What Tolerances Are the Most Difficult to Machine?
For any manufacturing method, tight tolerances are factors that encompass multiple zones of a manufactured component. Precision manufacturing processes like CNC machining, waterjet cutting, stamping, and laser cutting all provide excellent products within their capabilities. As a group, each has challenges to overcome regarding the best approach to achieving a precision component that has quality and durability. Tolerances are those check marks that give the thumbs up or perhaps thumbs down of any high accuracy cutting project. Not all tolerances are the same of course. Some in respect to many projects will be deemed to be large tolerances, which go beyond that industry or that manufacturer’s standard tolerance parameter. This really means that that component functions very well at this range. However, you will see a dramatic difference in ultra-precision engineering projects where tight tolerance can be challenging and difficult to attain. What constitutes a tight tolerance is subject to the manufacturing methods used, but there is overlap we can see in various methods and different approaches used to result in conformance.
Tight Tolerances and Industries
Listing the most difficult tolerances would be a broad listing and not cover adequately what manufacturers experience in reality. To assist in understanding what the most challenging tolerances in precision manufacturing processes can be, the following table will be a guide and give insight into the manufacturing process world.
MFG Method | Technology | Tolerance Challenge | Additional Tolerance Factors |
---|---|---|---|
CNC Machining | Includes: CNC Lathe, Milling, Turning. Rotation of high speed cutting tools, for 3,4,5 axis parts. | Tolerances of 0.03mm or less. Thes can be unilateral or bi-lateral tolerances. | GD&T- Geometric Dimensioning and Tolerancing-concentricity, perpendicularity, and true position, are challenging with tolerances below standards of 0.13mm |
Laser Cutting | Using light energy from focused beams. Different systems such as: Ultraviolet, Picosecond, Femtosecond, Fiber. Great for thin, materials for 2D profiles. | Achieving sub-micron tolerance with UV lasers. Pico and femtosecond lasers- difficult to maintain accuracy through multi-layer materials. Fiber laser -sub 0.025mm is challenging. | Lasers like UV and Fiber- can exert HAZ or heat-affect. Pico and femtosecond lasers cost is consideration especially for high output along with high precision. |
Stamping | Using hardened dies to cut flat sheets of metal alloys into precision components. Good for 2D profiles. | As tight as +/- 0.025mm, Material factors such as grain direction, tensile strength. Tooling pressure and speed also are factors. | Tool wear, material “spring back”, vibration, and small intricate features and others can affect tolerance. |
Waterjet Cutting | Combining high water pressure and abrasive media like sand or agate forced through nozzles. Cuts very thick materials. | Tolerances sub +/- 0.050mm, some projects can go to +/- 0.025mm. Cutting speed, material thickness/hardness and abrasives used are just some of the factors. | Skill set of the operator can affect the tolerance along with the software and controller units used. |
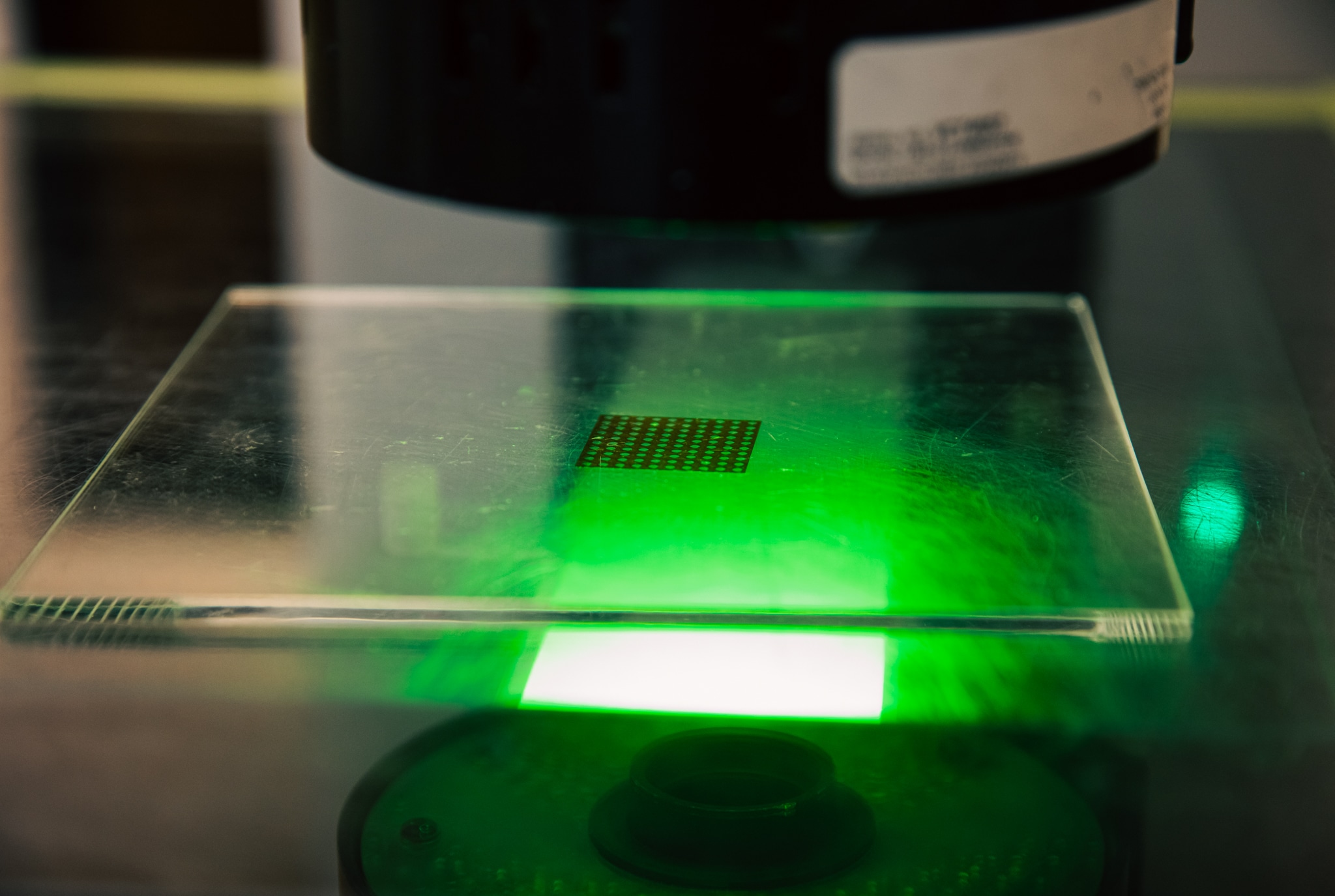
The most challenging and difficult tolerances varies greatly for any precision project. Manufacturing methods have a host of factors contributing to the final outcome and tolerance threshold that can be held. The table is an indication of general limits but does not account for the types of materials and geometry, as those factors add countless variances that could be encountered for every method of manufacturing used. There are limits nonetheless and realizing this before production takes place will save cost, time and frustration. Research of the best suited technology for your project can help in directing the best methods and materials that are available to met your precision component’s requirements.