3M Double Sided Tape
Adhesive Technology Solutions
The way materials would be bonded changed with the development of 3M double-sided tapes. 3M began as a small mining company and was not intending to produce products such it now does. Through experiences that companies have it was innovation that steered the company from failure to success and then to its modern-day versatility. The evolution of double-sided tapes showcases a journey of this innovation and practicality. 3M Tapes have a rich history, driven by a commitment to focus on developing solutions to real-world problems. From humble beginnings, 3M has grown to become a global leader in adhesive technologies. Though this topic will focus on 3M double sided tape, it will be difficult to not mention some of the wide range of tapes that are essential in countless applications across various industries, that 3M manufactures. 3M, initially the Minnesota Mining and Manufacturing Company, was founded in 1902.
In the early 1920s, Richard Drew, a 3M lab assistant, observed the need for painters to have a method to make the process cleaner and with more accurate results, as they struggled with paint jobs due to the lack of an effective masking material. This observation led to the invention of masking tape in 1925. This was a significant breakthrough, as it allowed for cleaner paint lines and streamlined the painting process and was found to be beneficial in numerous other applications. With the success of masking tape, 3M was prompted to explore other types of tapes where industry and public use could benefit and created tapes such as scotch tape, duct tape, and electrical tape, just to name a few. These first tapes were single sided but could not bond in ways that manufacturers needed and were reclined to use liquid glues and pastes. The development of double-sided tapes would change all this.
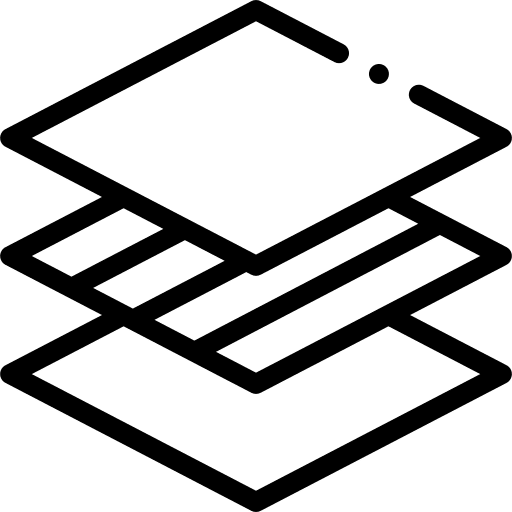
Base Types of Double-Sided Tapes
Double-Sided tapes have a pressure-sensitive adhesive applied to both sides. The carrier that the adhesive is applied to can be ultra-thin in fractions of a millimeter or up to thick foams used for in dampening vibrations. These double-sided tapes made by 3M come in two forms, Double Coated Tape and Adhesive Transfer Tape. The differences and uses of each are shown in the table below:
Tape Type | General Characteristics | Benefits | Adhesive |
---|---|---|---|
Double Coated Tape | Carrier is the material that holds or “carries” the adhesive; in double coated tapes it separates the two adhesives. Carriers can be made of paper, plastic film, tissue or foam, depending on application. | Having a carrier in the middle enables two different adhesives to be applied for adhering dissimilar materials that require different bonding properties. | Acrylic, Silicone |
Adhesive Transfer Tape | Adhesive Transfer Tape is composed of a thin film of adhesive with a liner over the top so it can be easily handled. | No carrier for separation. Thin bonding tapes consist of one type of adhesive. Overall temperature resistance not limited by the temperature resistance of the carrier and they are extremely conformable to irregular surfaces. | Acrylic, Silicone |
Data taken from 3M Corporation.
Revolutionary Bonding
Double-sided tapes have adhesive on both sides, enabling them to bond two surfaces together without the need for visible tape or adhesive. As progress is made in technology with materials, adhesives, and the method of manufacturing, industry uses of double-sided tapes are done so for advantages such as:
- Aesthetics:
- Clean Appearance: Double-sided tapes create a sleek, seamless bond with no visible fasteners like screws, rivets, or nails. This is key for maintaining a clean, professional look in many applications.
- Improved Design: They allow for more streamlined and elegant designs by eliminating the need for bulky hardware or visible attachment points.
- Efficiency & Speed:
- Simplified Assembly: Double-sided tapes can simplify the assembly process, reducing the time and labor required compared to methods like drilling and screwing.
- Automation-Friendly: Many applications can be automated using robotic systems to apply double-sided tape, increasing production speed and consistency.
- Versatility:
- Wide Range of Applications: Double-sided tapes are available in various strengths and formulations, making them suitable for a wide range of applications, from light-duty mounting to heavy-duty industrial bonding.
- Adhesion to Diverse Materials: They can bond to a variety of materials, including metals, plastics, glass, wood, and more.
- Other Benefits:
- Vibration Dampening: Some double-sided tapes have vibration-dampening properties, making them ideal for applications where noise and vibration reduction are important.
- Water and Weather Resistance: Many industrial tapes are designed to withstand harsh environmental conditions, including moisture, temperature extremes, and UV exposure.
Manufacturing Methods with Double-Sided Tape
Having abundant rolls of any double-sided adhesive tape does not solve bonding challenges until the tape is applied to specific parts of the intended product or device. To accomplish this, manufactures will use various technologies to produce the necessary precision parts. These types of components can very well become part of any production process and be manufactured in thousands, hundreds of thousands, or even millions of units. Selecting the appropriate technology is done early on in R&D and prototype stages and can be processed by the following manufacturing methods:
- Die Cutting: Die cutting is a process that covers heat seal die-cutting, flash die-cutting (for prototypes) and rotary die-cutting. Die cutting is used in many forms of production. Challenges for some projects that require straight edges, as the die can round edges of certain materials.
- CNC Knife Cutting: A computer numerically controlled blade that can process smaller sized components up to larger industrial uses.
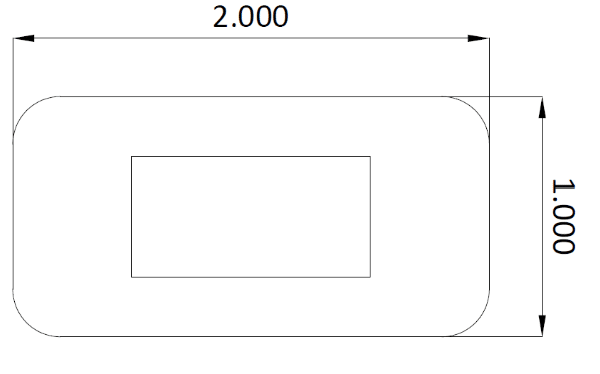
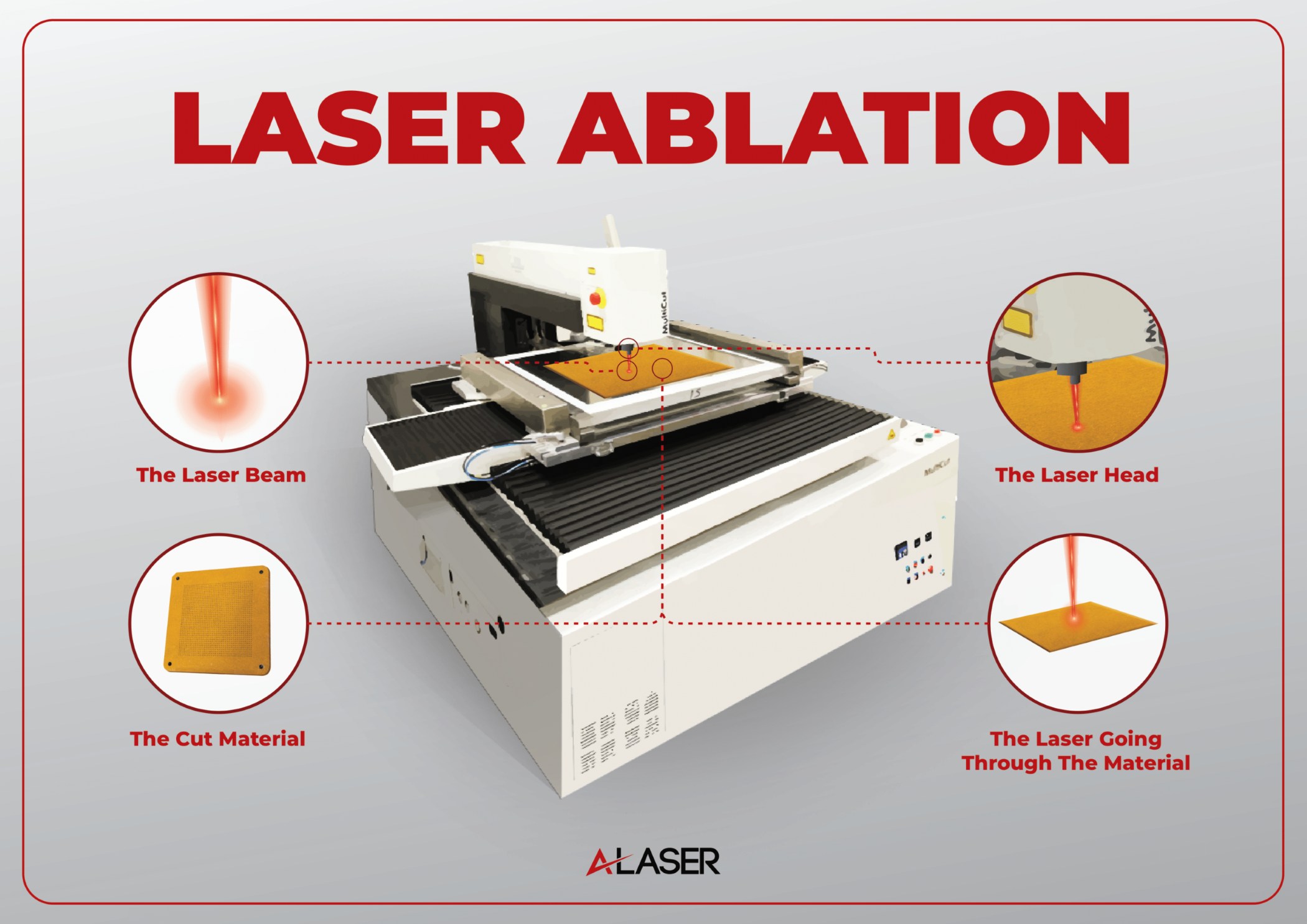
- Laser Cutting: Laser technology can support R&D and prototype stages and is versatile in processing materials with and without adhesives. Doubled-tape projects using laser technology are best done on diode lasers with ultraviolet wavelengths or CO2 laser technology.
Creating The Bond with Manufacturers
Learning of the advantages to using 3M Double-Sided Tape, and the technologies used in manufacturing precision components from it, do not demonstrate the vast applications supported by this bonding technology. The following table is mere glimpse of how 3M Double-Sided Tapes are used:
Application/Industry | 3M Double-Sided Tape(s)* | Notes |
---|---|---|
Print-POP-Graphic Arts | 3M Adhesive Transfer Tape 465, 3M Double Coated Tape 950 | Commercial printers, print finishing, fulfillment and media service companies- suppliers to the retail and consumer packaged goods industries. |
Food & Beverage | 3M Double Coated Tape 9579, 3M Double Coated Tape 9443NP | Flexible plastic films use tapes in a variety of applications, including splicing and attaching. |
Metal Stamping-Engraving-Embossing | 3M VHB Adhesive Transfer Tape F9473PC, 3M Adhesive Transfer Tape 9485PC | This 5 mil transfer tape offers a thin profile and a long-lasting bond on metals with high temperature resistance also chemical, UV and solvent resistant |
Manufacturing Process Aids | 3M Double Coated Tape 410M, 3M Double Coated Tape 9579 | These tapes are a convenient way to hold parts or materials in place. They are frequently used in machine shops, wood shops and small manufacturing job shops. |
Construction & MRO | 3M Double Coated Paper Tape 410M, 3M Double Coated Tape 9579 | New construction and MRO facilities maintenance. Solutions are available for many temporary applications, such as attaching carpet in a tradeshow booth |
Medical Industry | 3M Medical Tape 1587, 3M Medical Tape 9877EL | May be used for healthcare medical devices. |
Electronics | 3M Electrically Conductive Double-Sided Tape 9772 | Heat shielding, XY-axis electrical resistance. |
*Data is taken from 3M Corporation and does not include all available products. For more information visit 3M Corporation website.
Conclusion
Double-sided tapes have revolutionized industries by offering a versatile and efficient bonding solution. Their aesthetic appeal, ease of use, and adaptability across diverse materials have made them indispensable in various sectors. Precise manufacturing techniques, including laser cutting, die-cutting, and CNC knife cutting, enable the creation of intricate shapes and precise dimensions from double-sided tape, further enhancing their applicability. These methods facilitate the production of customized components for specific applications, from automotive interiors to advanced electronics, showcasing the significant impact of double-sided tapes on modern manufacturing and design.