What Manufacturing Methods Are Best for Holding Tolerances Within 0.5 Mil?
Holding tolerances within 0.5 mil (0.0005”) requires specialized precision manufacturing processes that minimize material distortion, tool deflection, and environmental interference.
Manufacturing Method | Tolerance Capability | Best For |
---|---|---|
CNC Machining | ±0.001” | Aerospace, medical, precision metal parts |
Wire EDM (Electrical Discharge Machining) | ±0.0001” | Complex geometries, hard metals |
Laser Cutting | ±0.0005” | Intricate patterns, thin materials |
Lapping & Grinding | ±0.0002” | High-surface-finish applications |
How to Maintain Tight Tolerances
-
Use High-Stability Machines – Avoid vibrations that could impact accuracy. Machines with granite bases provide better stability.
-
Optimize Cutting Parameters – Adjust speed, feed rate, and depth of cut. Cutting too fast can cause excessive heat buildup, leading to material expansion.
-
Employ Non-Contact Methods – Laser cutting and EDM reduce tool wear and mechanical stress on the material.
-
Regular Calibration & Inspection – Coordinate measuring machines (CMMs) and laser scanners ensure precision throughout production.
-
Use High-Quality Tooling – Carbide or diamond tools last longer and maintain sharper edges for consistent cuts.
-
Post-Processing for Accuracy – Secondary finishing methods like honing and lapping improve final tolerances.
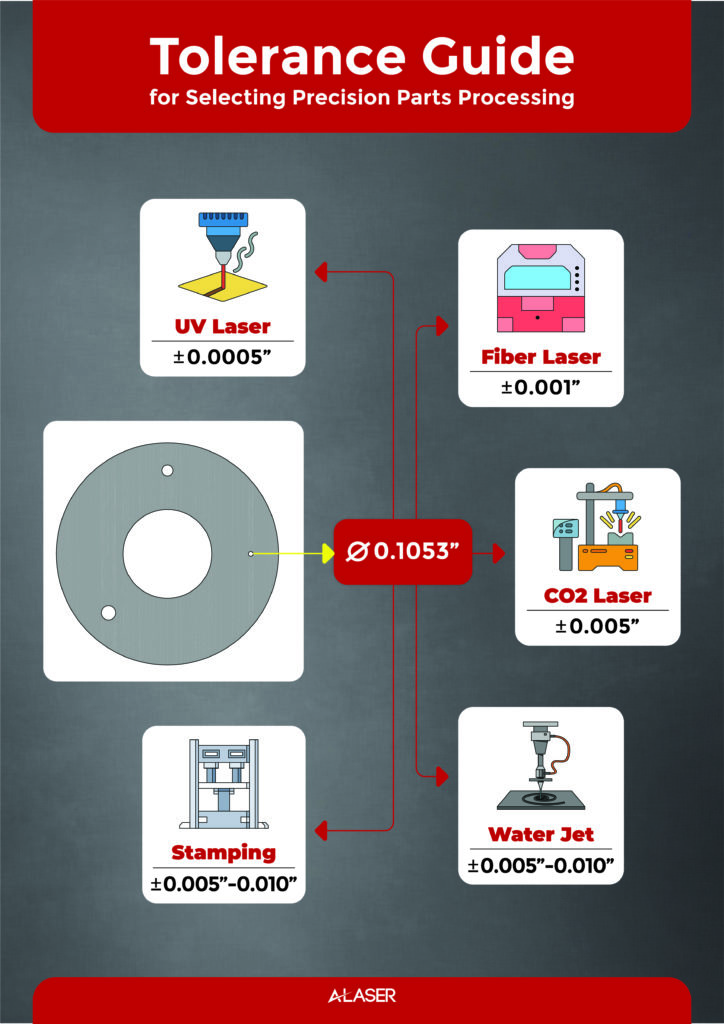