How Does Edge Radius Affect Part Performance and Fit in Precision Components?
Edge radius can dramatically affect the function and reliability of complex geometry manufacturing and fine detail machining. The edge radius refers to the rounding of a sharp edge in machining of metal parts. When a metal material is cut by means of cutting technologies like CNC Milling, CNC Lathe or laser cutting, the cut edge is not perfectly sharp. In manufacturing sharpness cannot be measured directly. It is the edge roundness that is measured, and a resulting sharpness is inversely proportional to roundness. The less sharp a radius is, it means it has been measured at a higher level and vice versa. The measured value of a parts edge radius can influence the amount of stress the component will be subjected to. This stress potentially can affect an adjoining component during its primary function, so measures need to be taken especially during small feature manufacturing. The following examples offer further insight into the influence of edge radius:
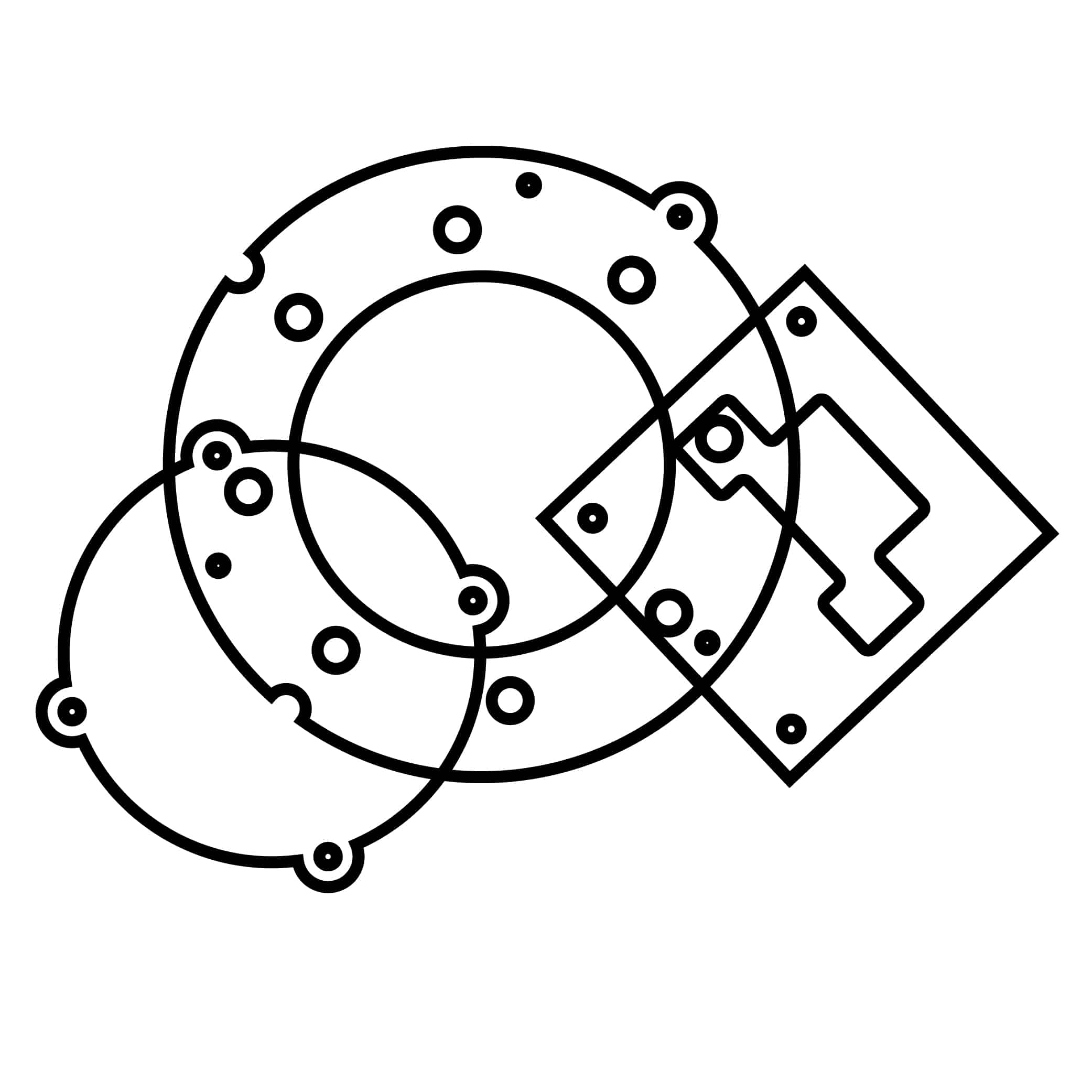
- Stress Reduction: Sharp edges can concentrate stress, making these areas more susceptible to cracks and failures under load. Radiused edges distribute will stress more evenly. By increasing the part’s resistance to fatigue and fracture, the lifespan is increased.
- Improved Fit: In mechanical assemblies, radiused edges promote smoother engagement and prevent wear between parts. This is crucial in precision components where tight tolerances are essential.
- Enhanced Durability: Radiused edges are less prone to chipping and damage from impacts or handling. This extends the lifespan of the component and reduces the need for replacements.
- Safety: Sharp edges pose a risk of injury during handling and assembly and the function of the component. Radiused edges minimize this risk, improving workplace and product safety.
- Improved Coating Adhesion: Coatings such as paint, and galvanizing, tend to pull away from sharp edges. By adding a radius, the coating can better adhere to the edge.
- Improved Fluid Flow: In applications where fluids or gases flow over parts, radiused edges can reduce turbulence and improve efficiency.
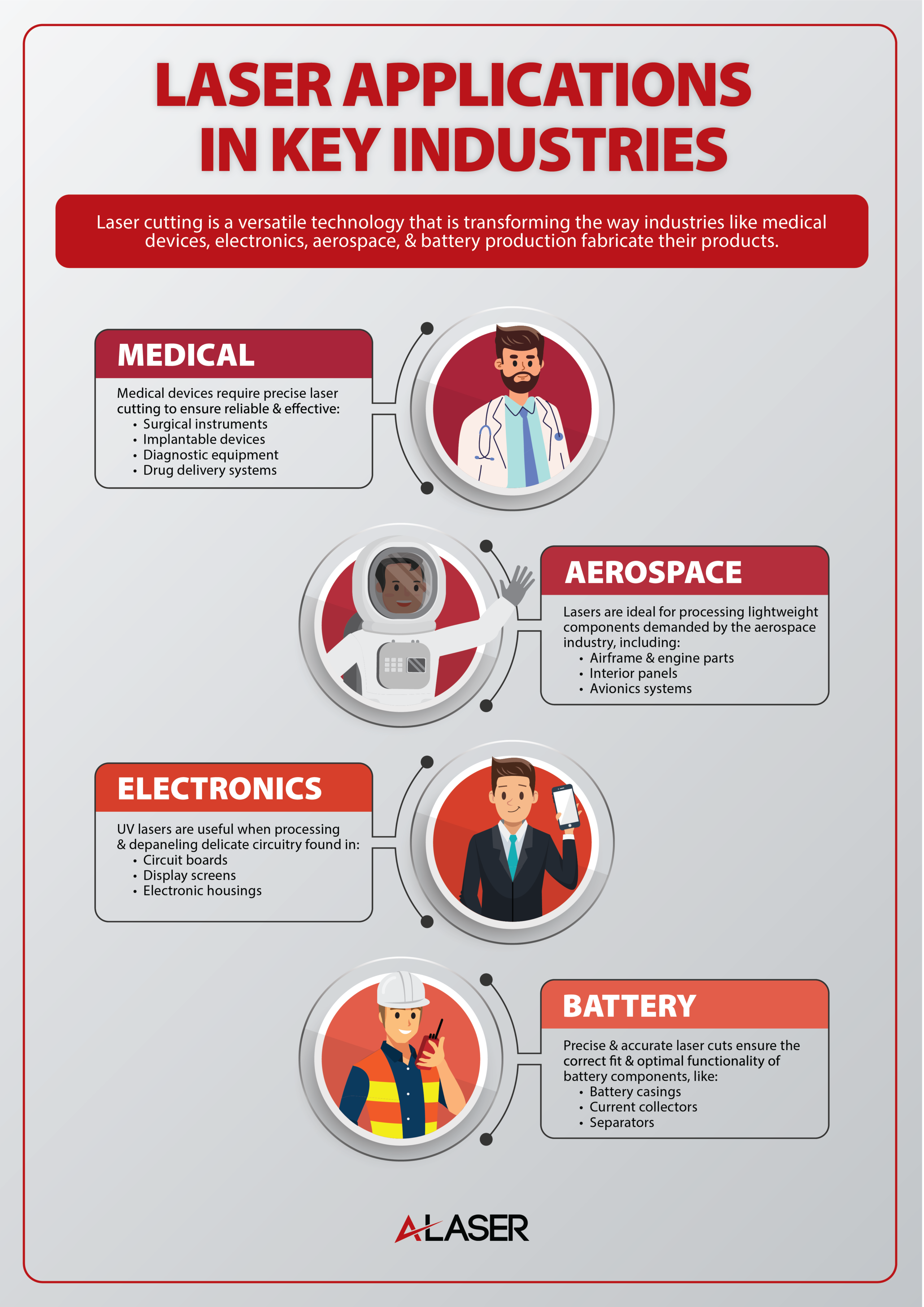
Applying The Edge Radius
Edge radius is a critical factor in complex geometry manufacturing that affects the structural integrity, functionality, and safety of components. By controlling the edge radius, manufacturers are able to participate in fine detail manufacturing for industries who demand superb and consistent quality. You can see examples of these applications like:
- Aerospace Components: Turbine blades and other aerodynamic parts require precisely controlled edge radii to ensure optimal airflow and prevent stress fractures.
- Medical Devices: Implants and surgical instruments often have radiused edges to minimize tissue damage and improve patient safety.
- Automotive Parts: Gears, bearings, and other high-stress components benefit from radiused edges to enhance durability and reduce wear.
- Cutting Tools: Cutting tool edges are often radiused to increase tool life and improve cutting performance.
- Textiles: The fabrication of materials requires smooth operation of all mechanisms in contact with the raw threads. Any sharp edge can cut or damage the material during the manufacturing process.
- Adhesive Dispensing: Carboard boxes, to materials and diapers, are made in part through high volume manufacturing. Edge radius is critical to provide uniformity of adhesives through the dispensing nozzles.
Making The Adjustment
Controlling the edge radius is done in numerous ways and is project specific in complex geometric manufacturing. Some techniques are done by adjusting the cutting parameters such as tool speed, cut entry location and the angle of cut on the specific machines. Other techniques used are done by post machining and can include tumble deburring, grinding, electro-chemical processes (electro-polishing, acid cleaning). The intended function of a precision component determines the amount of edge radius required and is adjusted to meet the required specifications.
In Conclusion
Edge radius, the curvature of the edge of a component, is pivotal in ensuring the optimal performance and fit of precision components. This seemingly small detail holds immense importance as it directly influences the quality and durability of parts. A properly controlled edge radius can minimize stress concentrations, reduce the likelihood of fractures, and enhance the overall lifespan of a component. By fine-tuning cutting parameters and employing post-machining techniques such as tumble deburring, grinding, and electro-chemical processes, manufacturers can achieve the desired edge radius. The benefits of achieving a conforming edge radius are manifold, including improved efficiency, better safety, and higher reliability of precision parts across various industries. Ultimately, attention to edge radius is a testament to the commitment to excellence in manufacturing.