Why Choose Laser Cutting?
I have had the privilege of speaking with many precision parts manufacturers to learn about the technology and methods they use to achieve critical geometries for a number of different industries and needs. Each technology has its pros and cons, and different foundations for success in the world of precision manufacturing. I work for a laser cutting service provider and would like to highlight why I believe that laser could be a preferable method over other available technologies. But while I will speak of the differences as positives, I do not feel that one technology is ultimately the better choice. There are numerous variables and qualities that each method available to industry offers that should be considered when choosing which technology to use for a project.
The different methods for precision parts manufacturing include:
- Die cutting
- Metal stamping
- Chemical etching
- Laser cutting
- Micro molding
- 3D printing, both plastics and metals
So why choose laser technology?
Laser offers quick turn manufacturing capabilities. It can cut 1 part or entire production runs. Laser technology also allows for change in geometry. No tooling is required, so an adjustment is simple. Lasers offer the ability to cut many different materials on a single system; You can go from flexible epoxies, to stainless steel, to FR4 and finish the day with polyimide with an acrylic adhesive. No changes to the laser hardware are needed.
Precision is often one major reason for switching to laser. Tolerances of +/- .001” are standard for many with tighter tolerances available for different manufacturers. Laser technology often results in a clean smooth edge, with straight walls. Small features can be designed due to beam diameters of 20 micron or smaller on many systems. Laser system set-up is so easy, it’s almost plug and play. Electrical and air hook up will be needed for many of the large and smaller machines. Laser technology has been a great fit for lab research and R&D, especially in universities and start-ups. Laser allows for a quick and easy way to bring concepts to life. Some laser systems are adjustable to do surface ablation and remove top layers or create geometry on the surface, but not cut through the material entirely. Such lasers can process what is called a ”kiss cut”, this will allow the user to have parts cut down to a liner so the part can be peeled away.
The versatility of laser technology has many benefits to offer for industry, whether it be in-house support, or service providers who specialize in laser technology. Lasers are great for R&D and prototype work. They are also useful for high production runs. They are reliable and repeatable and will continue to grow in demand and use
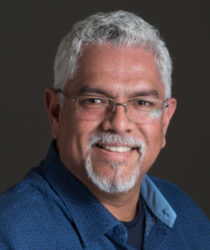
About the Author
Joe has been part of the A-Laser team for over 10 years and has extensive experience with laser cutting technology, sales, and customer service. Joe was born and raised in San Jose, CA and has resided with his family in Gilroy, CA since 1997. The unique projects he gets to learn about and the industries they support, keep everyday new! His hobbies include photography, he is a member of the Morgan Hill Photography Club, hiking, model building and collecting vintage camping lanterns and stoves. His favorite places include Mount Lassen Volcanic National Park, Portland OR, and Boston MA.