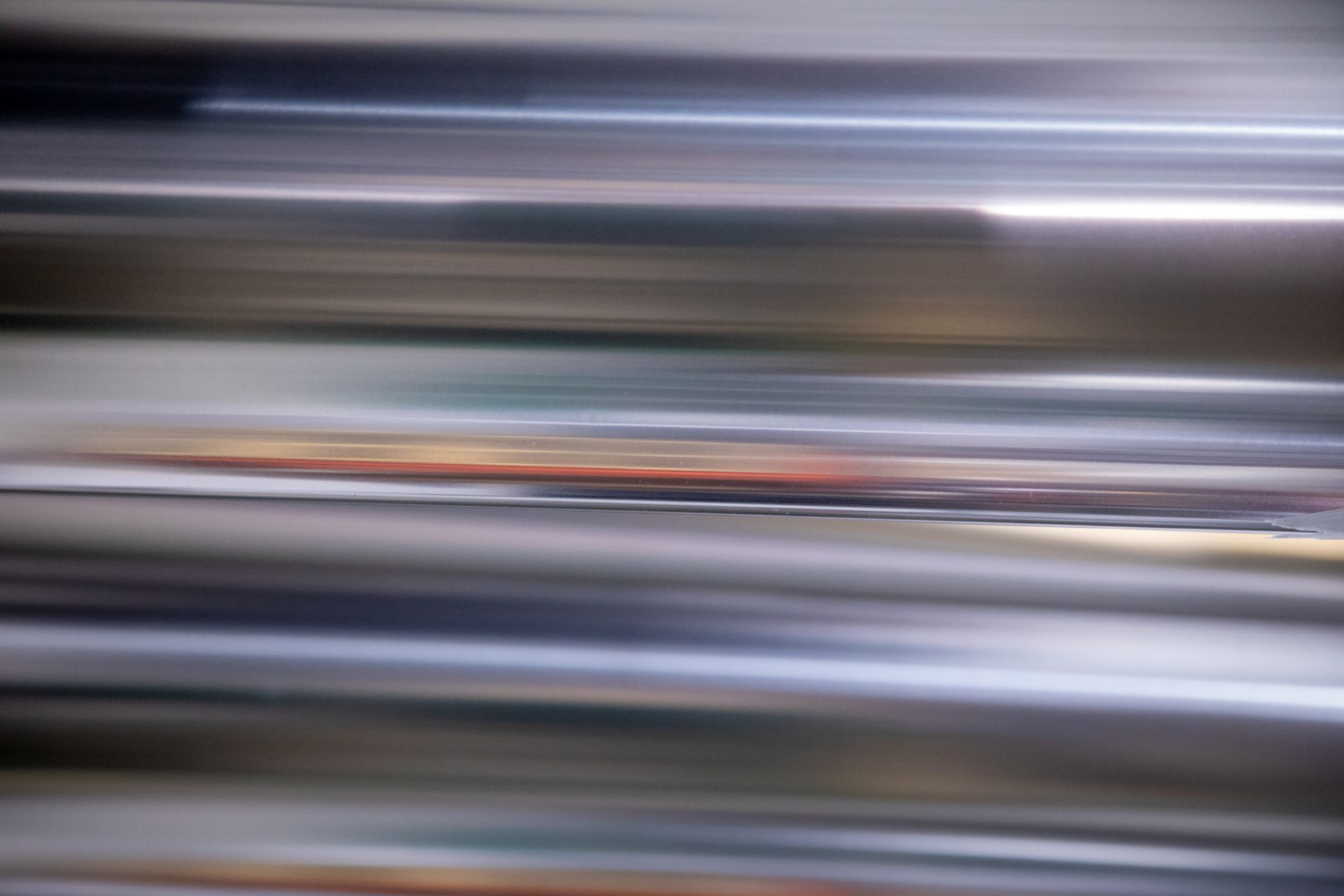
High precision metal laser cutting supports manufacturing by offering great capabilities and supporting numerous industries. These industries include wireless energy, semiconductor processing, battery technology, oil and gas, medical device, and aerospace, to name just a few. Laser manufacturing really started its influence by becoming a proven method back in the 1990’s and ever since it has found its niche in producing 2D high precision profiles. The technology for laser cutting metal, however, is as diverse as the types of projects that are supported. For this, let’s review what types of laser systems are available.
Cutting Through Multiple Systems
The available laser systems for precision manufacturing of metal parts allow many industries to benefit from utilization of laser manufacturing for industrial, high-tech, and consumer applications. Metal components are laser cut from a wide range of alloys such as aluminum, copper, titanium, stainless steel, tungsten, brass, nitinol, nickel, gold and many others. Projects requiring laser precision require precise cutting of these alloys in thicknesses from just a few microns to multiple millimeters. Each system type however creates a range of capabilities not only in designed form, but also in the materials they can cut. Though there can be some cross-over in capabilities between different laser systems, most are unique in the types of metal laser cutting possibilities. The following table will give more insight on cutting metal alloys into high-precision parts with laser technology.
Laser System | Metal Alloy Cut | Thickness Range | Laser Accuracy | Additional Capabilities |
---|---|---|---|---|
Fiber | Stainless steel, titanium, copper, nickel, tungsten, aluminum, brass | From 0.254mm up to 4mm, depending on the alloy | +/- 0.0254mm to 0.0762mm | Only metal alloys, thicker gauges than other laser system types. |
CO2 | Stainless steel, aluminum, carbon steel. | From higher powered systems- thickness steel alloys from1.5mm to 4mm | +/- 0.0508mm to 0.127mm | Cutting plastics, paper and wood are best. |
Ultraviolet (UV) | Copper, nickel, stainless steel, aluminum, gold, brazing alloys. | From 0.0254mm up to 0.254mm | +/- 0.0127mm to 0.0254mm | Small beam diameter and capability to cut non-metallic materials like polyimides, Rubber, graphene, and many more. |
Femtosecond | Stainless steel, copper, aluminum, titanium. | From 5um up to 10um | 3um to 5um | Ultra-thin materials, no HAZ, medical use for treatment of cataracts. |
Picosecond | Stainless steel, carbon steel. | From 5um up to 10um | 3um to 5um | Additional ultra-thin materials like ceramic, silicon, glass, no heat affect or HAZ. |
The table gives a general summary of laser technologies used in service today. However, the laser themselves offers more than just the capability to cut metal alloys and have become highly regarded as tools that industries favor for their high precision manufacturing needs. Let’s explore why metal laser cutting is a preferred method for many critical components.
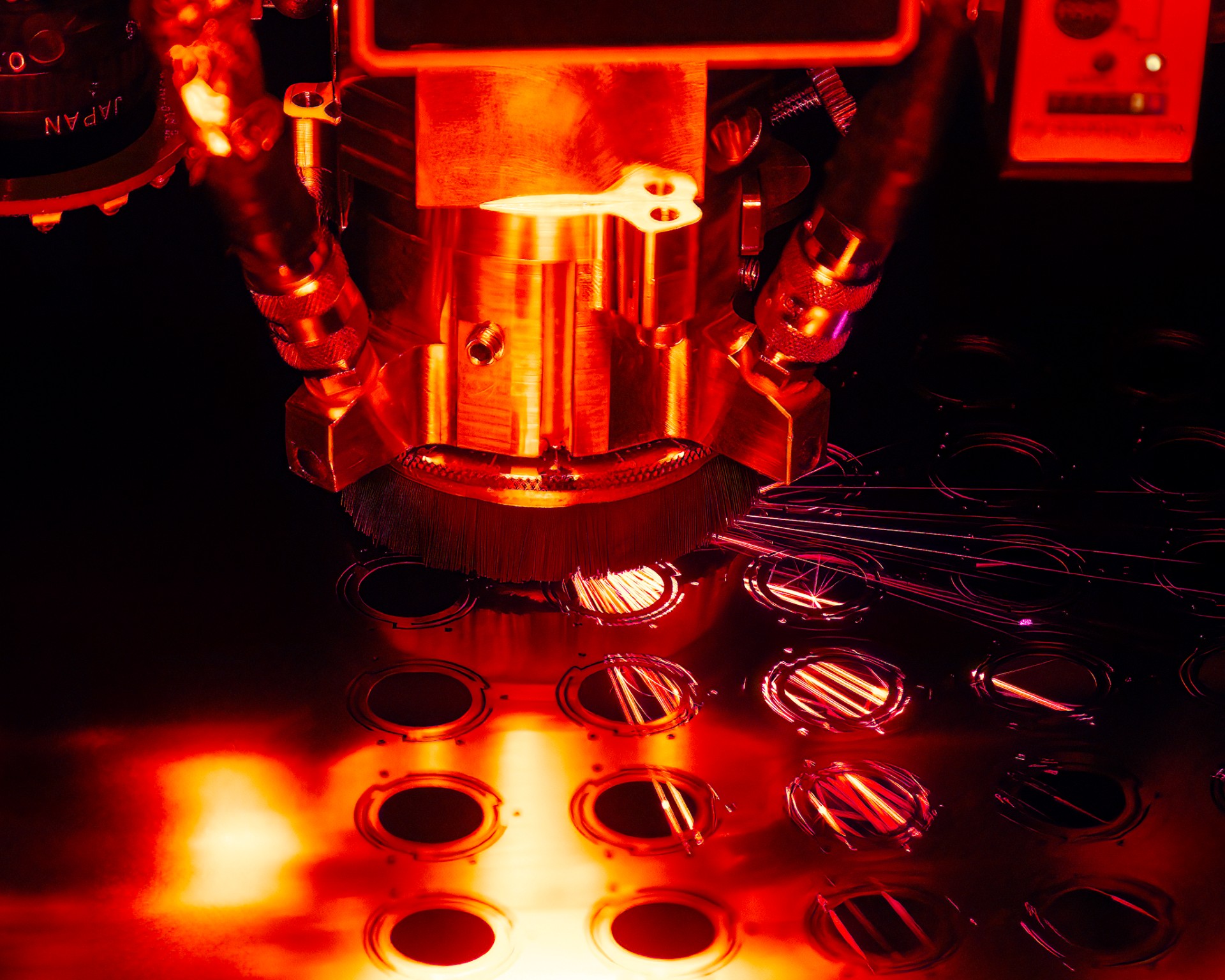
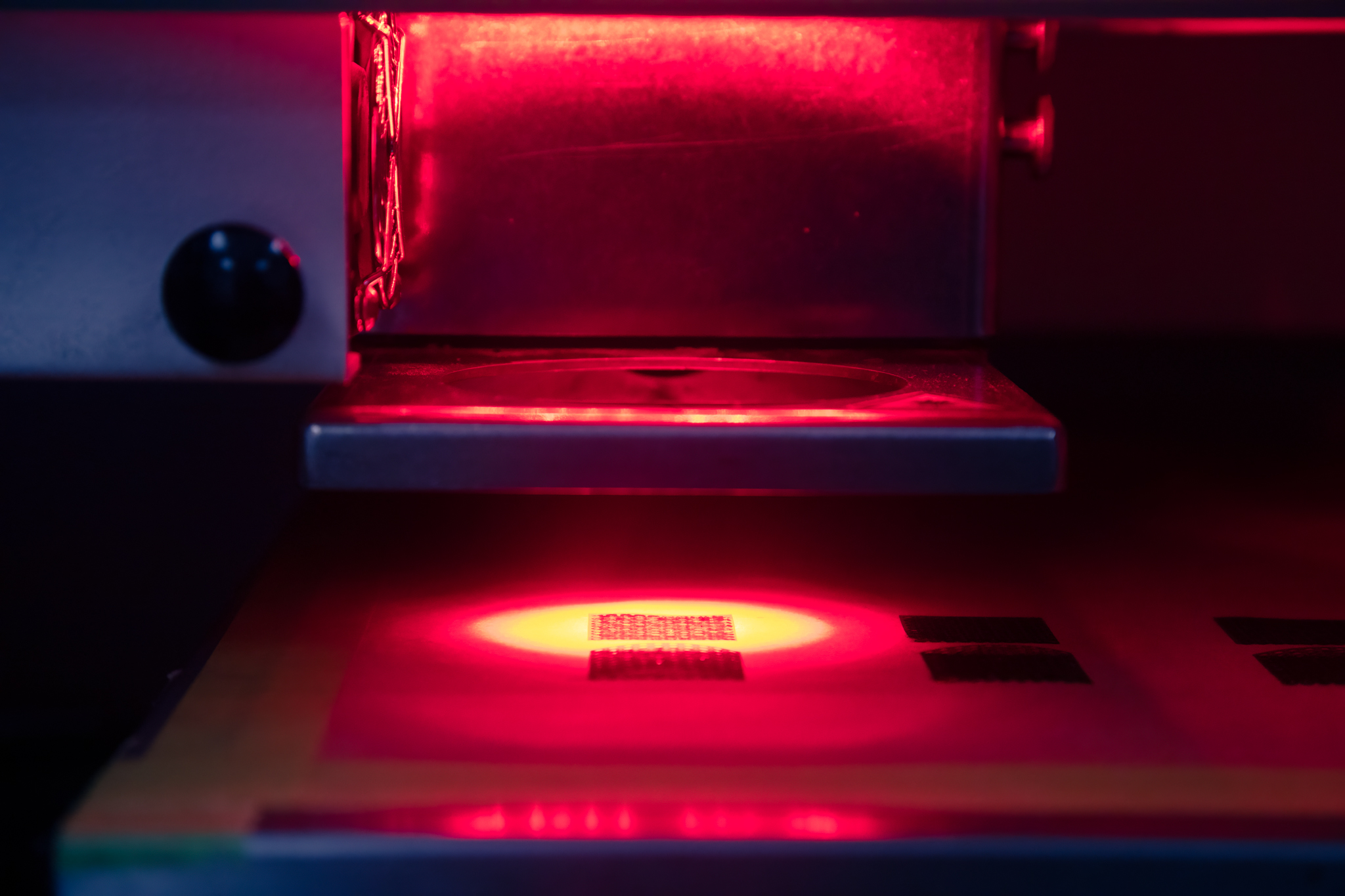
Fiber Laser
Ultraviolet Laser
The Call for Precision Support
Why do industries such as battery technology, wireless energy, nuclear science and medical device sectors depend on laser cutting? Other methods such as CNC Milling, CNC Lathe, Waterjet cutting and metal stamping are all wonderful technologies providing support to those same industries. The outreach to laser manufacturing specialists is due to a group of factors for the flexibility that laser cutting offers, both in materials, quantities and lead time. For laser manufacturing, there are no tools or dies needed, nor is there any complex set-up of the laser, unlike other methods. Laser technology is a key partner with many industries for prototype and R&D support. The ability to cut 1 part and move into full production is really just a matter of scheduling. Laser cutting of metal components is highly accurate and ideal for precision profiles in a 2D form. These flat parts are made to rigorous standards demanded for public safety and consumer satisfaction. The following examples will give more insight into high precision laser cut metal components.
- Medical Device: Using different grades of stainless steel, complex mechanisms were developed and approved for full production by laser technology. The complex parts needed to fit together and form a box to hold micro staples for surgical applications.
- Alternative Energy: The need for better energy cells, keeps the laser manufacturing community busy with new and demanding profiles. Copper is a key part of these cells and creating energy sources that fulfill efficiency and streamlines production is key.
- Nuclear Research: Working with national laboratories can be a great milestone to undergo and achieve. The custom components produced by laser technology supports research and related nuclear projects.
- Aerospace: Weight is a major concern for the aerospace industry. Producing high precision parts made from titanium and aluminum allows for the high reliability these parts require.
- Cathodes: Manufacturing cathodes is an extremely complex process, and only qualified services take on these challenges. The need for precise custom stainless-steel shims keeps the integrity of the process intact.
- Textiles: Supporting the automotive industry with fabric is a tremendous task. Being able to provide high precision guides for the fibers during the manufacturing process is critical to this industry. A bad part can require the looms to be taken off production. Consistency and accuracy are factors this industry asks for regarding laser technology.
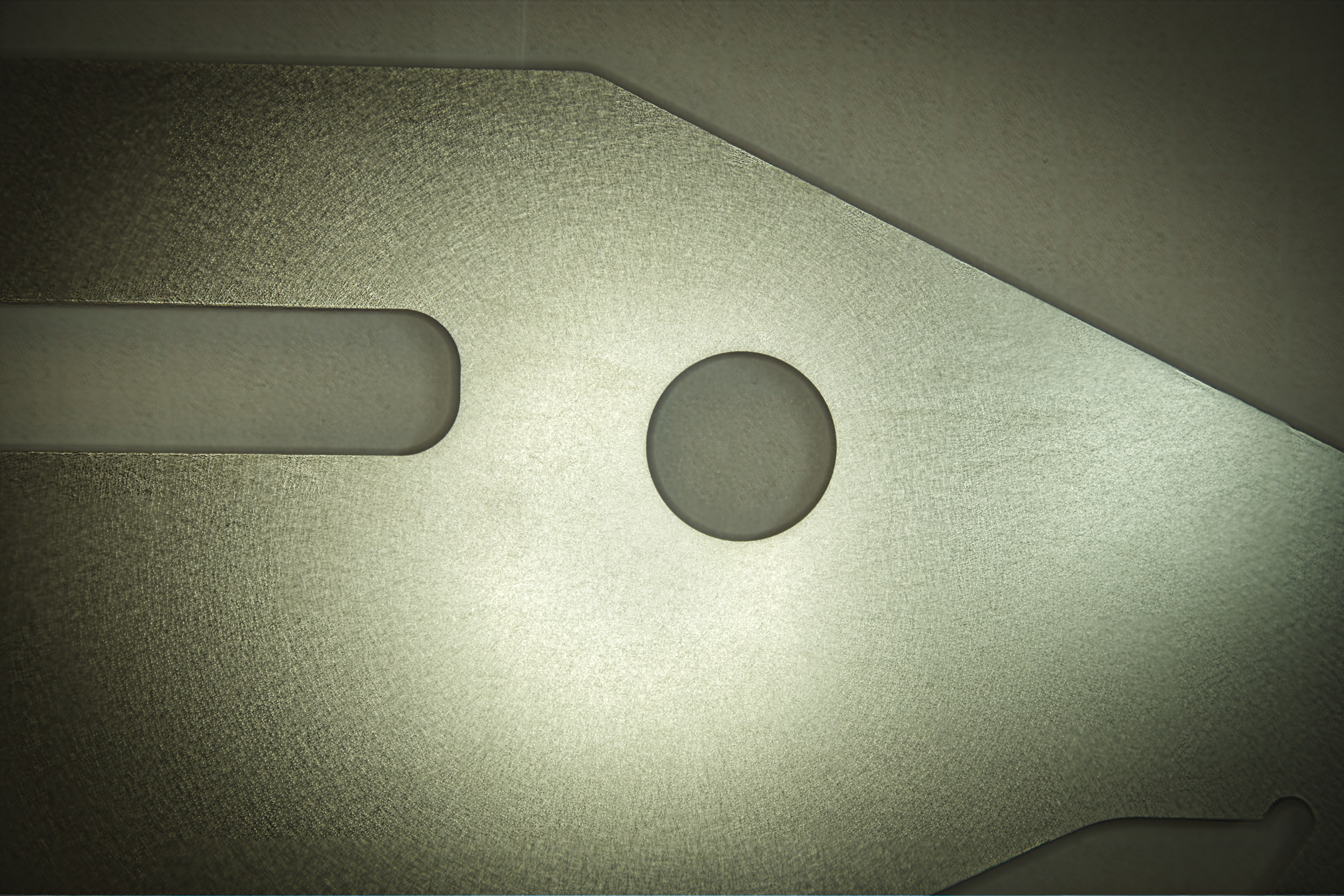
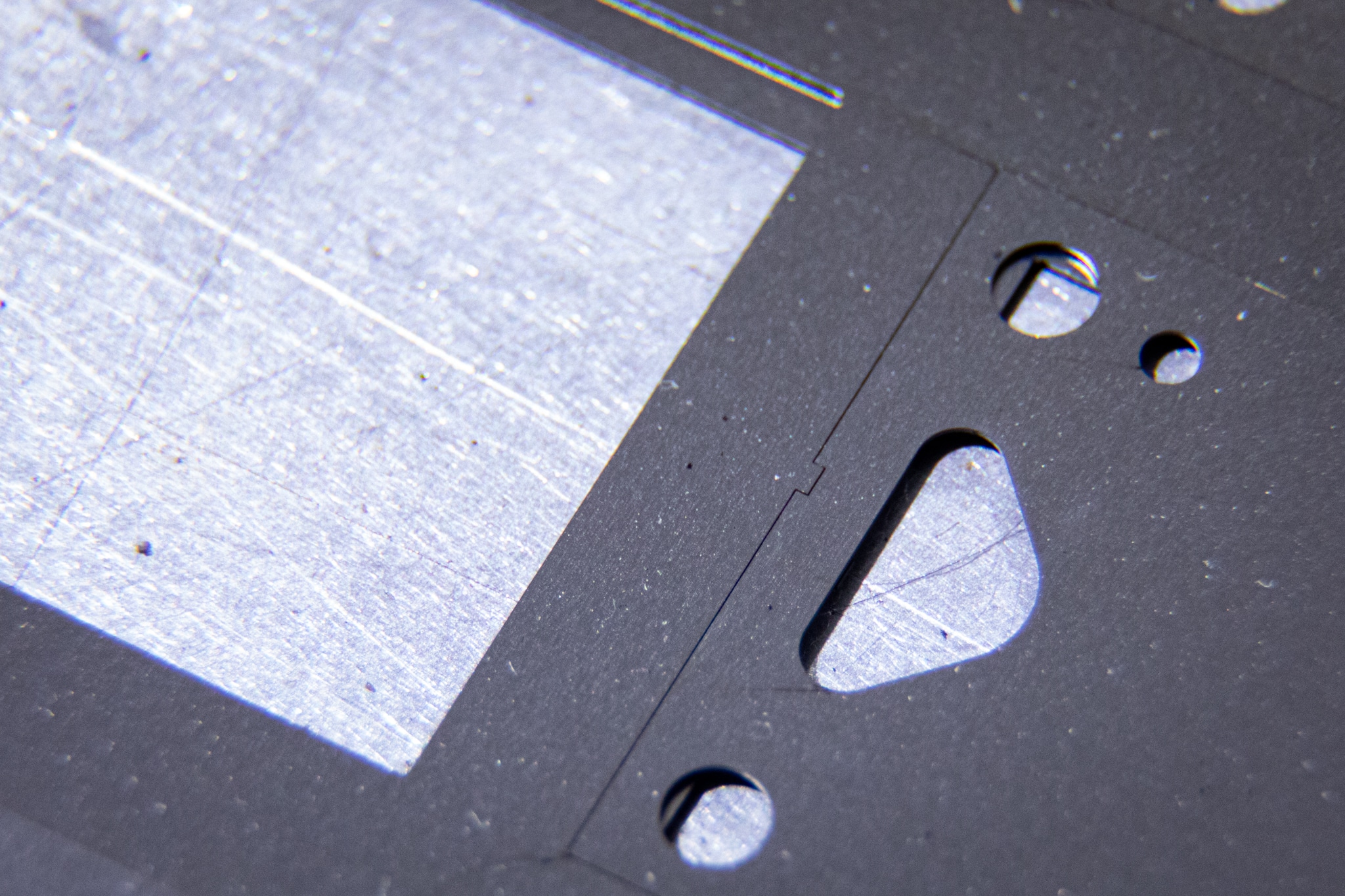
In conclusion, the unparalleled precision and versatility of metal laser cutting have established it as a cornerstone in numerous industries, ranging from medical devices to aerospace. Its ability to render intricate designs with exactitude, coupled with the efficiency in transitioning from prototype to full-scale production, underscores its vital role in advancing technology and innovation. As industries evolve and demand even higher standards of quality and precision, metal laser cutting will undoubtedly continue to be at the forefront, driving progress and meeting the exacting requirements of modern manufacturing.