Laser Cutting Brass
Laser Cutting Brass
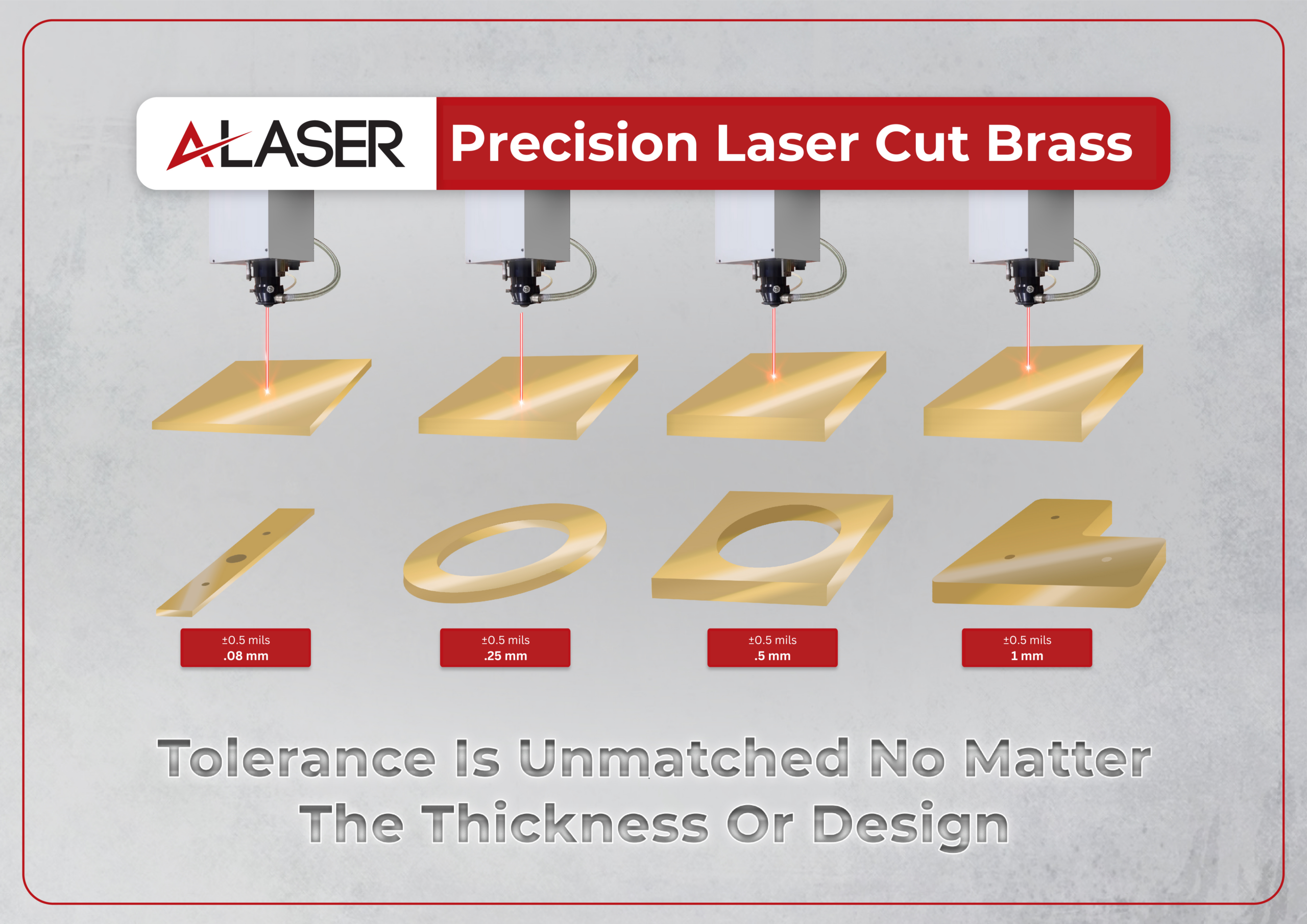
What Criteria Influences the Cost of Laser Cutting Brass?
The cost of laser cutting brass considers factors such as material thickness, alloy type, design complexity, laser system used, and other factors. Brass is an alloy formed by combining other alloys, namely copper and zinc. The earliest known creation of brass was about 3000 BCE. The discovery then was favored by early rulers of these ancient civilizations. Brass is shiny and therefore was favored for helmets, jewelry, and sacred vessels of the aristocrats at that time. Today, brass comes in formulations for a range of uses and products. A 60/40 formulations which mean 60% copper and 40% zinc is used widely for musical instruments. A ratio of 70/30 brass is used to make plumbing fixtures while “red brass” is used for architectural and decorative items. The red comes from the higher percentage of copper. Brass can be CNC Milled, CNC Lathed, drilled, cut by saws and formed into shapes. When precision components are made using laser technology, the
manufacturers consider criteria and special factors to determine the cost. The most often laser system types used to cut brass are fiber laser, plasma laser, CO2 laser, and ultraviolet laser technology. Fiber lasers are used for many precision projects requiring brass due to their capability in cutting sheets of the alloy to tolerances of +/- 0.0508mm. Plasma systems can cut brass but generally used to cut thicker gauges mostly more than 10mm thick. CO2 lasers are used to sheet metal type of projects including brass and UV laser can also cut brass, but generally applied when thin foils are used. Ultraviolet lasers can offer tolerance as tight as +/- 0.0127mm, depending on the project’s details. Since each project will have its own set of details, the following list of criteria is an example of what goes into determining the cost of cutting brass by laser technology:
Material Factors:
- Thickness: Thicker brass will require more laser power, (wattage) and time.
- Alloy composition: Different alloys will cut easier due to the percentage of copper/zinc. Some alloys like “free brass” may contain lead as well to make the material more machinable. In all, specific laser parameters are needed for each alloy type. These parameters are called the laser “tool” and consist partly of laser power, laser focus, laser dwell time, laser speed, laser frequency, and laser passes, (the number of times the laser runs through the cut path).
Design Complexity:
- Geometry: A simple washer type of component, at .2mm thick with 100mm linear total distance will cut faster than another of the same thickness and linear distance but is more complex. Perhaps there are some intricate shapes and small radius that the laser speed will need to be slowed. To prevent heat affected zones or HAZ, multiple laser passes may be required, adding processing time.
- Tolerance: A tolerance of +/- 0.127mm will cut faster than the same design at a +/- 0.0254mm.
Project Volume:
- Quantity: Laser technology is great in supporting R&D and prototyping projects. However, most manufacturers do have a minimum order amount. To receive more competitive pricing, many laser manufacturers do offer volume discounts.
- Batch size: Processing multiple parts in a single batch can reduce setup time and costs.
Laser System Type:
- Laser capabilities: The different system types mentioned earlier, fiber, plasma, CO2, and Ultraviolet all their unique capabilities. Laser manufacturers having multiple system types have the advantage of offering potential more competitive costs when several system types are available. These differences include power availability, beam diameter (the smaller the beam, the smaller the feature size that can be cut), thickness range (goes hand with power), set-up costs that requiring any special handling procedures?
- Operating costs: Laser systems may need more maintenance than others. Keeping the optics and laser source at optimum performance does add cost.
Lead Time:
- Standard or Expedite: Faster turn times can add cost as expedited processing goes into effect. If you have time and can work within the manufacturer’s suggested lead time, you can save cost.
Additional Services:
- Post Finishing: Many projects require a post finishing process like polishing, plating, or engraving. If done in-house or by a third-party provider, the additional steps add cost and lead time.
- Special Packaging: Not to be forgotten and at times a very crucial requirement is special packaging. Precision laser cut components can be very delicate and need packaging that will ensure undamaged parts are received. This can be crucial to the way the parts perform during their lifespan. Procurement of specialized packaging and or the handling of supplied packaging can add cost to the production process.
How Much Does It Cost to Laser Cut Brass?
With the criteria mentioned, a more accurate determination of your specific project can be made by consultation with your preferred service provider. A well-established laser manufacturer will be able to review your project and offer a quotation, within 24hours, in most cases. The following examples of laser cut brass indicate the cost difference between laser systems and material thickness:
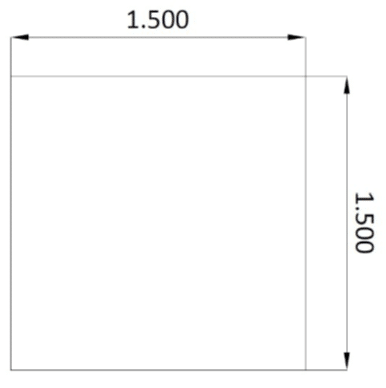
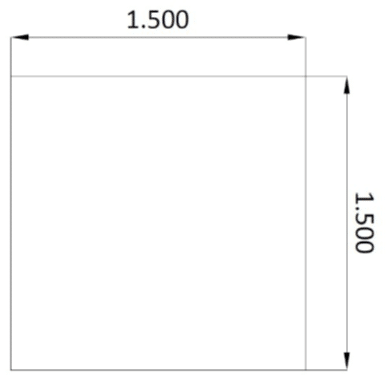
0.0254mm thick brass, cut by Ultraviolet laser: $15.00
0.254mm thick brass, cut by fiber laser: $7.50
To aid in receiving a prompt and qualified quotation, keep in mind the criteria that will be used to determine feasibility and cost. Additionally, the following tips will be most helpful to process your quotation:
- Cad Data: Computer Aided Design, this is the design of your desired brass component. Many manufacturers accept data in the form of an AutoCAD dxf file, Solid Works step file, or other similar types. A pdf file can be used if the geometry is simple as the manufacture will need to create the CAD data design in house. More complex designs in PDF form can add cost or may not be possible for the manufacturer to create.
- Brass alloy type: The brass type and thickness must be known. Will you supply the brass or need the manufacturer to procure?
- Lead Time: How fast do you need the brass components? Expedited requests will have a premium charge in most cases. If time is available, go with the manufacturer’s recommendation.
Scope Of Work: Initial projects sometime do not convey the size of the opportunity. If the project has a scope of work that goes beyond the basic one-time order, this is where opportunities can grow. Smaller R&D needs that lead to volume production allow the manufacture to develop more efficient methods and processes. Keeping the communication open can be beneficial to both parties.
The cost of laser cutting brass is influenced by a variety of factors, including material properties, design complexity, job volume, laser technology, and additional services. Understanding these criteria allows manufacturers to make informed decisions regarding their production processes and costs. By carefully considering these factors, businesses can optimize their laser cutting operations and achieve the desired balance between quality and affordability.

Can We Engrave Brass?
Regarding brass, yes it can be laser engraved. This statement is the easy part as the characteristics of brass can be challenging to engrave if the proper steps and brass alloys are not used. Brass is a well-known alloy and is favored for use in decorative elements in the home or signage and well-established manufacturing of brass musical instruments. Brass is highly reflective and gives a glistening sparkle to any application. There are a couple of brass formulations that are used most often and those are 260 brass and 360 brass. The versatility of 360 brass is seen in electrical and plumbing components and for door or trophy nameplates to ammunition casing and many more applications. When laser engraving onto brass there generally are two methods that are used:
Bare Metal Engraving: Engraving onto bare metal brass is exactly as the name states. This is where engraving onto brass that does not have an added coating. This type of brass is called premium leaded brass. The alloy of lead is added to the formulation of the copper and zinc. The resulting engraving is shiny and robust but needs to be enhanced by post processing to add more contrast. To produce this type of engraving a laser system type like a fiber laser would be best. Fiber lasers have a wavelength that is absorbed by brass and gives precise and accurate designs.
Laserable Brass Engraving: The other commonly laser engraved brass is called laserable brass. It’s given this name because it has an outer coating of enamel or lacquer applied to the brass surface. The lacquered coating is clear and does not affect the color of the brass surface but allows the brass to be laser engraved. When an enamel coating is applied to brass, this can be applied in different colors and once engraved the contrast of the shiny brass material comes through. Both coatings enable CO2 lasers to engrave, since these lower powered systems are engraving on the coatings and not the brass.
Tips For Laser Engraving Brass
An engraved brass nameplate or component will have a clean polished look, but it does need to be done right. Using laser technology is a wonderful way to achieve a quality result. Experienced laser service providers will keep in mind the following and in use in practice:
Design and Software: The laser run programs of the selected designs, much like ones used for laser cutting. There are dedicated software programs for laser engraving that create bi-directional hatch patterns or optimized two-way patterns. Keep in mind that the more complex the design or amount of text to be engraved will add time and cost to the project. If the area to be engraved is too small for the design to fit, reducing the size of the image or font can be done, but may not be as legible.
Laser Power: More powerful laser systems will engrave faster and have the capability for higher throughput. Caution is needed when using a higher-powered system when engraving thinner gauges of materials, as too much power can cut through and much of the energy is being reflected. Because of this high reflectivity, safety precautions need to be used to protect the operators from possible beam reflection.
Optimum Contrast: To enhance the appearance of the engraved brass, oxidizers can be applied to the engraved area. This is done soon after the engraved brass is taken off the laser for the best results of a black color to the engraving. Commercial names of oxidizers are Patina Solution, Brass Black and others. These oxidizers have a combination of chemicals including acids, to improve the oxidation, sodium hydroxide, potassium sulfide, or ammonium persulfate, cause the metal to react and change color. They can include colorants to result in a specific shade or color to the laser engraved area.
A Word About Laser Etching
Laser etching is another method to mark a component or design on brass or other metal alloys. Laser etching, however, is different from engraving in that just the material surface if altered, often just enough to create a visible change in the contrast on the material surface. There are laser marking inks that can be applied on the surface to enhance contrast. Laser etching is not as robust as laser engraving and the markings can be worn off through handling and surface abrasion. It is a quicker process and requires less laser power, therefore a good option for specific projects and cost considerations.
Laser engraving brass is a great method to use when a high quality and uniform design is desired. It is a non-contact method that keeps the brass surface from scratches and marring during the engraving process. Laser service providers have experience in making the fine adjustments needed when engraving a highly reflective material like brass. Additionally, by using oxidizers the resulting clarity of the font and design details will stand out handsomely with durability that lasts for many years.