutting is exemplary and produces exact copies of components with tight tolerances and high inspection levels. Changes to materials or design features will undergo a process review and if needed, a new “laser cutting tool” will be developed and archived.
Future Design Support
Another aspect to consider when planning a thin and delicate metal part is the support needed to transition from the prototype and R&D stages to full production support with laser technology. Procurement of these hard to handle and sometimes difficult to source materials are part of the job for manufacturing with laser specialists. Having formed relationships with material providers gives them the edge on lead time and many do have many alloys in stock that saves time and cost. Provided materials are welcomed and can be returned upon completion of a project or held for future use and that potential for volume production. With many highly critical industries requiring tight specifications to be held, many laser providers are registered under ISO guidelines and audited on a bi-yearly schedule to ensure that all manufacturing practices are met such as calibration to laser cutting machines and inspection measurement devices. Training in personnel and safety regulations. Material handling and process control from receiving orders to shipping of the final product. Laser cutting thin metal components is challenging and rewarding for both parties and when planned with the considerations mentioned, provides some of the best and accurate solutions of precision manufacturing.